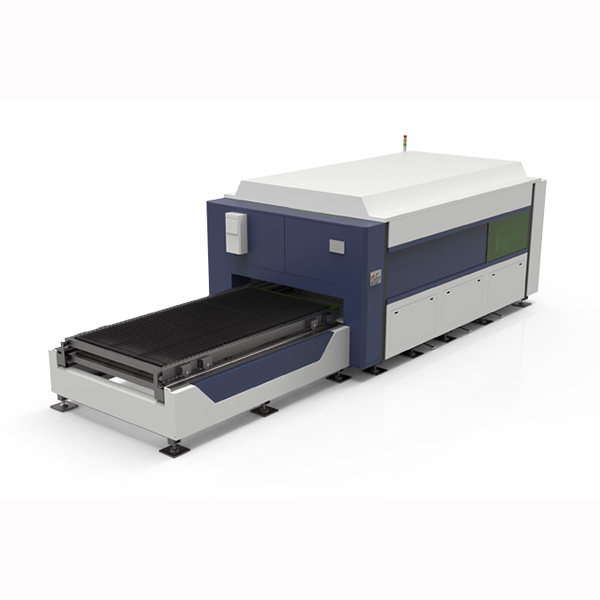
In current industrial production, in order to facilitate transportation and storage, boards are harvested into rolls. During production and processing, the coil material is uncoiled and leveled to form a sheet metal, which is then imported into laser cutting equipment for cutting. The coil laser cutting production line, also known as the coil laser cutting machine, is mainly composed of a CAD/CAM programming system, an automatic unwinding and leveling system, a servo automatic feeding system, and a laser cutting system. It can operate according to the plan, greatly improving production efficiency, reducing labor burden, reducing production costs, and occupying less land. It has the characteristics of high efficiency, high precision, low cost, and easy operation.
The FC series of SC SHENCHONG Blanking Production Line is a high-end coil laser cutting machine that solves the problem of metal coil uncoiling, cutting, and palletizing. It is designed with full process automation, including uncoiling, leveling, cutting, cutting, and palletizing, achieving full process automation. It can continuously cut and produce, saving time, materials, and labor.
The fully automatic Steel Coils Laser Metal Cutting Machine with Decoiling and Levelling breaks the traditional processing method, and can simultaneously realize the four functions of raw material leveling, feeding, cutting, and unloading.
The innovative design of the unique hydraulic uncoiler allows the weight of the coil to reach 8T/10T/15T in a single feeding, breaking through the tonnage limitations of traditional feeding equipment. After uncoiling the coil, it is leveled using a quadruple 9-roll leveling machine/quadruple 11-roll leveling machine to fully release the stress on the sheet, making it smoother and providing a better cutting experience. Innovative research and development of laser cutting heads with high cutting efficiency and wide processing range, capable of batch processing various types of coils such as carbon steel coils, galvanized coils, and stainless steel coils.
Model |
SC1502FC |
SC1503FC |
|
Applicable standard coils and processing thickness |
Carbon steel coil |
0.5-2mm |
0.5-3mm |
Galvanized coil |
0.5-2mm |
0.5-3mm |
|
Stainless steel coil |
0.5-1.5mm |
0.5-3mm |
|
Hot rolled steel coils |
/ |
/ |
|
Laser Power |
1000W-6000W |
||
Processing Width |
800-1500mm |
||
Processing Weight |
8T/10T/15T |
Heavy duty material rack, cantilever structure, stress annealing, high load-bearing capacity of the rack, stable operation, frequency conversion control, stable material discharge, hydraulic expansion, flexible operation
The efficiency of single feeding is doubled, and the weight of the coil material in a single feeding can reach 8T/10T/15T, breaking through the tonnage limit of traditional feeding equipment in the past
Optional gantry type unloading system/robot type unloading system
Implement automatic sorting.
SC SHENCHONG automatic coil feeding laser cutting machine production line achieves 24-hour online non-stop continuous cutting, cutting and feeding uninterrupted operation, cutting while moving. The coil conveying equipment continuously transports materials, with synchronous feeding and discharging. Its superior continuous conveying performance and seamless power cutting connection greatly save time and efficiently interpret the first productivity for users.
Abandoning the traditional method of material cutting for press molds, eliminating their expensive manufacturing costs and drawbacks of long-term storage space, replacing press machines and material cutting molds to achieve automatic material cutting for metal strips, with low operating costs and high production efficiency, maximizing material utilization, shortening production cycles, and reducing investment in cutting equipment and mold consumption costs.
Changing the traditional flying shear assembly line working mode, using laser cutting machines to cut, greatly improving cutting accuracy, flexible production, laser cutting, one-time forming, without the need for post-processing, high cutting surface quality, no burrs, and no small cracks.
By adopting advanced optimization layout software and control system, automatic material layout and common edge cutting are achieved, saving cutting time, reducing perforation frequency, reducing waste generation, and pursuing maximum material utilization.
Can you pls tell us your plate thickness and length? Our sales will recommend machine model for you.