Table of Contents
The press brake tooling is a mold used by the hydraulic press brake machine to shape and process sheet materials. This tool consists of various parts, and different molds are made up of different parts. It mainly achieves the processing of the shape of the object by changing the physical state of the formed material. A tool used to turn a blank into a workpiece with a specific shape and size under the pressure of a bending brake.
The material, thickness, length and width dimensions of the sheet metal, as well as the different shapes and angles designed, require the use of different press brake tooling for bending. Generally speaking, bending requires the use of press brake upper punch and lower dies with different heights, shapes, and V-width sizes, and even more so, special molds with special shapes are needed. This article introduces the different types of press brake tooling and teach users how to select, use and maintain the press brake upper punch and lower dies.
Press Brake Tooling General Introduction
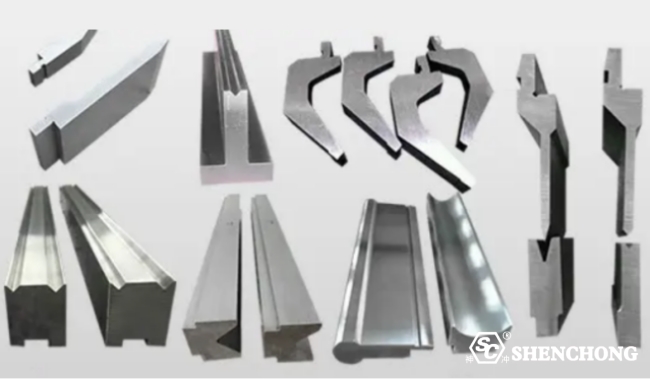
Press Brake Molds Structure
The press brake mold can be divided into two categories in terms of structure: press brake upper punch and press brake lower dies. In bending operations, the vast majority of the upper punch is the active mold and the lower die is the passive mold. If the lower die is fixed and not moved, the upper punch is moved by force. Generally speaking, except for special sets of press brake tooling, a press brake lower die can correspond to multiple upper punches, and operators can choose according to product design needs.
Press Brake Tooling Types
There are various types of press brake machine molds, including V-shaped molds, U-shaped molds, polygonal molds, semi-circular molds, etc. Each type of mold is suitable for specific processing needs and material types. For example, V-shaped and U-shaped molds are commonly used for bending metal sheets, while polygonal and semi-circular molds are suitable for bending specific shapes and angles. The specific shape and size of these molds are selected based on the design and processing requirements of the workpiece.
There are many types of cutting tools for CNC bending machines, generally including standard upper molds for right angle bending, pointed upper molds, flattening knife molds, R-shaped knife molds, offset upper punch, 1V bottom dies, 2V bottom dies, 3U, 4V bottom dies, Yuli rubber press brake bottom dies, hard rubber lower dies, lower mold guide rails, lower die support, segment difference bending molds, forming bending molds, combination bending molds, scratch free bending molds, etc. Various non-standard molds can be designed according to different situations.
In terms of usage, bending brake machine molds are generally divided into standard molds and special molds. Generally speaking, the press brake upper punch tip angle is 30 degrees (actual angle is 26-28 degrees), the lower die notch angle is 30 degrees, 45 degrees, 60 degrees, 80-90 degrees, etc., and 60 degrees, 78-88 degrees, etc.
From the perspective of shape, the upper punch of the bending machine can be divided into sharp blade mold, circular arc mold, bending blade mold, and forming mold. Generally speaking, sharp knife molds are mostly 30 degrees and 60 degrees, occasionally with special specified angles such as 45 degrees and 55 degrees. Arc molds are mainly designed with different arc diameters and lengths. The bending die is mainly used for avoiding U-shaped workpieces or multiple bends. The most complex is the forming die. The forming die can be integrated or combined. Generally speaking, the combination die is designed, manufactured, and combined from the upper and lower molds. From the perspective of production cost, the manufacturing cost of the comprehensive forming die will be much higher (especially for large molds), and the accuracy is difficult to control. The combination die has great advantages in large molds and complex graphic molds.
