สารบัญ
ในระหว่างกระบวนการผลิตและการผลิต อาจเกิดปัญหาคุณภาพการดัดต่างๆ ขึ้นเมื่อดัดชิ้นส่วนโลหะแผ่น ซึ่งอาจส่งผลต่อการปรับปรุงประสิทธิภาพการผลิตและความเสถียรของคุณภาพผลิตภัณฑ์ บทความนี้จะอธิบายปัญหาคุณภาพการดัดและการตัดทั่วไปในกระบวนการผลิต วิเคราะห์สาเหตุของปัญหา และเสนอแนวทางแก้ไขเพื่อให้มีประสบการณ์และใช้เป็นข้อมูลอ้างอิงสำหรับปัญหาที่คล้ายคลึงกันในกระบวนการผลิตครั้งต่อไป
การแนะนำ
การดัดแผ่นโลหะเป็นกระบวนการใช้แม่พิมพ์สากล (หรือแม่พิมพ์เฉพาะทาง) ที่มีอุปกรณ์ เครื่องกดเบรก CNC การดัดแผ่นโลหะให้เป็นรูปทรงหน้าตัดทางเรขาคณิตต่างๆ ของชิ้นงานตามต้องการ ความสมเหตุสมผลของกระบวนการดัดส่งผลโดยตรงต่อขนาดและรูปลักษณ์ของผลิตภัณฑ์ที่ขึ้นรูปขั้นสุดท้าย การเลือกแม่พิมพ์ดัดที่เหมาะสมมีความสำคัญอย่างยิ่งต่อการขึ้นรูปผลิตภัณฑ์ขั้นสุดท้าย
ในกระบวนการผลิตจริง เนื่องจากความไม่แน่นอนของขนาดผลิตภัณฑ์และความหลากหลายของประเภทผลิตภัณฑ์ เรามักพบปัญหา เช่น การรบกวนของขนาดและมุมแม่พิมพ์ที่ไม่ตรงกันระหว่างการดัดชิ้นงานที่ผ่านการแปรรูปแบบเย็น ซึ่งนำมาซึ่งความยากลำบากอย่างมากในการผลิต เนื่องจากอิทธิพลของปัจจัยต่างๆ เช่น ขนาดของผลิตภัณฑ์ รูปร่าง วัสดุ แม่พิมพ์ อุปกรณ์ และสิ่งอำนวยความสะดวกเสริมในระหว่างกระบวนการดัด อาจเกิดปัญหาคุณภาพต่างๆ ขึ้นได้ ซึ่งส่งผลกระทบต่อประสิทธิภาพการผลิตและความเสถียรของคุณภาพผลิตภัณฑ์ ดังนั้น จึงมีความสำคัญอย่างยิ่งที่จะต้องจัดการและหลีกเลี่ยงการเกิดปัญหาคุณภาพการดัดเหล่านี้ บทความนี้สรุปและอธิบายปัญหาคุณภาพทั่วไปของการดัดแผ่นโลหะในกระบวนการผลิตเป็นหลัก วิเคราะห์สาเหตุโดยอิงจากประสบการณ์การผลิต และเสนอแนวทางแก้ไข
