目录
在生产制造过程中,钣金件折弯时可能会出现各种折弯质量问题,影响生产效率的提高和产品质量的稳定性。本文阐述生产实践中常见的折弯切割质量问题,分析问题产生的原因,提出解决办法,为后续生产实践中出现类似问题提供经验和借鉴。
介绍
钣金折弯是使用配备有 数控折弯机 将金属板料弯曲成各种所需几何截面形状的工件。弯曲工艺的合理性直接影响产品最终成形的尺寸和外观。合理选择弯曲模具对产品的最终成形至关重要。
在实际生产过程中,由于产品尺寸的不确定性以及产品种类的多样性,在冷加工工件折弯过程中经常会遇到尺寸干扰、模具角度不匹配等问题,给生产带来很大的困难。折弯过程中由于受到产品尺寸、形状、材料、模具、设备、辅助设施等因素的影响,可能会出现各种质量问题,影响生产效率和产品质量的稳定性。因此,解决和避免这些折弯质量问题的发生尤为重要。本文主要对生产实践中板料折弯常见的质量问题进行总结和描述,并结合生产经验分析其原因,提出解决办法。
常见的折弯质量问题
弯曲和开裂
弯曲开裂是指材料在经过切割、剪切或冲压加工后,边缘处经常出现毛刺或小裂纹,在弯曲时易形成应力集中,从而产生开裂的现象。机车零件U型加强槽在弯曲后拐角处开裂,如图1所示。
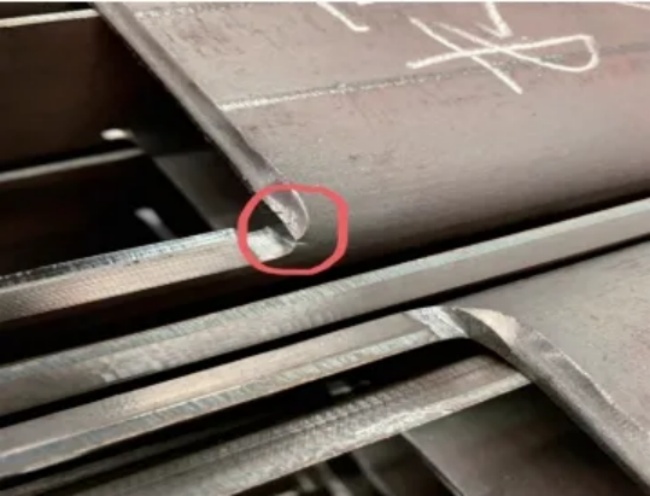
图1 弯曲和开裂
弯曲、开裂的主要原因有:
- 零件边缘有未清理的毛刺。
- 弯曲方向与金属板的轧制方向平行。
- 钣金折弯半径太小。
在生产制造过程中,需要根据具体情况对弯曲、开裂现象进行处理。针对图1中的弯曲、开裂问题,可以采取增加工艺孔或者工艺槽的方法来解决,如图2所示。
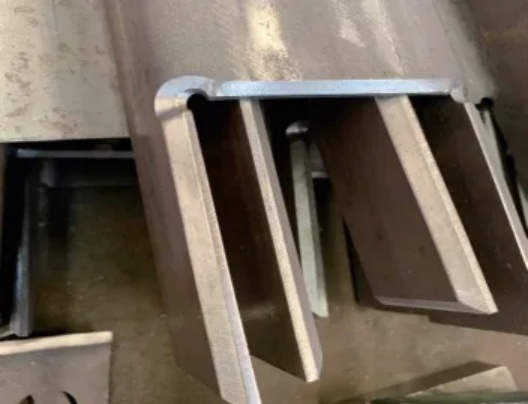
图 2:添加工艺孔
弯曲干扰
折弯干涉主要针对二次以上折弯的产品,折弯边与模具或设备发生碰撞,导致无法正常成形。折弯干涉主要受零件形状、尺寸、模具的影响,主要由折弯件本身的设计结构、所选折弯顺序、所选折弯模具等因素造成。因此,主要解决方法有:
- 制作新的或更换模具(如弯曲刀模)。
- 改造弯曲模具(如对局部零件进行机械加工)。