Press brake tooling can be divided into single mold and multi-function mold according to its function. Single mold can only make a single type of workpiece, while the multi-functional mold can process different types of workpieces. Some can be disassembled and assembled, which is also called composite mold, such as segment difference mold and forming mold.
According to the number of mold notches, the lower die of the press brake machine can be roughly divided into single V bottom die, double V bottom die, and multi V bottom die. As the name suggests, the surface of single V and double V bottom die only has one or two mold notches, which is common in CNC press brake machines and has high accuracy. Because it has a fixed benchmark, also known as a concentric mold, it can be easily replaced. The multi V bottom die is mostly a square mold, with multiple mold notches on the four surfaces and different sizes. The advantage is that the mold has multiple grooves, which can adapt to the bending of various thick plates.
Nowadays, with the continuous progress of society, the requirements for products are also constantly increasing, and the various requirements for bent products and materials are also constantly increasing. The lower mold of bending machines is also constantly developing. Embedded bottom molds, non indentation bottom molds, and adjustable opening bottom molds have been widely used in various industries.
Common Types Of Press Brake Upper Punch And Lower Dies For Sale
1. Ordinary Standard Upper Punch And Lower Dies
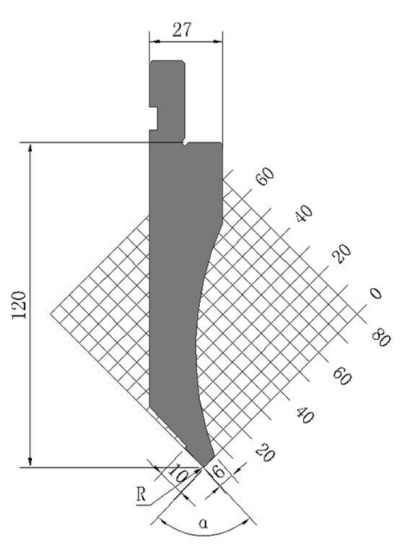
Standard upper punch and lower dies are used for bending at angles of 90 ° -180 °. Advantages: versatile for thick and thin plates, durable, and widely used.
2. Sharp Blade Upper Punch
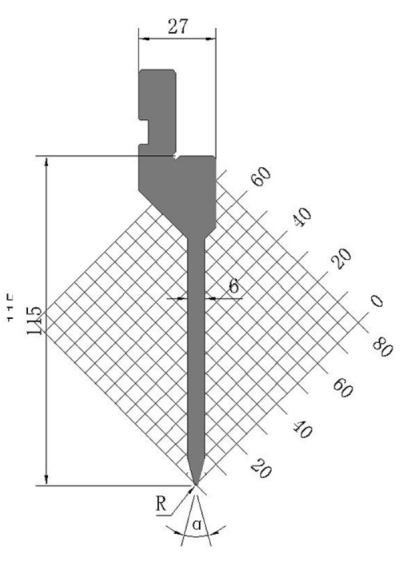
Sharp blade upper punch is used for bending angles of 20 ° – 180 °. Advantages: it can bend smaller angles and sizes, with a smaller R-curve after bending, beautiful appearance, and clear edges.
3. Big Bending Upper Punch (Goose Neck Upper Punch)
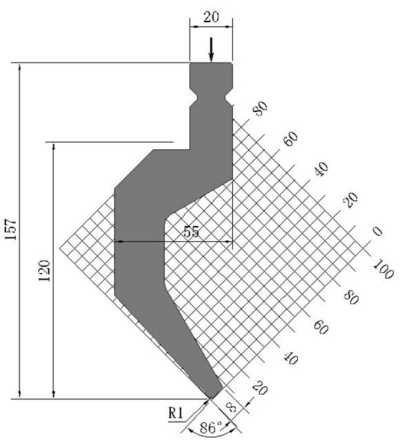
Goose neck press brake upper punch is used for bending angles of 30 ° -180 °. Advantages: used for U-shaped products that cannot be completed by standard and pointed molds, with a wide range of applications.
