目前,智能化、柔性化的加工技术已经成为高端钣金加工厂商的追求和渴求,因此机器人折弯单元在这样的市场环境下应运而生。
目录
钣金折弯技术现状分析
在钣金行业,目前大多数企业都采用传统的折弯工艺,在生产过程中,由于产品的品种、规格、批量小,需要采用多种 液压折弯机 机器 仍需要大量熟练、经验丰富的板料折弯操作工来完成工件的折弯。
但在实际工作中,存在如下问题:
- 首先,由于操作人员长时间作业,耐力不持久,造成每次放置的工件高低位置不一致。
- 其次,操作人员不像机器人那样保持稳定性,因此折弯工件的尺寸和折弯精度会受到人工的影响而无法保证,导致成品的质量较差。
- 第三,面对大型工件时,一般需要3-4名操作人员才能完成搬运操作,招工难、成本高是企业面临的困难。
- 第四,按照传统的折弯工艺进行作业对操作人员的安全影响较大,在吊运工件时存在较大的安全隐患,容易引发工伤事故。
如今,虽然折弯机的制造水平和精度较过去已经有了很大的提高,但与当前智能制造的要求相比,还存在着不小的差距。
在智能化生产、个性化定制、服务化延伸、网络化协同等方面,钣金装备制造细分领域仍需要与需求侧进行联合创新发展,这种创新和应用的推广,是生产力的又一次提升和解放。
传统钣金折弯行业亟待解决的问题
钣金行业传统折弯需要解决以下问题:
- 传统的折弯工艺无法实现多品种、小批量、快速切换。
- 钣金行业工件的高精度折弯精度较低,质量不稳定。
- 钣金折弯操作工稀缺,工人劳动强度大。
- 人员成本、安全隐患、工艺布局、管理和操作。
以上问题可以通过选择智能机器人折弯单元来解决,其中包括: 数控系统 按刹车 机器、6轴机器人及7轴导轨、上料站、磁性板材分选装置、预对位定位工作台、板材翻转机构、送料夹爪、成品堆叠、模具库、离线编程软件、参数化编程软件、二次开发折弯软件、及延伸服务。
机器人折弯单元的组成
以机器人为核心执行部件的数控液压折弯机是高度自动化的设备组合,具有高效率、高质量、高柔性等优点。
在柔性折弯机组中,选择合适的零部件组合可以为折弯效率和柔性提供更好的支撑。折弯精度取决于折弯机本身的精度、折弯机器人的定位精度以及机器人与折弯机的协同控制。
协同控制的难点在于机器人与折弯机的速度匹配,以及机器人支撑工件的运行轨迹,跟随效果不好会严重影响折弯角度成型结果和板面的平整度,进而影响成品质量。
如下图所示,标准的折弯加工单元是由机器人、数控液压折弯机为核心,夹爪、上料台、下料台、定位工作台、翻转架、夹爪更换装置、以及各类检测传感器等为辅助部件组成。
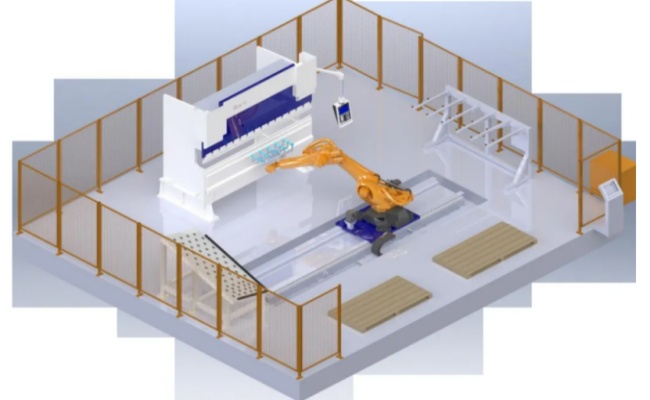
机器人折弯机的主要部件
夹爪是机器人用来代替人工抓取、放置工件的“手”,折弯机器人的夹爪通常由安装在金属框架上的多个吸盘组成。
