Table of Contents
Press brake axis is an integral part of bending machine work. When it comes to CNC press brake, we often hear people talking about professional words such as the X axis, Y axis, Z axis, R axis, etc. Many users who come into contact with the press brake for the first time will need to distinguish between these axes and learn how to distinguish them.
From simple bends to complex designs, these axes control the movements and adjustments that turn raw materials into perfectly formed parts. Whether you’re using a straightforward 2-axis machine or a cutting-edge multi-axis CNC press brake, understanding how these systems work is key to getting consistent, high-quality results.
Every press brake axis plays a part in shaping your workpiece by guiding backgauge movement, positioning, and adjustments in perfect harmony. By mastering their role, you not only improve accuracy and productivity but also reduce waste and handle diverse materials with ease.
This article helps you understand what is press brake axis and how to choose them for your new machine.
Introduce To Press Brake Axis
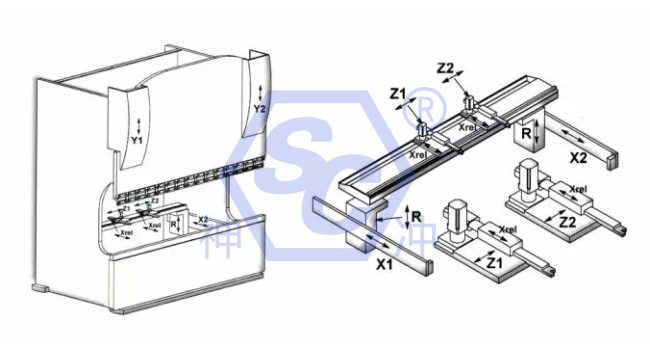
We often see the X-axis, Y-axis, Z-axis, and R-axis in machine specification. What are the X-axis and Y-axis? What are their functions?
On a CNC press brake machine, the various axes control the movement of different parts in different directions. The press brake can use these axes to adjust the size and angle of the bend.
What Are The Functions Of Press Brake Axis?
A press brake axis refers to the controlled movement paths within a press brake machine that allow precise adjustments during the bending process. These axes control how the ram, back gauge, and other components move to position the sheet metal accurately and achieve the desired bending angle. Each axis serves a specific purpose, contributing to the overall functionality and versatility of the press brake.
Modern press brakes typically use a combination of axes to manage tasks such as positioning the workpiece, aligning the back gauge fingers, and compensating for machine deflection. For instance, the Y-axis controls the vertical movement of the ram, determining the depth of the bend. The X-axis governs the horizontal movement of the back gauge, ensuring proper positioning of the sheet metal. Additional axes, such as the R-axis and Z-axes, enable adjustments for flange height and lateral positioning, respectively. Some machines also include a V-axis for crowning compensation, which counteracts deflection in the bed of the machine.
In CNC press brakes, these axes are managed through a computerized control system, allowing for automatic adjustments and enhanced precision.
Y-axis
What is the Y-axis of the press brake? We can find the Y axis on various CNC bending machines, usually divided into Y1-axis and Y2-axis. The Y-axis of the CNC press brake machine can control the stroke of the cylinders on both sides, that is, the up and down movement of the press brake ram.
What is the role of the Y-axis? The Y-axis controls the movement of the ram, which applies the force required for bending. For CNC press brake machines, Y1, Y2 axis work independently on both sides of the top of the machine. Y-axis makes the descent of the ram very smooth, uniform, and stable. Y1,Y2 controlled by the CNC controller, which can ensure the perfect synchronicity.
X-axis
The X-axis is used to control the back-and-forth movement of the back gauge. So, what is the role of the X-axis and the back gauge?
The X-axis manages the horizontal positioning of the back gauge, a crucial element for accuracy during bending. This axis ensures that the sheet metal is placed correctly relative to the punch and die, enabling consistent bending angles across multiple parts.
When we need to measure the flange length of a bending workpiece, the X-axis of the press brake is useful. We only need to contact the metal plate with the backstop to determine the exact bending point and perform the bending operation.
Like the Y-axis of the press brake, the X-axis of the CNC bending machine also includes the X1-axis and X2-axis, which are the front and rear movement axes of the left and right rear stop, respectively.
