目录
在市场竞争日趋激烈、劳动力成本不断上升的背景下,市场对高效、节能、环保的钣金制造设备的要求越来越高,降低产品生产制造成本是企业不得不面对的问题,“节能降耗、绿色环保”成为企业首选主题。设备用电量已成为企业生产成本的重要组成部分,降低折弯机能耗成为企业降低成本、提高产品竞争力的有效途径之一。随着工业技术的不断发展和市场竞争的日趋激烈,传统电液数控折弯机因控制原理上的障碍,在节流、发热、无功功耗高等问题越来越突出。混合伺服折弯机将成为市场上最受欢迎的折弯机类型。本文将介绍混合伺服折弯机优势,并将该系列与传统液压折弯机进行比较。
电动伺服混合动力折弯机简介
混合伺服折弯机配备两个独立的不锈钢油箱,结构简洁紧凑,清洗方便,减少液压油的二次污染。为实现高效稳定的折弯效率,主油缸采用特殊的加速缸结构设计。数控系统通过两台伺服动力单元驱动油缸,通过光栅尺(或磁栅尺)的检测反馈控制折弯机油缸同步运行,实现工件的高精度加工。伺服混合折弯机具有高速、节能、低噪音、环保等特点。
伺服混合折弯机与电液同步数控折弯机
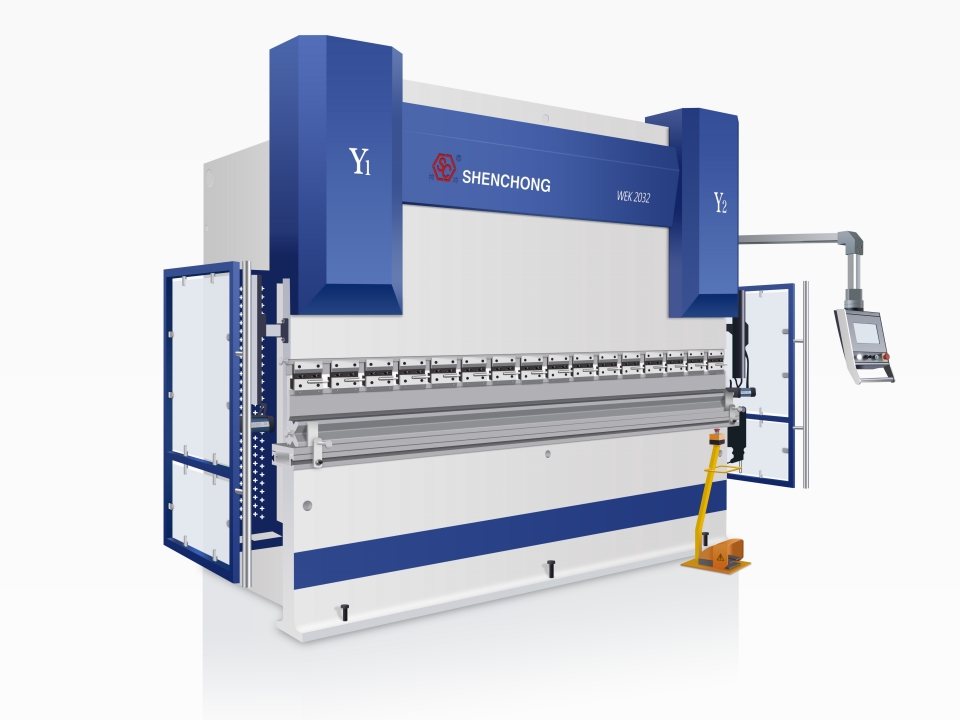
控制原理及比较
电液同步系统(阀控)的原理及存在的问题
油电混合数控系统原理(泵控)
油电混合数控(泵控)折弯机包括动力单元和与数控系统连接的控制阀组,动力单元包括伺服电机、与伺服电机连接的单向定量泵及独立的油箱,控制阀组包括溢流阀、卸荷阀、单向阀、换向阀、背压阀、提升阀、安全阀、充液阀。
通过数控系统控制动力单元伺服电机的转速,可以控制与其相连的油泵的排量,从而实现执行元件(油缸)的位移速度控制;通过数控系统设定伺服电机的扭矩,可以控制左、右执行元件(油缸)的输出力。
左、右执行机构(油缸)的位移读数通过位移传感器(光栅尺或磁栅尺)反馈给数控系统,数控系统经过比较后控制左、右动力单元,实现左、右执行机构(油缸)同步、定位的闭环控制,位移传感器形成内部反馈环,提高系统的控制精度。
独特的生长圆柱结构
传统电液同步数控折弯机采用单作用活塞缸作为主油缸,主要依靠滑块自重实现快速下行,难以进一步实现较高的运行速度。通过将单作用活塞缸内部设计结构改为增速缸,可实现缸体高速下行,不受滑块自重的制约,大大提高折弯效率。
这 混合伺服折弯机 同步性更好,真正节能,结构简单,速度更快,单向定量泵与增速缸在双伺服油电混合数控(泵控)系统中的应用是申冲双伺服油电混合系统的最大特点,单向定量泵比双向定量泵具有更好的经济性,而增速缸则具有稳定、高效的特性。
CNC 混合伺服折弯机优势(泵控制)
- 效率:设备在90%负载下运行2小时,提高效率30%至50%。
- 节能效果:设备以90%负载运行2小时,节能效果由28%增加到54%。
- 精度:设备在90%负载下运行2小时,Y轴行走误差小,任意位置精度平均提高5倍。
- 噪音低:设备在90%负载下运行2小时,噪音降低10-12分贝,大大优化了工作环境。
- 环保:设备在90%负载下运行2小时,减少液压油量50%至80%。
- 温度控制:设备在90%负载下运行2小时,油温控制优越,有利于机器整体运行。
- 外观:安装简洁、大方、美观,无外部管线。
通过以上两种控制方式的比较,我们可以明显的看到混合油电数控(泵控)系统具有高效、节能、低噪音、环保的特点。
结论
随着越来越多应用经验的积累和技术的改进优化,无锡神冲锻压机床有限公司生产制造的油电混合数控折弯机已广泛应用于钣金生产制造企业,主要服务于船舶制造、轨道交通、电气开关、建筑装饰、5G通讯等行业。
混合式油电数控折弯机属于节能环保产品,其技术优越性在实际生产应用中得到了充分体现。既响应了国家建设节能环保绿色社会环境的号召,又满足了企业越来越高精度、高效率的生产需求,深受用户的好评。未来将有部分替代传统数控折弯机的趋势,市场前景十分广阔。