What is a panel bender? Welcome to read below ultimate guide and you can find all you need to know about panel benders.
In today’s highly competitive manufacturing landscape, utilizing the right technology is crucial for success. Compared with other bending machine, panel benders have more complete functions, higher automation levels, and safer operation environment in the metal manufacturing industry. When choosing a press brake and a panel bender machine, manufacturers should consider the specific needs of their production process. In metal manufacturing, accuracy and efficiency are crucial, and panel benders perform excellently in both aspects. The use of panel benders can also reduce labor and material costs through efficient mass production. The production cost of a panel bender is much lower than that of a press brake in some working condition, but the operation of a panel bender is simple. The CNC (Computer Numerical Control) panel bending center represents the pinnacle of panel bender technology. This article explores the origin and development of panel bending machines, from basic operations to advanced automation, and how they fundamentally change metal manufacturing. Whether you are a small operator or a large industrial enterprise purchaser, understanding the functions of these machines can significantly improve your production efficiency and product quality.
Table of Contents
Working Principle Of Sheet Metal Panel Bender
What is a panel bender working principle? The magic behind the seamless operation of the panel bender lies in its complex working mechanism, which combines precision engineering with advanced technology. This collaborative effect enables machines to convert flat metal plates into precise shapes and angles, which is crucial for various applications in industries from automobiles to construction.
Difference From Hydraulic Press Brake
The working principle of the panel bending machine is different from that of the hydraulic press brake. When operating a panel bender, the operator only needs to load the metal plate. The positioning, bending, and reversal of workpieces are controlled by machines and software.
The panel bending machine will not press the metal plate into the lower mold through a punch. The panel bender is a pair of blades that fix the sheet metal and bend it up and down to form the final contour. When bending a complex angle, the blade oscillates around a bending point until the desired angle is reached.
Panel bender molds will not move up and down in a straight line, which is different from a press brake tooling. After positioning the sheet, the panel bending machine can quickly adjust to the correct tool length. When bending, after positioning the workpiece, the clamping beam tool clamps the workpiece in place. Move the lower tool upwards to bend in the positive direction and move the top tool downwards to bend in the negative direction.
What Is A Panel Bender Working Principle?
Initially, the preparation phase begins with selecting the metal plate to be bent. The operator inputs necessary parameters into the control system, including metal type, thickness, size, and required bending angle. This setup stage is crucial to ensure that the machine’s settings meet the specific requirements of the work at hand.
After setting up, place the metal plate on the workbench of the machine. The rear gauge is adjusted according to the programming settings to accurately align the sheet for the first bending. This positioning is crucial for the accuracy of bending position and angle.
Once the sheet is in place, the clamping system will activate to secure the metal sheet, preventing any movement during the bending process. This stability is crucial for achieving precise bending and maintaining material dimensional integrity.
The bending process begins when the panel bender blade applies force to the metal plate to produce bending at a specified angle. The control system carefully adjusts the force and angle to ensure precise execution of each bend. Based on the complexity of the parts, the machine may perform multiple bends in sequence, and if necessary, reposition the sheet with the help of a rear gauge.
Throughout the entire operation process, the control system continuously monitors the process and makes real-time adjustments to compensate for any changes in material properties or external factors. This adaptive ability ensures that the final product meets the specified dimensions and tolerances, demonstrating the accuracy and flexibility of the machine.
In summary, the panel bending machine operates through careful preparation, positioning, fixation, bending, and continuous monitoring processes. This process highlights the role of machines in modern manufacturing, where accuracy, efficiency, and adaptability are crucial. By understanding the working principles of these machines, operators can optimize their use, thereby improving the productivity and quality of metal forming operations.
Types Of Panel Bender Machines
A panel bending machine is a machine that functions similar to a press brake, but is more automated and has more functions. In the past, manual panel benders were used for metal bending. With the continuous advancement of technology, sheet metal forming has entered the era of automation. There are various types of sheet metal panel bender machines, each designed to meet the different needs of the manufacturing industry. Sheet metal panel benders can be divided into manual, semi-automatic, and fully automatic panel bending centers. Automatic tool changing system, measurement system, etc. to improve metal bending efficiency. Let’s explore different types of panel bending machines, their advantages and disadvantages, and determine the most suitable project for them.
Manual Panel Bender
The manual panel bender is simple and reasonably priced. However, they do require skilled operators and are not efficient for large-scale production. The semi-automatic panel bending machine integrates manual and automatic functions, which can reduce the need for continuous manual intervention.
- Advantages: The manual panel benderis simple and affordable. They are very suitable for small workshops or enterprises that are just starting to engage in sheet metal manufacturing. These machines provide direct control over the bending process, allowing for adjustments based on the operator’s skills and experience.
