Table of Contents
CNC machining centers are one of the highest production and most widely used CNC machine tools in the world, and so there are thousands of CNC machine manufacturers in the global market. CNC machine’s comprehensive processing ability is strong, and the work-pieces can complete a lot of processing content after being clamped in one go. The processing accuracy is high, and for batch workpieces with medium processing difficulty, its efficiency is 5-10 times higher than that of ordinary equipment. Especially, it can complete many processing tasks that ordinary equipment cannot complete. It is more suitable for single piece processing with complex shapes and high precision requirements, or for small and medium-sized batch multi variety production.
With the rapid development of the manufacturing industry, CNC machining centers have become indispensable and important equipment in modern manufacturing. There are so many CNC machine companies in the market, and clients may feel confused about the CNC machine brands when they never purchase them. In order to help clients better understand the CNC machining center brands in the market, this article will provide you with a detailed introduction to the top 12 CNC machine manufacturers brand ranking list, explore the advantages and disadvantages of each companies, and help you make wiser decisions when purchasing.
Top 12 CNC Machine Manufacturers In Global Market
1.Mazak (Japan)
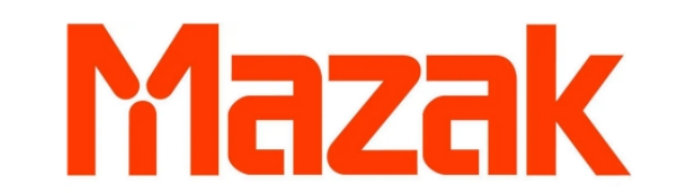
Mazak Company Overview:
If you are interested in manufacturing, you must have heard of the name Mazak. Mazak is a Japanese machine tool manufacturer and one of the largest CNC machine manufacturers in the world. Its products cover various types from lathes, milling machines, machining centers to multi task machine tools.
At present, Yamazaki Mazak Company has a total of 10 production companies worldwide, distributed in Japan, United States, United Kingdom, Singapore, and China. In addition, Yamazaki Mazak has established 30 technology centers in over 60 locations around the world. Along with Mazak technical centers located around the world, Yamazaki Mazak has established over 80 customer support bases around the world.
Mazak's Products
Mazak’s products include lathes, milling machines, machining centers, and multitasking machines, all of which use Mazak’s independently developed CNC systems to achieve high-precision, high-speed, high-efficiency, and high-quality machining. Mazak’s products can be divided into the following series:
- INTEGREX series: This is Mazak’s multitasking machine tool series, which can complete various operations such as turning, milling, drilling, and cutting on a single machine tool, greatly improving production efficiency and saving space. The INTEGREX series machine tools are also equipped with high-performance spindles, tool libraries, rotary tables, etc., which can process various shapes and sizes of parts, suitable for complex part processing in industries such as aviation, automotive, and energy.
- QUICK TURN series: This is Mazak’s lathe series, which can achieve high-speed, high-precision, and high stability turning processing, suitable for processing parts of various materials and specifications. The QUICK TURN series machine tools can also be equipped with a second spindle, tool turret, tool magazine, etc., to achieve synchronous processing of multiple axes and tools, improving production efficiency and quality.
- VARIAXIS series: This is Mazak’s five axis machining center series, which can achieve simultaneous machining in five directions and is suitable for machining various curved surfaces and complex shaped parts. The VARIAXIS series machine tools can also be equipped with high-speed and high-power spindles, tool libraries, rotary tables, etc., to achieve efficient, high-precision, and high-quality processing, suitable for high-end parts processing in industries such as aviation, automotive, and medical.
- Vertical Center series: This is Mazak’s vertical machining center series, which can achieve high speed and precision.
Mazak's Advantages
Mazak’s advantages lie in its innovation ability, technological advantage, brand influence, and market share. Mazak invests a large amount of funds and manpower in research and development every year, committed to improving the performance, intelligence, and environmental friendliness of CNC machine tools. Mazak also collaborates with multiple well-known scientific research institutions and enterprises to jointly develop new technologies and applications. Mazak’s brand enjoys a high reputation worldwide, and its products have also been trusted and recognized by numerous customers. Mazak holds a significant share in the global CNC machine tool market, especially in the high-end CNC machine tool market, with strong competitiveness.
