Table of Contents
What is fiber laser cutting machine? Fiber laser cutting machine is a laser cutting machine that uses a fiber laser generator as the light source. Fiber laser cutting machine is a kind of equipment that uses high-energy laser beams emitted by fiber lasers for cutting.
It is widely used in metal processing, aerospace, electronic manufacturing and other fields. It is favored by the market for its high efficiency, precision and flexible processing capabilities, and is one of the important tools in modern industrial manufacturing.
1. Introduce To Fiber Laser Cutting Machine
The cnc fiber laser cutting machine can perform both flat cutting and oblique cutting, with neat and smooth edges, suitable for high-precision cutting of metal plates and other materials. In addition, the mechanical arm can perform three-dimensional cutting instead of the original imported five axis laser.
Compared to ordinary carbon dioxide laser cutting machines, it saves more space and gas consumption, has a high photoelectric conversion rate, is a new energy-saving and environmentally friendly product, and is also one of the world’s leading technological products.
Fiber laser is a newly developed type of fiber laser internationally that outputs a high-energy density laser beam, which is concentrated on the surface of the workpiece, causing the area illuminated by the ultra-fine focal spot on the workpiece to instantly melt and vaporize.
The automatic cutting is achieved by moving the position of the spot through a CNC mechanical system. Compared with bulky gas lasers and solid lasers, gas lasers have obvious advantages and have gradually developed into important candidates in fields such as high-precision laser processing, LiDAR systems, space technology, and laser medicine.
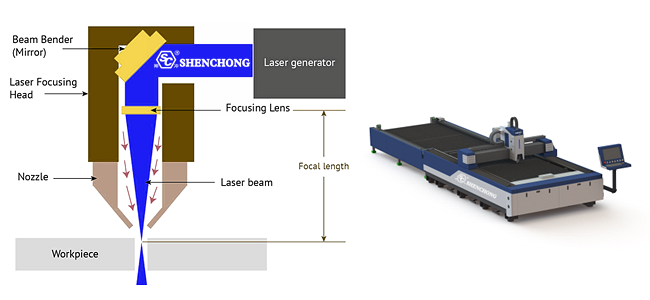
1) Working principle of fiber laser cutting machine
The high-energy laser beam generated by fiber laser transmission is focused on the surface of the material, so that it is heated to the melting point or vaporization point in a very short time, and the melted or vaporized material is blown away by auxiliary gas (such as oxygen, nitrogen or air), thereby achieving cutting.
2) Main components
Fiber laser:
Core component, providing high energy density laser beam.
Cutting head:
Including focusing lens, nozzle and sensor, responsible for focusing the laser beam onto the surface of the material.
Transmission system:
Including servo motor, guide rail and rack to ensure the precise movement of the cutting head.
Control system:
CNC system is used to control parameters such as cutting path, speed and power.
Auxiliary gas system:
Provides oxygen, nitrogen or air to assist the cutting process.
Cooling system:
Used to cool the laser and cutting head to ensure stable operation of the equipment.
Machine body:
Provides a stable processing platform, usually made of high-strength materials to ensure processing accuracy.
2. Fiber Laser Cutting Machine Main Features
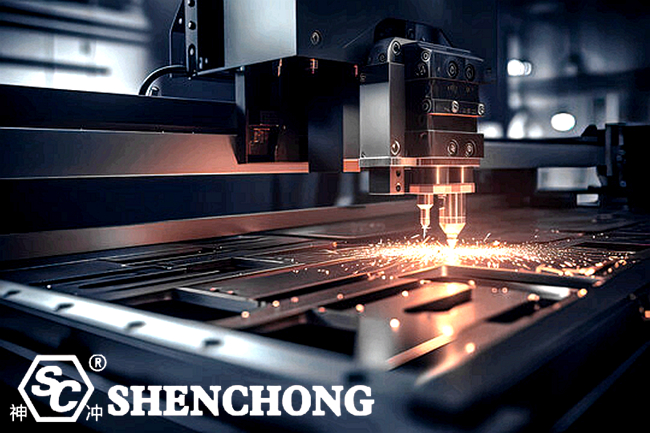
What is fiber laser cutting machine feature? We can analyze as follow:
- Fiber laser has high electro-optical conversion efficiency, with a conversion efficiency of over 30%. Low power fiber lasers do not require a chiller and use air cooling, which can significantly save power consumption during operation, save operating costs, and achieve the highest production efficiency.