ปัญหาคุณภาพการดัดทั่วไป
การดัดและการแตกร้าว
รอยแตกร้าวจากการดัดหมายถึงปรากฏการณ์ที่มักมีเสี้ยนหรือรอยแตกร้าวเล็กๆ เกิดขึ้นที่ขอบของวัสดุหลังจากการตัด การเฉือน หรือการปั๊ม และเกิดการรวมตัวของความเค้นได้ง่ายในระหว่างการดัด ส่งผลให้เกิดรอยแตกร้าว ร่องเสริมแรงรูปตัว U ของชิ้นส่วนหัวรถจักรมีรอยแตกร้าวที่มุมหลังจากการดัด ดังที่แสดงในรูปที่ 1
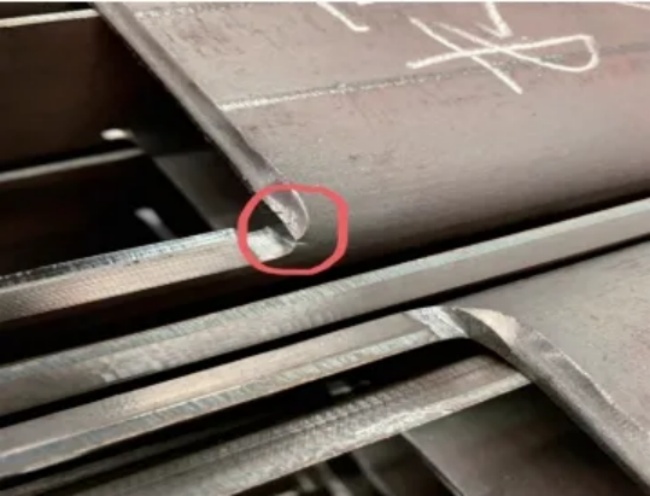
รูปที่ 1 การดัดและการแตกร้าว
สาเหตุหลักของการงอและแตกร้าว ได้แก่:
- มีเสี้ยนที่ไม่สะอาดอยู่ที่ขอบชิ้นส่วน
- ทิศทางการดัดจะขนานกับทิศทางการรีดแผ่นโลหะ
- รัศมีการดัดของแผ่นโลหะน้อยเกินไป
ในระหว่างกระบวนการผลิต จำเป็นต้องจัดการกับปรากฏการณ์การดัดและแตกร้าวตามสถานการณ์เฉพาะ สำหรับปัญหาการดัดและแตกร้าวในรูปที่ 1 สามารถใช้แนวทางการเพิ่มรูหรือร่องในกระบวนการเพื่อแก้ปัญหาได้ ดังที่แสดงในรูปที่ 2
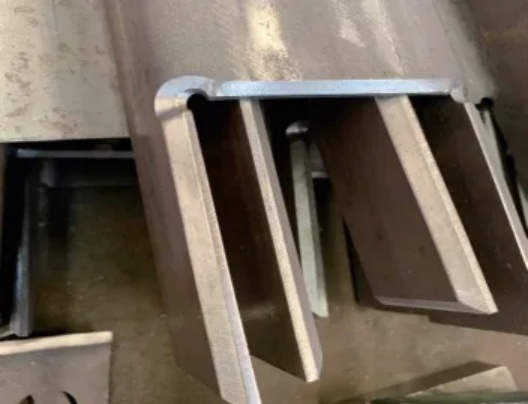
รูปที่ 2: การเพิ่มรูกระบวนการ
การรบกวนการดัดงอ
การรบกวนจากการดัดนั้นมุ่งเป้าไปที่ผลิตภัณฑ์ที่มีการดัดแบบรองหรือสูงกว่าเป็นหลัก โดยที่ขอบดัดจะชนกับแม่พิมพ์หรืออุปกรณ์ ส่งผลให้ไม่สามารถขึ้นรูปได้อย่างถูกต้อง การรบกวนจากการดัดนั้นส่วนใหญ่ได้รับอิทธิพลจากรูปร่าง ขนาด และแม่พิมพ์ของชิ้นส่วน และส่วนใหญ่เกิดจากโครงสร้างการออกแบบของชิ้นส่วนที่ดัดเอง ลำดับการดัดที่เลือก และแม่พิมพ์ดัดที่เลือก ดังนั้น วิธีแก้ปัญหาหลักๆ มีดังนี้
- การสร้างแม่พิมพ์ใหม่หรือการเปลี่ยนแม่พิมพ์ (เช่น แม่พิมพ์มีดดัด)
- แปรรูปแม่พิมพ์ดัด (เช่น การประมวลผลทางกลของชิ้นส่วนในท้องถิ่น)
- ปรับลำดับการดัด (เช่น วิธีการเปลี่ยนรูปย้อนกลับ)