2. DMG MORI (German + Japan)
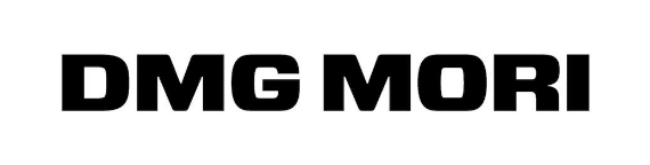
DMG MORI Products
DMGMORI from Germany is a joint venture between German company Demage and Japanese company Mori Seiji. The DMGMORI brand integrates the advantages of MORISEIKI in 65 and DMG in 143. Demajisen Precision Machine Tool has a very high reputation in global market, and is one of the most important CNC machine manufacturers in the high-end manufacturing industry. The vertical, horizontal, three-axis, four axis, five axis, as well as turning milling composite machining centers and ultrasonic/laser machining centers produced by Demajisen Precision Machinery represent the development direction and highest technical level of the domestic and foreign machine tool industry. DMG has become the largest machine tool group in Europe, especially with the integration of German company DMG and Japanese company Mori Seiki. The strong alliance of German manufacturing (DMG 143) and Japanese manufacturing (MORI SEIKI 65) has formed a new global leader in CNC machine tools – DMG MORI
The DMG MORI machine tool has excellent workmanship and an extremely beautiful appearance. The LaserTec65, a composite machining center previously launched by DMG MORI, is a unique composite machine tool that integrates innovative laser cladding technology into a fully functional 5-axis milling machine. It integrates additive manufacturing and cutting (subtractive manufacturing), and can quickly manufacture blanks through the additive manufacturing process of laser cladding, becoming a new highly complex and personalized production method.
It is worth mentioning that in an era where product lifecycles are becoming shorter, components are becoming more complex, and personalized, creative manufacturing processes can achieve the production of complex geometric shapes and complex workpieces. The unique composite technology composed of laser cladding and milling through powder nozzles by Demagisen Precision Machine provides users with new applications and geometric shape possibilities. Through the LASERTEC 65 additive manufacturing process, the forming speed can be up to 20 times faster than in a powder bed!
DMG MORI is one of the largest CNC machining center manufacturers in Europe and a leading innovator in the machine tool industry, constantly developing trendsetting products. DMG MORI brings innovative technologies in multiple fields such as aerospace, automotive, and additive manufacturing, while also showcasing rich digital solutions covering the entire process from task planning and preparation to production and monitoring.
DMG Advantages
The advantages of certain DMG MORI machine tools are highlighted:
Firstly, they have a three-year warranty period, which is not commonly seen in the machine tool industry. The extended warranty period also stems from DMG MORI’s confidence.
Secondly, it allows users to create their own apps based on their own experience, calling them as macro programs, greatly improving production efficiency. Once again, some machine tools have touch screen operation interfaces, which have extremely strong oil resistance and allow users to wear gloves for operation, reflecting the humanization that DMG MORI emphasizes in human-machine cooperation.
DMG MORI once claimed that they have all the production technologies in the aerospace industry. If it weren’t for DMG MORI’s processing of components, DMG’s plane might not have been able to take off. In fact, DMG MORI provides customers with numerous high-tech and high-performance machine tools in the aerospace field, collaborating with customers to develop groundbreaking production processes and complete turnkey solutions. As a comprehensive CNC machine supplier, DMG MORI’s complete machine tool product line meets the machining requirements of the most advanced and complex workpieces in the aerospace industry. For example, many aircraft landing gears, engines, bladed discs, blades, etc. are machined by DMG MORI’s machines, and these components are made of titanium alloy or high-temperature alloy, which have particularly high requirements for machine torque and power.
Of course, DMG MORI is not just about technology, one-step service is the biggest pursuit of DMG MORI. For example, DMG MORI has a sales service center, a team of over 200 service engineers, 100 service vehicles, an 80 person sales service team, as well as an 80 person technical engineer and training team. The large and complete service team configuration allows them to quickly respond to user needs and solve customer problems.
The person in charge of DMG MORI once said: technology integration services, being fully responsible to customers, are the cornerstone of our success. This may be the enduring secret of DMG MORI worldwide.
3. TRUMPF (German)
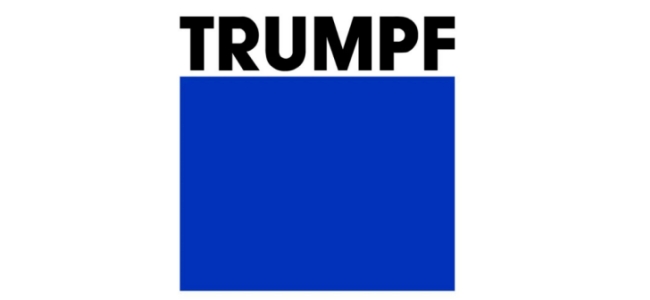
TRUMPF Company Overview
The German TRUMPF Group is one of the leading enterprises in the global manufacturing technology field. TRUMPF Group is also one of the initiators of German Industry 4.0, and is a highly powerful global high-tech enterprise. Since its establishment in 1923, it has a glorious history of over 80 years. The headquarters of TRUMPF Group is located in Ditzingen, near Stuttgart, Germany. It is a global leader in technology and market in the field of industrial lasers, laser systems and CNC machines.
