สารบัญ
ภาพรวมการเชื่อมด้วยเลเซอร์
การเชื่อมด้วยเลเซอร์เป็นเทคโนโลยีการเชื่อมสมัยใหม่ที่มีข้อดีหลายประการ เช่น การเจาะลึก ความเร็วสูง การเสียรูปน้อย ความหนาแน่นของพลังงานสูง และไม่ได้รับผลกระทบจากสนามแม่เหล็ก มีการใช้กันอย่างแพร่หลายในด้านการผลิตที่มีความแม่นยำระดับสูง เช่น ยานยนต์ เรือ และอวกาศ บทความนี้จะแนะนำหลักการเชื่อมด้วยเลเซอร์ ข้อดีและข้อเสียเป็นหลัก ช่วยให้ผู้ที่ไม่เคยใช้การเชื่อมด้วยเลเซอร์มีความเข้าใจเบื้องต้นเกี่ยวกับเทคโนโลยีการเชื่อมนี้
หลักการเชื่อมด้วยเลเซอร์
การเชื่อมเลเซอร์สามารถทำได้โดยใช้ลำแสงเลเซอร์ต่อเนื่องหรือแบบพัลส์ และหลักการเชื่อมเลเซอร์สามารถแบ่งออกได้เป็นการเชื่อมด้วยการนำความร้อนและการเชื่อมด้วยการเจาะลึกด้วยเลเซอร์
- ความหนาแน่นของพลังงานที่น้อยกว่า 104-105 W/cm2 ถือเป็นการเชื่อมแบบนำความร้อน ซึ่งความลึกของการหลอมเหลวจะตื้นและความเร็วในการเชื่อมจะช้า หลักการของการเชื่อมด้วยเลเซอร์คือ การแผ่รังสีเลเซอร์ให้ความร้อนแก่พื้นผิวที่จะประมวลผล และความร้อนบนพื้นผิวจะถูกส่งไปยังภายในเพื่อแพร่กระจายผ่านการถ่ายเทความร้อน โดยการควบคุมพารามิเตอร์ต่างๆ เช่น ความกว้าง พลังงาน กำลัง และความถี่ของพัลส์เลเซอร์ ชิ้นงานจะถูกหลอมละลายเพื่อสร้างแอ่งหลอมเหลวเฉพาะ
- การเชื่อมด้วยเลเซอร์แบบเจาะลึกโดยทั่วไปจะใช้ลำแสงเลเซอร์ต่อเนื่องในการเชื่อมต่อวัสดุ และกระบวนการทางกายภาพทางโลหะวิทยาของการเชื่อมด้วยลำแสงอิเล็กตรอนนั้นคล้ายคลึงกับการเชื่อมด้วยลำแสงอิเล็กตรอนมาก กลไกการแปลงพลังงานทำได้โดยผ่านรูเล็กๆ ภายใต้การฉายแสงเลเซอร์ความหนาแน่นกำลังสูง วัสดุจะระเหยจนเกิดรูเล็กๆ ซึ่งเต็มไปด้วยไอเหมือนวัตถุดำและดูดซับพลังงานแสงที่ตกกระทบเกือบทั้งหมด ความร้อนจะถูกถ่ายเทจากผนังด้านนอกของโพรงอุณหภูมิสูง ทำให้โลหะที่อยู่รอบๆ โพรงหลอมละลาย ภายใต้การฉายแสงของลำแสง วัสดุของผนังจะระเหยอย่างต่อเนื่องเพื่อผลิตไอน้ำอุณหภูมิสูง