- Disadvantages: The main drawback is that they rely on physical labor, which can lead to inconsistent production and limit output and speed. In addition, they require higher levels of operator skills to achieve bending accuracy.
Suitable projects: Manual panel bending machines are most suitable for customized or small batch projects, where operator flexibility and craftsmanship can be used to produce unique or customized products.
Semi-Automatic Panel Bending Machine
- Advantages: Semi automatic models achieve a balance between manual and fully automatic machines, providing higher levels of accuracy and productivity without the need for comprehensive investment in automation. Compared to manual panel bender, they require less manual operation and provide more consistent results.
- Disadvantage: Although semi-automatic panel bending machines improve efficiency and consistency, compared to fully automatic models, semi-automatic panel bending machines still require operator intervention in certain tasks, thereby limiting their production.
Suitable projects: These machines are the ideal choice for medium-sized production operations or workshops handling various projects, providing a good balance between speed, flexibility, and cost.
Fully Automatic Panel Bending Machine
The blade of the panel bending machine can form a flange in the horizontal direction, while the blank holder in the other direction can maintain the stability of the material. Standard curved blades can produce many types of radii. The bending of the panel bending machine will not leave any marks.
Compared to the bending workpiece of the CNC press brake machine, it will be more beautiful and cleaner. Compared with previous bending machines, this automatic panel bender has the advantages of being labor-saving and high-speed.
Panel bender is a widely used tool that can perform fully automatic bending processes, including automatic loading and unloading of tools, feeding, measurement, bending, and output. It has a short bending stroke and fast feed rate, which can produce highly accurate workpieces.
Special tools can be used for complex bending, such as crimping and offset bending. However, not all workpieces are suitable for panel bending machines. Generally speaking, it is more suitable for producing box shaped workpieces because it can bend the entire side of the box in one go.
Nowadays, press brake can also connect to robots to achieve complete automation, but their functions are not as complete as those of robot panel bending centers in some bending conditions.
- Advantages: The fully automatic panel benderis the pinnacle of metal manufacturing technology and efficiency. They provide the highest level of accuracy, speed, and consistency with minimal human intervention. Thanks to advanced control systems and automation technology, these machines can easily handle a large amount of work.
- Disadvantages: The main drawbacks are high investment costs and the complexity of operation and maintenance. In addition, compared to manual or semi-automatic machines, the flexibility of handling unique one-time items may be reduced.Also, panel bender is only suitable to bend thin plate, which means the machine cannot bend the plate thickness above 4mm.
Suitable project: The fully automatic panel bending machine is most suitable for large-scale production environments where efficiency, speed, and repeatability are crucial. They have performed well in industries such as automotive, electrical manufacturing, and construction, where precision and productivity are crucial.
The Characteristics Of A CNC Panel Bender
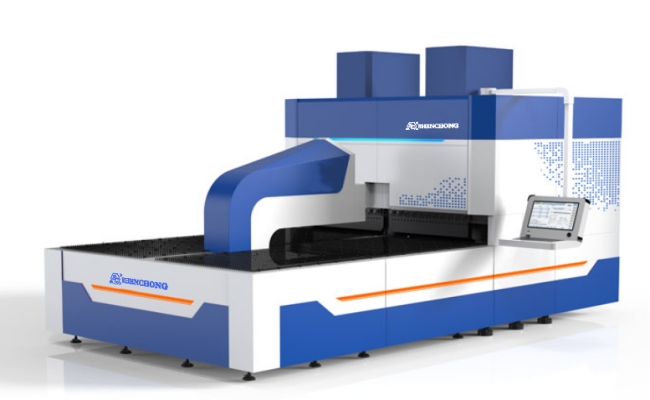
Advantages
A panel bender is a specialized machine used for bending metal sheets. It has an automatic tool changer, which reduces installation time. A complete set of tools can complete the complex bending of all workpieces. The tool of the panel bending machine has a very small interaction area on the surface of the metal plate.
The surface of the workpiece produced in this way has almost no scratches. The tool wear of the automatic panel bender machine is also minimal because there is little friction between the tool and the metal surface. The entire process of the sheet metal bending can be automated, saving human resources.
The bending angle variation of a panel bender is formed by the movement of the upper and lower blades, so its tools are not as complex as those of a bending machine. The fully automatic panel bending machine is equipped with an automatic tool changer, which can quickly change tools and adjust bending operations at various angles in various bending tasks.
Some large workpieces with positive and negative flanges are suitable for manufacturing using panel bending machines. If the panel bender can automatically set the billet gripper, only one operator can operate it. The panel bending machine only applies pressure to the metal plate through the upper and lower blades.