Mr. Christian Trumpf, the founder of TRUMPF Group, opened a flexible shaft company in Stuttgart, Germany in 1923, which became the predecessor of TRUMPF Group. In the 1960s, TRUMPF Group began to venture into the laser field and produced industry-leading lasers in the 1980s. At one point, TRUMPF Group invested 296.2 million euros in research and development, a year-on-year increase of 11.7%, to maintain its technological leadership. TRUMPF Group ranks first globally in the field of laser processing and is also the third largest machine tool manufacturing enterprise in the world.
TRUMPF Products Range
By checking product range of TRUMPFi Group, you can see the processing links of TRUMPF’s laser cutting machines, punching machines, bending machines, and automatic loading and unloading devices, especially the processing efficiency and accuracy, which are very impressive. You have experienced the world’s most advanced machine tool processing technology.
The laser products of TRUMPF Group mainly include high-power carbon dioxide lasers and solid-state lasers, among which solid-state lasers mainly include disc lasers, fiber lasers, diode lasers, pulse lasers, etc.
The machine tool products of TRUMPF Group mainly include: sheet metal laser cutting machines, punching machines, punching laser composite processing, press brake machines, etc. It is worth mentioning that the processing efficiency of TRUMPF Group’s high-end laser cutting machine tools is more than three times that of ordinary machine tools, which can achieve high-speed and high-precision laser processing, punching, bending, marking, etc. Laser sources can be shared among multiple devices and achieve three-dimensional laser cutting and welding. The punching machine tool of TRUMPF Group can complete all the machining processes of workpieces on one machine, so it is capable of handling complex three-dimensional sheet metal processing and also provides supporting automatic loading and unloading equipment.
It is worth mentioning that TRUMPF Group’s laser metal 3D printing technology is also leading in the global industry. The LMF (Laser Metal Melting) system of the TruPrint product series mainly uses a 200 watt laser to irradiate the powder layer, while the construction chamber sinks and pours excess powder into an overflow powder receiver. All of this happens in enclosed spaces with only 0.1% oxygen content to prevent oxidation and potential fires; The LMD (Laser Metal Deposition) technology of the TruPrint product series can create a molten pool on the surface of existing components by laser cladding 3D printing of new metal structures, while melting metal powder and depositing it onto objects. Combining LMD and LMF complementary metal 3D printing technologies, TRUMPF claims that it can meet various metal 3D printing needs of customers.
4. Okuma (Japan)
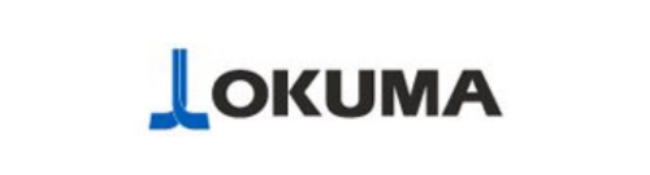
Okuma is one of the largest CNC machine manufacturers in Japan, with a hundred years of experience in machine tool manufacturing. Okuma Corporation is one of the CNC machining center manufacturers in Japan, with a history of over 100 years. It produces various CNC lathes, turning centers, vertical, horizontal, gantry (pentahedral) machining centers, CNC grinders, etc. Its annual output exceeds 7000 units (with a sales revenue of 170 billion yen in 2006, about 1.5 billion US dollars), of which about 50% is for export. Okuma’s products are renowned for their outstanding characteristics: good rigidity, high cutting efficiency, high accuracy, long service life, and easy operation, and have won praise from users around the world.
As early as 1937, Okuma Corporation’s machine tool products (output value) ranked first in Japan. In 1963, a CNC system (OSP) with absolute position detection was independently developed. Becoming the only comprehensive enterprise in Japan that produces machine tools and CNC systems. Production of LA-N CNC lathes and MDB gantry machining centers began in 1966. In 1987, Okuma Machine Tool Company was established in the United States. In 1991, the company name was changed to Okuma Corporation. In 1995, Okuma USA Company was established in the United States.
5. MAKINO (Japan)
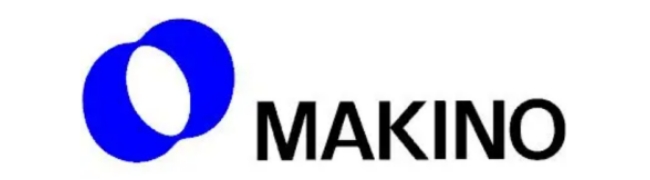
As the world-renowned manufacturer of milling and electrical machining machines, Makino Milling Machine Co., Ltd., has acquired a majority stake in LeBLond Machine Tool Company in the United States. In order to demonstrate Makino’s participation, the company was renamed LeBLond Makino Asia Limited. With the expansion of new business, the company was officially renamed as Makino Asia Limited on June 16, 1992.