แรงตึงผิวของชั้นผนังที่เกิดจากการไหลของของเหลวภายนอกผนังรูจะอยู่ในภาวะสมดุลคงที่โดยมีแรงดันไอน้ำที่เกิดขึ้นอย่างต่อเนื่องภายในโพรงรู ลำแสงจะเข้าไปในรูเล็กๆ อย่างต่อเนื่อง ซึ่งจะอยู่ในสถานะการไหลที่เสถียรอยู่เสมอ โลหะหลอมเหลวที่อยู่รอบๆ ผนังรูจะเคลื่อนไปข้างหน้าพร้อมกับลำแสงนำหน้า เติมช่องว่างที่รูเล็กๆ ทิ้งไว้และควบแน่นตามลำดับ จึงสร้างรอยเชื่อมขึ้น
ขอบเขตการประยุกต์ใช้งานการเชื่อมด้วยเลเซอร์
การเชื่อมด้วยเลเซอร์ได้รับการใช้กันอย่างแพร่หลายในหลายอุตสาหกรรม เช่น:
- อุตสาหกรรมยานยนต์: การเชื่อมด้วยเลเซอร์สามารถเชื่อมต่อส่วนประกอบยานยนต์ได้อย่างมีประสิทธิภาพและแม่นยำ ปรับปรุงผลผลิตและคุณภาพ ลดต้นทุนและมลพิษ การเชื่อมด้วยเลเซอร์สามารถใช้เชื่อมส่วนประกอบต่างๆ เช่น ตัวถังรถ แชสซี เครื่องยนต์ เกียร์ ท่อไอเสีย ถุงลมนิรภัย แผงหน้าปัด เป็นต้น ตัวอย่างเช่น การเชื่อมด้วยเลเซอร์สามารถออกแบบประตูท้ายรถแบบบูรณาการ ลดจำนวนและน้ำหนักของชิ้นส่วน ปรับปรุงความแข็งแรงและความแข็งแกร่ง และเพิ่มรูปลักษณ์และความปลอดภัย
- การต่อเรือ: การเชื่อมด้วยเลเซอร์สามารถใช้เชื่อมแผ่นเรือ แก้ปัญหาการบิดงอและการเสียรูปในงานเชื่อมแบบเดิม ปรับปรุงคุณภาพและความแข็งแรงของรอยเชื่อม และลดการใช้วัสดุและต้นทุนแรงงาน การเชื่อมด้วยเลเซอร์สามารถใช้เชื่อมโครงสร้างเรือ ดาดฟ้า กำแพงกันดิน ท้องเรือ ท่อส่ง และส่วนประกอบอื่นๆ ตัวอย่างเช่น การเชื่อมด้วยเลเซอร์สามารถประกอบโครงสร้างเรือขนาดใหญ่ได้อย่างรวดเร็ว ลดรอบการก่อสร้าง และปรับปรุงประสิทธิภาพการผลิต
- การใช้งานในบ้าน: การเชื่อมด้วยเลเซอร์สามารถใช้ในการผลิตบ้านอะลูมิเนียมทั้งหมด ทำให้สามารถเชื่อมต่อโปรไฟล์โลหะผสมอะลูมิเนียมได้อย่างราบรื่น ปรับปรุงความสวยงามและความทนทานของบ้าน และตอบสนองความต้องการในการปกป้องสิ่งแวดล้อมและสุขภาพ การเชื่อมด้วยเลเซอร์สามารถใช้ในการผลิตผลิตภัณฑ์ภายในบ้าน เช่น ตู้เสื้อผ้าอะลูมิเนียมทั้งหมด