Introduction
Table of Contents
Sheet metal bending is a critical manufacturing process used to shape metal plates into the desired angle and shape. It plays an important role in industries such as automotive, aerospace, construction, and electronics. But why do sheet metal plates bending often fail to maintain their shape? The answer lies in a phenomenon called springback. One of the main challenges encountered during the bending process is springback. This occurs when the metal partially returns to its original shape after bending, which is influenced by factors such as material properties, bending radius, and applied force. Springback in sheet metal bending may result in inaccurate final products. In this article, we will explore the reasons for springback in sheet metal bending, the impact of springback on accuracy, and effective strategies to minimize springback. Understanding these concepts can greatly improve the accuracy and quality of metal processing works.
What Is Springback In Sheet Metal Bending?
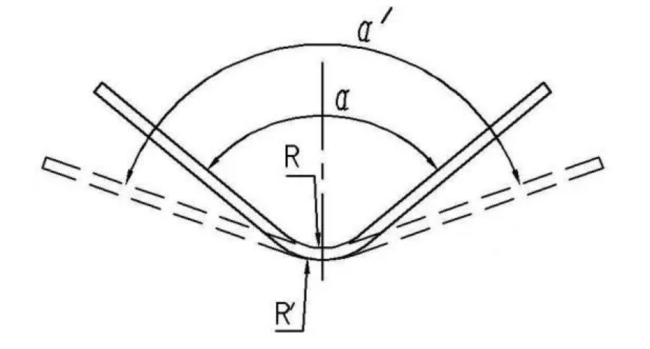
When a metal plate cannot maintain the expected precise angle or curvature after bending, springback occurs. When force is applied to bend a metal plate, it undergoes elastic and plastic deformation. Plastic deformation is permanent, while elastic deformation is temporary and will recover once the external force is eliminated. The recovery of this elastic deformation causes the sheet to partially return to its original position, resulting in springback.
Physical Principle
The principle behind springback lies in the internal stresses generated during bending. When the sheet is bent, the outer surface of the bend is stretched (tensile stress), while the inner surface is compressed (compressive stress). Once the bending force is removed, the elastic component of these stresses attempts to return the material to its undeformed state. The degree of springback depends on the balance between elastic and plastic deformation within the material.
Factors Affecting Springback
Several factors influence the amount of springback that occurs in sheet metal bending. Understanding these factors can help in predicting and controlling springback during the design and manufacturing process.
1. Material Properties
- Yield Strength: Metals with higher yield strength are more prone to springback because they resist permanent deformation and have a greater tendency to return to their original shape. High-strength steels and aluminum alloys often exhibit more significant springback compared to low-carbon steel.
- Elastic Modulus: A material’s elastic modulus, or stiffness, defines its ability to return to its original shape after being deformed. Metals with a higher elastic modulus, such as steel, exhibit more springback than softer materials like aluminum or copper.
The size of the springback angle is directly proportional to the yield strength αa of the material and inversely proportional to the elastic modulus (E). That is to say, the higher the yield strength of the material, the smaller the elastic modulus, and the smaller the springback in the sheet metal. On the contrary, the greater the springback.
For bend workpiece with high precision requirements, in order to minimize springback, low-carbon steel should be selected instead of materials such as high carbon steel or stainless steel.
2. Sheet Thickness
Thicker sheets tend to experience less springback than thinner ones. This is because thicker sheets undergo more plastic deformation during bending, which reduces the effect of elastic recovery. Conversely, thinner sheets are more flexible and elastic, leading to more pronounced springback.
3. Bending Radius
The ratio of the sheet thickness to the bend radius significantly impacts springback. When the bend radius is large relative to the sheet thickness, more elastic deformation occurs, leading to greater springback. A smaller bending radius results in more plastic deformation and reduces springback.
This is an important concept. When material properties permit, the fillet of sheet metal bent parts should choose the smallest possible bending radius to improve machining precision. It is particularly noteworthy that parts with large bending radii pose certain challenges in controlling machining accuracy and quality.
4. Bending Angle
The greater the bending angle, the more significant the springback in sheet metal bending effect. For example, when bending a sheet to a large angle (such as 90 degrees or more), the material experiences more stress, which increases the likelihood of springback once the bending force is removed.
On the contrary, a smaller bending center angle means a smaller deformation area, resulting in a smaller cumulative amount of elastic deformation and therefore a smaller total springback in sheet metal bending.
5. Bending Method
Different bending methods, such as air bending and bottoming, affect the degree of springback. In air bending, the sheet is only partially supported, leading to more elastic recovery, whereas in bottoming (where the sheet is fully pressed into the die), the metal is constrained more tightly, reducing springback.
6. Influence Of Bending Force F
Given a certain bending radius, center angle, and material thickness, a larger bending force F will result in smaller springback, while a smaller bending force will result in larger springback in sheet metal bending.