上下料台通常采用叠放托盘,也有采用传送带或滚筒输送原材料和成品的单位。油性板容易发生粘连,造成一次抓取多张板。可在上料台旁安装各种分板装置(如磁力分板装置)及检测传感器,确保抓取的板为单张板。
定位工作台是一个带有挡边的倾斜平台,台面分布有略微凸起的钢球。机器人将钢板传送到定位台上,钢板在重力作用下自由滑动到边缘。由于定位台的位置和边缘固定,当机器人重新抓取板子时,板子和夹钳的位置就相对准确地固定了,为下一步折弯工序提供了参考。
翻转架是抓取装置的固定框架,当机器人需要从不同位置取取工件时,可以将工件放在翻转架上固定,然后机器人再在新的位置抓取工件。在一些特殊场合,也可用折弯机模具夹紧工件,改变抓取位置。
机器人折弯加工单元工作流程
折弯加工单元工作主要分为上料、取料、定心、翻转、弯曲、堆垛六个工序。
- 上料:采用人工将整叠需要加工的板材放置在上料平台上,并在上料平台上安装板材检测开关,防止板材全部加工完成后,机器人无法抓取托盘。
- 抓取:机器人运行至送料台位置,通过夹持器上安装的超声波传感器检测板子的高度,根据检测数据自动运行至合适位置抓取板子,抓取板子后通过测厚装置测量板子厚度,避免因一次抓取多张板子造成加工故障,测厚合格后即可对位。
- 定心:机器人运行至定位台位置,将板料放在定位台上进行精确定位,定位完成后再次抓取板料,准备折弯。
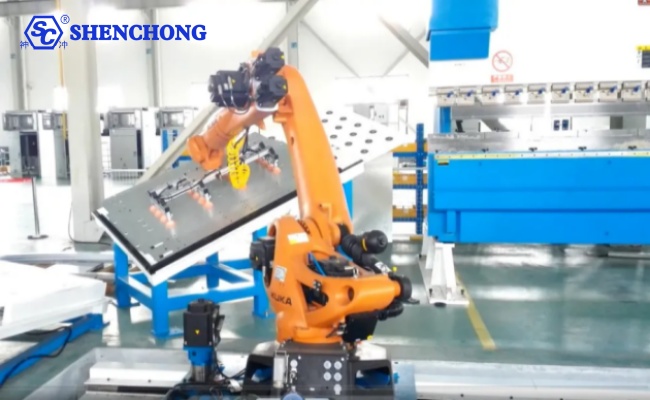
- 翻转:根据工艺要求确定是否使用翻转架,如需要,将机器人运行至翻转架位置,将板料放到翻转架上,松开板料并避让,翻转完成后抓取板料。
- 折弯:机器人运行到折弯机位置,将板料平铺到折弯机下模上,通过折弯机后指传感器准确定位。定位完成后,机器人向数控折弯机发出折弯信号,配合折弯机完成折弯动作,判断是否需要再次折弯,决定是否继续折弯。折弯是关键环节,折弯的技术难点在于机器人与折弯机的协调动作,即折弯跟随。当机器人夹紧或支撑板料折弯时,板料发生变形,机器人需要按照特定的轨迹算法跟随板料做圆弧运动,始终与板料保持相对固定的位置。
- 码垛:当机器人运行到卸料台位置时,因工件成型的不同,有各种码垛工艺动作,如常规矩阵码垛、单双层交叉码垛、正反向互锁码垛等。
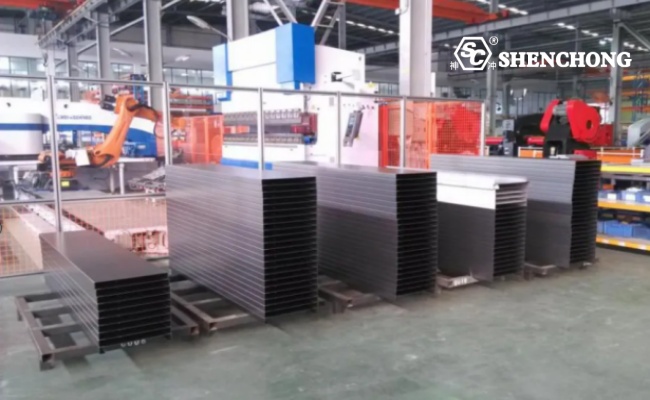
机器人折弯单元的技术特点
设计和开发
机器人折弯设计的研发注重用户的个性化需求和定制化,以客户需求和目标为首要任务。机器人折弯厂家在指定折弯机器人解决方案前,需要实现以下几点:
- 在每一个技术方案的制定过程中与客户进行详细的技术交流
- 对客户提供的工件加工图纸进行计算机模拟分析
- 对典型客户工件进行现场样品测试
- 对客户工件及工艺数据进行分类、分析。
在确认以上程序工作完成后,制定技术方案,技术方案及方案图纸经客户认可后,进行全面设计。