- เปลี่ยนขนาดการดัดของชิ้นส่วน เช่น ตัวยึดสำหรับรางเสริมแชสซีของรถไฟฟ้าใต้ดินเซี่ยงไฮ้สาย 18 ทำด้วยเหล็กช่องรูปตัว U มีความกว้างปานกลาง 100 มม. ความสูงขอบ 80 มม. และรัศมีการดัด 15 มม. จำลองการดัดโดยอิงจากแม่พิมพ์ที่มีอยู่ในเวิร์กช็อปเพื่อสร้างการรบกวนจากการดัด
เพื่อตอบสนองต่อปรากฏการณ์การรบกวนนี้ จึงได้นำวิธีการประมวลผลทางกลในพื้นที่มาใช้กับแม่พิมพ์ดัดด้านบน (ดูรูปที่ 3) รอยบากขนาด 140 มม. × 48 มม. ถูกตัดตามแนวเส้นกึ่งกลางของแม่พิมพ์ดัดด้านบนมีดตรง R15 มม. ที่มีอยู่ (ยาว = 800 มม.) (ดูรูปที่ 4) ตำแหน่งของรอยบากถูกกำหนดโดยการรวมกับตำแหน่งการรบกวนการดัดที่จำลองขึ้น โดยไม่ส่งผลกระทบต่อการทำงานเดิมของแม่พิมพ์ หลังจากปรับเปลี่ยนแม่พิมพ์ดัดแล้ว ปัญหาของการรบกวนการดัดก็ได้รับการแก้ไขสำเร็จ
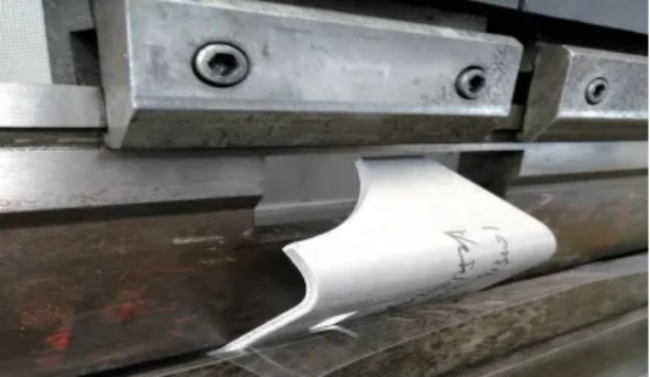
รูปที่ 3: การดัดหลังการประมวลผลแม่พิมพ์ด้านบน
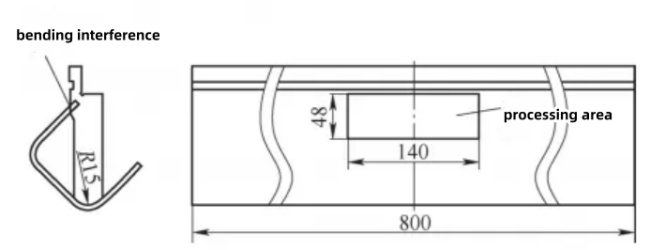
รูปที่ 4: การรบกวนจากการดัดงอ การกำหนดพื้นที่การประมวลผล
การดัดรอยบุ๋ม
รอยบุ๋มจากการดัดเป็นปรากฏการณ์ที่แรงเสียดทานเกิดขึ้นระหว่างกระบวนการนำแผ่นโลหะมาสัมผัสกับพื้นผิวด้านในของร่องรูปตัววีของแม่พิมพ์เว้าทีละน้อย ส่งผลให้เกิดรอยบุ๋มที่เห็นได้ชัดบนพื้นผิวแผ่นโลหะ สำหรับอุปกรณ์เสริมบางอย่างที่มีข้อกำหนดด้านพื้นผิวสูง การดัดแบบดั้งเดิมไม่สามารถตอบสนองความต้องการด้านคุณภาพของผลิตภัณฑ์ได้ และรอยบุ๋มจากการดัด (ดูรูปที่ 5) ไม่สามารถตอบสนองความต้องการของกระบวนการถัดไปได้
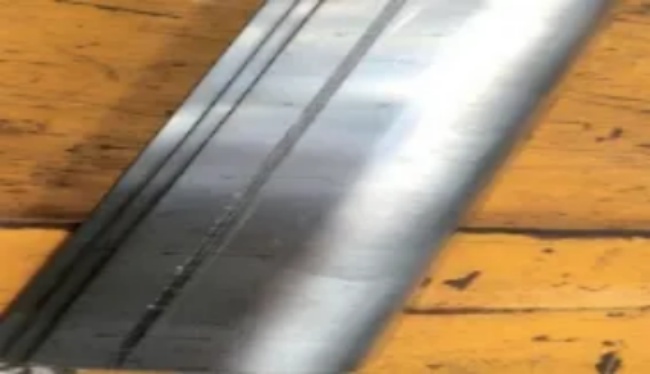
รูปที่ 5: การบุ๋มแบบดัด
