Table of Contents
What is metal plate rolling machine? A metal plate rolling machine is a processing device used to roll metal plates into a circular, curved or other shape. It applies pressure to the metal plate through the rotation and relative movement of the roller, causing it to gradually undergo plastic deformation and eventually form the desired arc or curved surface. Plate rolling machines are widely used in the manufacture of pressure vessels, pipelines, boilers, fan housings, aerospace parts and other fields.
1. What is a metal plate rolling machine?
1) Definition Of Plate Rolling Machines:
The main steps include:
– Plate positioning: Place the metal plate between the rollers of the plate rolling machine.
Clamping and pre-bending: The upper roller applies downward pressure to clamp the plate and pre-bend the edge to reduce the length of the straight edge after forming.
– Curling forming: Through the rotation of the rollers and pressure adjustment, the plate is gradually bent into the required arc or curved surface.
– Unloading: After rolling, release the rollers and take out the finished product.
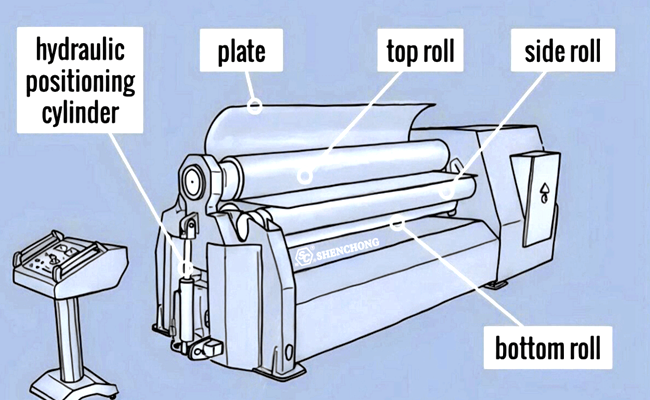
2. Main components of plate bending rollers
Roller system:
Usually composed of upper roller, lower roller and side roller, responsible for clamping and curling the plate. Roller material is usually high-strength alloy steel, which is wear-resistant and hard.
Drive system:
Provides the rotation power of the roller. The mechanical type adopts gear transmission, and the hydraulic and servo types are driven by hydraulic cylinders or motors.
Hydraulic system:
Used to control the lifting and pressure adjustment of the roller to ensure processing accuracy and stability.
Control system:
Includes manual control and CNC system. The CNC system can preset processing parameters and realize automatic operation.
Base and frame:
Support the entire equipment to ensure the stability and accuracy of the equipment during operation.
3. Plate Rolling Machine Working Principle
machine is to use rollers to apply pressure and rotation to the metal plate, so that the plate undergoes plastic deformation, thereby gradually bending it into the desired shape (such as a cylinder, cone or arc).
What is metal plate rolling machine working principle? This process is achieved by adjusting the relative position of the rollers and power drive. The following is a detailed analysis of the working principle.
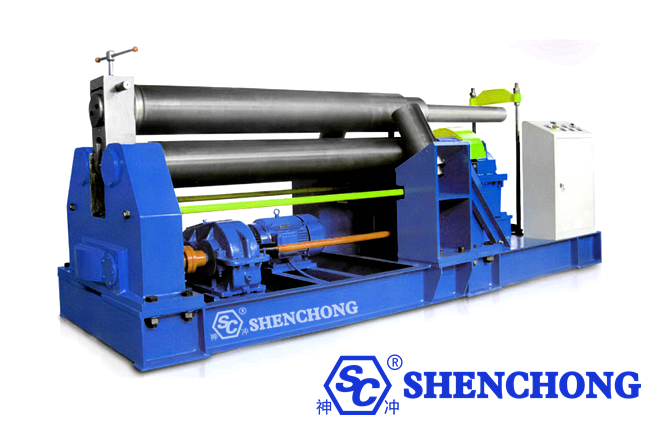
1) Basic working process
The plate rolling machine usually consists of an upper roller and a lower roller (or side roller), and the plate is gradually formed by clamping, rotating and bending between the rollers. The specific steps are as follows:
- Clamping the plate
The plate is placed between the rollers. The upper roller (or lower roller) applies downward (or upward) pressure to clamp the plate to prevent sliding.
- Pre-bending treatment
In order to reduce the straight edge length of the plate edge, the plate rolling machine performs a preliminary bend (called pre-bending) on both ends of the plate.
The initial arc forming of the plate edge is achieved by adjusting the pressure and position of the rollers.
- Bending roll forming
The rollers begin to rotate, driving the plate to move in a clamped state. As the plate passes between the rollers, plastic bending gradually occurs to form the target curvature.
- Adjustment and correction
If necessary, the arc or shape can be further optimized by adjusting the pressure and position of the rollers.
