Table of Contents
The magnitude and effect of sheet metal shear force are affected by many factors. For the shear force on metal sheets, the main influencing factors include material properties, geometric dimensions, shearing process and external conditions. The following are the main factors that affect the shear force.
1. What are the factors that affect metal shear force?
The shear force a metal can withstand depends on a variety of factors, which include both material properties and external conditions. Here are some of the key factors:
1) Shear strength
The shear strength of a metal sheet refers to the maximum shear stress that the metal sheet can withstand under shear. The shear strength of a metal sheet is very important in metal processing and manufacturing processes such as cutting, stamping, stretching and forming.
The shear strength of a metal sheet is usually closely related to the type, thickness, processing state and surface condition of the material. Generally speaking, the shear strength of a metal sheet is lower than its tensile strength, but for the processing process, understanding its shear strength helps to determine the shear force required in the actual process.
Common metal material shear strength:
- Low carbon steel: shear strength is about 250–300 MPa.
- High-strength steel (such as strength steel and alloy steel): high shear strength, up to 400–600 MPa.
- Aluminum alloy: shear strength is about 150–250 MPa.
- Stainless steel: shear strength is about 300–450 MPa.
- Copper and its alloys: shear strength is about 150 MPa.
The shear strength of sheet metal is a key material property parameter that determines the shear behavior of the material during processing. By understanding the shear strength, the design and optimization of the production process can be effectively guided to ensure smooth processing and reduce material waste.
- Materials with high shear strength (such as high-strength steel, hardened alloys, etc.) usually require greater shear force.
- Materials with low shear strength (such as aluminum, copper, etc.) require less shear force.
2) Plate thickness
The thickness of the sheet directly affects the magnitude of the shear force. The thicker the sheet, the greater the force required for shearing.
- Increased thickness, increased shear force:
From the formula, it can be seen that the greater the thickness t, the greater the required shear force F. Because during the shearing process, the shear force acts on the entire thickness of the sheet. Therefore, the thicker the sheet, the greater the required shear force.
For example, if the thickness of the sheet increases from 5 mm to 10 mm, the shear force will approximately double.
- Linear relationship between shear force and thickness:
In most cases, the shear force is linearly related to the thickness of the sheet. Assuming that other conditions (such as the width and shear strength of the sheet) remain unchanged, the required shear force will approximately double for each doubling of the thickness.
3) Shear length
The effect of shear length on shear force is similar to the thickness of the plate and also plays a key role. Shear length refers to the length of the material in contact with the tool during the shearing process, which is usually equal to the width of the metal plate. It determines the total area of the material sheared during the processing, which in turn affects the required shear force.
Linear relationship between shear force and shear length:
Shear force is linearly related to shear length. That is, if other conditions remain unchanged, the required shear force will approximately double for every doubling of the shear length.
For example, if the shear length increases from 100mm to 200mm, the required shear force will also double.
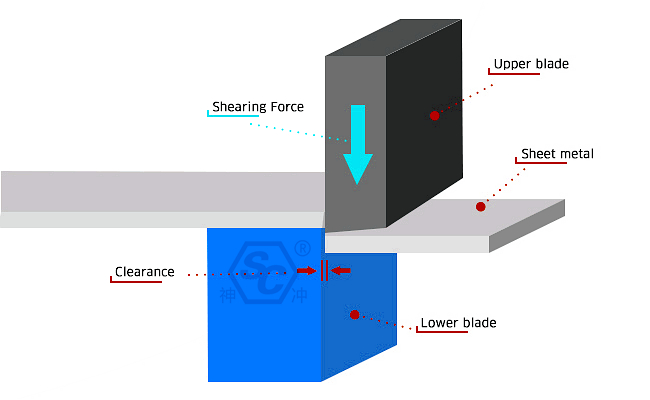
4) Shear gap
Gap size:
Too small or too large a shear gap will affect the shear force. An appropriate gap can reduce the shear force and improve the quality of the shear section.
Gap uniformity:
Uneven gaps may cause local shear forces to increase, affecting the shearing effect.
5) Shear blade angle
Shear angle:
An appropriate metal shear angle can reduce the shear force. The larger the shear angle, the more dispersed the cutting force during the shearing process, thereby reducing the instantaneous shear force.
Blade sharpness:
The sharper the blade, the smaller the shear force. Blunting the blade will increase the sheet metal shear force.
6) Shear speed
The effect of shear rate on shear force is an important consideration in metalworking, especially during high-speed cutting and processing. Shear rate refers to the relative speed of the shear edge during the shearing operation, usually the speed of the tool or table movement.
During the shearing process, the amount of shear force depends not only on the nature and thickness of the material, but also on the shear rate. The effect of shear rate on shear force is usually non-linear, and the specific influencing factors depend on a variety of factors, such as material type, temperature, processing method, etc.