รอยบุ๋มจากการดัดนั้นส่วนใหญ่ได้รับผลกระทบจากความแข็งของแผ่นโลหะและโครงสร้างของแม่พิมพ์ด้านล่าง ยิ่งแผ่นมีความแข็งมากเท่าไร ความสามารถในการต้านทานการเสียรูปถาวรก็จะยิ่งมากขึ้นเท่านั้น ทำให้วัสดุเกิดการเสียรูปถาวรได้ยากขึ้นและเกิดรอยบุ๋มได้ง่ายขึ้น โอกาสที่รอยบุ๋มจากการดัดจะเกิดในวัสดุแผ่นที่ใช้กันทั่วไปคือ: อลูมิเนียม > เหล็กกล้าคาร์บอน > เหล็กกล้าไร้สนิม ยิ่งความกว้างของช่องเปิดของแม่พิมพ์ดัดมากเท่าไร ความกว้างของรอยบุ๋มจากการดัดก็จะมากขึ้นเท่านั้น และความลึกของรอยบุ๋มก็จะยิ่งตื้นขึ้นเท่านั้น ยิ่งขนาด R ของไหล่ช่องเปิดแม่พิมพ์ด้านล่างมีขนาดใหญ่ขึ้น ความลึกของรอยบุ๋มก็จะยิ่งตื้นขึ้นเท่านั้น
นอกจากการปรับปรุงความแข็งของวัสดุและโครงสร้างแม่พิมพ์ส่วนล่างแล้ว แผ่นยางป้องกันการบุ๋มและแม่พิมพ์ส่วนล่างดัดแบบลูกบอลยังสามารถใช้เพื่อแก้ปัญหาการบุ๋มจากการดัดได้อีกด้วย แผ่นยางป้องกันการบุ๋มนั้นส่วนใหญ่อาศัยการแยกทางกายภาพเพื่อลดการเกิดการบุ๋ม ดังที่แสดงในรูปที่ 6 แม่พิมพ์ดัดแบบลูกบอลจะเปลี่ยนแรงเสียดทานจากการอัดขึ้นรูปที่จำเป็นสำหรับแม่พิมพ์ดัดแบบดั้งเดิมเป็นแรงเสียดทานแบบกลิ้ง ช่วยลดแรงเสียดทานและลดความเสียหายต่อผลิตภัณฑ์ ดังที่แสดงในรูปที่ 7
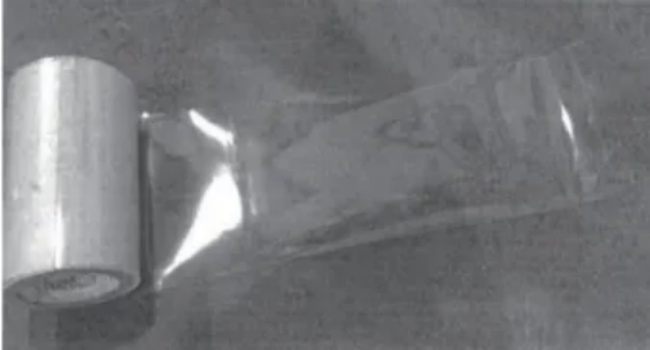
รูปที่ 6 : แผ่นยางป้องกันการบุบ
รูปที่ 7: แม่พิมพ์ล่างดัดด้วยลูกบอล
การดัดสปริงกลับ
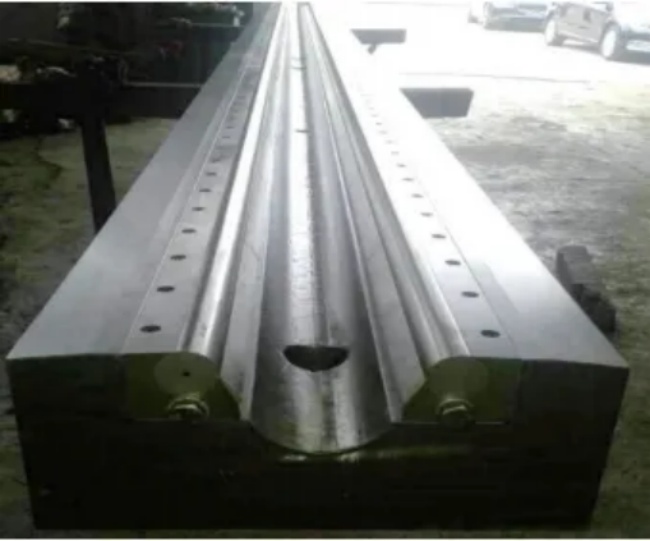
ในระหว่างกระบวนการดัด วัสดุจะเกิดการเสียรูปทั้งแบบยืดหยุ่นและแบบยืดหยุ่นพร้อมกัน เมื่อชิ้นงานออกจากแม่พิมพ์ดัด จะเกิดการคืนตัวแบบยืดหยุ่น ทำให้รูปร่างและขนาดของชิ้นส่วนที่ดัดไม่สอดคล้องกับแรงกด ซึ่งเรียกว่าการคืนตัวแบบดัด การดัดสปริงกลับ เป็นสาเหตุหลักประการหนึ่งที่ทำให้มุมดัดไม่เพียงพอ ปัจจัยหลักที่มีผลต่อการคืนตัวคือคุณสมบัติเชิงกลของแผ่นโลหะและเงื่อนไขของการเสียรูปจากการดัด