Calculate Springback Valve In Sheet Metal Bending
Calculating springback in sheet metal bending involves determining the difference between the initial bend angle and the angle after the material recovers some of its original shape due to elastic recovery. Here’s a step-by-step process for estimating and calculating springback.
Key Parameters
The amount of springback depends on several factors like material properties, thickness, bend radius, and the bending method.
- Young’s Modulus (E):This is the modulus of elasticity for the material, which measures its stiffness.
- Yield Strength (σ_y):This is the stress at which the material begins to deform plastically.
- Initial Bend Radius (R_b):The radius of the bend formed by the punch before springback.
- Sheet Thickness (t):The thickness of the sheet metal.
- Final Bend Angle (θ):The angle after springback.
Springback Factor (Ks)
One of the simplest ways to calculate springback is by using the springback factor Ks, which is the ratio of the final bend angle after springback to the initial bend angle before springback. It can be estimated using the following equation:
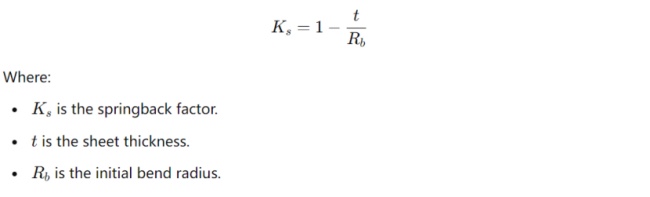
Springback Angle Calculation
The springback angle can be calculated by multiplying the initial bend angle by the springback factor:
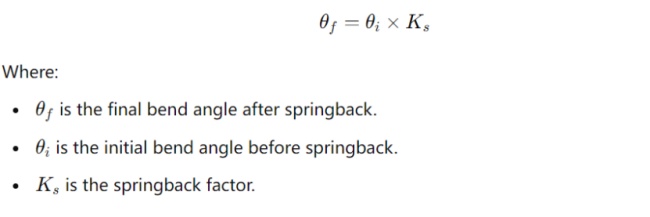
Springback Estimation Based on Material Properties
For a more detailed approach, especially when using high-strength materials, springback can be calculated using the following formula:
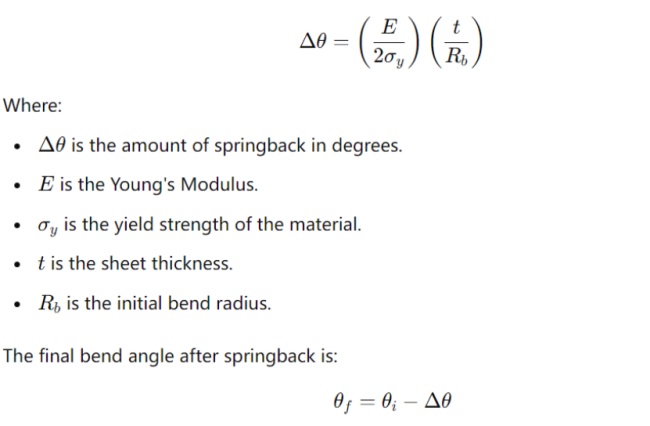
Example Calculation
Let’s assume you have the following data:
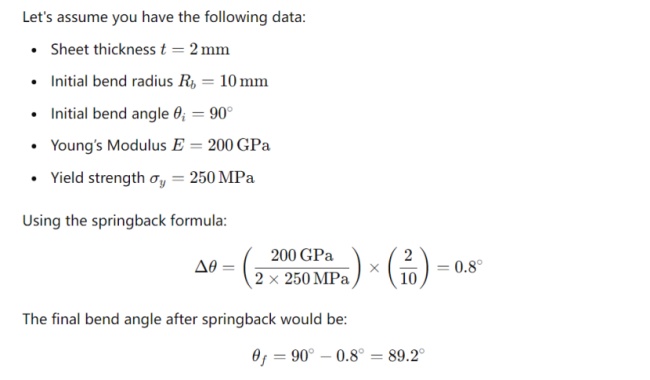
Thus, after springback, the bend angle will be approximately 89.2∘89.2^\circ89.2∘, indicating a small amount of recovery. Adjusting the bend angle during the process compensates for this.
Solutions To Mitigate Springback
Although springback in sheet metal bending cannot be completely eliminated, various strategies can be employed to control and minimize its effects during the bending process.
Applications and Importance of Controlling Springback
Springback control is essential in industries where precision is critical, such as automotive and aerospace. Components like car body panels, aircraft skins, and structural frames must adhere to tight tolerances. Excessive springback can lead to costly rework, waste of materials, or even compromised structural integrity.
In mass production, minimizing springback helps maintain consistent quality across large batches, reducing material costs and improving efficiency. Accurate control of springback also allows manufacturers to use high-strength materials without compromising product quality.
Improve the Design of Bent Parts
- Improving the structural design of bendingpart can reduce the springback angle without affecting their functionality. For example, suppressing the strengthening ribs in the curved area or using formed edges can increase the stiffness and plastic deformation of the curved part, thereby reducing springback.