ชั้นวางหนังสืออะลูมิเนียมทั้งหมด และตู้รองเท้าอะลูมิเนียมทั้งหมด ตัวอย่างเช่น การเชื่อมด้วยเลเซอร์สามารถทำให้ฟอร์มาลดีไฮด์เป็นศูนย์ มลพิษเป็นศูนย์ และมูลค่าการรีไซเคิลในบ้านอะลูมิเนียมทั้งหมด สร้างแนวคิดใหม่ของการตกแต่งบ้านที่เป็นมิตรต่อสิ่งแวดล้อมและทันสมัย
การจำแนกประเภทของการเชื่อมด้วยเลเซอร์
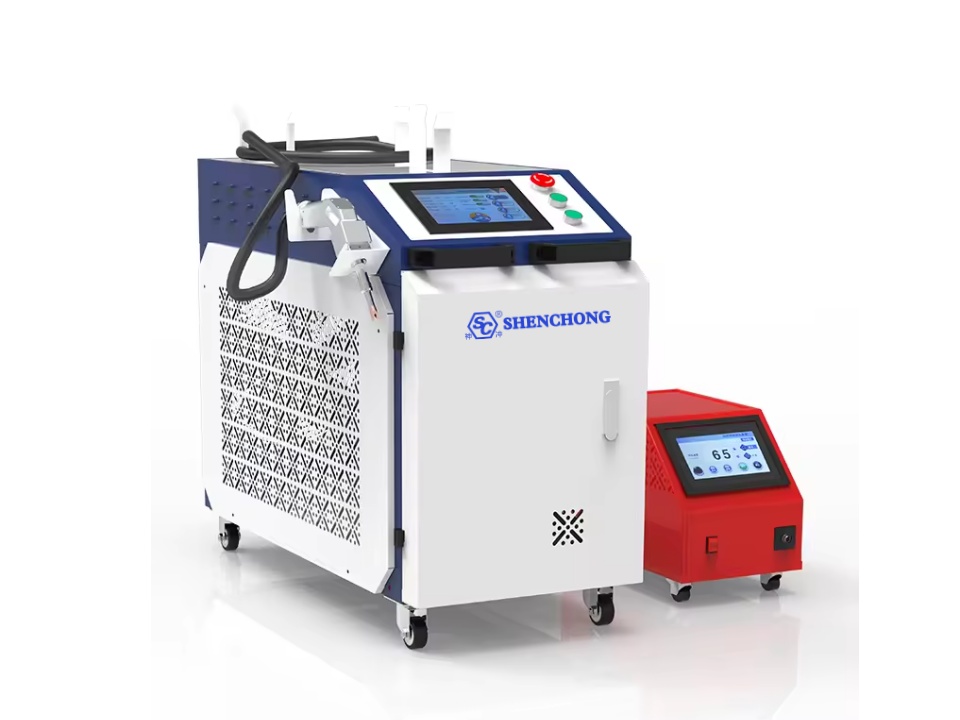
การเชื่อมด้วยเลเซอร์สามารถแบ่งออกได้เป็นการเชื่อมด้วยเลเซอร์แบบต่อเนื่องและการเชื่อมด้วยเลเซอร์แบบพัลส์ตามโหมดการส่งออกพลังงานที่แตกต่างกันของเลเซอร์ การเชื่อมด้วยเลเซอร์แบบต่อเนื่องจะสร้างรอยเชื่อมที่ต่อเนื่องและต่อเนื่องตลอดกระบวนการเชื่อม ในขณะที่การเชื่อมด้วยเลเซอร์แบบพัลส์จะสร้างจุดเชื่อมแบบวงกลมบนพื้นผิวของชิ้นงานที่เชื่อมเนื่องจากพลังงานที่ป้อนเข้าสู่พื้นผิวของชิ้นงานไม่ต่อเนื่อง สามารถสร้างรอยเชื่อมแบบต่างๆ ได้ตามการเปลี่ยนแปลงของพารามิเตอร์ของเลเซอร์ ตามความหนาแน่นของพลังงานที่แตกต่างกันของจุดโฟกัสด้วยเลเซอร์ การเชื่อมด้วยเลเซอร์สามารถแบ่งออกได้เป็นการเชื่อมด้วยการนำความร้อนและการเชื่อมแบบเจาะลึก
1. การเชื่อมด้วยการนำความร้อนด้วยเลเซอร์
ความหนาแน่นของพลังงานของจุดเชื่อมด้วยการนำความร้อนด้วยเลเซอร์บนพื้นผิวของชิ้นงานนั้นค่อนข้างต่ำ โดยทั่วไปจะน้อยกว่า 105W/cm2 เลเซอร์จะส่งพลังงานไปยังพื้นผิวของชิ้นงานที่เชื่อม ทำให้พื้นผิวโลหะร้อนขึ้นจนถึงอุณหภูมิระหว่างจุดหลอมเหลวและจุดเดือด พื้นผิวของวัสดุโลหะจะแปลงพลังงานแสงที่ดูดซับไว้เป็นพลังงานความร้อน ทำให้อุณหภูมิของพื้นผิวโลหะเพิ่มขึ้นอย่างต่อเนื่องและหลอมละลาย จากนั้นพลังงานความร้อนจะถูกถ่ายโอนไปยังภายในของโลหะผ่านการนำความร้อน ทำให้พื้นที่หลอมเหลวขยายขึ้นทีละน้อย หลังจากเย็นตัวลง จุดเชื่อมหรือรอยเชื่อมก็จะเกิดขึ้น หลักการเชื่อมนี้คล้ายกับการเชื่อมด้วยอาร์กก๊าซเฉื่อยทังสเตน (TIG) ซึ่งเรียกว่าการเชื่อมด้วยการนำความร้อน