Effect of shear rate on shear force:
During the shearing process, an increase in shear rate will have different effects on shear force, which are mainly reflected in the following aspects:
– Temperature effect
High shear rate will cause a local temperature increase because the surface of the material will experience greater friction and plastic deformation during high-speed cutting, generating more heat. This temperature rise will cause the strength of the metal material to decrease, which in turn reduces the shear force.
– Metal heating
For example, materials such as aluminum and steel will lose their shear strength at high shear rates, especially at high temperatures, the material will become softer and the shear force will decrease. On the other hand, low shear rates may result in less heat accumulation and relatively high shear force.
– Dynamic Effect and Inertia
When the shear speed is high, dynamic effects will occur in the shearing area of the material, including elastic response and plastic flow of the material. In high-speed shearing, the response speed of the material may be more sensitive than that of low-speed shearing, which may lead to instability or instantaneous fluctuations in the shear force.
Inertia effect:In high-speed shearing, the material may produce instantaneous vibration or stress concentration due to inertia, which will affect the stability of the shear force.
– Plastic flow and yield of materials
When the shear speed is high, the plastic flow characteristics of the material in the shearing zone will change, and the shear force may change. Due to the increase in the plastic deformation rate in the shearing zone at higher speeds, the yield strength of the material may decrease, resulting in a reduction in shear force.
In high-speed cutting of some materials (especially metals), different fracture modes may occur in the shearing process, such as local melting or microcracks in the shearing area, which affects the shear force.
Quantitative analysis of shear speed on shear force:
The relationship between shear speed and shear force is not a simple linear relationship, but is affected by the combined influence of material properties, temperature effects and processing methods. Generally, shear force tends to decrease at high shear speeds, but the specific extent of the impact depends on the following factors:
– Material type
Different materials have different temperature sensitivities. High shear speeds have a greater impact on some soft metals (such as aluminum and copper) and a smaller impact on some hard metals (such as hardened steel).
– Shear temperature
During the shearing process, higher shear speeds will increase the local temperature, thereby reducing the strength of the material and reducing the shear force.
– Cutting method
The impact of high-speed cutting is different in processes such as laser cutting, shearing machine cutting and stamping. For example, in laser cutting, the shear force will be significantly reduced due to the high temperature generated by the laser.
– Tool wear
During high-speed shearing, the contact time between the tool and the material is shorter, which reduces the degree of tool wear, but may also cause surface quality problems of the material.
Shear speed control in practical applications:
In the actual processing process, the appropriate shear speed is selected according to the needs to optimize the shear force and cutting quality:
– High shear speed
In high-speed processing processes such as laser cutting and laser marking, it is usually necessary to increase the processing speed to improve production efficiency. At the same time, due to the increase in material temperature, the shear force is often lower. Suitable for materials that require high cutting edge quality and can tolerate temperature rise.
– Low shear speed
In conventional mechanical shearing (such as stamping, shearing machine), the speed is usually low and the shear force is large. This is suitable for situations with high requirements for cutting quality and precision.
Shear speed and material temperature effect:
The shear speed is closely related to the temperature effect of the material, especially when cutting at high speed, the rise in material surface temperature may affect the shear strength and cutting performance of the material. For some materials (such as aluminum alloys), the shear force will be significantly reduced during high-speed shearing due to temperature rise and material softening. For some high-hardness materials (such as tool steel), the change in shear force may be small.
High shear speed usually leads to a reduction in shear force, mainly due to the combined effect of factors such as temperature increase, material softening, and intensified plastic flow. Low shear speed may lead to larger shear force because the material has higher shear strength and the deformation process is slower.
In the metal processing process, optimizing the shear speed is an important means to improve production efficiency, reduce energy consumption and extend tool life. Therefore, when selecting the shear speed, factors such as the nature of the material, the required cutting quality, the capacity of the equipment, and production efficiency need to be considered comprehensively.
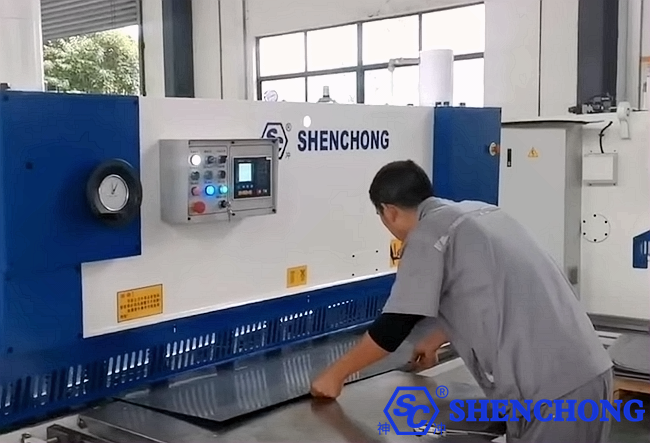
7) Cutting method and tools
Single cut vs. multiple cuts:
Some materials may require multiple step-by-step cuts to complete the entire cutting process, which can reduce the force required for each cut.