SC机器人折弯单元在材料、结构、传感器、实时补偿、随动、激光测角、自动换模、自动换夹爪、软件与控制、参数化编程、离线编程、生产管理软件、总线控制技术等方面均采用先进的三维设计,全部采用并使用国际一流品牌的软硬件。在折弯机机身设计方面,采用目前世界上最先进的设计软件和方法进行结构力学分析,凭借多年的设计经验和对折弯机架结构特点的了解,对各个受力点进行有限元分析,实现折弯机侧肩、上横梁、下横梁、下横梁的力学分析,充分保证了机床设计的合理性、可靠性、稳定性。
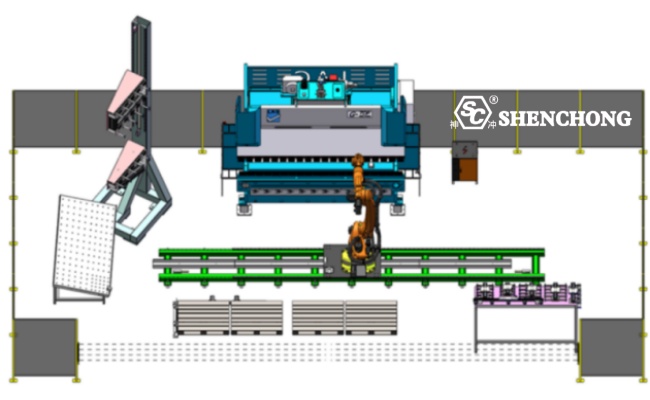
机器人折弯单元的设计旨在利用最新技术(软件、硬件)实现生产过程中的实时数据交换、补偿和折弯跟踪,实现智能化产品概念。主要解决的问题和取得的成果是:
(1)解决了定制钣金生产的工艺难点,解决了电梯行业多产品、小批量(5-10件)、多品种零件的快速切换生产难题。
(2)解决了产品质量不稳定、零件精度低、产品一致性差的问题。
(3)解决了生产效率低、生产布局和工艺路线不合理的问题。
(4)解决了手工折弯招工难、用工成本高、劳动强度大的问题。
(5)提高了折弯精度和自动化程度,增强了企业智能制造能力,增强了客户参观的视觉效果。
弯曲跟踪技术
在折弯过程中,SC机器人折弯单元可根据折弯机滑块的运行速度,对不同尺寸、不同板厚的工件进行自动跟踪和调整,该技术由SC申冲专用机器人折弯应用软件包实现。
激光角度测量技术
AMS角度测量系统采用闭环激光角度在线测量系统,在机器人自动折弯过程中,AMS的自动应用程序和内置激光测角装置的自动测角系统与SHENCHONG系统协同工作,保证折弯角度的准确性。其主要特点有:
(1)通过激光在线检测工件回弹后的弯曲角度。
(2)力检测系统自动计算弯曲回弹量。
(3)可根据下模宽度自动调整制件深度。
(4)通过闭环激光角度在线测量系统,保证折弯成品率达到99.5%以上。
机器人自动 (ATC) 夹持器更换和折弯机工具更换
机器人自动(ATC)夹持器和 折弯机模具 换模是钣金领域全智能自动化作业方式,由自动换模软件、机器人、模具库组成。配备自动换模系统后,精密折弯中心可自动随机折弯不同产品的小批量。利用自动换模功能,折弯机中的模具不再是限制因素,可实现全程无人操作加工。机器人自动机械装置的夹爪可非常快速地更换模具,随时可折弯下一批部件。
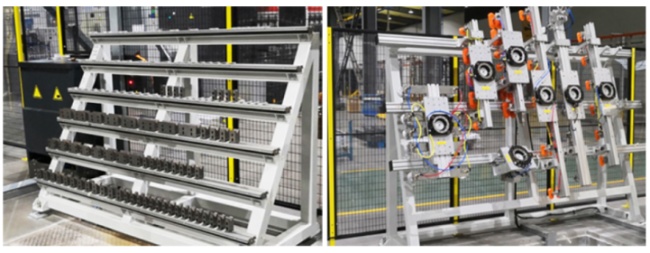
自动折弯机模具更换软件
自动换模软件的主要特点有:
(1)通过附件的图形界面,用户可以立即看到整个系统的当前状态。在界面的右侧,有一个表示模具状态的图形,它划分了这些模具的当前位置。
(2)整个界面包括折弯上冲区域、折弯下模区域、模具库,模具的显示跟随模具本身的尺寸和夹紧工位的位置。