ขนาดของค่าการคืนตัวจะแปรผันโดยตรงกับความแข็งแรงผลผลิตของแผ่นโลหะและแปรผกผันกับโมดูลัสของความยืดหยุ่น ยิ่งรัศมีการดัดสัมพันธ์ (อัตราส่วน R/t ของรัศมีการดัดต่อความหนาของแผ่นโลหะ) ของชิ้นส่วนที่ดัดเล็กลง ค่าการคืนตัวของการดัดก็จะยิ่งน้อยลง รูปร่างของชิ้นส่วนที่ดัดยังส่งผลต่อขนาดของค่าการคืนตัวของการดัดอีกด้วย โดยทั่วไป ชิ้นส่วนรูปตัว U จะมีค่าการคืนตัวน้อยกว่าชิ้นส่วนรูปตัว V
วิธีหลักในการเอาชนะแรงสปริงกลับแบบดัดคือวิธีการชดเชยมุม ซึ่งโดยทั่วไปจะใช้วิธีการทำให้ความลาดเอียงเท่ากับมุมสปริงกลับบนแม่พิมพ์ดัด ซึ่งสามารถปรับสมดุลผลกระทบของแรงสปริงกลับแบบดัดได้อย่างมีประสิทธิภาพ ดังที่แสดงในรูปที่ 8 การใช้แม่พิมพ์ดัดที่มีความลาดเอียง 80° สามารถดัดชิ้นงานที่มีมุมดัด 90° ได้อย่างราบรื่น
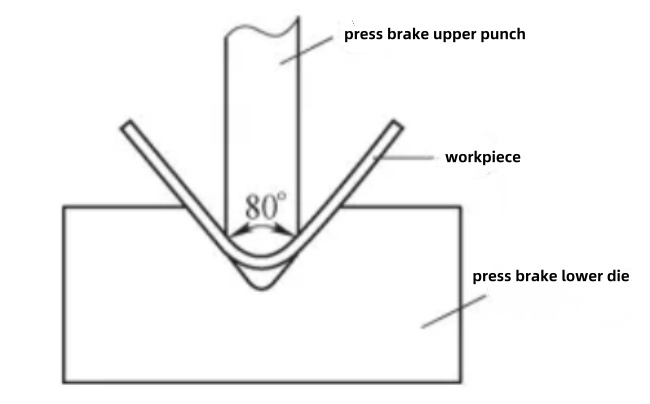
รูปที่ 8: การชดเชยการสปริงกลับแบบดัด
เนื่องมาจากปัจจัยหลายประการที่ส่งผลต่อการหดตัวแบบดัด จึงเป็นการยากมากที่จะคำนวณค่าการหดตัวได้อย่างแม่นยำ การแก้ไขแม่พิมพ์และการสะสมประสบการณ์ การเชี่ยวชาญกฎการหดตัว การปรับค่าชดเชยที่เหมาะสม และการใช้มาตรการเพื่อเอาชนะการหดตัวในโครงสร้างแม่พิมพ์และด้านอื่นๆ ถือเป็นวิธีที่มีประสิทธิภาพในการรับประกันคุณภาพของผลิตภัณฑ์
วัสดุสไลด์ดัด
สไลด์ดัด หมายถึงปรากฏการณ์ที่ชิ้นงานที่จะดัดไม่มีจุดรองรับที่สมบูรณ์และมีประสิทธิภาพบนร่องแม่พิมพ์ด้านล่าง ส่งผลให้ชิ้นงานมีแนวโน้มที่จะลื่น และไม่สามารถดัดให้วางตำแหน่งได้อย่างถูกต้อง
เหตุผลหลักในการดัดวัสดุเลื่อนมีดังต่อไปนี้
- เมื่อความกว้างของแม่พิมพ์ด้านล่างกว้างเกินไป และขนาดการดัดโค้งน้อยกว่าครึ่งหนึ่งของความกว้างของแม่พิมพ์ด้านล่าง จะเกิดการเลื่อนไถล