Mr. Tsunezo Makino is the founder of the company, founded in 1937, specializing in the production of Type 1 vertical milling machines. Makino developed Japan’s first CNC milling machine in 1958 and successfully developed Japan’s first machining center in 1966. The Makino International R&D Center has invested SGD 75 million to develop and enhance human resources and knowledge capital not only in Makino, but also throughout Singapore. It recruits talents from various industries around the world, becoming a breeding ground for new ideas, technologies, and products, and creating more valuable intellectual property.
In 1996 (Heisei 08), the vertical machining center V55, high-speed underwater wire cutting electric discharge machining machines U32K and U35K, high-speed gloss machining machine EDNCS series, and 3D CAD/CAM UNIGRHICS/EYE molds were successfully developed. The high-speed water cutting electric discharge machining machines U32 and U35 won the 26th Industrial Machinery Design Award.
The horizontal CNC machining center A55 type D won the 31st Machinery Revitalization Association Award.
The micrometer FF machining machine HYPER5 won the 16th Precision Industry Society Technology Award.
In 1999, V33/SG2.3 was successfully developed and became the new standard for high-speed machining.
In 2001, the Hyper 2 ultra-fine electrical machining machine was launched into the market. Successfully developed 5-axis linear guide rail aviation high-speed machining center MAG4.
In 2003, the world’s first 0.02mm automatic threading ultra precision wire cutting machine was successfully developed.
Why Choose MAKINO
In the manufacturing industry, quality cannot be falsified. All parts, products, and processes will demonstrate their true quality in the short term. Makino equipment has unparalleled operating hours, higher quality, and lower scrap rates, thereby minimizing ownership costs and achieving excellent performance. Employees in Makino are all true craftsmen in the industry, using their unique professional skills to deliver high-quality products to users. MAKINO’s pre shipment quality inspection requirements often far exceed the highest standards set internally.
In an industry known for its small incremental changes, Makino has introduced disruptive technological innovations that have revolutionized the industry and established a competitive advantage for users. Since its establishment, Makino has always been proud of its innovative tradition. Now, Makino is pushing this tradition to a new height. Makino’s innovative solutions and system improvements bring more connectivity, foresight, reliability, and precision to devices, ensuring users have more confidence in controlling the future.
6. AMADA (Japan)
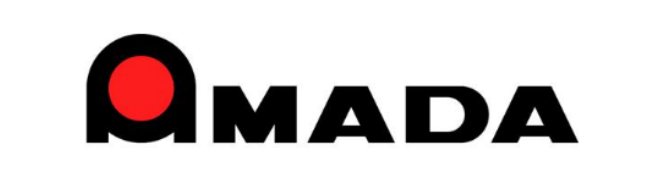
AMADA Company Overview
AMADA CO., LTD is a large multinational company specializing in the production of sheet metal processing machinery. From the aspects of market size, product structure, product technical performance, and comprehensive business management system, AMADA has gradually formed a group listed company that integrates product development, design, manufacturing, education and training after-sales service, and has a marketing network.
The company has 83 branches on various continents around the world, and its products are marketed in over 100 countries and regions worldwide. It produces a wide variety of sheet metal processing machinery (nearly a thousand varieties) with excellent performance and advanced technology, making it the industry leader in the world’s sheet metal processing machinery. The 21st century intelligent automatic sheet metal processing center developed and manufactured by the company in the 1990s has set a precedent for intelligent processing in the global sheet metal industry and received the highest technological invention award in Japan.
AMADA Products Range
The main products include CNC punching machines, press brake machines, shearing machines, laser cutting machines and other sheet metal processing machinery, as well as corresponding molds, spare parts, and cutting products.
AMADA releases new products every year. In 2009, the proportion of new products in product sales was 22%, increased to 29% in 2010, and the plan for 2011 was 38%. In the past two years, Tiantian has introduced and applied new management methods and technologies, which have greatly shortened the research and development cycle of new products, from the previous two to three years to about one and a half years.
AMADA defined the competition of future sheet metal machinery as fiber laser cutting machines and released the latest developed fiber laser cutting machine FOL-3015FiberAJ at the EuroBlech exhibition in Germany in October 2010.
7. Doosan (South Korea)
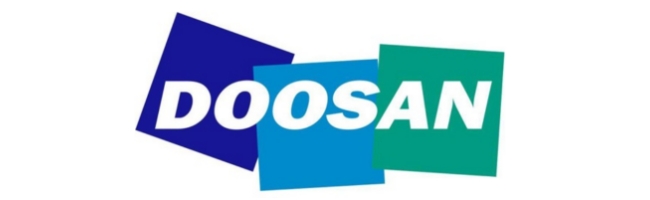
Doosan Overview
Doosan Machine Tool established its production base in Changwon, South Korea in 1976. In 1979, the total production of machine tools exceeded 1000 units.