This bending method makes the changes and rebound of the metal plate less obvious, and can bend the entire box side in one go. The bending method of the panel bender is very suitable for producing boxes, lids, and similar items.
There are some safety issues when using modern pressure brakes to manufacture small parts. The panel bender can produce smaller profiles through clamping claws or manual operation.
Disadvantages
Size And Material Limitations
- Size limitation: Plate bending machines are usually suitable for processing small and medium-sized metal plates, but their ability to process oversized or ultra thick plates is limited. The bending of extra large/thick plates requires the use of larger hydraulic bending machines or other specialized equipment.
- Material limitations: Panel bendermachines are mainly suitable for processing relatively soft metals, such as aluminum and stainless steel. However, their performance may not be suitable for processing harder metal materials such as steel plates, leading to potential mold wear or reduced bending accuracy and precision.
Shape And Batch Restrictions
- Shape limitation: Panel bending machines are good at bending flat materials, but their ability to handle complex three-dimensional bending structures is limited, which may need to be combined with other manufacturing processes such as welding.
- Batch limitations: Although automatic panel bending machines have automation advantages, their advantages may not be significant for small batch, multi variety processing orders, and may even increase the time and cost associated with process adjustments and mold replacement.
Other Restrictions
- Structural limitations: Due to the limited throat depth and opening height of panel benders, they are more suitable for producing smaller flanges. The position of the clamping tool and bending blade on the panel bending machine makes it relatively difficult to perform internal bending on the machine.
- Noise issue: The sheet metal bending machine produces significant noise during high-speed operation, which may have an impact on the factory environment and operators. Measures such as sound insulation and noise reduction need to be taken.
- High cost: Compared to traditional bending machines, panel bending machines are relatively expensive and therefore less popular in certain application scenarios.
Basic Knowledge Of Sheet Metal Bending Machines: Components And Mechanics
In the field of sheet metal forming, panel bending machines are the cornerstone of efficient and precise metal bending. This engineering miracle not only simplifies the bending process, but also ensures unparalleled accuracy and repeatability. The core of a CNC panel bender machine is to process metal plates into specific angles and shapes to adapt to a wide range of industrial applications. Let’s uncover and understand the components and mechanisms of the automatic panel bender.
What Is a Panel Bender Key Component And Functions
Firstly, the frame of the panel bender machine provides necessary support and stability. It is made of high-strength materials and can withstand strict bending operations without affecting accuracy.
The control system is the brain of the automatic CNC panel bender. Modern panel bending machines are equipped with complex software that enables precise control of the bending process. This system enables operators to input parameters such as bending angle and sheet thickness, ensuring accurate execution of each bend. In addition, the control system provides the ability to store and call duplicate production running programs, improving efficiency and consistency.
The bending blade is a critical component that performs the actual bending action. Its design varies according to the specific requirements of the machine model and bending process, to adapt to various material thicknesses and bending angles, ensuring flexibility in a range of applications. The material and structure of the bending blade are key to achieving clean and crisp bending.
Another basic component is the clamping system. During the bending operation, it can firmly fix the metal plate in place, prevent slipping, and ensure accuracy. The design of clamping systems varies, and some machines use pneumatic or hydraulic clamping to increase strength and reliability.
Finally, backgauge plays a crucial role in accurately positioning the metal plate before each bend. The accuracy of bending is not only related to the bending action, but also to the correct positioning of the sheet metal before bending. Backgauge is adjustable and programmable to move to specific positions, enabling precise control of the bending position. Backage ensures that every product is processed consistently, which is crucial for mass production and maintaining high quality standards.
The Application Of Automatic Panel Bender
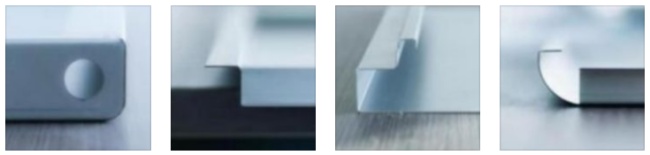
Panel bender is very suitable for producing square, large, rectangular and thin thickness workpieces when bending and forming metal sheets. These workpieces have high requirements for appearance and shape. The surface of the workpiece manufactured by the sheet metal bending machine has almost no scratches.
Electrical appliances such as refrigerators, air conditioners, as well as doors, elevators, metal furniture, etc. When choosing a sheet metal bending machine, it is important to understand which workpieces its bending method is suitable for.
Due to the automated nature of bending, panel benders not only take on more work, but these units also help complete more complex tasks such as edge folding. In addition, panel bending machines can achieve unparalleled accuracy and repeatability in metal plate manufacturing.