- Using materials with high elastic modulus, low yield strength, low hardness, and good plasticity can reduce rebound and facilitate rebound control while meeting usage requirements.
Improve Process Measures
1. Overbending
Overbending involves bending the sheet metal slightly beyond the desired angle to compensate for springback. This technique requires experience and precise calculations to determine the correct amount of overbend needed for different materials and thicknesses.
2. Bending Force Adjustment
Increasing the bending force or applying a secondary bending operation can help increase plastic deformation in the material. This reduces the elastic recovery and minimizes springback. This technique is particularly effective in reducing springback for high-strength materials.
3. Using a Smaller Bend Radius
By designing the bend radius to be smaller, the material experiences more plastic deformation, which reduces the elastic recovery responsible for springback. However, care must be taken to avoid creating too small a radius, which can lead to cracking or damage to the material.
4. Material Selection and Treatment
Choosing materials with lower yield strength or using heat treatments to reduce material hardness can reduce springback. For example, annealing can be used to soften metals, making them more ductile and less prone to springback.
5. Finite Element Analysis (FEA) Simulation
Modern software tools, such as Finite Element Analysis (FEA), allow manufacturers to simulate the bending process and predict the degree of springback before physically bending the sheet. These simulations help engineers adjust bending parameters to ensure accurate results, reducing trial and error in the production phase.
Adjusting Bending Molds Clearance
Reducing the gap between molds helps to minimize springback. When the gap between the curved die surfaces is less than the material thickness, rebound can be significantly reduced, even leading to slight negative rebound. A too small gap can lead to material thinning, surface scratches on the workpiece, and shortened mold life. When the thickness of the slab deviates negatively, the excessive gap formed between the punch and the mold can also cause rebound. The solution is to design adjustable gap bending molds.
Improve the Design of Bending Molds
Based on estimated or experimental rebound values, we can compensate (or deduct) within the shape and size range of the mold working parts to make the bent parts meet the shape and size requirements of the product drawing.
1) The bending rebound angle of soft materials such as 0215, 0235, 08, 10, 20, and H2 soft brass is less than 5 °. When the thickness deviation of the material is small, a slope (rebound compensation angle) can be designed on the punch or mold. The gap between the punch and the mold is equal to the minimum material thickness, and even a negative gap can be used to overcome rebound.
2) For soft materials such as Q215, Q235, 08, 10, 20, and H62 soft brass, when the material thickness exceeds 0.8mm and the bending radius is large, the working part of the punch can be designed with local protrusions. This concentrates the working pressure of the punch at the curved corners.
By increasing the stress at the bend, we enhanced the plastic deformation component in the deformation zone, improved stress distribution, thereby reducing elastic deformation and minimizing rebound to the greatest extent possible.
3) For hard materials such as Q275, 45, 50, H62, when the bending radius r>t, a rebound compensation angle can be designed on the mold or punch based on pre-estimated or experimentally obtained rebound values to eliminate rebound.
Alternatively, the top of the mold can be designed as an arc-shaped surface (for U-shaped bending), resulting in local reverse bending at the bottom. That is to say, when the part is removed from the mold, the rebound of the reverse curve will cause negative rebound on both sides, offsetting the positive rebound of the side walls.
4) For Z-shaped bending, the two bending angles of Z-shaped bending may have different rebound values, which may cause the top and bottom surfaces of Z-shaped parts to be non parallel. To avoid this phenomenon, the punch and mold should be tilted outward at an angle of Δ φ. For cold-rolled plates with a thickness less than 1mm, the inclination angle is generally taken as 2 °~3 °.
5) For softer materials, rubber molds can be used instead of rigid molds, as shown in Figure 1-10. Due to the fact that rubber can transmit pressure in various directions like a liquid in a rigid container, the bending process undergoes beneficial changes compared to using rigid molds.
The board is fully supported on the rubber, with stronger support in the middle than on the sides. Therefore, when the two straight walls of the board bend around the rounded corners of the punch, they fully adhere to the surface of the punch, and the straight walls are less prone to excessive bending, reducing rebound.
If high hardness rubber elastomers are used, the effect is even better. In addition to high precision, the use of rubber molds does not leave scratches on the surface of bent parts, and the versatility of rubber and rubber elastomer molds is very good.
Conclusion
Springback is an inherent challenge in sheet metal bending, driven by the material’s elastic recovery after plastic deformation. Factors such as material properties, sheet thickness, bend radius, and bending method all influence the degree of springback. However, by employing strategies such as overbending, adjusting bending forces, and utilizing simulation tools, manufacturers can effectively control springback and produce high-quality, precision-formed parts. As the demand for lightweight, strong, and precise components continues to grow in industries like automotive and aerospace, mastering the management of springback will remain a critical aspect of sheet metal fabrication.
SC Machinery is a professional CNC press brake and punch press machine factory, and we provide bending solutions for clients for than 25 years. Please feel free to contact with us if you need bending machines.