4. Hemming Press Brake Tooling
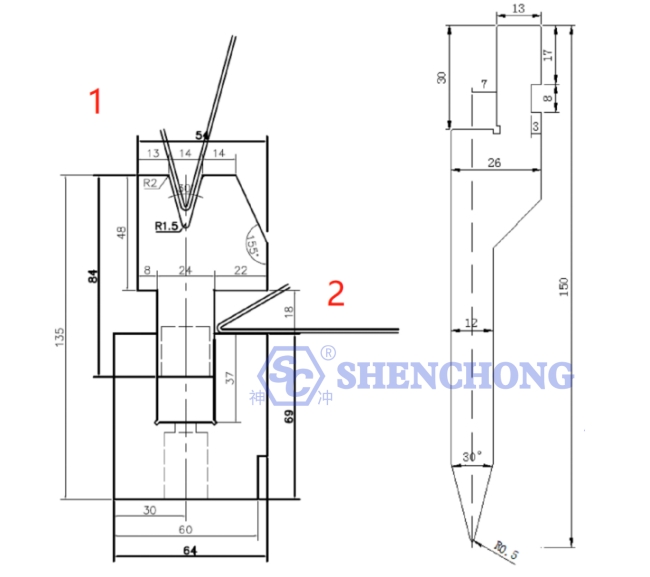
Hemming press brake tooling is used for hemming edges, suitable for matching with pointed dies. First, use the pointed die to bend the workpiece to an angle of less than 45 °, and then use the flattening die to press the dead edge, mainly used for reinforcing the frame.
5. “Z” Press Brake Tooling
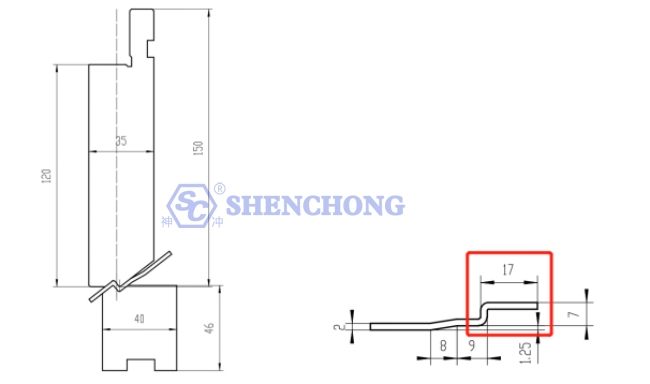
“Z” die is mainly used for one-time bending of small-sized “Z” shaped workpieces, divided into fixed and adjustable types.
6. Press Brake Forming Mold
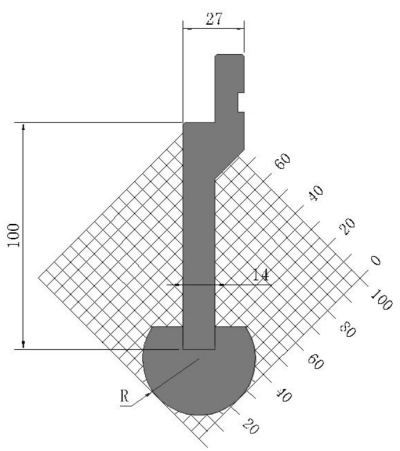
Forming Mold (including arc mold, door frame one-time forming mold, U-shaped forming, lamp pole mold, etc.) is usually used for bending complex products, and includes multiple bending angles and styles. Therefore, a one-time bending forming mold is designed to improve bending accuracy and efficiency.