- 调整折弯顺序(如反向变形法)。
- 改变零件折弯尺寸。例如上海地铁18号线底盘附件线槽安装支架采用U型槽钢,中宽100mm,边高80mm,折弯半径15mm。根据车间现有的模具进行模拟折弯,产生折弯干涉。
针对此干涉现象,对折弯上模采取局部机械加工的方法(见图3),在现有R15mm直刀上模(L=800mm)上沿中线切出一个140mm×48mm的缺口(见图4),结合模拟折弯干涉位置确定缺口位置,不影响其原有功能。修改折弯模具后,成功解决了折弯干涉问题。
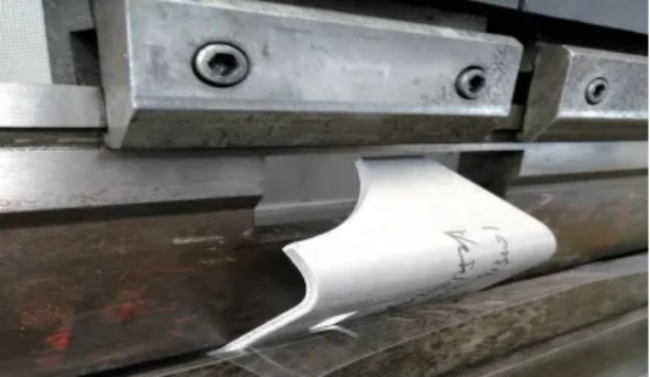
图3:上模加工后折弯
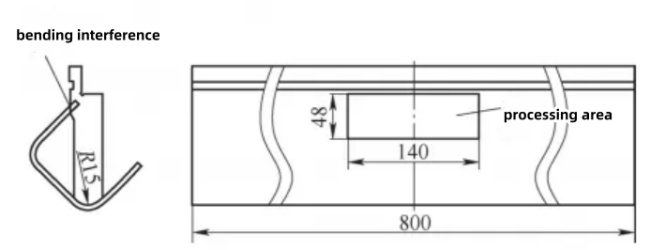
图4:弯曲干扰,确定加工区域
弯曲压痕
折弯压痕是板材在逐渐与凹模V型槽内表面接触的过程中产生摩擦,导致板材表面留下明显痕迹的现象。对于一些表面要求较高的配件,传统的折弯无法满足产品质量要求,折弯压痕(见图5)无法满足下道工序的要求。
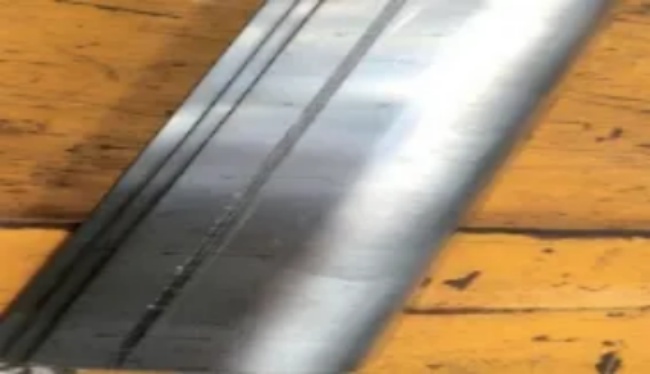
图5:弯曲压痕
折弯压痕主要受板料硬度及下模结构影响,板料硬度越高,抵抗塑性变形的能力越大,材料越难发生塑性变形,越容易产生压痕。常用板料折弯压痕的概率为:铝>碳钢>不锈钢。折弯模开口宽度越大,折弯压痕宽度越大,压痕深度越浅。下模开口肩部R尺寸越大,压痕深度越浅。
解决折弯压痕问题除了改善材料硬度、下模结构外,还可以采用防压痕橡胶垫、滚珠型折弯下模等方式。防压痕橡胶垫主要依靠物理隔离,减少压痕的发生,如图6所示。滚珠型折弯模具将传统折弯模具所需的挤压摩擦转化为滚动摩擦,减少了摩擦,最大程度减少了对产品的损伤,如图7所示。
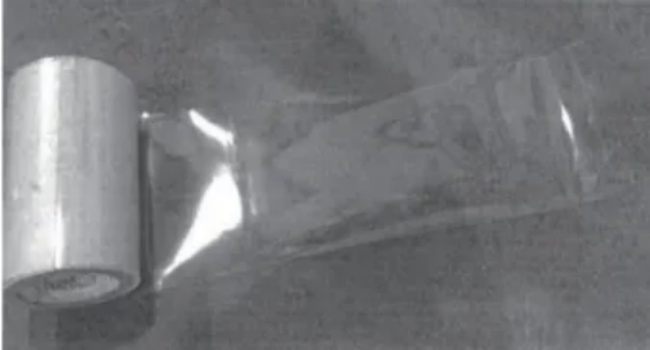
图 6:防压痕橡胶垫
图7:球弯下模
弯曲回弹
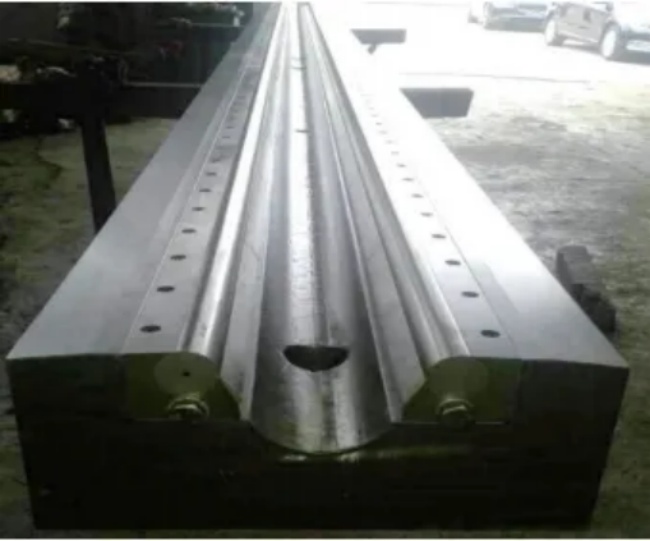