R-axis
The R-axis of the press brake is similar to the X-axis and can control the up-and-down movement of the back gauge. It is ideal for bending work of inclined and customized workpieces. If you want to put an already turned workpiece into the press brake for re-bending, and the workpiece has a height difference, the R-axis will be especially important. Adjustments to the R-axis help maintain the desired bend quality, even when working with non-standard workpieces.
The R1-axis and the R2-axis are the up and down moving axes of the left and right back gauge fingers, respectively.
Z-axis
The CNC bending machine’s Z-axis controls the back gauge’s left-and-right movement. The Z-axis also includes the Z1-axis and Z2-axis, which are the left and right moving axes of the left and right rear gear, respectively, and both can be independently programmed.
If you need to bend a small workpiece or adjust the width of the back gauge finger frequently, the independently programmable Z-axis will be your time-saving and labor-saving helper. Z axis is especially useful for creating bends with varying positions or working on asymmetrical workpieces.
V-axis
The V-axis of the press brake is the crowning compensation of the work table. If the workpiece you need to bend is heavy, the table crowning will become a severe problem. press brake V axis can help you reduce this risk by symmetrically adjusting the beam of light. It alters the entire shaft of light but focuses more on the bending resistance in the middle.
To obtain the highest accuracy, most CNC press brake manufacturers will directly install the crowning compensation of the worktable during the production process of the press brake.
How To Understand The Number Of The Cnc Press Brake Axis?
What is a 2 axis CNC press brake? The torque bar synchronous press brake with a numerical control system usually has two axes, namely: X-axis and Y-axis. The CNC electro-hydraulic servo press brake has more axes, including 6+1 axes, 8+1 axes, and even up to 18 axes.
In the configuration of the CNC bending machine, we often see 3 + 1, 4 + 1, 6 + 1, and 8 + 1… what do these represent?
- 3+1 axis: Y1, Y2, X, + V;
- 4+1 axis: Y1, Y2, X, R, +V;
- 6+1 axis: Y1, Y2, X, R, Z1, Z2, +V;
- 8+1 axis: Y1, Y2, X1, X2, R1, R2, Z1, Z2, +V;
The general standard CNC press brake is the 4 + 1 axis press brake. The 3 + 1 axis press brake is usually a low-profile press brake. The 6 + 1 axis and 8 + 1 axis press brakes, also known as multi-axis CNC press brakes, have higher performance. The higher the high-end, multi-axis numerical control press brake usually has more axes.
Common Axis Configurations and Their Meanings
Understanding axis configurations is key to choosing the right press brake for your needs. Each configuration is tailored to specific bending tasks, providing varying degrees of precision and flexibility.
2-Axis: Y and X Axes: This basic configuration includes the Y-axis for vertical movement of the ram and the X-axis for horizontal adjustment of the back gauge. It is ideal for simple bending operations and smaller workpieces.
3+1 Axis: Y1, Y2, X, and V: This setup adds independent control of Y1 and Y2 axes for precise ram movement, along with the V-axis for crowning compensation. It is suitable for applications requiring consistent bending angles across the length of the sheet.
4+1 Axis: Y1, Y2, X, R, and V: The R-axis allows vertical adjustment of the back gauge fingers, making this configuration more versatile. It is well-suited for handling materials with varying flange lengths or thicknesses.
6+1 Axis: Y1, Y2, X, R, Z1, Z2, and V: With the addition of Z1 and Z2 axes, this setup enables lateral movement of the back gauge fingers. It is ideal for producing complex parts with multiple bends or asymmetrical designs.
8+1 Axis: Y1, Y2, X1, X2, R1, R2, Z1, Z2, and V: This advanced configuration includes independent control of additional X and R axes, providing unparalleled flexibility and precision. It is designed for high-end manufacturing processes requiring intricate bending tasks and large-scale production.
How To Choose The Number Of Axes Of The CNC Bending Machine?
When most customers buy press brakes, the number of axes is critical in the configuration discussion. Because the number of axes of the press brake determines the machining capacity of the machine, in short, the more axes of the press brake, the more complex the workpiece can be machined.
At the same time, the more axes of the press brakes, the higher the machine’s price. Therefore, we need to make reasonable purchases according to demand and budget.
How Many Axes Should A Press Brake Have?
The number of axes a press brake should have depends on your specific operational needs, including the complexity of parts, material types, and production volumes. While a 2-axis machine is suitable for basic tasks, more advanced configurations with multiple axes are often required for precision manufacturing and complex geometries.