- เมื่อชิ้นงานได้รับผลกระทบจากรูปร่างและขนาด และขนาดการวางตำแหน่งของเทมเพลตสั้นเกินไปหรือไม่มีขอบการวางตำแหน่งเทมเพลตที่มีประสิทธิภาพ อาจเกิดปรากฏการณ์การดัดงอและการเลื่อนได้
มีสองวิธีหลักในการแก้ปัญหาวัสดุงอและเลื่อนไหล
- วิธีที่ 1. เลือกแม่พิมพ์ดัดที่เหมาะสม โดยทั่วไปควรเลือกความกว้างของแม่พิมพ์ประมาณ 4-6 เท่าของความหนาของแผ่นไม้ที่จะดัด
- วิธีที่ 2 การใช้วิธีการเพิ่มเทมเพลตหรือขอบกระบวนการ สามารถแก้ไขปัญหาการลื่นของวัสดุที่เกิดจากการวางตำแหน่งที่ไม่ถูกต้องเนื่องจากการดัดได้ โดยทั่วไป การดัดจะวางตำแหน่งโดยใช้ขอบตรงของชิ้นงาน ซึ่งต้องใช้หน้าตัดสองด้านที่สัมผัสกับเทมเพลตการดัดเพื่อวางตำแหน่ง อย่างไรก็ตาม ในกระบวนการผลิตจริง มีบางสถานการณ์ที่ขอบเทมเพลตผลิตภัณฑ์สั้นเกินไปหรือไม่มีขอบสำหรับวางตำแหน่งที่มีประสิทธิภาพ ส่งผลให้ไม่สามารถวางตำแหน่งการดัดได้อย่างสมบูรณ์ วิธีแก้ปัญหามีดังนี้
- เมื่อความหนาของแผ่น t ≤ 6 มม. ให้เพิ่มขอบกระบวนการสำหรับการวางตำแหน่ง และตำแหน่งของขอบกระบวนการที่ขยายออกไปควรอยู่ในระดับเดียวกับขอบด้านท้ายของอุปกรณ์เสริม ควรใช้การตัดด้วยเลเซอร์ที่จุดต่อเพื่อให้การเจียรและการกำจัดทำได้สะดวกหลังจากการดำเนินการดัดเสร็จสิ้น
- เมื่อความหนาของแผ่น t มากกว่า 6 มม. สามารถตัดเทมเพลตเพื่อวางตำแหน่งได้ โดยความหนาของเทมเพลตอาจเท่ากับหรือต่ำกว่าความหนาของชิ้นงานเล็กน้อยได้ ทั้งสองวิธีการวางตำแหน่งสามารถแก้ปัญหาการดัดงอและการเลื่อนของวัสดุได้
การดัดส่วนโค้งขนาดใหญ่