弯曲加工过程中,材料同时发生塑性变形和弹性变形,当工件离开弯曲模具时,发生弹性回复,造成弯曲件形状、尺寸与载荷不一致,称为弯曲回弹。 弯曲回弹 是造成折弯角度不足的主要原因之一。影响回弹的主要因素有板料的力学性能和折弯变形的条件。回弹值的大小与板料的屈服强度成正比,与弹性模量成反比。折弯件的相对折弯半径(折弯半径与板厚之比R/t)越小,折弯回弹值越小。折弯件的形状也会影响折弯回弹值的大小,一般U形件的回弹值比V形件小。
克服弯曲回弹的主要方法是角度补偿法,一般采用在弯曲模具上做出等于回弹角度的斜度的方法,可以有效地平衡弯曲回弹的影响。如图8所示,采用斜度为80°的弯曲模具,可以顺利地弯曲出弯曲角度为90°的工件。
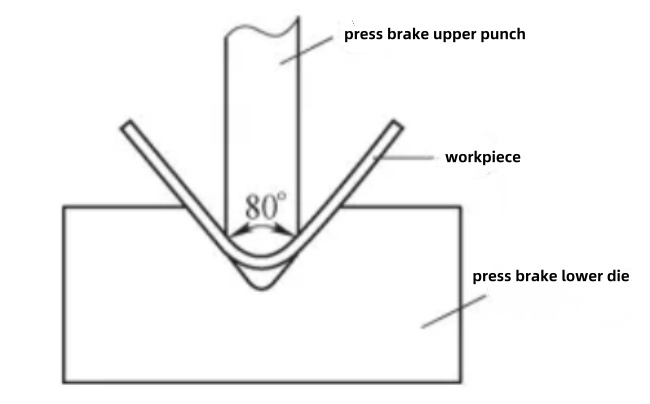
图8:弯曲回弹补偿
由于影响弯曲回弹的因素很多,准确计算回弹值十分困难,通过试模修正和经验积累,掌握回弹规律,采用适当的补偿,在模具结构等方面采取克服回弹的措施是保证产品质量的有效方法。
折弯滑块材质
折弯滑落是指被折弯的工件在下模槽上没有完整有效的支撑点,导致工件容易发生打滑,折弯不能正确定位的现象。
滑动材料弯曲的主要原因有以下几点。
- 当下模宽度太大,折弯尺寸小于下模宽度的一半时,就会产生滑动。
- 当工件受其形状、尺寸影响,而模板定位尺寸过短或无有效的模板定位边时,就会产生弯曲、滑动现象。
解决材料弯曲滑动问题的方法主要有两种。
- 方法1、选择合适的折弯模具,一般选择4-6倍板厚的模具宽度进行折弯。
- 方法二、采用增加模板或工艺边的方法,可以解决由于折弯定位不好导致材料滑移的问题。一般折弯都是通过工件直边进行定位,需要两个端面与折弯模板接触进行定位。但在实际生产过程中,存在产品模板边太短或没有有效定位边的情况,导致无法完成折弯定位。解决方法为:
- 当板厚t≤6mm时,应增加一条工艺边用于定位,工艺边延伸的位置应与零件端边平齐。交界处应采用激光切割,以方便折弯作业完成后打磨、消除。
- 当板厚t大于6mm时,可以切一块模板来定位,模板厚度可等于或略小于工件厚度。两种定位方法都可以解决弯曲和滑料的问题。
大弧折弯