Since opening up the overseas market in South Korea in 1981, on January 1, 2007, the Doushan Engineering Machinery Division and Doushan Machine Tool Division, which were divided into two companies, were merged, thereby enhancing the competitiveness of the machine tool industry and laying a solid foundation for developing into a global leading enterprise. Doushan machine tools are exported to markets in countries such as the UK and Italy, with a global market share ranking 15th.
Doosan Products Range:
- Efficient CNC lathe
Compact and efficient CNC machine tools equipped with linear guides greatly reduce non cutting time, minimize footprint, maximize production efficiency, and increase spindle output torque. This series includes Lynx225, Lynx225G, Lynx235, and Lynx235D, respectively.
- High performance CNC lathe
Small and efficient CNC lathes can be used for intermittent machining under heavy loads, with long-term accuracy retention and optimal surface smoothness. The high-speed turret and fast axial movement speed reduce non cutting time, making the machine truly cost-effective. This series includes PUMA205, PUMA215, PUMA245, PUMA305, and PUMA405 respectively.
- High performance vertical CNC lathe
High efficiency vertical CNC lathe, with a special vertical structure that makes machining accuracy higher, component loading and unloading more convenient, and high spindle torque output. This series includes PUMAV405 and PUMAV835.
- CNC lathe for aluminum wheel hub machining
Aluminum wheel hub machining CNC lathe, specially designed for aluminum wheel hub machining, with high rigidity guide rail and high spindle torque output. This series includes PUMAAW505BIKE, PUMAAW560, and PUMAAW660
- Tapping machining center
The high-speed CNC tapping machining center, high-speed rail and high-speed servo motor ensure high-speed axial speed, shorten non machining time, high efficiency, high precision, and high economy. This series has DT400.
- High efficiency vertical machining center
High efficiency vertical machining center, high-speed linear guide rail and high-speed servo motor ensure high-speed axial speed, high efficiency, high economy, shorten non machining time, and wide applicability. This series includes CNM560, DNM415, and DNM515.
- High production capacity vertical machining center
High production capacity vertical machining center, high rigidity guide rail, high-performance and high-precision standard new model, with long-term precision maintenance and ultra precision surface processing performance, high durability can create extraordinary value. This series includes CMV920, Mynx545, Mynx545/50, Mynx650, and Mynx650/50.
- High speed heavy-duty vertical machining center
High speed heavy-duty vertical machining center, designed for high-speed and high load machining, with a powerful, heavy-duty structure and high rigidity guarantee. This series has V435.
- Economical horizontal machining center
Economical horizontal machining center, which integrates high-speed, high-precision, and high reliability, has a high reliability and spacious working area. The workpiece adjustment is simple, and the double tray exchange structure greatly reduces the workpiece loading time and improves work efficiency. This series has HC505.
- High rigidity heavy cutting horizontal machining center
High rigidity heavy cutting horizontal machining center, heavy-duty, high rigidity guide rail, strong cutting, strong spindle drive mode, stable position accuracy and repeated positioning accuracy. This series includes HM635 and HM805.
8. DMTG (China)
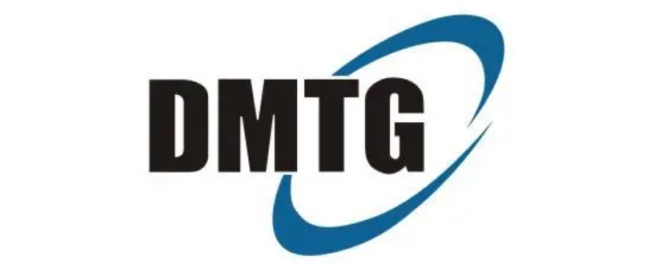
Dalian Machine Tool Factory (DMTG), established in 1935, is one of the backbone enterprises in the new China machine tool industry. DMTG is also one of the most famous CNC machine manufacturers in China market. In 2000, Dalian Modular Machine Tool Research Institute directly under the former Ministry of Machinery of China entered the group as a whole. Since 2002, DMTG have continuously acquired three old foreign machine tool companies, including Ingersoll Production Systems from the United States, crankshaft company, and Zimmerman from Germany. DMTG have also established eight foreign joint ventures with countries such as the United States, Germany, Japan, Switzerland, and South Korea.
At present, DMTG has built two modern industrial bases covering an area of 1.1 million square meters, integrating the research and development and manufacturing of CNC machine tools, flexible manufacturing systems, and automation complete technology and equipment, as well as the industrialization of functional components. The existing equipment includes nearly 2500 units of “close, large, fine, and thin” equipment, with more than 80 valid patents. DMTG provide high-quality product services and comprehensive solutions to over 100 countries and regions worldwide in industries such as automobiles, rail transit, engineering machinery, petroleum machinery, mining metallurgy, communication equipment, and vocational education.