A 3+1 axis press brake, which includes Y1, Y2, X, and V axes, provides enhanced accuracy and consistency. The independent control of Y1 and Y2 ensures precise ram movement, while the V-axis compensates for bed deflection during bending. This setup is ideal for applications requiring uniform angles across the length of the sheet.
For operations involving intricate bends or varying flange lengths, a 4+1 axis press brake is recommended. The inclusion of the R-axis allows for vertical adjustment of the back gauge fingers, enabling more flexibility. Adding Z1 and Z2 axes to create a 6+1 configuration further improves the machine’s ability to handle asymmetrical parts or workpieces with complex dimensions.
High-end manufacturing processes may require an 8+1 axis press brake, which includes additional control over back gauge positioning and angled sheet placement. This configuration supports advanced operations, including multi-step bending and handling of large workpieces with tight tolerances.
Determining Your Press Brake Axis Requirements
Several factors influence how many axes your press brake needs. Evaluating these ensures you select a machine suited to your production goals.
- Bending Complexity: The complexity of your bending operations is the first consideration. Simple 90-degree bends require fewer axes, while intricate designs with multiple angles or tight tolerances demand advanced configurations.
- Precision and Accuracy Requirements: Higher precision demands more axes for independent control, such as Y1 and Y2 for ram movement. These ensure uniform bends and minimize errors across the sheet’s length.
- Material Specifications: Material type, thickness, and length affect the required axes. Thicker materials may need crowning (V-axis) to counter deflection, while longer sheets benefit from Z1 and Z2 axes for lateral adjustments.
- Back Gauge Requirements: The back gauge system’s flexibility determines the range of workpieces you can handle. Additional axes like R, Z1, and Z2 enhance the back gauge’s capability to accommodate varying flange lengths and positions.
- Tooling Considerations: If your operation uses specialized or multi-stage tooling, more axes can help manage the tooling’s alignment and compatibility with different bending processes.
- Automation and Software Integration: CNC press brakes with advanced axis controls allow for automation and programming, reducing manual intervention and increasing production efficiency. Software integration supports better axis synchronization.
- Space and Layout Constraints: The physical layout of your workshop might limit the size or complexity of the press brake. Compact machines with fewer axes can still handle many tasks but may lack the versatility of larger models.
What Is A 2-Axis Press Brake?
A 2-axis press brake is the simplest configuration, equipped with the Y-axis and X-axis. 2 axis press brake is torsion bar synchronous press brake. The Y-axis controls the vertical movement of the ram, which applies pressure to bend the sheet metal, while the X-axis manages the horizontal positioning of the back gauge to align the workpiece accurately.
This configuration is ideal for straightforward bending tasks, such as creating uniform angles on smaller workpieces. It is a cost-effective solution for operations that involve basic parts and minimal adjustments. However, the lack of additional axes limits flexibility, making it unsuitable for projects requiring intricate bends, varying flange lengths, or complex geometries.
What Is a 3-Axis Press Brake?
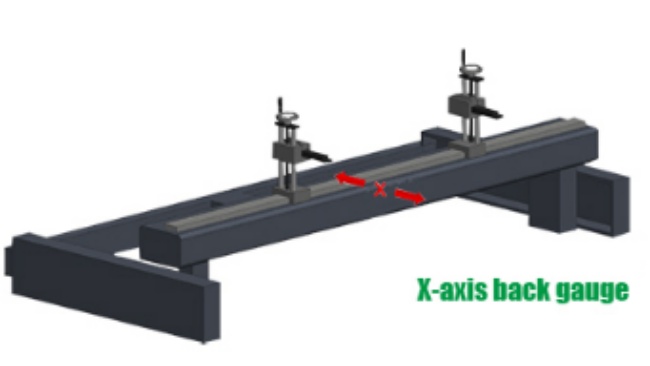
A 3-axis press brake adds more functionality by including the V-axis alongside the Y-axis and X-axis. The V-axis is responsible for crowning, which compensates for any deflection in the machine bed during the bending process. This feature ensures consistent bending angles across the entire sheet, improving accuracy and reliability.
This setup is well-suited for manufacturers who need enhanced precision without moving into the complexity of higher-axis machines. It supports operations involving slightly thicker materials or larger workpieces, where maintaining uniform angles becomes critical.