在生产制造过程中,经常会遇到工件折弯半径较大而车间没有与之配套的大圆弧模具的情况。这种情况下,整体成形模具或大圆弧模具生产周期较长且成本过高,而采用小圆弧多道次折弯成形技术成本较低,适用性较广。例如,在超级巴士2.0项目中,有一个立板加三块竖板的部件,其折弯半径为125mm,折弯角度为90°,如图9所示。由于车间没有相应的折弯模具,因此可以采用多次折弯工艺。首先用3D软件建模排版,在R125mm位置进行折弯。建模完成后,软件自动展开2D平板图。通过在软件中输入45mm的折弯半径,对比多次数据输入,确认采用8道切口折弯即可保证圆弧段。然后生成每次切割的折弯数据(折弯角度、折弯线位置长度),如图10所示。最后根据折弯数据进行现场试折弯,如图11所示。
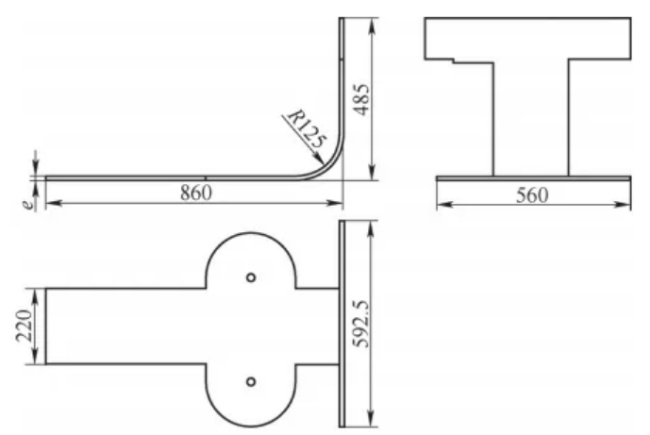
图9:弧形工件
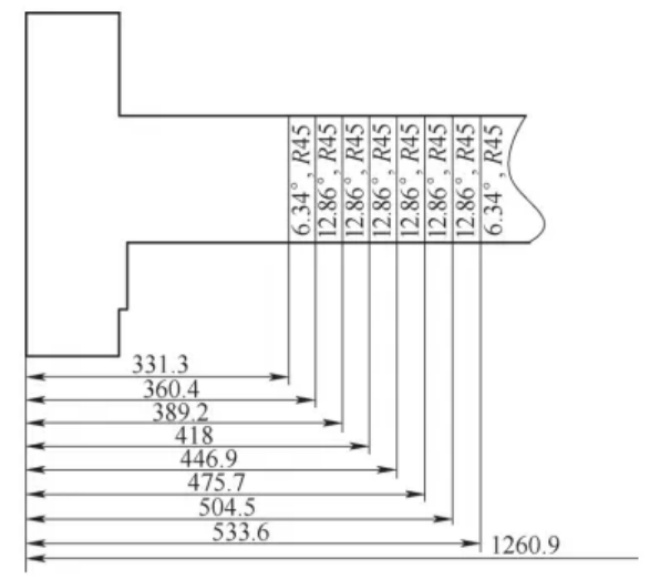
图10:展开图及折弯线位置

图11:现场试模折弯
弯曲凸出
折弯凸起是指金属材料在钣金折弯转角处两侧因材料压缩而凸起,导致宽度大于原尺寸的现象。折弯凸起的大小一般与配件板厚、折弯半径有关,板厚越厚,折弯半径越小,凸起越明显。
为了避免这种折弯质量问题,可以在绘制折弯展开图时,在折弯线两侧增加工艺缺口,如图12所示。工艺缺口一般采用圆弧形式,直径至少为工件厚度的1.5倍,目的是为了抵消折弯凸起,有效解决折弯凸起问题。对于已经产生折弯凸起的工件,一般采用手工打磨进行处理。
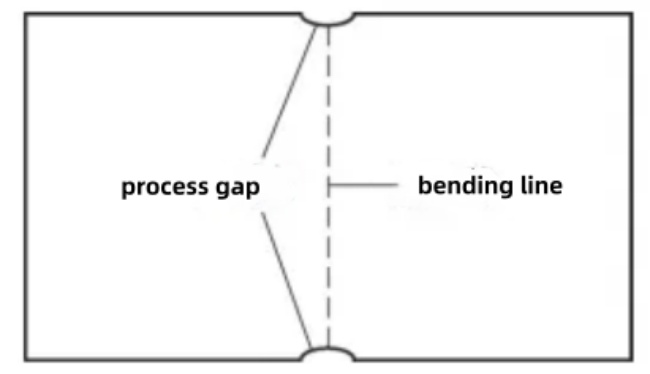
图 12:流程差距
结论
需要注意的是,以上列举的生产实践中常见的折弯下料质量问题,均未考虑人为或设备因素的影响(如展开尺寸不正确、折弯参数选择不正确、设备老化等)。在生产实践中,应根据设备性能、产品尺寸、材料特性等选择合适的折弯工艺参数,并严格按照操作规范执行。我们不仅需要综合考虑工程进度、成本、质量等各方面因素的影响,采取合适的方法解决折弯质量问题,还需要积累经验,在工艺分析阶段预测折弯问题的发生及其影响,并采取针对性的措施进行预防。本文列举了几种常见的折弯质量问题及其解决方法,希望能为业内同仁提供一些参考和指导。