7. Same Core Lower Die
Same core lower die usually refers to the lower mold used in conjunction with a CNC bending machine, consisting of a mold holder and segmented lower molds. Same core refers to the use of any groove that only needs to be changed to the specified groove, without the need to re center the upper and lower mold positions. The mold change is very convenient and the machining accuracy is high.
8. Non Indentation Lower Die
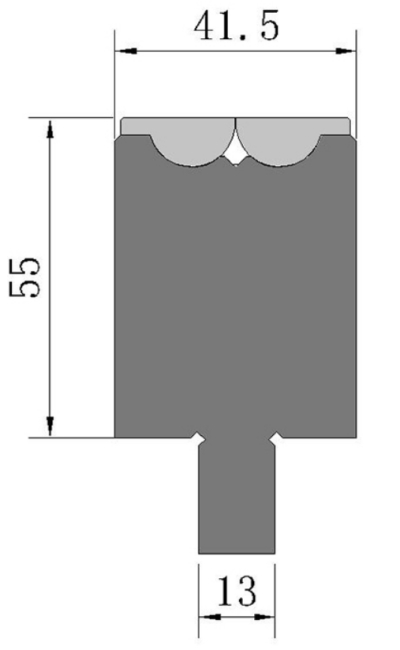
The structure of the rotating flip plate non indentation mold. During the process of pressing the workpiece into the lower die body by the upper punch, due to the contact between the workpiece and the rotating flip plate plane, the rotating flip plate rotates in the lower mold body, and the workpiece does not slide relative to the rotating flip plate during the entire bending process. At the same time, the workpiece is in contact with the rotating flip plate, eliminating the pressure marks and scratches caused by compression on the surface of the workpiece, effectively improving the appearance quality and accuracy of the workpiece. In addition to the two types of non indentation mold structures mentioned above, which can solve the indentation on the surface of the workpiece during bending, the use of anti indentation rubber pads, single V concave mold anti indentation rubber sleeves, block shaped superior glue+AT pad lining, hard rubber concave molds, and other methods can also be used to solve the indentation on the surface of the workpiece during bending, achieving product quality requirements. However, rubber pads, rubber sleeves, superior rubber blocks, and hard rubber are prone to deformation and have a short service life during the bending process, which affects the dimensional accuracy of the bent workpiece. They are only suitable for bending workpieces with low dimensional accuracy requirements.
The non indentation lower die includes a ball type non indentation lower die, a flipping plate non indentation lower die, and a superior adhesive non indentation lower die. The main purpose of a non indentation lower die is to avoid scratches, scratches, and indentations on the material surface.
Press Brake Tooling Material
Generally, press brake tooling is made of T8, T10, T10A, and 42CrMo, which mainly require high strength, toughness, and good wear resistance. Cold work mold steel is selected Cr12MoV is a very good material. Its performance can meet the requirements, and its process performance is also good. The price will be higher. 42CrMo is a high-strength alloy quenched and tempered steel with high strength and good toughness. It can work below 500 degrees
When choosing the material for the press brake machine tooling, factories and users need to consider several characteristics: hardness, heat resistance, and wear resistance. We usually choose T8-T12 carbon steel for press brake tooling, among which T10 is more commonly used, with moderate toughness and good wear resistance. After heat treatment, the highest hardness can reach 60HRC or above, and its production cost is relatively low. However, it has poor hardenability and heat resistance (250 ℃).
If you need better mold materials, choose 42CrMo high-strength alloy structural steel. 42CrMo belongs to ultra-high strength steel, which has high strength and toughness, good quenching properties, and high fatigue limit and resistance to multiple impacts after quenching and tempering treatment. It can work below 500 ℃. The hardness after heat treatment is around 45-48HRC, which is more suitable.
Selection Of Press Brake Tooling
Using different press brake tooling combinations can obtain different mold combination heights for processing different parts. The distance between the tool tips of different mold combinations cannot exceed half of their stroke minus the width of the V notch.
When processing different parts, different molds need to be used. Incorrect mold selection not only makes processing difficult, but also may cause product scrapping. Before selecting a mold, it is necessary to understand the processing parameters of the press brake and mold to avoid situations where they cannot match each other.
Machine tool parameters include: stroke, pressurization capacity, opening height, and type of quick clamp.
Parameters of the press brake tooling: (punch holder type), pressure resistance tonnage (maximum bending pressure).
Selection Of Press Brake Upper Punch
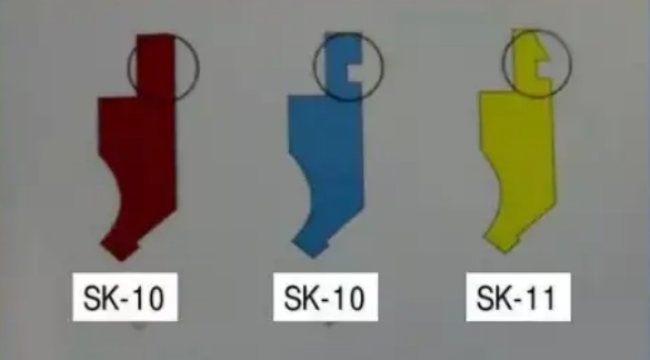
There are three types of the upper punch holder.
- The angle upper punch should be smaller than the machining angle. For example, processing 90 degrees using an 88 degree upper punch.
- Choosing a suitable tip R usually uses R0.6 below 3mm, but if there are special requirements for processing, other R molds such as R0.2 can be used.
- Make sure the pressure resistance range of the upper punch exceed the processing range.
- Different shapes of upper punch are required for different shapes of bending.
Selection Of Press Brake Bottom Dies
- Make sure you choose the correct V width for the lower die.
- The angle between the V notch of the lower mold should be consistent with that of the upper mold, for example, an 88 degree upper mold with a 88 degree lower mold
- Make sure the pressure resistance range of the lower die exceed the processing range
- Lower die includes single V and double V. Among these two types, there are also different types of molds for segmentation and whole segments, which are suitable for different processing needs. Generally speaking, single V molds have a wider range of processing applications than double V molds, and segmented molds have a wider range of applications than whole segment molds. However, the former is relatively expensive.
Selection Of Lower Die Support
Select the lower die base according to the selected lower die, and use different lower die bases for single V and double V lower die.
When selecting the lower die support, it is also important to note that there are several different heights of mold support used to match different processing methods.
Introduction To The Installation Method Of Press Brake Tooling
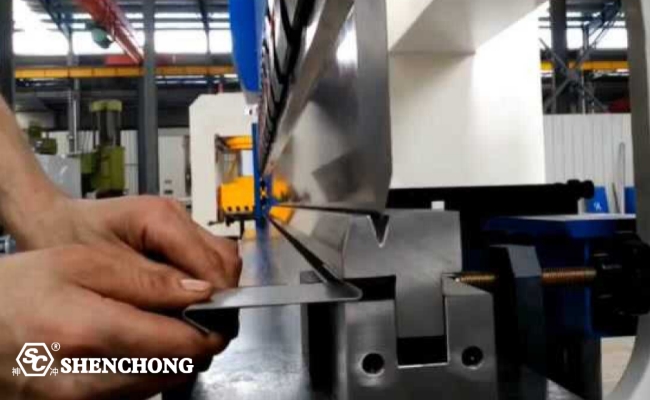
Select Press Brake Mold
Choosing a press brake mold that suits your work needs is a prerequisite for using a bending brake machine. When selecting a bending mold, pay attention to the following points:
- Determine the required pressure range and working material thickness.
- Choose the press brake toolingtype based on the required bending angle and bending radius.
Adjusting The Mold
Before installing the press brake tooling, we need to first to adjust it.
- Adjust the clamping force of the press brake toolingto ensure a good fit with the workpiece.
- Adjust the bending angle and radius of the mold to meet the requirements of the workpiece.