(3)用不同颜色区分上下模,界面左上角有折弯机安装模具的详细说明,分为两部分,一部分是上模说明,一部分是下模说明,通过识别码和存在位置来描述夹紧的模具。
数控连续折弯技术
数控顺序折弯技术是一种高精度折弯控制系统,适用于对形位公差有要求的工件加工。该设备由一套两套带轨道的数控前推装置操作系统组成,位移通过传感器传递和反馈,整个操作由数控系统控制。控制轴由X3\X4和Z3\Z4组成。通过配置位移数控前推装置和折弯后挡料装置,即使工件尺寸达到±1mm,也能轻松保证关键尺寸在可控误差范围内,提高工件的精度和效率。
软件和控制
在机器人折弯单元中,我们应用了参数化编程软件、离线编程软件、生产管理软件,同时开发了二次折弯跟踪、自动换模、自动换夹爪、柔性堆垛、实时补偿、板边寻边、柔性翻转技术、总线控制技术等,可以极大的满足各类客户对钣金折弯的技术和软件需求。
机器人折弯问题及解决方案
当我们使用 机器人折弯机 对于钣金折弯,我们可能会遇到一些不知道如何解决或避免的小问题。下面SC SHENCHONG整理了机器人容易出现的五大问题,并提供了相应的解决方案。
长边压平后,有一个抬升。
原因分析:由于需要压平的边缘较长,压平时压不紧,导致端部被压平后又翘曲。这种情况与压平的位置有很大的关系,所以压平时一定要注意压平的位置。
- 弯曲之前,先将角弯曲,然后将其弄平。
- 逐步压平:首先按压末端,使压平边缘向下弯曲。压平底部。
更换折弯机模具时,加工尺寸将会改变。
原因分析:由于加工过程中工件受到向前的挤压力,使工件向前移动,造成前端的小前角尺寸L增大。
解决方案:
- 把图片中阴影部分磨掉。一般情况下,我们会尽量弥补差异。
- 将易模的自定位部分全部磨掉,然后使用固定规进行定位。
切割材料总尺寸(指展开)过小或过大,与圆面不匹配。
原因分析:
- 工程部署错误。
- 裁剪尺寸不正确。
解决方案:
根据偏差方向、上偏总量、折弯工具数量,计算每次折弯的分配量,计算出的分配量公差在公差范围内,则该工件为合格品。
若尺寸过大,可采用小V型槽进行加工。
若尺寸太小,可以采用较大的V型槽进行加工。
折弯机器人打孔与榫卯啮合后,产生膨胀或者开裂,或者榫卯配合不紧密,导致变形。
原因分析:
- 榫眼不紧的原因是由于孔的扩径不够。
- 变形是由于孔未对准或榫卯连接方法不正确造成的。
解决方案:
- 选择R角较大的冲头,拉、翻动时注意孔周围的毛刺。
- 增加沙拉孔的压力,加深它,并改用大R角的冲头。
- 改变榫卯连接方式及孔不对中的原因。
结论
随着机械行业整体水平的提升,钣金制造行业对生产设备的要求也会有一个新的台阶,最终能帮助用户解决问题的设备才会受到用户的青睐。SC机器人折弯单元拥有适合客户的生产方式,硬件与软件的最佳组合,适合多品种、小批量、切换快、无需首件试产的客户。