What is a shearing machine? Sheet metal plate shearing machine is a specialized tool used in the sheet metal industry to cut metal sheets into various shapes and sizes. Sheet metal shearing machines are widely used in various industries such as automotive and aerospace manufacturing, mechanical production, household appliance production, and construction. A comprehensive understanding of what is a shearing machine can help maintain and use the machine more efficiently to cut sheets.
Table of Contents
What Is Sheet Metal Shearing?
Shearing is the process of cutting metal plates, bars, and sheets by applying shear stress using molds and punches, which is very similar to stamping paper. The mold and punch can have different shapes, such as circular or straight blades resembling scissors. Shearing machines include punching machines for small discs, cutting machines for washing machine production, etc. Usually, cutting operations are used to divide metal into sheets or strips. The type of blade used for cutting – straight or rotating edges – determines the process of cutting sheets, sheets, or strips.
Below article we explore the plate shearing machine to cut sheet metals.
Principle Of A Shearing Machine
The basic shear frame includes workbench components welded or bolted to the side frame, hydraulic or mechanically driven moving gate components, and clamping gate components fixed to the side frame.
The shearing process of a shearing machine is simple. Cut the metal sheet into smaller pieces using two blades, which are at a certain angle to each other. The lower blade is firmly fixed in the pocket of the fixed workbench, while the upper blade is assembly on the moving ram.
The pressure cylinder is used to press the sheet material, preventing it from moving during the shearing process. Protect guardrails are safety devices that prevent accidents from occurring. The return process is driven by nitrogen gas, with a fast speed and minimal impact.
Cutting Principle Of Mechanical And Hydraulic Shearing Machines
- The mechanical shear device is driven by an eccentric device, which is engaged by a flywheel clutch combination. This drive system is usually rigid and fast, but provides less operator control and overload protection.
- The hydraulic drive system includes a motor connected to a pump, which is connected to a manifold with hydraulic valves and one or more hydraulic cylinders. The oil is pumped into the oil cylinder, which in turn activates theram.
Types Of Plate Shearing Machines
The shearing machine and other related cutting machinery are used in the first stage of metal plate manufacturing, which includes cutting the metal plate into a certain size. These machines are universal tools used for cutting metal plates and other alloys. The working principle of some shearing machines is similar to that of shearing machine, using angle shearing to cut metal into strips or sheets. Direct shear action, where the edges are fixed at an angle opposite to angular motion, is used for specific large machines.
There are various types of shearing machines, each suitable for specific materials and applications. The following are comprehensive information of various types to specifically show you what is a shearing machine.
Swing Beam Shearing Machine
The swing beam shearing machine is a precision cutting instrument used in the metal processing process. Unlike traditional manual or mechanical shearing machines, CNC swing beam shearing machines is a type of hydraulic shear that use computer digital control to automate and improve cutting accuracy.
The movement of the upper blade, swinging to perform cutting actions, is known as the “swinging beam” design. The upper blade moves in an arc around the pivot bearing. Usually, the upper blade is conical with only two available edges to avoid interference with the lower blade during arc motion. The swinging beam shear machine usually adopts a smaller shape design and weight than the shear machine, but it also makes it easier to adjust the blade clearance through the eccentric device in the pivot bearing. The numerous advantages of this design include improved blade alignment and reduced material deformation during the cutting process. Due to swinging, the workpiece is subjected to less force, resulting in smoother cutting.
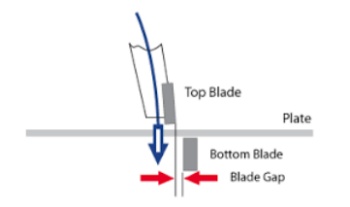
Hydraulic Guillotine Shearing Machine
Metal plates can be directly cut using a mechanical tool called a hydraulic guillotine shear. Guillotine is a term used to describe a shearing machine that uses hydraulic power to transform a fixed lower blade into a scissor like action, cutting the metal between it and the moving upper blade. The term “guillotine” describes the vertical movement of the upper blade as it descends to accurately and cleanly cut the material. Guillotine shear allows the use of 4-edge blades. This is a great rigid design.
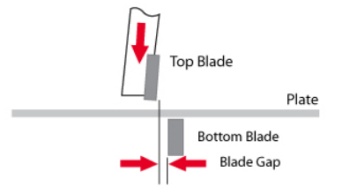
Mechanical Crank Down Shear
Metal plates can be sheared or cut into the desired shape or size using a mechanical power driven machine called a mechanical crank shearing machine. The phrase “below the crank” describes the machine drive mechanism located below the device frame. A manual metal plate shearing machine is a device that can cut sheets by manually moving the blades up and down. This type of shearing machine is easy to operate and suitable for cutting small boards, but its cutting accuracy is low and cannot meet the requirements of large boards. The mechanical shearing machine is operated using a power device consisting of an electric motor, flywheel, worm shaft, and clutch. Compared to hydraulic shearing machines, it has a faster cutting speed and more strokes per minute.
Components Of A Plate Shearing Machine
- The main components of a sheet metal shearing machine are a workbench, upper and lower shearing blades, clamping tools, baffles, and electrical components.
- Blades are usually made of high-strength steel with good hardness and wear resistance, and are the main working components of machines.They can move up and down to perform metal plate cutting. The fixture is used to fix the metal plate in place for precise cutting.
- Baffle servesare a protective measure for shearing machines. It is made of high-strength metal materials, which can prevent external forces from impacting the sheet metal. Baffles are usually installed near the cutting edge of the machine to ensure maximum safety for workers.
- Electrical components control the operation of the shearing machine, consisting of a circuit board, motor, and controller.These components monitor and control the operating status of the machine to ensure safe operation.