- The laser only requires electrical energy during operation and does not generate additional gas from the laser, with the lowest operating and maintenance costs.
- The fiber laser adopts semiconductor modularity and redundant design, with no optical lenses in the resonant cavity, no need for startup time, and has the advantages of no adjustment, no maintenance, and high stability, reducing accessory costs and maintenance time, which is incomparable to traditional lasers.
- The output wavelength of the fiber laser is 1.064 micrometers, which is 1/10 of the CO2 wavelength. The output beam quality is good, the power density is high, and it is very conducive to the absorption of metal materials. It has excellent cutting and welding capabilities, thereby minimizing processing costs.
- The entire machine is transmitted through optical fiber, without the need for complex light guiding systems such as reflectors. The optical path is simple, the structure is stable, and the external optical path is maintenance free.
- The cutting head contains protective lenses, which minimize the consumption of valuable consumables such as focusing lenses.
- Light is exported through optical fibers, making the design of mechanical systems very simple and easy to integrate with robots or multi-dimensional workbenches.
- After adding a shutter to the laser, it can be used for multiple machines. Through fiber optic splitting, it can be divided into multiple channels to work simultaneously, making it easy to expand its functions and upgrade easily and simply.
- Fiber laser has a small volume, light weight, movable working position, and small footprint.
1) Customized beam
The customized beam shape in fiber laser cutting machines is based on a principle that compared to traditional laser cutting using a single circular laser beam, the new cutting process adopts a complex laser beam shape.
By utilizing the unique focusing characteristics of high-power single-mode fiber lasers, complex beam shapes are generated, making it possible to separate a portion of the overall laser energy, in order to create a “keyhole” for laser welding or cutting applications. The remaining energy will be distributed to the melt. Prior to this, the main beam was used to create an appropriate high vapor pressure distribution on the surface of the molten material.
This allows it to apply local pressure to the molten material flowing out of the incision, which far exceeds the pressure of coaxial gas injection commonly used in laser cutting. The result is that the incision is very narrow. The new process has great potential, as it does not produce burrs within a large cutting speed range and can also perform high-speed cutting in narrow contour cutting, producing high-quality cuts
2) Rapid prototyping
The rapid prototyping technology in fiber laser cutting machines is a general term for the technology of directly producing samples or parts based on CAD models. It integrates modern technological achievements such as CAD technology, CNC technology, laser technology, and material technology, and is an important component of advanced manufacturing technology.
It can automatically, directly, quickly, and accurately materialize design ideas into prototypes or directly manufactured parts with certain functions based on CAD models (electronic models), generating almost any complex component without the use of molds and tools, solving the problem of rapid docking from design to manufacturing.
Therefore, this technology can quickly evaluate and modify product design, effectively shorten the product development cycle, reduce development costs, meet the requirements of today’s fiercely competitive market for rapid development and manufacturing of new products, and improve the market competitiveness of products and the comprehensive competitiveness of enterprises.
3) Water Cooling
As a supporting cooling equipment for fiber laser cutting machines, the chiller ensures that the fiber laser cutting machine operates normally at a constant temperature. The dedicated chiller for fiber laser cutting machine belongs to the refrigeration type industrial chiller, which has two working modes of constant temperature and intelligent temperature adjustment, with a temperature control accuracy of ± 0.3 ℃.
Rich in configuration, including input and output control equipment switches, advanced functions such as cooling water flow and high and low temperature alarms, stable and durable performance, and particularly outstanding in energy conservation and environmental protection.