2. การเชื่อมด้วยเลเซอร์แบบเจาะลึก (การเชื่อมรูเล็ก)
เมื่อความหนาแน่นของพลังงานเลเซอร์ที่ใช้กับพื้นผิวโลหะมีค่ามากกว่า 105W/cm2 ลำแสงเลเซอร์กำลังสูงจะกระทบกับพื้นผิวของวัสดุโลหะ ทำให้เกิดการหลอมละลายในบริเวณนั้นและเกิดเป็น “รูเล็กๆ” ลำแสงเลเซอร์จะทะลุเข้าไปในส่วนภายในของแอ่งหลอมเหลวผ่าน “รูเล็กๆ” ในขณะที่โลหะจะหลอมละลายที่ด้านหน้าของรูเล็กๆ โลหะหลอมเหลวจะไหลผ่านรูเล็กๆ ไปทางด้านหลัง แข็งตัวอีกครั้ง และก่อตัวเป็นรอยเชื่อม
ข้อดีและข้อเสียของการเชื่อมด้วยเลเซอร์
การเชื่อมด้วยเลเซอร์เป็นวิธีการเชื่อมที่มีประสิทธิภาพและแม่นยำซึ่งใช้ลำแสงเลเซอร์ที่มีความหนาแน่นพลังงานสูงเป็นแหล่งความร้อน การเชื่อมด้วยเลเซอร์เป็นหนึ่งในแง่มุมที่สำคัญของการประยุกต์ใช้เทคโนโลยีการประมวลผลวัสดุด้วยเลเซอร์ ซึ่งใช้กันอย่างแพร่หลายในสาขาต่างๆ เช่น ยานยนต์ อวกาศ อิเล็กทรอนิกส์ และการแพทย์ การเชื่อมด้วยเลเซอร์มีข้อดีคือมีความรวดเร็ว คุณภาพสูง มีความยืดหยุ่นสูง และปกป้องสิ่งแวดล้อม
ข้อดีของการเชื่อมด้วยเลเซอร์เมื่อเทียบกับวิธีการเชื่อมแบบเดิมคืออะไร การเชื่อมด้วยเลเซอร์มีปัญหาอะไรบ้าง และจะแก้ไขได้อย่างไร การเชื่อมด้วยเลเซอร์มีการใช้งานทั่วไปในด้านใดบ้าง
ข้อดีของการเชื่อมด้วยเลเซอร์
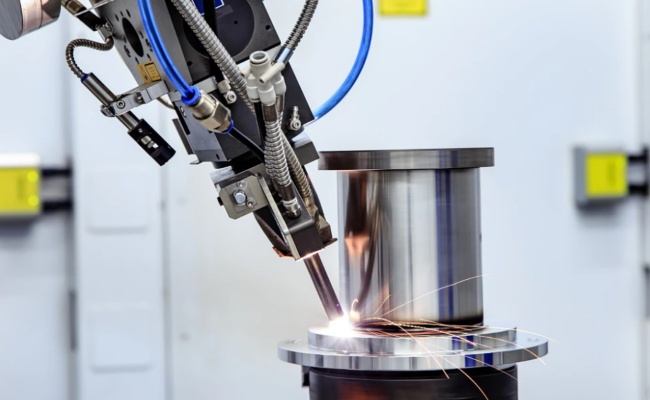
เมื่อเทียบกับวิธีการเชื่อมแบบดั้งเดิม การเชื่อมด้วยเลเซอร์มีข้อดีดังต่อไปนี้:
- ความเร็วที่รวดเร็ว ความลึกที่ลึก และการเสียรูปเพียงเล็กน้อย การเชื่อมด้วยเลเซอร์มีความหนาแน่นของพลังงานสูง อัตราการให้ความร้อนและการทำความเย็นที่รวดเร็ว โซนที่ได้รับผลกระทบจากความร้อนมีขนาดเล็ก และความเครียดในการเชื่อมและการเสียรูปต่ำ การเชื่อมด้วยเลเซอร์สามารถเชื่อมด้วยอัตราส่วนความกว้างยาวได้สูงสุด 10:1