Tool shape and material:
The shape of the cutting tool (such as the bend angle of the blade, the sharpness of the edge) and the material (such as hardened tool steel) directly affect the shear force.
8) Lubrication and friction
Lubrication:
During the shearing process, lubrication can reduce the friction between the blade and the material surface, reduce the shear force, and increase the cutting efficiency.
Friction:
High friction will lead to increased shear force because the friction force needs to overcome more resistance, which increases the energy consumption in the shearing process.
9) Temperature of the material
The effect of temperature on shear strength:
At high temperatures, the shear strength of metals is generally lower, so the shear force is smaller. Conversely, at low temperatures, the shear strength of the material is higher and a greater shear force is required.
Hot shearing:
Some metalworking processes, such as hot shearing, heat the metal sheet to reduce its shear strength, thereby reducing the shear force.
10) Crystalline structure of materials
The crystal structure of metal materials affects their shear strength. For example, when the grains of metal are finer, their shear strength is higher and a greater shear force is required. The lattice defects of the metal (such as dislocations) also affect the shear force.
11) Ductility and hardness of materials
Materials with better ductility (such as copper and aluminum) are generally easier to shear than materials with higher hardness (such as hard steel). Therefore, more ductile materials may require less shear force.
Materials with higher hardness (such as high-strength steel, cemented carbide, etc.) generally have higher shear strength, resulting in the need for greater shear force.
12) Material pretreatment (such as annealing, hardening, etc.)
Annealing:
Annealing makes the metal material softer and reduces its shear strength, thereby reducing shear forces.
Hardening:
Metal materials treated by hardening (such as quenching) are harder and have higher shear strength, so they require greater shear force to cut.
Overall, shear force is the result of multiple factors. In actual processing, appropriate shearing conditions should be selected according to material properties and processing requirements to obtain ideal shearing effects.
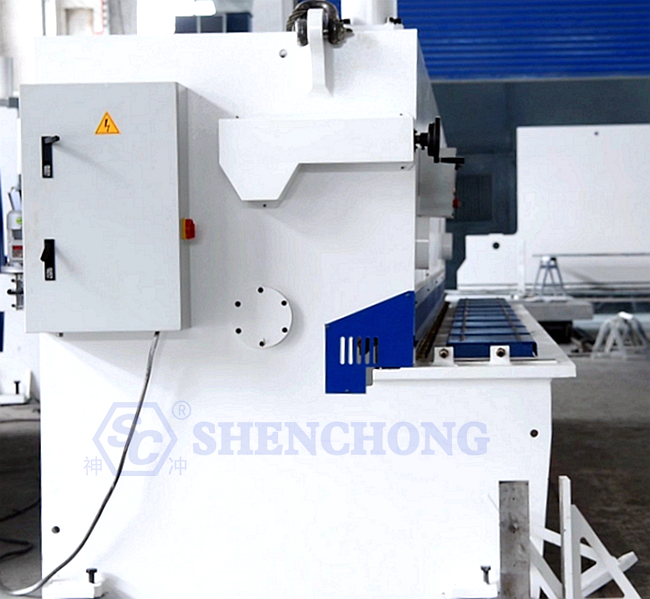
2. Relationship between shear force and sheet metal properties
There is a close relationship between shear force and sheet metal properties, mainly reflected in the shear strength, hardness, ductility and other aspects of the material. The physical and mechanical properties of different materials directly affect their behavior during shearing and the required shear force. Let’s explore the relationship between metal shear force and material properties in detail.
Shear strength:
Shear strength is the maximum resistance of a metal sheet in shear state, indicating the critical stress at which the material begins to break under the action of shear force. The greater the shear strength, the greater the shear force.
Different metal materials have different shear strengths. For example, steel usually has a higher shear strength than aluminum alloys.
Material Thickness:
The thicker the plate, the greater the shear force. This is because the shear force required for thick plates is proportional to the thickness.
Shear Length:
The longer the shear blade is in contact with the metal plate, the greater the shear force. A longer shear length means a larger shear area, which requires a greater shear force to overcome the shear strength of the material.
The ability of sheet metal to resist shear forces depends on a combination of material properties (like shear strength, tensile strength, hardness, and ductility) and external factors like thickness, grain structure, and surface conditions. Thicker, harder, and stronger materials will generally resist higher shear forces, while softer, more ductile materials will deform more easily. The relationship between these factors plays a critical role in processes like cutting, punching, and forming sheet metal.
3. Conclusion
The shear force of metal plates is affected by multiple factors, including:
- The shear strength of the material.
- The thickness of the plate and the shear length.
- The sharpness, design and angle of the blade.
- The temperature, shear speed and lubrication conditions.
- The pretreatment and hardness of the material.
In practical applications, optimizing these factors (such as selecting appropriate shearing tools, adjusting shear speed, and heating materials reasonably) can effectively reduce the metal shear force, improve cutting efficiency and processing quality.