目录
激光焊接概述
激光焊接作为一种现代焊接技术,具有熔深深、速度快、变形小、功率密度高、不受磁场影响等优点,广泛应用于汽车、船舶、航空航天等高端精密制造领域。本文主要介绍激光焊接的原理、优缺点,帮助没有使用过激光焊接的人对这项焊接技术有一个初步的了解。
激光焊接原理
激光焊接可采用连续或脉冲激光束来实现,根据激光焊接的原理可分为热传导焊接和激光深熔焊接。
- 功率密度低于104~105W/cm2属于热传导焊接,熔深较浅,焊接速度较慢;激光焊接的原理是:激光辐射加热被加工表面,通过热传导将表面热量引导到内部进行扩散,通过控制激光脉冲的宽度、能量、功率、频率等参数,使工件熔化,形成特定的熔池。
- 激光深熔焊接一般采用连续的激光束连接材料,其冶金物理过程与电子束焊接十分相似。其能量转换机理是通过小孔来实现的。在高功率密度激光的照射下,材料蒸发形成小孔,小孔内犹如黑体般充满蒸气,几乎吸收了全部的入射光能。热量从高温腔体外壁传递过来,使腔体周围的金属熔化。在光束的照射下,壁面材料不断蒸发产生高温蒸汽。孔壁外部由液体流动形成的壁层表面张力与孔腔内部不断产生的蒸汽压力处于不断的平衡状态。光束不断进入小孔,小孔始终处于稳定的流动状态。环绕孔壁的熔融金属随先导光束向前移动,填充小孔留下的缝隙并随之冷凝,从而形成焊缝。
激光焊接的应用领域
激光焊接已广泛应用于各个行业,例如:
- 汽车行业:激光焊接可实现汽车零部件的高效精密连接,提高生产率和质量,降低成本和污染。激光焊接可用于汽车车身、底盘、发动机、变速箱、排气管、安全气囊、仪表板等零部件的焊接。例如,激光焊接可实现汽车后尾门的一体化设计,减少零部件数量和重量,提高刚度和强度,增强美观性和安全性。
- 船舶制造:激光焊接可用于船板连接,解决传统焊接中出现的翘曲变形问题,提高焊缝质量和强度,降低材料消耗和人工成本。激光焊接可用于船舶结构、甲板、舱壁、舱底、管线等部件的焊接。例如,激光焊接可实现大型船舶结构的快速组装,缩短建造周期,提高生产效率。
- 家居领域:激光焊接可用于全铝家居制造,实现铝合金型材无缝连接,提升家居美观度和耐用度,满足环保健康需求。激光焊接可用于全铝衣柜、全铝书柜、全铝鞋柜等家居产品的生产。如全铝家居激光焊接可实现零甲醛、零污染、可回收利用,打造绿色时尚家居新概念。
激光焊接的分类
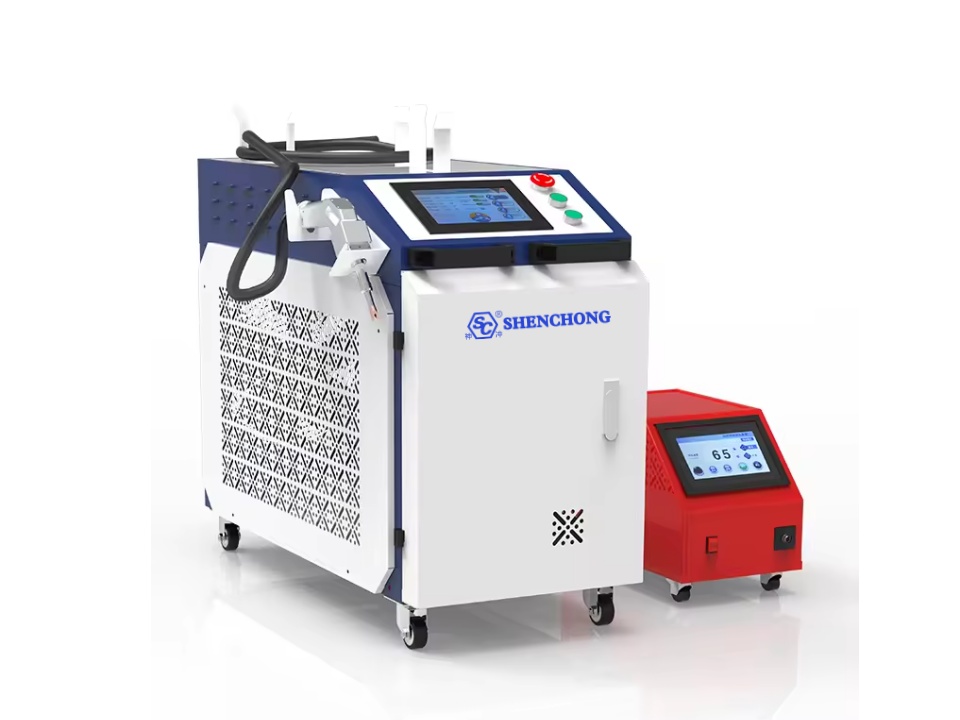
根据激光能量输出方式不同,激光焊接可分为连续激光焊接和脉冲激光焊接。连续激光焊接在焊接过程中形成连续不间断的焊缝形貌,而脉冲激光焊接由于向工件表面输入的能量是不连续的,因此在焊接工件表面形成圆形焊点。根据激光参数的变化可获得不同的焊缝形貌。根据激光聚焦斑的功率密度不同,激光焊接可分为热导焊接和深熔焊接。
1.激光热导焊接
激光热导焊点在工件表面的功率密度较低,一般小于105W/cm2。激光将能量传递到被焊工件表面,将金属表面加热到熔点与沸点之间的温度。金属材料表面将吸收的光能转化为热能,使金属表面温度不断上升而熔化。然后,热能通过热传导传递到金属内部,熔化面积逐渐扩大。冷却后,形成焊接点或焊缝。这种焊接原理类似于钨极惰性气体保护电弧焊(TIG),称为热导焊接。
2、激光深熔焊接(小孔焊接)
当施加在金属表面的激光功率密度大于105W/cm2时,大功率激光束作用于金属材料表面,引起局部熔化,形成“小孔”,激光束通过“小孔”透入熔池内部,而金属在小孔前方熔化,熔融金属绕过小孔向后流动,重新凝固,形成焊缝。
激光焊接的优点和缺点
激光焊接是一种利用高能量密度激光束作为热源的高效精密焊接方法。激光焊接是激光材料加工技术应用的重要方面之一,广泛应用于汽车、航空航天、电子、医疗等领域。具有速度快、质量高、灵活性高、绿色环保等优点。
那么,激光焊接相比传统焊接方式究竟有哪些优势呢?激光焊接过程中会遇到哪些困难,又该如何解决?激光焊接常见的应用领域又有哪些呢?
激光焊接的优点
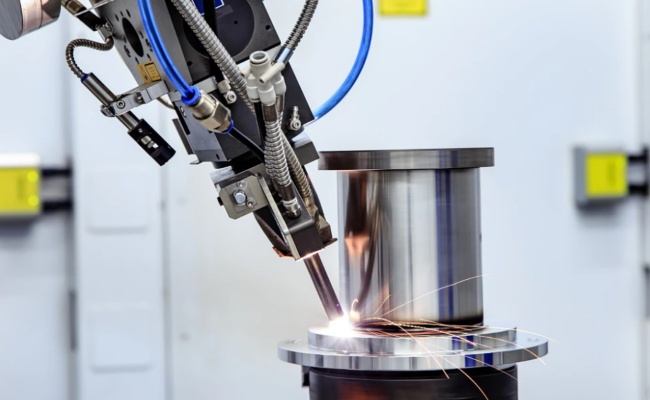
与传统焊接方法相比,激光焊接具有以下优点:
- 速度快、深度深、变形小。激光焊接能量密度高,加热和冷却速度快,热影响区小,焊接应力和变形小。激光焊接可实现高纵横比焊缝,最高可达10:1。
- 非接触加工,灵活性高。激光焊接不需要接触工件,也不需要电极或填充材料,可以减少污染和损失。激光焊接可以通过光学元件进行传输和变换,易于与机器人配合,实现自动化和多工位加工。激光焊接还可以在室温或特殊条件下进行,适合焊接难以接触的部件或难熔材料。
- 质量高、性能好。激光焊接由于热输入小、冷却速度快,可以减少气孔、裂纹等缺陷,提高焊缝的致密性和强度。激光焊接还可以实现不同金属或异种材料的连接,改善组织和性能。
- 绿色环保,安全无污染。激光焊接不产生有害气体和噪音,不受电场、磁场影响,对人体健康和环境无害。
激光焊接的难点及解决方法
虽然激光焊接具有很多优点,但焊接时仍然存在一些问题:
- 焊接飞溅:是指焊接完成后,材料表面出现许多金属颗粒,粘附在材料表面。这会影响焊缝的表面质量,也会污染和损坏镜片。飞溅的原因可能是材料表面不干净,有油污或污染物,或镀锌层挥发。
解决的办法是焊前清理材料表面,适当降低焊接能量,尽量减少飞溅。
- 裂纹:指激光连续焊接产生的热裂纹,如结晶裂纹、液化裂纹等,产生裂纹的主要原因是焊缝在未充分凝固之前,收缩力过大。
解决的方法是采用填丝、预热等措施,减少或消除裂纹。
- 气孔:是指焊缝表面出现的孔隙。气孔形成的原因可能是激光焊接熔池深而窄,冷却速度快,液态熔池中产生的气体来不及及时逸出;或者是焊缝表面清理不彻底,或者是镀锌板中锌蒸气蒸发。
解决方法是清理焊缝表面,改善锌在加热时的挥发,调整吹气方向等。
- 咬边:指焊缝与母材结合不良,产生深度大于0.5mm的坡口,总长度大于焊缝长度的10%,或长度大于验收标准要求。咬边产生的原因可能是焊接速度太快,阻碍了液态金属在小孔背面的重新分布;或者接头装配间隙过大,导致填充过程中熔融金属减少;或者激光焊接结束时能量下降时间过快,导致小孔塌陷。
解决方案是控制匹配 激光焊接机 加工能力和速度以避免咬边;抛光、清洁和修复检查中发现的咬边。
结论
激光焊接是一种高精度、高效率的焊接技术,具有广阔的应用前景。不同的焊接方式和应用场景需要选择不同的激光焊接方式才能达到最佳的焊接效果。激光焊接技术还在不断发展和创新,未来还会有更多新型激光器和工艺涌现,为各行业提供更高质量、更高效率、更低成本的焊接解决方案。