Plate Shearing Machine Blades
The blades of the shearing machine are mainly composed of materials such as high-speed steel and carbon steel. High speed steel is a commonly used blade material, characterized by high wear resistance and stiffness. Due to its high stiffness, high-speed steel blades can significantly improve the cutting efficiency of shearing machines. After fine processing, they can also improve the cutting accuracy of the machine. On the other hand, carbon steel is an economical blade material with high toughness. The high toughness of carbon steel blades enables them to resist vibration and deformation during the shearing process. In addition, after heat treatment, they can also improve the cutting accuracy of the machine. In short, the blade materials of a shearing machine can include high-speed steel, hard alloy, carbon steel, etc. The selection of blade materials depends on the specific working conditions and budget of the machine.
The sharpness of the blade is crucial for achieving high-quality cutting. Blunt blades must further penetrate the material to form clean cracks. This leaves behind less than ideal cutting and also increases cutting pressure. Two factors – the type of material being sheared and the number of shear cycles – determine the normal lifespan of the blade. Harder materials such as T1 plates and stainless steel will correspondingly shorten the blade life. To extend the service life of shear blades, the following rules should be followed:
- Do not cut metal at the burnt edge.
- Do not cut round steel bars.
- Do not cut materials that exceed the rated capacity of the shearing machine.
- Do not use blunt or circular blade surfaces for cutting.
- Do not cut with improper blade clearance settings.
Factors Affecting Shearing Accuracy
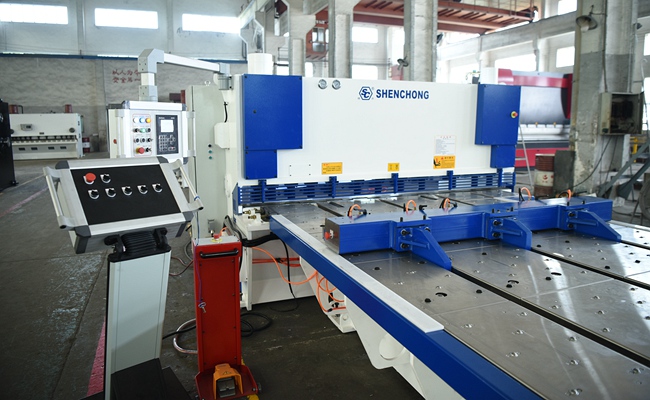
Sheet Plate Drop
The shearing machine backgauge cannot completely hold the sheet from the blade to the rear finger, which leads to the sheet plate drop. When cutting long and thin materials, this issue is more critical and may require a sheet support system to ensure good accuracy.
Blade Clearance Setting
The blade gap setting will affect the cutting points related to the bottom shear blade. Adjust the rules to read the distance from the fixed bottom tool, but as the gap between thicker metal blades increases, the cutting point will also move away from the tool.
Blade Sharpness
The cutting quality is directly proportional to the sharpness of the cutting blade. Blunt blades will leave rough edges.
Backgauge Maintenance
Normal preventive maintenance, including lubrication and readjusting the parallelism of the stop lever, is necessary to continuously achieve high stop accuracy.
Cut Bevel
The cut edges may be beveled depending upon the blade clearance setting. In effect, the length of the sheared piece may differ by several thousandths of an inch when measuring from the top, middle, or bottom of the cut. Cut bevel is more noticeable on heavier gauges.
The Shearing Effects Of The Hydraulic Shearing Machine
Twisting
Twist is a common shear condition described as the tendency of the cut material to curl into a spiral or spiral shape. Although distortion may be caused by internal stress in the material and blunt blade, it is mainly generated through the front angle of the upper blade and the width of the descending blade. During the shearing process, a high inclination angle will greatly increase the twisting effect of the material.
Camber Angle
When the material being cut moves horizontally away from the sheet metal, a camber angle occurs. This is almost entirely the result of internal stress in the material itself, however, punch speed, grain direction, and tool clearance may also have some impact on curvature.
Bow
Bow is described as the tendency of a material to curl downwards during the shearing process. Similarly, this situation is most common when cutting slender bands. It is caused by defects or stresses in the material and shear at higher shearing angles.
Shearing Angle And Shearing Quality
The shearing angle is the slope of the upper tool from left to right. The shearing machine will have a fixed or adjustable shearing angle, allowing the operator to set the angle for the appropriate specification of metal being sheared.
The required load for shearing materials depends on the thickness and inclination angle of the upper blade. As the thickness of the metal increases, the shear load rapidly increases. Increasing the shearing angle will greatly reduce the load, but due to the increased amount of twisting, it will lead to a decrease in the quality of the shear material.
Why Is Adjustable Blade Clearance Important
The blade gap is the distance between the upper and lower blades of the shearing machine during the shearing process. To achieve the best shear quality, the gap between the upper and lower blades should be set to approximately 7% of the material thickness.
When the clearance between the blades is too large, the cut material will leave burrs. Insufficient clearance can cause double cutting of the shear part.
The optimal blade setting will allow the material to fracture cleanly. Most plate shearing machines are equipped with manual or electric blade gap clearance system, but in some cases, they may be difficult to set or have limited adjustments.
Future Development Trend Of Metal Sheet Shearing Machines
The future development direction of sheet metal shearing machines may be influenced by various factors, including economic growth, market demand, and technological progress.
With the rise of intelligent technology, CNC plate shearing machines are expected to become more advanced, with additional intelligent functions such as automatic blade position adjustment, automatic plate type and thickness recognition. The implementation of digital technology can bring more efficient production management and quality control, making shearing machines more efficient.
In addition, the integration of the shearing machine with other equipment to be an automatic shearing production line is expected to improve production efficiency and quality by achieving seamless connections.