- การประมวลผลแบบไม่ต้องสัมผัส มีความยืดหยุ่นสูง การเชื่อมด้วยเลเซอร์ไม่จำเป็นต้องสัมผัสกับชิ้นงาน และไม่จำเป็นต้องใช้ขั้วไฟฟ้าหรือวัสดุตัวเติม ซึ่งสามารถลดมลภาวะและการสูญเสียได้ การเชื่อมด้วยเลเซอร์สามารถส่งผ่านและแปลงผ่านส่วนประกอบออปติก ทำให้ทำงานร่วมกับหุ่นยนต์ได้ง่าย และทำให้สามารถทำงานอัตโนมัติและประมวลผลแบบหลายสถานีได้ การเชื่อมด้วยเลเซอร์สามารถทำได้ที่อุณหภูมิห้องหรือภายใต้เงื่อนไขพิเศษ เหมาะสำหรับการเชื่อมชิ้นส่วนหรือวัสดุทนไฟที่เข้าถึงได้ยาก
- คุณภาพสูงและประสิทธิภาพที่ดี การเชื่อมด้วยเลเซอร์สามารถลดข้อบกพร่อง เช่น รูพรุนและรอยแตกได้ เนื่องจากความร้อนที่ต่ำและอัตราการระบายความร้อนที่รวดเร็ว และปรับปรุงความหนาแน่นและความแข็งแรงของรอยเชื่อม การเชื่อมด้วยเลเซอร์ยังสามารถเชื่อมต่อโลหะต่างชนิดหรือวัสดุต่างชนิดได้ ทำให้โครงสร้างและคุณสมบัติดีขึ้น
- เป็นมิตรต่อสิ่งแวดล้อม ปลอดภัย และปราศจากมลภาวะ การเชื่อมด้วยเลเซอร์ไม่ก่อให้เกิดก๊าซหรือเสียงรบกวนที่เป็นอันตราย ไม่ได้รับผลกระทบจากสนามไฟฟ้าหรือสนามแม่เหล็ก และไม่เป็นอันตรายต่อสุขภาพของมนุษย์และสิ่งแวดล้อม
ความยากลำบากและแนวทางแก้ไขในการเชื่อมด้วยเลเซอร์
แม้ว่าการเชื่อมด้วยเลเซอร์จะมีข้อดีหลายประการ แต่การเชื่อมก็ยังคงมีปัญหาอยู่บ้าง:
- สะเก็ดโลหะจากการเชื่อม: หมายถึงการปรากฏของอนุภาคโลหะจำนวนมากบนพื้นผิวของวัสดุหลังจากการเชื่อมเสร็จสิ้น ซึ่งจะเกาะติดกับพื้นผิวของวัสดุ ซึ่งจะส่งผลต่อคุณภาพพื้นผิวของรอยเชื่อม และยังทำให้เลนส์ปนเปื้อนและเสียหายได้อีกด้วย สาเหตุของการกระเซ็นอาจเกิดจากพื้นผิวของวัสดุไม่สะอาด มีคราบน้ำมันหรือสารมลพิษ หรือการระเหยของชั้นสังกะสี
วิธีแก้ไขคือทำความสะอาดพื้นผิววัสดุก่อนเชื่อม ลดพลังงานในการเชื่อมให้เหมาะสม และลดการกระเด็นให้เหลือน้อยที่สุด
- รอยแตกร้าว: หมายถึงรอยแตกร้าวที่เกิดจากความร้อนที่เกิดจากการเชื่อมเลเซอร์อย่างต่อเนื่อง เช่น รอยแตกร้าวแบบผลึก รอยแตกร้าวแบบเหลว ฯลฯ สาเหตุหลักของรอยแตกร้าวคือแรงหดตัวที่มากเกินไปของรอยเชื่อมก่อนที่จะแข็งตัวอย่างสมบูรณ์
วิธีแก้ปัญหาคือการใช้วิธีการต่างๆ เช่น การเติมลวดและการอุ่นล่วงหน้าเพื่อลดหรือกำจัดรอยแตกร้าว