ในระหว่างกระบวนการผลิตและการผลิต มักจะพบสถานการณ์ที่รัศมีการดัดของชิ้นงานมีขนาดใหญ่และไม่มีแม่พิมพ์โค้งขนาดใหญ่ที่ตรงกันในเวิร์กช็อป ในกรณีนี้ วงจรการผลิตของแม่พิมพ์ขึ้นรูปชิ้นเดียวหรือแม่พิมพ์โค้งขนาดใหญ่จะยาวนานขึ้นและต้นทุนสูงเกินไป ในขณะที่การใช้เทคโนโลยีการดัดโค้งหลายรอบแบบโค้งขนาดเล็กมีต้นทุนต่ำกว่าและใช้งานได้กว้างกว่า ตัวอย่างเช่น ในโครงการ Super Bus 2.0 มีชิ้นส่วนที่มีแผ่นแนวตั้ง 1 แผ่นและแผ่นแนวตั้ง 3 แผ่น โดยมีรัศมีการดัด 125 มม. และมุมการดัด 90 ° ดังแสดงในรูปที่ 9 เนื่องจากไม่มีแม่พิมพ์ดัดที่สอดคล้องกันในเวิร์กช็อป จึงสามารถใช้กระบวนการดัดหลายกระบวนการได้ ประการแรก มีการใช้ซอฟต์แวร์ 3 มิติเพื่อสร้างแบบจำลองเค้าโครงและการดัดที่ตำแหน่ง R125 มม. หลังจากสร้างแบบจำลองแล้ว ซอฟต์แวร์จะกางไดอะแกรมแผ่นแบน 2 มิติโดยอัตโนมัติ จากการป้อนรัศมีการดัด 45 มม. ลงในซอฟต์แวร์และเปรียบเทียบข้อมูลอินพุตหลายรายการ ได้รับการยืนยันว่าส่วนโค้งวงกลมสามารถรับประกันได้โดยการดัดด้วยการตัด 8 ครั้ง จากนั้นจึงสร้างข้อมูลการดัด (มุมการดัด ความยาวตำแหน่งเส้นการดัด) สำหรับการตัดแต่ละครั้งตามที่แสดงในรูปที่ 10 ในที่สุด ดำเนินการทดลองดัดในสถานที่โดยอิงจากข้อมูลการดัดตามที่แสดงในรูปที่ 11
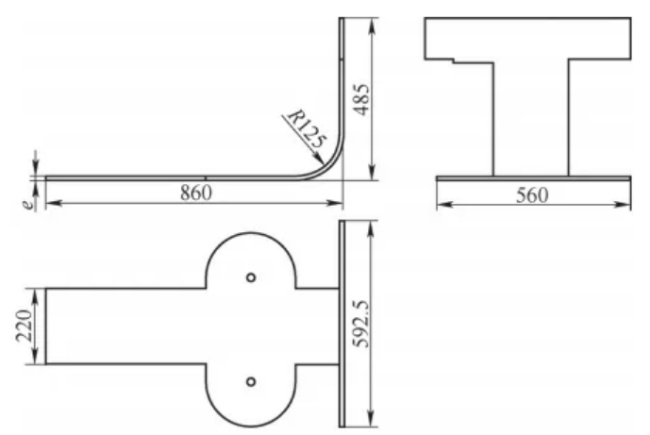
รูปที่ 9: ชิ้นงานรูปทรงโค้ง
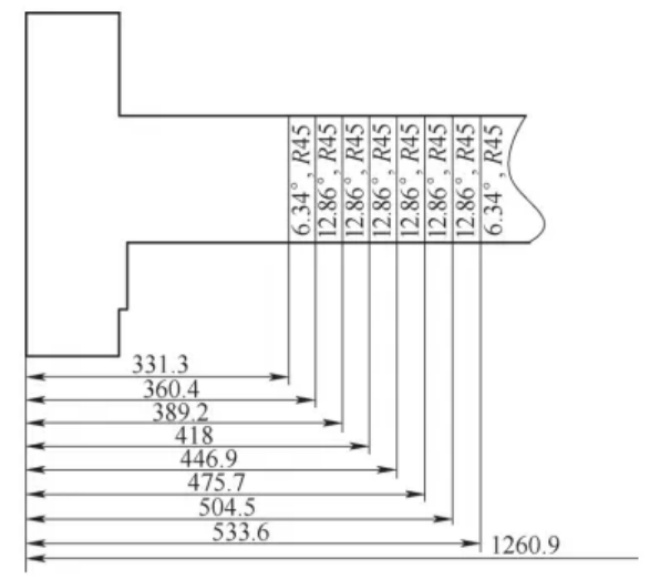
รูปที่ 10: แผนภาพการกางและตำแหน่งเส้นดัด

รูปที่ 11: การทดลองดัดแม่พิมพ์ในสถานที่
การยื่นโค้งงอ
การยื่นออกมาเนื่องจากการดัด หมายถึงปรากฏการณ์ที่วัสดุโลหะยื่นออกมาทั้งสองด้านของมุมที่ดัดของแผ่นโลหะเนื่องจากการบีบอัดวัสดุ ส่งผลให้ความกว้างมีขนาดใหญ่กว่าขนาดเดิม ขนาดของส่วนที่ยื่นออกมาเนื่องจากการดัดโดยทั่วไปจะสัมพันธ์กับความหนาของแผ่นเสริมและรัศมีการดัด ยิ่งแผ่นหนาขึ้น รัศมีการดัดก็จะเล็กลง และส่วนที่ยื่นออกมาจะชัดเจนมากขึ้น