The four-roller plate rolling machine can be corrected more accurately with the assistance of the side rollers.
- Finished product unloading
After rolling, release the rollers and remove the processed product from the plate rolling machine.
2) Working principle of plate rolling machines with different structures
- Three-roller symmetrical plate rolling machine
Structural features:
The upper roller is symmetrically arranged between the two lower rollers, the upper roller can move vertically, and the two lower rollers rotate to drive the plate.
Working principle:
The plate is pressed downward by the upper roller and clamped between the lower rollers.
The rotation of the lower roller drives the plate to move, and the upper roller applies bending force to the plate.
The plate is bent repeatedly by the rotation of the lower roller and finally formed.
Features:
The structure is simple, but the edge of the plate cannot be pre-bent directly.
- Three-roller asymmetric plate rolling machine
Structural features:
The upper roller is the main roller, one lower roller is used to clamp the plate, and the other lower roller is used for auxiliary bending.
Working principle:
After the plate is clamped, the edge is pre-bent by adjusting the roller position.
The upper roller rotates to drive the plate to move and applies bending force at the same time.
The relative movement between the rollers gradually forms the target arc.
Features:
It can be pre-bent and is suitable for high-precision processing.
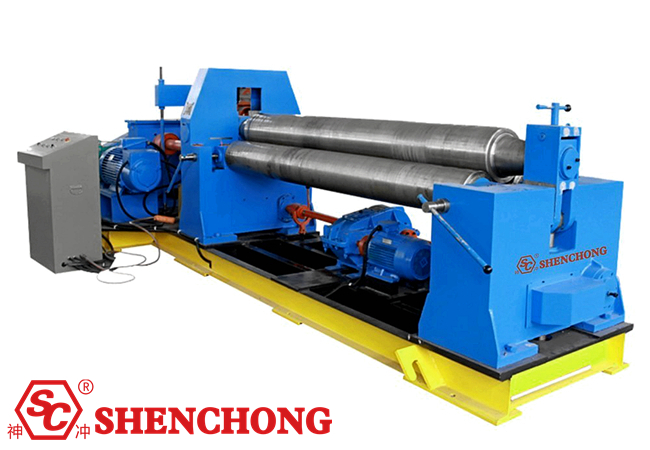
- Four-roller plate rolling machine
Structural features:
One upper roller, one lower roller and two side rollers, the side rollers are used to clamp and correct the plate.
Working principle:
The plate is clamped by the upper and lower rollers, and the side rollers assist in positioning.
The upper roller applies bending force to drive the plate to move.
The side rollers further correct the bending shape of the plate.
Features:
Simple operation, high precision, can complete pre-bending and rolling at one time.
3) Key physical principles
The working principle of metal plate rolling machine is based on the principle of plastic deformation of metal. Specifically, it includes:
The effect of bending force:
When the bending force applied by the roller exceeds the yield strength of the metal material, the metal sheet undergoes plastic deformation. By gradually adding force, the sheet is bent from a straight state to the target shape.
Control of elastic rebound:
The sheet will produce a certain elastic rebound during the bending process. The plate rolling machine compensates for the rebound by applying additional bending force to ensure the arc accuracy of the finished product.
Multiple forming:
For thicker or harder sheets, it is necessary to gradually reach the target shape through repeated bending.
4. Application fields of metal plate rolling machine
What is the use of metal plate rolling machine? They are as follows:
Application industries:
– Pressure vessel manufacturing: rolling cylindrical or curved shells of large containers such as boilers and storage tanks.
– Pipeline processing: manufacturing large-diameter pipes or ventilation ducts.
– Shipbuilding: processing the curved surface of the hull plate.
– Aerospace: manufacturing curved or cylindrical parts of aircraft, rockets and other equipment.
– Construction engineering: rolling steel structure components for construction, such as columns, curved beams, etc.
Application examples:
– Manufacturing cylindrical storage tanks: forming the tank shell by continuously bending the metal sheet.
– Processing conical pipes: using a conical plate rolling machine to gradually reduce the diameter of the plate.
– Making building steel structures: such as bridge curved beams or cylindrical support structures.
5. Conclusion
The plate rolling machine gradually bends the metal sheet into the target shape through the rotation and pressure of the roller. Its core principle is to use the plastic deformation characteristics of the metal, combined with a precise control system, to complete efficient and precise bending processing. Different types of plate rolling machines are suitable for different materials and shape requirements, providing important support for modern manufacturing.
What is metal plate rolling machine? Plate rolling machine is one of the important equipment for modern metal processing. Through continuous development and technological upgrading, it has become a core tool for efficient and high-precision bending processing. Both traditional mechanical equipment and modern CNC plate rolling machines provide important support for metal forming processing in various industries.