What Is a 4-Axis Press Brake?
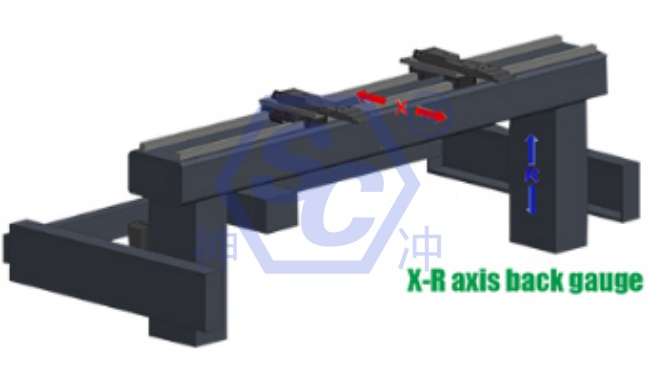
A 4-axis press brake builds upon the 3-axis configuration by incorporating the R-axis, which controls the vertical movement of the back gauge fingers. This additional control allows for adjustments to accommodate varying flange heights and material thicknesses. With the R-axis, the back gauge can be positioned more flexibly, enabling the machine to handle a wider range of bending tasks.
This configuration is ideal for operations requiring versatility. For example, if you work with parts that have complex shapes or require multiple bends with varying depths, the 4-axis machine ensures precise alignment and positioning. It is also suitable for mid-scale production environments where flexibility and precision are equally important.
What Is a 6-Axis Press Brake?
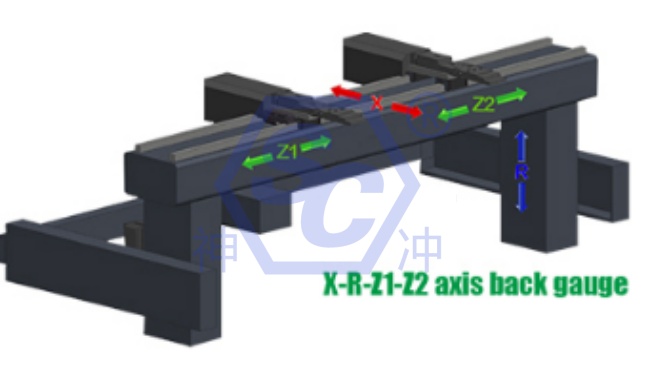
A 6-axis press brake includes Y1 and Y2 axes for controlling the independent movement of the ram, the X-axis for back gauge positioning, the R-axis for vertical back gauge finger adjustments, and Z1 and Z2 axes for lateral movement of the back gauge fingers. These axes work together to provide precise control over the bending process.
This configuration is ideal for industries that require intricate bending operations, such as automotive, aerospace, and custom metal fabrication. With a 6-axis press brake, you can handle tasks like multi-bend parts with complex angles and varying flange lengths. The independent movement of the Z1 and Z2 axes allows for flexibility in part positioning, making it easier to fabricate asymmetric components or workpieces with unconventional geometries.
What Is An 8-Axis Press Brake?
An 8-axis press brake represents the pinnacle of bending technology, incorporating all the functionalities of a 6-axis machine with additional features for unparalleled precision. Alongside Y1, Y2, X, R, Z1, and Z2 axes, it includes X1 and X2 axes, which control independent horizontal movement of the back gauge fingers. This enables angled bends and offset positioning, further enhancing the machine’s capabilities.
This configuration is specifically designed for high-precision applications in industries like aerospace, where consistency, repeatability, and minimal error margins are critical. The independent control of each axis allows operators to fabricate highly complex parts with minimal manual intervention. This reduces the likelihood of errors and enhances productivity.
Conclusion
Press brake axis is one of the most important configuration of the machine. We know choosing the right machine can feel overwhelming, but it’s all about focusing on what you need right now—and what you might need down the road. Think about the materials you use, the size of your parts, and how much you need to produce. It’s about finding that balance between performance and budget so your investment pays off both today and in the future.
At SC Machinery, we’re here to make that choice simpler for you. Our press brakes, from 2 to 11 axes, are built to handle anything you throw at them, with precision and reliability you can count on. When you’re ready to take your metalworking to the next level, we’ve got the tools to help you make it happen.