เพื่อหลีกเลี่ยงปัญหาคุณภาพการดัดนี้ สามารถเพิ่มรอยบากของกระบวนการทั้งสองด้านของเส้นดัดระหว่างการวาดไดอะแกรมการคลี่การดัด ดังที่แสดงในรูปที่ 12 ช่องว่างของกระบวนการโดยทั่วไปจะมีลักษณะเป็นส่วนโค้งวงกลม โดยมีเส้นผ่านศูนย์กลางอย่างน้อย 1.5 เท่าของความหนาของชิ้นงาน เพื่อชดเชยส่วนที่ยื่นออกมาจากการดัดและแก้ปัญหาส่วนที่ยื่นออกมาจากการดัดได้อย่างมีประสิทธิภาพ สำหรับชิ้นงานที่มีส่วนที่ยื่นออกมาจากการดัดแล้ว โดยทั่วไปแล้วจะใช้การขัดด้วยมือในการประมวลผล
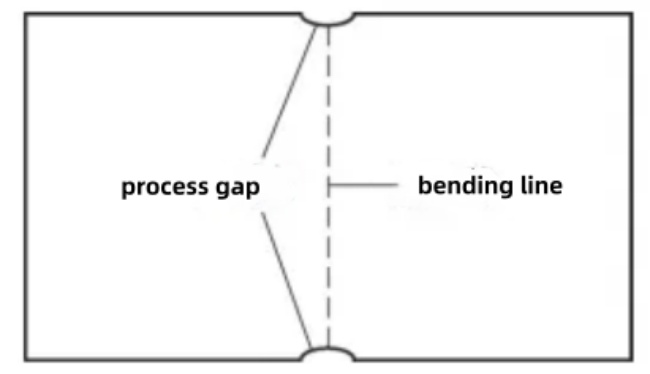
รูปที่ 12: ช่องว่างกระบวนการ
บทสรุป
ควรสังเกตว่าปัญหาคุณภาพการดัดและการตัดทั่วไปที่ระบุไว้ข้างต้นในการปฏิบัติการผลิตไม่ได้คำนึงถึงผลกระทบจากปัจจัยของมนุษย์หรืออุปกรณ์ (เช่น ขนาดการคลี่ที่ไม่ถูกต้อง การเลือกพารามิเตอร์การดัดที่ไม่ถูกต้อง และการเสื่อมสภาพของอุปกรณ์) ในการปฏิบัติการผลิต ควรเลือกพารามิเตอร์กระบวนการดัดที่เหมาะสมโดยพิจารณาจากประสิทธิภาพของอุปกรณ์ ขนาดผลิตภัณฑ์ และลักษณะของวัสดุ และดำเนินการอย่างเคร่งครัดตามข้อกำหนดการทำงาน เราไม่เพียงแต่ต้องพิจารณาผลกระทบของปัจจัยต่างๆ อย่างครอบคลุม เช่น ความคืบหน้าของโครงการ ต้นทุน และคุณภาพ และนำวิธีการที่เหมาะสมมาใช้เพื่อแก้ปัญหาคุณภาพการดัดเท่านั้น แต่ยังต้องสะสมประสบการณ์เพื่อคาดการณ์การเกิดขึ้นและผลกระทบของปัญหาการดัดในขั้นตอนการวิเคราะห์กระบวนการ และดำเนินมาตรการเฉพาะเพื่อป้องกันปัญหาเหล่านี้ บทความนี้แสดงรายการปัญหาคุณภาพการดัดทั่วไปหลายประการและแนวทางแก้ไข โดยหวังว่าจะให้ข้อมูลอ้างอิงและแนวทางแก่เพื่อนร่วมอุตสาหกรรม