Panel Bender Bending Application: Material Selection
Panel bending machines have multi-functional bending capabilities and have become an indispensable tool in the metal manufacturing industry. These machines are designed to process various materials, each with its unique characteristics and applications. Understanding which materials can be processed is crucial for maximizing the potential of panel bending machines and ensuring the efficiency of manufacturing projects. The following is an overview of the most commonly used forming materials for these dynamic machines.
- Aluminum: Due to its lightweight and corrosion resistance, aluminum is a popular choice for various applications. The panel bending machine can easily process aluminum sheets, making them an ideal choice for automotive, aerospace, and construction projects. But if not handled properly, its surface is prone to damage and cracking, so precision is required.
- Steel: Known for its strength and durability, steel is a fundamental material in the manufacturing industry. Panel bending machines can handle both soft steel and high-strength steel, and are widely used in manufacturing, construction, and infrastructure.
- Stainless steel: Stainless steel is known for its beautiful surface treatment, corrosion resistance, and oxidation resistance, and is commonly used in medical, food processing, and construction projects. The panel bending machine can shape stainless steel plates for such applications.
- Copper: Copper has good conductivity and is often used for panel bending and machining of electrical components, roofs, and decorative components.
- Brass: Brass is an alloy of copper and zinc, known for its ductility and corrosion resistance. It is often used for decoration, construction, and marine applications. Usually chosen for its conductivity and aesthetics. Their softness requires precise methods to prevent excessive bending and deformation.
Above materials can be bent by panel bender, but operators need to pay attention to the sheet metal thickness before bending. Panel bender only can bend thin thickness plate, so users should check with panel bender manufacturers if the machine can meet the bending requirements.
How To Choose The Right Panel Bending Machine?
Choosing the appropriate panel bender is a key decision that significantly affects the efficiency, productivity, and quality of metal manufacturing operations. With various models and configurations, it is important to consider several key factors to ensure that the machine you choose meets your specific bending needs.
- Material type and thickness: Evaluate the range of materials planned for bending, including their thickness. Different machines have different capacities, so choosing a machine that can handle project diversity is crucial.
- The complexity of bending: Consider the complexity of the parts you need to produce. If your project requires complex bends or shapes, look for machines with advanced and programmable features to meet these requirements.
- Yield: Evaluate your yield. For large-scale operations, a fully automatic panel bending machine may be the best choice due to its speed and efficiency. For short distance operations with lower volumes or more variations, semi-automatic or manual machines can provide you with the flexibility you need.
- Budget: Budget is always a consideration factor. Fully automated machines provide the highest productivity, but the price is also higher. Based on your production needs and efficiency benefits, weigh the initial investment against the potential return on investment.
- Future needs: Think about your future projects and potential growth. Investing in a machine with features that exceed your current needs can provide flexibility and prevent the need for early upgrades as your business expands.
- Support and maintenance: Understand the support and maintenance services provided by the manufacturer. Reliable after-sales support and convenient maintenance are crucial for minimizing downtime and maintaining productivity.
By carefully considering these factors, you can choose a panel bender that not only meets your current needs but also meets your long-term operational goals. The right machine will be a valuable asset in your manufacturing factory, enhancing your capabilities and helping you maintain a competitive advantage in the market.
Automatic Panel Bender Future Trends
The integration of automation in sheet metal bending machines has completely changed the metal manufacturing industry, greatly affecting the cost-effectiveness of operations. Automation brings precision, speed, and efficiency to the bending process, but its value is not limited to improving production capacity.
Full Automation Panel Bender Provides Several Key Advantages
Improve production speed: The running speed of automated panel bending machines is faster than manual or semi-automatic machines, greatly reducing production time. This increased speed allows for higher throughput, enabling enterprises to more effectively complete larger orders.
Reduce labor costs: Automation reduces the need for manual labor during the bending process. Although skilled operators are still needed to supervise operations, the required number of personnel is relatively low, resulting in significant savings in labor costs.
Enhanced precision and consistency: Automated machines provide high precision and consistency during bending, reducing error and rework rates. This consistency ensures the efficiency of material use, minimizes waste, and improves the quality of the final product.
Optimize material utilization: Advanced software used in automated panel bending machines can optimize material layout, further reduce waste, and maximize resource utilization. Over time, this optimization helps to save material costs.
Conclusion
Automation panel bender significantly improve production efficiency, reducing waste, and lowering operating costs. Although the upfront costs may be higher, the long-term benefits of automation provide a convincing reason for investment, especially for enterprises looking to expand production capacity and improve market competitiveness.
SC Machinery is at the forefront of innovation and quality, and is a top panel bender manufacturer. We commitment to excellence, focus on cutting-edge solutions, and provide clients with professional solutions to improve the sheet metal production lines.