DMTG Product Range
The products include: ordinary lathes, CNC lathes, CNC milling machines, machining centers, gantry machining centers, turning centers, and original machine tool accessories. Machine tool accessories include chucks, center frames, tool holders, hydraulic components, cutting edge measuring tools, and other mechanical products. DMTG also undertake major and medium repairs and technical renovations of machine tools, as well as domestic and foreign drawing processing services and technical consulting. Currently, DMTG focuses on intelligent manufacturing units and intelligent production lines, machining center product series, lathe product series, key functional components manufacturing.
9. EMAG (German)
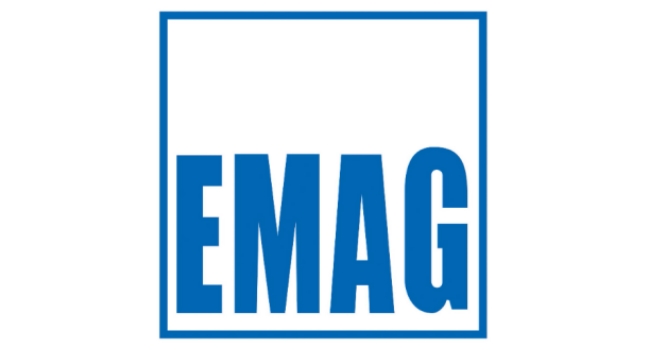
The headquarters of Emark Group is located in Salah, near Stuttgart, Germany, and is a typical “hidden champion” of the German machine tool industry. The company was established in 1867 and has extensive experience in machine tool manufacturing. Emark Group’s business is mainly distributed in industries such as automotive manufacturing and supporting industries, mechanical manufacturing and aerospace, renewable energy, electricity, and oil. Emark is a pivotal manufacturer of CNC inverted machine tools in the world.
The origin of Emark can be traced back to 1867. Originally, it was a cast iron and machine tool manufacturing factory established in the city of Baocen, Saxony. In 1952, the company was rebuilt and located between Stuttgart and Ulm, not far from the current location of the company in Salah. After the company was rebuilt, it began manufacturing lathes. The first inverted lathe was born in Emark in 1992. Unlike ordinary horizontal lathes, the inverted lathe uses the spindle to grab the workpiece, revolutionizing the traditional concept of automation. Compared with traditional gantry truss manipulators or robots, this loading and unloading method has the advantage of low cost, reliable performance, and is particularly suitable for high-precision large-scale production. Once launched, it has been favored by global customers represented by automotive parts.
In the 1980s, Emark achieved remarkable results in manufacturing highly automated CNC lathe units. In 1992, Emark launched an inverted lathe as a world machine tool factory. The characteristic of this lathe is that the spindle completes loading and unloading, and the spindle moves while the tool holder is fixed. That is to say, Emark overturned traditional lathes.
After 30 years of development, Emark has evolved from a simple lathe to a composite machine tool capable of various processes such as turning, drilling, boring, milling, grinding, gear hobbing, and laser processing. Its advantages are automatic loading and unloading of workpieces, short processing and rhythm time, high workpiece processing quality, short process chain, reliable process, and low single piece processing cost. With the continuous improvement of production hardware and technical requirements in series mass production, both assembly manufacturers and component suppliers deeply feel that multifunctional integrated production and processing centers are a new development trend. At present, Emark Group’s products can cover the processing of two-thirds of circular and non circular parts in automotive components.
Emark Group has become a global market leader in the field of inverted automatic loading and unloading turning machines, leading the industry trend. In addition to its three production bases in Germany, Emark also has 29 brand subsidiaries worldwide. The export share accounts for almost 69% of the company’s total revenue.
10. MAG (United States)
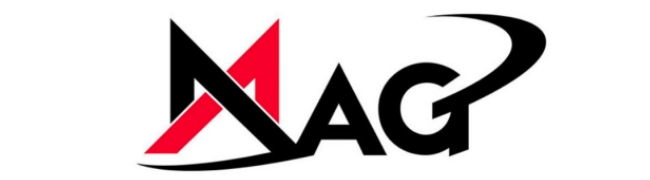
MAG Corporation is a multinational machine tool manufacturing company headquartered in Michigan, United States. MAG Company is a group company composed of numerous world-class machine tool manufacturing companies and control system companies. MAG Group’s machine tool production value once reached 1.5 billion US dollars, ranking 6th in the world. As a machine tool and automation system company, MAG can provide users with tailored machining solutions, mainly serving the durable goods industry.
MAG has numerous well-known brands under its umbrella, including Berliner Ger, Cincinnati, Klaus Welle, Axelo, Fado, Giddens Lewis, Heyseep, Huntsberg, Welle Joy, and Witchley Frank. As the leading CNC machine company, MAG is renowned as an outstanding supplier for its perfect craftsmanship and tailored production solutions based on this foundation. Widely serving industries such as aerospace, automotive, heavy machinery, oil fields, rail transit, solar energy, wind turbine production, and general processing.
11. SMTCL (China)
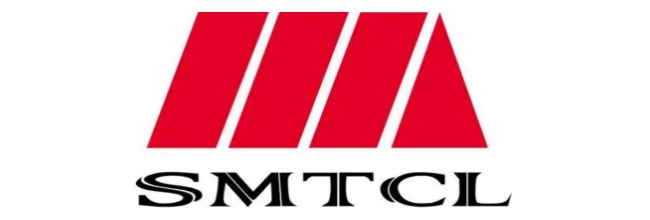
Shenyang Machine Tool (Group) Co., Ltd. was established in December 1995 through asset restructuring of the original three major machine tool factories in Shenyang: Shenyang First Machine Tool Factory, Shenyang Second Machine Tool Factory (Zhongjie Friendship Factory), and Liaoning Precision Instrument Factory.
In 2004, the production and sales of machine tools exceeded 50000 units, among which the production and sales of CNC machine tools exceeded 6000 units. For many years, as the most famous CNC machine supplier, the production and sales of SMTCL machine tools have consistently ranked first in the same industry in China.
The company’s leading products are metal cutting machine tools, including two categories: one is CNC machine tools, including CNC lathes, CNC milling and boring machines, vertical machining centers, horizontal machining centers, CNC drilling machines, high-speed profile milling machines, laser cutting machines, quality centering machines, various CNC special machine tools and CNC tool holders, etc. Another type is ordinary machine tools, including ordinary lathes, radial drilling machines, horizontal boring machines, multi axis automatic lathes, various ordinary special machines and accessories. There are over 300 varieties and over a thousand specifications in total. The market covers the whole country and exports to more than 80 countries and regions.
12. GROB (German)
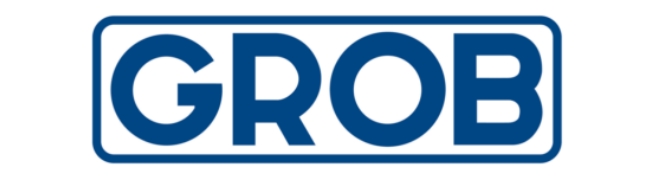
The German company GROB was founded in 1926 and is headquartered in Mindheim, Germany. GROB is an enterprise that produces a wide range of machine tools, from standard machine tools to complex production systems or assembly units on cutting lines, to fully automated assembly lines. GROB’s processes and technology are always at a high level. GROB specializes in turnkey engineering of engine components and is a global system integration supplier that covers different processes, technologies, resources, and cultures.
GROB’s products cover everything from universal machining centers to highly flexible and automated production systems, from assembly units in mechanical processing to fully automated assembly lines. In addition, motor production equipment, assembly equipment for battery and fuel cell technology are also included in the product scope. GROB also has thermal spraying technology suitable for engine components, and can provide customized solutions for processing turbine casings, frame structure workpieces, chassis workpieces, and battery casings. Under the Industry 4.0 framework, GROB has taken an important step by launching the GROB-NET4 industry software for comprehensive future oriented digital and networked production. In addition, GROB has successfully entered the field of additive manufacturing and developed a brand new liquid metal printing equipment.
Rating Criteria For CNC Machining Centers
How did we select the top 12 CNC machining center manufacturers? What are our selection criteria? We select the CNC machine manufacturers based on the machine quality and company market share.
1. Machine Tool Accuracy
The accuracy of machining centers is an important indicator for evaluating the quality of machine tools, including position accuracy, repeated positioning accuracy, angle accuracy, etc. Among them, position accuracy is the minimum movement that the machine tool can achieve, repeated positioning accuracy is the positioning accuracy of the machine tool when processing the same position multiple times, and angle accuracy is the angle error of the machine tool when tilting.
2. Machine Tool Reliability
The reliability of a machining center refers to whether the machine tool can operate stably during long-term use, without production stagnation caused by mechanical failures or human errors. The evaluation of machine tool reliability needs to consider factors such as the structural design, processing technology, and component quality of the machine tool.
3. Market Share
Market share is a very critical index. Large market share means the factory sell hundreds and thousands of machines and have the stable quality and rich after-sales experience. Market share is one of the most important rating criteria when we select the top CNC machine manufacturers. Above top 12 CNC machining center companies have excellent machine quality (not the best), but they all have large share share.
CNC Machine Manufacturers Quality Level Echelon
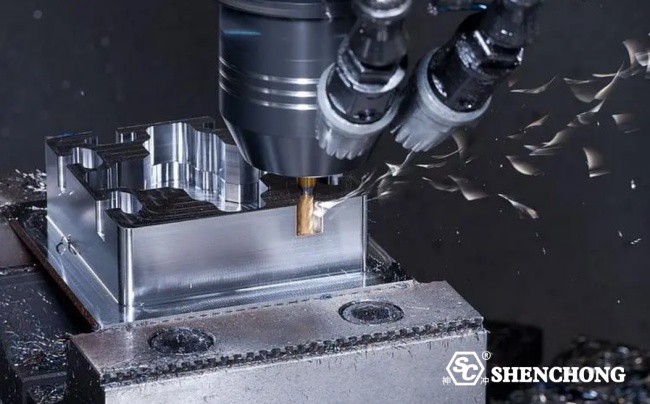
Divide typical CNC machining center manufacturers in the global market into 5 levels, and make a correct analysis of the positions occupied by each machine tool manufacturer through a hierarchical ranking.