- รูพรุน: หมายถึงลักษณะรูพรุนที่ปรากฏบนพื้นผิวของรอยเชื่อม สาเหตุของการเกิดรูพรุนอาจเกิดจากแอ่งหลอมเหลวของการเชื่อมด้วยเลเซอร์ที่มีความลึกและแคบ มีอัตราการเย็นตัวที่รวดเร็ว และก๊าซที่เกิดขึ้นในแอ่งหลอมเหลวไม่สามารถระบายออกได้ทันเวลา อาจเป็นเพราะพื้นผิวของรอยเชื่อมไม่ได้รับการทำความสะอาดอย่างทั่วถึง หรือไอสังกะสีระเหยออกจากแผ่นสังกะสี
วิธีแก้ไขคือทำความสะอาดพื้นผิวของรอยเชื่อม ปรับปรุงการระเหยของสังกะสีเมื่อได้รับความร้อน และปรับทิศทางการเป่าลม
- การกัดขอบ: หมายถึงการยึดติดที่ไม่ดีระหว่างรอยเชื่อมและโลหะฐาน ส่งผลให้ร่องมีความลึกมากกว่า 0.5 มม. ความยาวรวมมากกว่า 10% ของความยาวรอยเชื่อม หรือความยาวมากกว่าข้อกำหนดมาตรฐานที่ยอมรับ สาเหตุของการเกิดการตัดด้านล่างอาจเกิดจากความเร็วในการเชื่อมเร็วเกินไป ซึ่งป้องกันไม่ให้โลหะเหลวกระจายตัวที่ด้านหลังของรูเล็ก หรือช่องว่างระหว่างชุดประกอบรอยเชื่อมอาจใหญ่เกินไป ส่งผลให้โลหะหลอมเหลวลดลงในกระบวนการเติม หรือเวลาการหยดพลังงานในตอนท้ายของการเชื่อมด้วยเลเซอร์เร็วเกินไป ทำให้รูเล็กยุบลง
วิธีแก้ปัญหาคือการควบคุมการจับคู่ของ เครื่องเชื่อมเลเซอร์ พลังการประมวลผลและความเร็วในการหลีกเลี่ยงการกัดขอบ ขัด ทำความสะอาด และซ่อมแซมขอบกัดที่พบระหว่างการตรวจสอบ
บทสรุป
การเชื่อมด้วยเลเซอร์เป็นเทคโนโลยีการเชื่อมที่มีความแม่นยำสูงและมีประสิทธิภาพสูงซึ่งมีแนวโน้มการใช้งานที่หลากหลาย วิธีการเชื่อมและสถานการณ์การใช้งานที่แตกต่างกันนั้นจำเป็นต้องมีการเลือกใช้วิธีการเชื่อมด้วยเลเซอร์ที่แตกต่างกันเพื่อให้ได้ผลลัพธ์การเชื่อมที่ดีที่สุด เทคโนโลยีการเชื่อมด้วยเลเซอร์ยังคงพัฒนาและสร้างสรรค์นวัตกรรมอย่างต่อเนื่อง และจะมีเลเซอร์ประเภทใหม่ๆ และกระบวนการต่างๆ เกิดขึ้นในอนาคต ซึ่งให้โซลูชันการเชื่อมที่มีคุณภาพสูงกว่า ประสิทธิภาพที่สูงกว่า และต้นทุนที่ต่ำกว่าสำหรับอุตสาหกรรมต่างๆ