Technical parameters:
One stop fully automatic intelligent temperature control: Users can automatically switch to the appropriate control temperature without changing it in different environments.
CW-6100AT: Can be applied to cool a single 300W-1000W fiber laser.
Equipped with a heater and purified water quality configuration.
3. What is fiber laser cutting machine advantage?
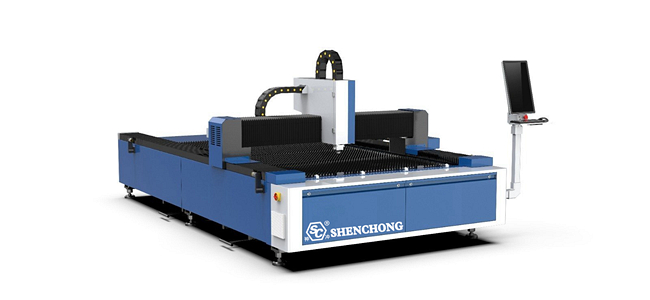
Main characteristics
Efficient energy conversion:
The electro-optical conversion efficiency of fiber lasers is as high as 30%, which is more energy-efficient than traditional CO₂ lasers.
High precision:
The laser beam has a small diameter after focusing, a narrow slit, and a cutting accuracy of ±0.1mm.
High-speed cutting:
Particularly suitable for rapid processing of thin sheet metals, the cutting speed is faster than traditional methods.
Low maintenance cost:
Fiber lasers adopt a maintenance-free design, have a long service life, and low operating costs.
Strong material adaptability:
Can cut a variety of metal materials, such as carbon steel, stainless steel, aluminum alloy, copper, etc.
Environmental protection:
No noise, no pollution during processing, in line with green manufacturing requirements.
Advantages of fiber laser cutting machine over CO2 laser cutting machine
- Excellent beam quality: smaller focusing spot, finer cutting lines, higher work efficiency, and better processing quality.
- Extremely high cutting speed: twice the power of CO2 laser cutting machines of the same power.
- Extremely stable: using world-class imported fiber lasers, with stable performance and a service life of up to 100000 hours for key components.
- Extremely high electro-optical conversion efficiency: The photoelectric conversion efficiency of the fiber laser cutting machine is about 30%, which is three times higher than that of the CO2 laser cutting machine, energy-saving and environmentally friendly.
- Extremely low usage cost: The power consumption of the entire machine is only 20-30% of that of similar CO2 laser cutting machines.
- Extremely low maintenance cost: no laser working gas. Fiber optic transmission without the need for reflective lenses. Can save a lot of maintenance costs.
- Easy operation and maintenance of the product: Fiber optic transmission, no need to adjust the optical path.
- Super strong flexible light guiding effect: compact size, compact structure, easy to meet flexible processing requirements.
Of course, compared to carbon dioxide laser cutting machines, the cutting range of optical fibers is relatively narrow. Due to the wavelength, it can only cut metal materials and is not easily absorbed by non-metals, thereby affecting its cutting range.
Advantages Compared To Yag Laser Cutting Machines
- Cutting speed: The speed of the fiber laser cutting machine is 4-5 times that of YAG, suitable for large-scale processing and production
- Usage cost: The usage cost of fiber laser cutting machine is lower than that of YAG solid laser cutting
- Optoelectronic conversion efficiency: The photoelectric conversion efficiency of fiber laser cutting machine is about 10 times that of YAG
The price of corresponding fiber lasers is relatively high, so the price of fiber laser cutting machines is much higher than that of YAG laser cutting machines, but much lower than that of carbon dioxide laser cutting machines. But its cost-effectiveness is indeed the highest among the three.
4. What is fiber laser cutting machine disadvantage?
Although fiber laser cutting machines have many advantages in metal processing, they also have some disadvantages and limitations, which are mainly reflected in the following aspects:
1) High equipment cost
The initial purchase cost of fiber laser cutting machines is high, especially high-power equipment.