Installing Molds
- First, insert the press brake lower die support onto the working table according to the positioning pin.
- Then install the movable mold in the mold base.
- Finally, install the seat frame of the top mold (the position of the theoretical bending curve) and complete the installation of the mold.
When installing the mold, safety precautions should be taken:
- Before installing the mold, turn off the power and wait for the machine to come to a standstill.
- During installation, attention should be paid to the support force to ensure stable installation.
- Strictly follow the operation manual to prevent emergency situations from occurring.
Using Molds
After the installation of the press brake tooling, a trial bending experiment is required to determine whether the mold and machine are stable and whether the mold meets the requirements of the workpiece.
In summary, the correct installation of the bending machine mold is the key to ensuring the normal operation of the machine. Therefore, when installing the mold, it is necessary to take the adjustment and installation steps seriously to ensure correct installation, operational safety, and production efficiency.
Use Of Press Brake Tooling
There are several types of bending molds, including L-shaped, R-shaped, U-shaped, Z-shaped, etc. The upper mold is mainly used at different angles such as 90 °, 88 °, 45 °, 30 °, 20 °, and 15 °. The lower mold has double and single notch with different notch widths of 4-18V, as well as R lower molds, sharp angle lower molds, and flattening molds. The upper and lower molds are divided into segments and a whole: the upper mold segments are generally 300mm, 200mm, 100mm, 100mm, 50mm, 40mm, 20mm, 15mm, 10mm, and the whole mold is 835mm. The lower mold is generally divided into 400mm, 200mm, 100mm, 50mm, 40mm, 20mm, 15mm, and 10mm, with an overall size of 835mm.
- The press brake toolingis made of high-quality steel through special heat treatment, which has the characteristics of high hardness, low wear resistance, and high pressure resistance. However, each set of mold has its ultimate pressure resistance: tons/meter. Therefore, when using the mold, it is important to correctly choose the length of the mold, that is, how much pressure should be added per meter, and never exceed the pressure indicated on the mold. This is very important, and we hope everyone will remember it.
- In order to avoid damaging the press brake tooling, we have stipulated that when aligning the origin, an upper punch and lower diewith a length of 300mm or more must be used. Only after aligning the origin can the same height of the upper and lower molds be used. It is strictly prohibited to use dividing molds to align the origin, and the origin pressure must be based on the bending machine’s origin pressure. It cannot exceed 7 tons for 80T, 10 tons for 100T, and 15 tons for 200T.
- When usingpress brake molds, due to the varying heights of various molds, only molds of the same height can be used on a single machine, and molds of different heights cannot be used.
- When using molds, appropriate upper and lower molds should be selected based on the bending material hardness, thickness, and length of the metal sheet. When the material is harder and thicker, a wider notchshould be used for the lower die.
- When bending sharp corners or crushing corners, a 30 degree angle should be selected, with the sharp corners first bent and then the edges crushed. When bending the R angle, both the upper and lower molds should be selected.
- When bending longer workpieces, it is best not to use segmented molds to reduce tool indentation.
- When selecting an upper mold, we should understand the parameters of all molds and decide which upper mold to use based on the shape of the product to be formed.
- After the machine has aligned the origin, the upper and lower molds should be locked to prevent them from falling off, causing injury to people or the mold. During the operation, be careful not to apply too much pressure at once, and pay attention to changes in the data displayed on the screen.
- After using the press brake tooling, it should be promptly placed back on the mold rackand placed according to the label. The dust on the mold should be regularly cleaned and coated with rust proof oil to avoid rusting and reduce the accuracy of the mold.
Conclusion
In recent years, China’s manufacturing industry has developed rapidly, which means a huge market for the CNC press machine tooling industry in China. In this context, the low level of manufacturing costs in China is also a recognized fact. According to data, the price difference between press brake tooling in China and developed countries in Europe and America is about 3-5 times. Customers can purchase cheaper press brake upper punch and lower dies from China.