Tier 1- Super First Class CNC Machine Manufacturers
In the first tier, brands such as Swiss Mikron, Swiss BUMOTEC, Swiss STARRAG, German HERMLE, German ALZMETALL, and German CHIRON are among the top players in the field of machining centers, priced at over 210 thousand USD dollars.
Whether in terms of appearance, design level and innovation, or processing ability and precision, it is almost impeccable. Exquisite craftsmanship, striving for excellence, machine tool processing accuracy is extremely high, and production output is very low. Due to the high price and cost of use, users often have to make purchases in a last resort.
The brand image of the processing center in the first tier is high, and the high cost of procurement and use directly leads to a very low market application rate. Although the price is high, the profit may not be high, and although the quality is good, the operation may not be good.
The quality of machine tools is ensured by factors such as the quality of bed materials, machining level, component quality, assembly quality, and production control. The assembly quality of machine tools is always guaranteed by manual labor. The level of assembly technicians varies, and there are strict delivery time restrictions for mass production of machine tools. Therefore, it is difficult to ensure a high level of quality for machine tools produced in large quantities. This is also why the top ten machine tool manufacturers in the world in terms of sales cannot enter the first tier.
Tier 2 CNC Machining Center Suppliers
The names of several companies in the second tier, including German DMG, Japanese Mori Seiji, Japanese Mazak, Japanese Makino, American MAG, are almost familiar and well-known. They are the main machine tools of world-class machinery production enterprises, with prices ranging from 110-210 thousand USD.
These contestants consistently rank among the top in the world’s machine tool sales rankings. Commonly produced in small and medium-sized batches, with proper control and good quality, only used for producing high profit products. The price is relatively lower than that of the first tier.
The second tier manufacturers have strong promotion efforts, high market share, and specialize in solving difficult mechanical processing problems, with brand awareness exceeding that of the first tier.
The first and second tier teams are significantly ahead in product quality and technological innovation. At present, advanced technologies such as natural or artificial marble bed technology, bed temperature control technology, linear motor drive, ball screw center cooling, center of gravity drive, ultra fast tool changing mechanism, high-speed electric spindle, etc. have all been applied in the first and second tier products.
The first and second tier teams are almost dominated by the Swiss, Germans, and Japanese companies. Their rigor and the consistent tradition of valuing skill training in these three countries are the foundation for their ability to manufacture excellent machine tools.
Tier 3 CNC Machining Center Manufacturers
Doosan from South Korea, Hyundai from South Korea, Samsung from South Korea, Yongjin from Taiwan, and Taichung Precision Machinery from Taiwan, DMTG are the main machine tool brands among first tier machinery production enterprises. The selling price ranges from 65-110 thousand USD.
Although enterprises processing first-class products also use machine tools from the first and second tier, due to high procurement costs, they still mainly use machine tools from the third tier in large quantities. These machine tools are sturdy, durable, reliable, and stable, making them a good helper in ensuring product quality and production efficiency.
Tier 4 CNC Machine Manufacturers
This echelon of enterprises consists of excellent domestic enterprises and some mainland factories of Taiwanese enterprises. The price is around 45-65 thousand USD.
The market share of machine tools in the fourth tier is no less than that in the third tier. Although it is slightly inferior in stability and accuracy retention compared to the third tier, the price is more affordable, and it has also become the main model in high-level mechanical processing enterprises.
Tier 5 CNC Machining Center Suppliers
Most of the CNC machining centers in this echelon come from factories in China, with the largest market sales and the best acceptance by ordinary mechanical users. There are as many as one or two hundred factories in this echelon, and the competition has reached a white hot point.
The products of this tier are severely homogenized, and the entry threshold is relatively low. If the factory scale is comparable and the management is reasonable, the difference in quality between different brands is very small. Choosing this echelon of machine tools requires users to have strong application capabilities, and they can flexibly choose the most suitable machine tool components and accessories according to their actual needs. Using the right and good machine tools can produce impressive products.
Conclusion
CNC machining centers are the most widely used machine tools in CNC machining, and there are many manufacturers worldwide. Among them, machine tools represented by Switzerland, Germany, and Japan occupy the vast majority of the mid to high end market. This article summarizes the top 12 leading CNC machining center brands worldwide. These CNC machine manufacturers represent industry leading levels in terms of processing capability, design level, and innovation.