For small and medium-sized enterprises, it may take a long time to recover the investment cost.
2) Challenges in cutting highly reflective materials
When cutting highly reflective materials (such as copper, aluminum, silver, gold, etc.), the laser may be partially reflected, reducing the cutting efficiency. Special processes or configurations (such as anti-reflection devices) are required to reduce the damage to the equipment caused by laser reflection.
In this case, professional manufacturers will recommend you to use a high-quality shearing machine.
3) Limited ability to cut thick plates
Fiber laser cutting machines perform well on thin plates and medium-thick plates (usually less than 25mm), but for thicker metal plates, the cutting speed and quality may not be as good as plasma cutting or water jet cutting. Higher power lasers are required for thick plate cutting, further increasing costs.
4) High requirements for the processing environment
A stable power supply and cooling system are required to ensure the normal operation of the equipment. The processing environment needs to be kept clean to avoid the influence of dust and oil on the optical system.
5) Maintenance and consumables costs
Although the fiber laser itself has low maintenance requirements, other components (such as cutting heads, lenses, and nozzles) still need regular maintenance and replacement. The consumption of auxiliary gases (such as nitrogen, oxygen) will also increase operating costs, especially when cutting for a long time and at high intensity.
6) Operation and technical threshold
Operation requires skilled technicians, especially for programming and parameter adjustment of complex parts. Improper operation may result in reduced cutting quality or equipment damage.
7) Material limitations
Limited processing capabilities for non-metallic materials, such as wood, glass, or certain plastics, usually require other types of laser cutting equipment (such as CO₂ laser cutting machines). Certain coatings or composite materials may have an adverse effect on cutting results.
8) Dependence of processing accuracy on machine tool stability
Cutting accuracy is highly dependent on the structural stability and motion accuracy of the machine tool. If the machine tool is of poor quality or wears out after long-term use, it will affect the processing accuracy.
9) Complex initial setup and debugging
For complex parts or specific materials, parameters need to be adjusted multiple times to obtain the best cutting effect. Improper parameter settings may result in unstable cutting quality.
Despite these disadvantages, fiber laser cutting machines are still irreplaceable tools in many industries due to their high efficiency and high precision. Potential disadvantages can be overcome by selecting high-quality equipment, optimizing process parameters, strengthening maintenance and training operators.
The initial equipment cost is high. When cutting highly reflective materials (such as copper and aluminum), special configuration may be required.
5. Key factors for selecting a fiber laser cutting machine
– Power
Choose the appropriate laser power according to the material type and thickness.
– Processing size
Choose a machine table that fits the workpiece size.
– Brand and service
Choose a brand with mature technology and perfect after-sales service.
– Auxiliary functions
Such as automatic loading and unloading, pipe cutting functions, etc., can improve production efficiency.
6. Conclusion
What is fiber laser cutting machine? The answer is as following. Fiber laser cutting machine is a technological revolution in sheet metal processing and a “machining center” in sheet metal processing. Laser cutting machines have a high level of flexibility, fast cutting speed, high consumption efficiency, and short product consumption cycles, which have won a widespread market for customers.
Fiber laser cutting machine has no cutting force and no deformation during processing. No tool wear, good data compliance. Whether it is a simple or complex part, it can be finely and rapidly formed and cut with laser in one go. Its narrow cutting seam, good cutting quality, high automation level, simple operation, low labor intensity, and no pollution. It can complete automatic cutting layout and nesting, improving the application rate of data, reducing consumption costs, and improving economic efficiency. The effective lifespan of this technology is long.
Currently, fiber laser cutting machines are mostly used for sheet metal thicknesses exceeding 2MM in foreign countries. Many foreign experts analyze that the next 30-40 years are the golden period for the expansion of laser processing technology (which is the direction for sheet metal processing expansion).
Other related information about fiber laser cutting: