Índice
Introdução
O sistema de carregamento e descarregamento de automação de metal é o equipamento revolucionário para mover automaticamente as chapas de metal de uma máquina para outra. A aplicação mais popular do sistema de carregamento e descarregamento automático é para máquina de corte a laser.
As máquinas de corte a laser revolucionaram a indústria de manufatura ao fornecer precisão, velocidade e versatilidade no corte de vários materiais. No entanto, para aproveitar totalmente as capacidades dessas máquinas, sistemas eficientes de manuseio de materiais são cruciais. Os sistemas de carga e descarga para máquinas de corte a laser desempenham um papel vital no aumento da produtividade, redução do tempo de inatividade e garantia da segurança. Este artigo se aprofunda nos diferentes tipos de sistemas de carga e descarga, seus benefícios, aplicações e tendências futuras, fornecendo uma visão geral abrangente desses componentes essenciais em operações de corte a laser.
A importância do sistema de carga e descarga de automação de metais
Os sistemas de carga e descarga são projetados para automatizar o processo de fornecimento de matérias-primas para a máquina de corte a laser e remoção de peças acabadas. Esses sistemas são essenciais por vários motivos:
- Aumento da produtividade:Os sistemas automatizados podem reduzir significativamente o tempo necessário para carregar e descarregar materiais, permitindo que a máquina de corte a laser opere de forma contínua e eficiente.
- Custos de mão de obra reduzidos:Ao automatizar esses processos, os fabricantes podem minimizar a necessidade de trabalho manual, reduzindo os custos de mão de obra e o potencial de erro humano.
- Segurança melhorada:Os sistemas automatizados aumentam a segurança no local de trabalho ao minimizar a necessidade de intervenção humana em operações potencialmente perigosas.
- Consistência e Qualidade: A automação garante o manuseio consistente dos materiais, o que contribui para manter altos padrões de qualidade no processo de corte.
Aplicações de sistemas de carga e descarga
1. Indústria Automotiva
Na indústria automotiva, sistemas de carga e descarga são usados para manusear grandes folhas de metal e peças complexas. Sistemas automatizados garantem qualidade consistente e alta produtividade, atendendo às demandas de produção em massa.
2. Indústria Aeroespacial
A indústria aeroespacial exige precisão e consistência na fabricação de componentes. Sistemas automatizados de carga e descarga ajudam a atingir esses requisitos ao garantir manuseio preciso de materiais e reduzir o risco de defeitos.
3. Fabricação de metais
A fabricação de metal envolve cortar, moldar e montar peças de metal. Os sistemas de carga e descarga simplificam esses processos ao automatizar o manuseio de matérias-primas e peças acabadas, aumentando a eficiência e a produtividade.
4. Indústria Eletrônica
Na indústria eletrônica, a precisão é primordial. Sistemas automatizados garantem o manuseio preciso de materiais e componentes delicados, minimizando o risco de danos e garantindo uma produção de alta qualidade.
5. Fabricação de Móveis
A indústria de fabricação de móveis se beneficia de sistemas automatizados que manipulam grandes folhas de madeira, metal ou materiais compostos. Esses sistemas aumentam a produtividade e garantem qualidade consistente na produção de componentes de móveis.
6. Fabricação de dispositivos médicos
Na fabricação de dispositivos médicos, sistemas automatizados de carga e descarga garantem o manuseio preciso de materiais e componentes, atendendo a rigorosos padrões de qualidade e segurança.
Tipos de sistemas de carga e descarga
1. Carregamento e descarregamento manual
Os sistemas manuais dependem de operadores humanos para carregar matérias-primas na máquina de corte a laser e remover peças acabadas. Embora esses sistemas sejam simples e econômicos, eles têm várias limitações:
- Aumento dos custos de mão de obra:Os sistemas manuais exigem uma quantidade significativa de mão de obra, o que pode ser caro, especialmente em ambientes de produção de alto volume.
- Inconsistência: Operadores humanos podem introduzir variabilidade no processo de carga e descarga, afetando a qualidade e a eficiência da operação de corte a laser.
- Riscos de segurança: O manuseio manual de materiais grandes e pesados pode representar riscos à segurança dos operadores.
2. Carregamento e descarregamento semiautomático
Os sistemas semiautomáticos combinam processos manuais e automatizados. Normalmente, um operador posiciona a matéria-prima, e o sistema a carrega automaticamente na máquina de corte a laser. Da mesma forma, o sistema descarrega peças acabadas, que o operador então coleta. Esses sistemas oferecem várias vantagens:
- Esforço de trabalho reduzido: Os sistemas semiautomáticos reduzem o esforço físico exigido dos operadores, melhorando a ergonomia e reduzindo a fadiga.
- Eficiência melhorada: A automação do processo de carga e descarga acelera a operação em comparação aos sistemas totalmente manuais.
- Segurança aprimorada: Ao reduzir a necessidade de manuseio manual de materiais, os sistemas semiautomáticos melhoram a segurança no local de trabalho.
3. Carregamento e descarregamento totalmente automáticos
Sistemas totalmente automáticos lidam com todo o processo de carregamento de matérias-primas e descarregamento de peças acabadas sem intervenção humana. Esses sistemas são equipados com tecnologias avançadas, como braços robóticos, transportadores e sensores para atingir altos níveis de automação:
- Produtividade Maximizada: Sistemas totalmente automáticos podem operar continuamente, aumentando significativamente o rendimento da máquina de corte a laser.
- Consistência e Precisão: A automação garante o manuseio consistente de materiais, mantendo altos padrões de qualidade e reduzindo o risco de erros.
- Economia de custos de mão de obra: Ao eliminar a necessidade de trabalho manual, os sistemas totalmente automáticos reduzem os custos de mão de obra e permitem que os operadores se concentrem em outras tarefas de valor agregado.
- Segurança: Sistemas totalmente automatizados aumentam a segurança ao minimizar a interação humana com máquinas e materiais.
Componentes do Sistema de Carga e Descarga de Automação de Metal
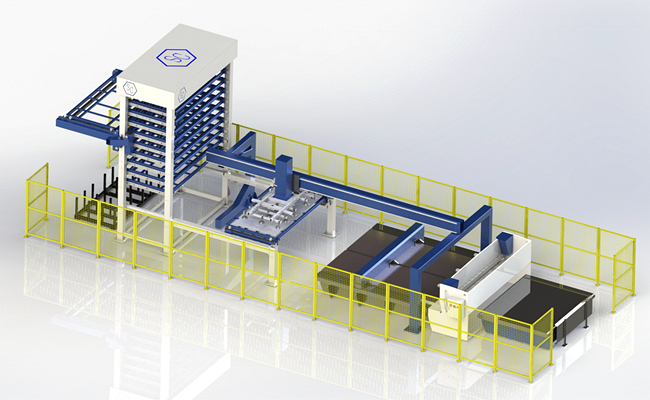
1. Armazenamento de materiais
O sistema de carga e descarga de automação de metal tem o sistema de armazenamento de metal. Ele tem a plataforma de paletização de metal simples ou pode se conectar com o sistema de armazenamento automático de metal. Os sistemas de armazenamento de materiais são usados para organizar e armazenar matérias-primas de uma maneira que facilite o acesso e o manuseio. Esses sistemas podem ser racks simples ou sistemas avançados de armazenamento e recuperação automatizados (AS/RS) que se integram à máquina de corte a laser.
- Prateleiras e estantes: Soluções básicas de armazenamento que permitem que os operadores recuperem materiais manualmente.
- Sistemas automatizados de armazenamento e recuperação (AS/RS): Sistemas avançados que armazenam e recuperam materiais automaticamente com base nos requisitos de produção, otimizando espaço e eficiência.
2. Equipamentos de movimentação de materiais
Equipamentos de manuseio de materiais são essenciais para transportar matérias-primas do armazenamento para a máquina de corte a laser e para mover peças acabadas para seu próximo destino. Tipos comuns de equipamentos de manuseio de materiais incluem:
- Transportadores: Transportadores de correia ou rolos transportam materiais entre diferentes estágios do processo de corte a laser.
- Braços Robóticos: Braços robóticos equipados com pinças ou dispositivos de sucção a vácuo manipulam materiais com precisão, permitindo carga e descarga automatizadas.
- Guindastes e Talhas: Usado para levantar e movimentar materiais pesados, especialmente em ambientes de fabricação em larga escala.
3. Carregadores e descarregadores
Carregadores e descarregadores são máquinas especializadas projetadas para automatizar o processo de colocação de matérias-primas na máquina de corte a laser e remoção de peças acabadas. Esses sistemas podem ser integrados a outros equipamentos de automação para criar um processo de manuseio de materiais sem emendas.
- Carregadores de folhas: Carregue automaticamente folhas de material na máquina de corte a laser, reduzindo o esforço manual e aumentando a eficiência.
- Descarregadores de peças: Remova automaticamente as peças acabadas da mesa de corte, garantindo uma operação suave e contínua.
4. Sistemas de controle
Os sistemas de controle gerenciam a operação de equipamentos de carga e descarga, garantindo movimentação precisa e coordenada de materiais. Esses sistemas podem ser autônomos ou integrados ao controle CNC da máquina de corte a laser.
- Controladores Lógicos Programáveis (CLPs):CLPs são usados para controlar a sequência de operações em sistemas automatizados, garantindo desempenho preciso e confiável.
- Interfaces Homem-Máquina (IHMs): As IHMs fornecem aos operadores uma interface amigável para monitorar e controlar o processo de carga e descarga.
Benefícios dos sistemas automatizados de carga e descarga
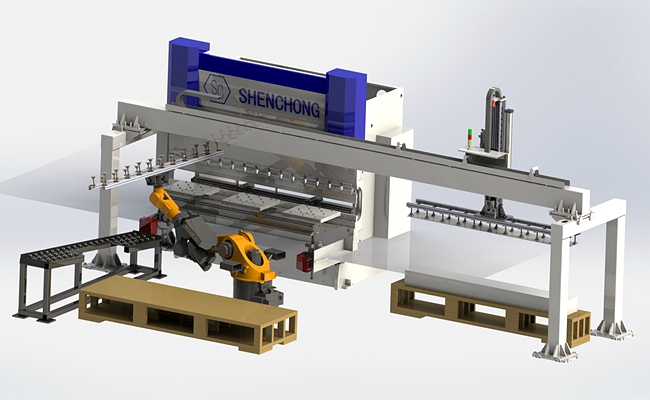
1. Produtividade aprimorada
Sistema automatizado de carga e descarga de chapas metálicas reduz significativamente o tempo necessário para carregar e descarregar materiais, permitindo que a máquina de corte a laser opere continuamente. Essa produtividade aumentada se traduz em maior rendimento e tempos de resposta mais rápidos.
2. Economia de custos de mão de obra
Ao automatizar os processos de manuseio de materiais, os fabricantes podem reduzir a dependência de trabalho manual. Isso não apenas reduz os custos de mão de obra, mas também minimiza o risco de erro humano, garantindo uma produção consistente e de alta qualidade.
3. Segurança melhorada
Sistemas automatizados de carga e descarga aumentam a segurança no local de trabalho ao reduzir a necessidade de interação humana com materiais pesados e potencialmente perigosos. Isso minimiza o risco de acidentes e ferimentos, criando um ambiente de trabalho mais seguro.
4. Consistência e Qualidade
A automação garante o manuseio consistente de materiais, o que é crucial para manter padrões de alta qualidade no processo de corte a laser. Sistemas automatizados podem posicionar materiais com precisão, reduzindo a probabilidade de desalinhamento e garantindo cortes precisos.
5. Otimização do espaço
Sistemas avançados de armazenamento e recuperação podem otimizar o uso do espaço disponível, permitindo que os fabricantes armazenem mais materiais em um espaço menor. Isso é particularmente benéfico em ambientes com espaço limitado.
6. Flexibilidade
Sistemas automatizados podem ser programados para lidar com diferentes tipos de materiais e tamanhos de peças, fornecendo flexibilidade na produção. Essa adaptabilidade é essencial para fabricantes que produzem uma variedade de produtos ou mudam frequentemente as execuções de produção.
Estudos de caso
1. Fabricante de automóveis
Um fabricante automotivo implementou um sistema de carga e descarga totalmente automatizado para suas máquinas de corte a laser. O sistema incluía braços robóticos, transportadores e um sistema avançado de armazenamento e recuperação. O resultado foi um aumento de 40% na produtividade, uma redução de 30% nos custos de mão de obra e segurança aprimorada para os operadores.
2. Fornecedor de componentes aeroespaciais
Um fornecedor de componentes aeroespaciais integrou sistemas automatizados de carga e descarga com suas máquinas de corte a laser. Os sistemas foram equipados com sensores e algoritmos de IA para monitoramento e otimização em tempo real. Essa integração levou a uma redução de 50% nos tempos de configuração, um aumento de 25% no rendimento da produção e controle de qualidade aprimorado.
3. Fabricante de eletrônicos
Um fabricante de eletrônicos adotou um sistema de carga e descarga semiautomático para suas operações de corte a laser. O sistema apresentava trocadores de ferramentas e transportadores automatizados para manuseio de materiais. A implementação resultou em uma redução de 35% no tempo de manuseio de materiais, precisão aprimorada e qualidade consistente na produção de componentes eletrônicos.
Pontos a considerar antes de comprar
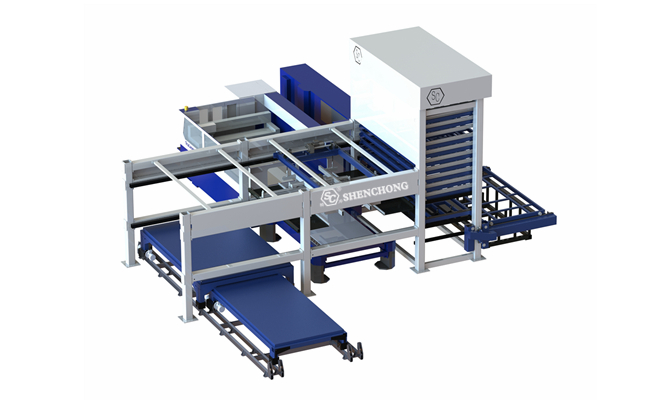
Ao comprar um sistema de carregamento e descarregamento de automação de metal, é essencial considerar cuidadosamente vários fatores para garantir que o sistema atenda aos seus requisitos de produção e necessidades de longo prazo. Aqui estão os pontos-chave para avaliar.
1. Capacidades de movimentação de materiais
- Tipo de Metal: Certifique-se de que o sistema seja compatível com os metais específicos com os quais você trabalha (por exemplo, aço, alumínio, etc.).
- Peso e tamanho: Confirme se o sistema pode suportar o peso, o tamanho e a espessura dos materiais a serem processados.
- Dimensões da folha/peça: Certifique-se de que o sistema acomoda a gama de dimensões que sua operação exige.
2. Nível de automação
- Manual, semi-automatizado ou totalmente automatizado: Determine se você precisa de automação total ou se um sistema semiautomatizado seria suficiente.
- Integração de Robótica: Avalie se braços robóticos ou outras tecnologias automatizadas são necessárias para sua aplicação específica.
- Eficiência do fluxo de trabalho: Considere o quão automatizado o processo deve ser para corresponder à sua velocidade de produção e reduzir o tempo de inatividade.
3. Capacidade e rendimento
- Velocidade de Carregamento/Descarregamento: Verifique se o sistema pode lidar com a produtividade necessária para corresponder ao seu ritmo de produção.
- Tempo de ciclo: Analise os tempos de ciclo das operações de carga e descarga para garantir que eles estejam alinhados com seu cronograma geral de produção.
- Carregamento em lote ou contínuo:Dependendo da sua escala de produção, determine se um sistema de lote ou um sistema de carregamento contínuo é mais apropriado.
4. Compatibilidade e integração do sistema
- Integração CNC/Prensa: Certifique-se de que o sistema se integra bem com suas máquinas CNC, lasers ou outras máquinas de corte e dobra.
- Compatibilidade de software: Verifique se o sistema é compatível com seu software de gerenciamento de produção ou sistemas ERP existentes.
- Controles de automação: Revise a interface do usuário e os sistemas de controle para facilitar o uso e a integração com outras máquinas no fluxo de trabalho.
5. Espaço e Layout
- Pegada: Considere o espaço físico que o sistema ocupará. Verifique se ele se encaixa na sua área de produção sem interromper o fluxo de trabalho.
- Acessibilidade: Garanta que o sistema seja facilmente acessível para manutenção, carregamento de matérias-primas e descarregamento de peças acabadas.
6. Opções de personalização
- Design modular: Procure sistemas com configurações modulares que permitam expansão ou personalização futura com base nas necessidades de produção em evolução.
- Soluções sob medida: Verifique se o fornecedor oferece opções de personalização com base em suas necessidades específicas de material ou operacionais.
7. Recursos de segurança
- Sensores e proteções de segurança: Certifique-se de que o sistema tenha mecanismos de segurança robustos, como botões de parada de emergência, sensores e proteções físicas para proteger os operadores.
- Conformidade com as Normas: Verifique se o sistema está em conformidade com os padrões de segurança locais e internacionais, como os regulamentos ISO ou OSHA.
8. Custo e ROI
- Custo inicial: Analise o investimento inicial e compare-o com os benefícios esperados, como aumento de produtividade ou redução de custos de mão de obra.
- Custos de manutenção: Considere os custos de manutenção a longo prazo e a disponibilidade de peças de reposição.
- Retorno do Investimento: Calcule o ROI do sistema com base em sua capacidade de reduzir mão de obra, aumentar a eficiência ou lidar com tarefas mais complexas.
9. Manutenção e Suporte
- Contratos de serviço: Avalie a garantia e o suporte de serviço fornecidos pelo fabricante.
- Requisitos de manutenção: Verifique a facilidade de manutenção do sistema, a disponibilidade de peças de reposição e a frequência de manutenção necessária.
- Treinamento e Instalação: Certifique-se de que o fornecedor oferece treinamento adequado para sua equipe e fornece suporte durante a instalação e configuração.
10. Reputação e referências do fornecedor
- Experiência do Fornecedor: Pesquise a experiência do fornecedor em fornecer sistemas de automação para o seu setor.
- Avaliações de clientes: Considere pedir referências de usuários atuais do sistema para avaliar a confiabilidade e o desempenho em aplicações do mundo real.
- Suporte Pós-Venda: Avalie a qualidade do serviço pós-venda, incluindo suporte técnico, tempo de resposta e disponibilidade de peças de reposição.
11. Impacto Ambiental
- Consumo de energia: Analisar a eficiência energética do sistema para manter os custos operacionais baixos e minimizar o impacto ambiental.
- Níveis de ruído: Considere recursos de redução de ruído se seu ambiente de produção tiver restrições de nível de ruído.
Avaliar esses fatores cuidadosamente ajudará você a selecionar um sistema que atenda às suas necessidades de produção, aumente a eficiência e forneça valor a longo prazo.
Faixa de preço do sistema de carga e descarga de chapas metálicas
A faixa de preço para o sistema de carregamento e descarregamento de automação de metal pode variar amplamente dependendo de fatores como tamanho do sistema, capacidade, nível de automação, marca e recursos específicos (por exemplo, integração CNC, robótica e recursos avançados de segurança). Geralmente, esses sistemas se enquadram nas seguintes faixas de preço:
- Sistemas Básicos:Para configurações menores ou menos complexas, os preços geralmente variam de $20.000 a $50.000.
- Sistemas de médio alcance: Sistemas com capacidades moderadas, melhor automação e opções de integração geralmente custam entre $50.000 e $150.000.
- Sistemas de ponta: Sistemas altamente avançados com recursos como automação completa, robótica integrada e maiores capacidades podem variar de $150.000 a $500.000 ou mais.
Personalização e recursos adicionais como integração de software ou mecanismos extras de segurança também podem afetar o preço. Para uma cotação específica, entrar em contato com fornecedores forneceria um valor mais preciso e adaptado às suas necessidades.
Tendências futuras em sistemas de carga e descarga
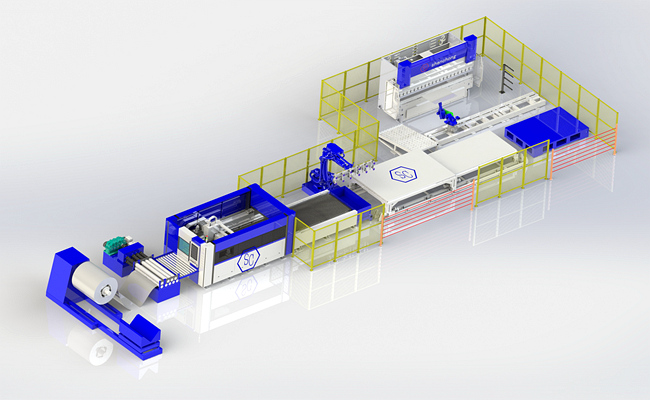
1. Integração com a Indústria 4.0
A integração de sistemas de carga e descarga com tecnologias da Indústria 4.0, como a Internet das Coisas (IoT), inteligência artificial (IA) e aprendizado de máquina, está pronta para revolucionar o manuseio de materiais. Essas tecnologias permitem monitoramento em tempo real, manutenção preditiva e tomada de decisão baseada em dados, aumentando a eficiência e a confiabilidade dos sistemas automatizados. Para conectar-se com outras unidades de automação, como sistema de armazenamento automático de metal, prensa dobradeira robótica, máquina de corte a laser para desenrolar e nivelar, a fábrica de processamento de chapas metálicas pode integrar linhas de produção de automação de chapas metálicas.
2. Robótica Avançada
Avanços na robótica estão impulsionando o desenvolvimento de sistemas automatizados mais sofisticados e capazes. Robôs colaborativos (cobots) que podem trabalhar junto com operadores humanos e robôs móveis autônomos (AMRs) que navegam e transportam materiais de forma independente estão se tornando cada vez mais prevalentes.
3. Flexibilidade aprimorada
Os futuros sistemas automáticos de carga e descarga de chapas metálicas oferecerão maior flexibilidade, permitindo que os fabricantes alternem facilmente entre diferentes materiais e tamanhos de peças. Sistemas modulares e reconfiguráveis permitirão uma rápida adaptação às mudanças nos requisitos de produção.
4. Eficiência Energética
À medida que a sustentabilidade se torna uma prioridade, os sistemas de carga e descarga de metais serão projetados com eficiência energética em mente. Inovações como motores com eficiência energética, sistemas de frenagem regenerativa e gerenciamento inteligente de energia reduzirão o impacto ambiental do manuseio automatizado de materiais.
5. Interfaces de usuário aprimoradas
Interfaces amigáveis ao usuário e sistemas de controle intuitivos aumentarão a facilidade de uso e acessibilidade de sistemas automatizados de carga e descarga. HMIs avançados e interfaces de realidade aumentada (AR) fornecerão aos operadores informações e orientação em tempo real, melhorando a eficiência geral.
Conclusão
Automação de metais O sistema de carga e descarga para máquinas de corte a laser são componentes cruciais que aumentam a produtividade, reduzem os custos de mão de obra e melhoram a segurança em ambientes de fabricação. De sistemas manuais a totalmente automatizados, essas tecnologias oferecem uma gama de soluções para atender às diversas necessidades de diferentes indústrias. À medida que os avanços em robótica, IA e tecnologias da Indústria 4.0 continuam a evoluir, o futuro do manuseio automatizado de materiais parece promissor, oferecendo ainda mais eficiência, flexibilidade e sustentabilidade.
Fabricantes que investem em sistemas avançados de carga e descarga podem esperar melhorias significativas em seus processos de produção, permitindo que permaneçam competitivos em um mercado cada vez mais exigente. Ao entender os benefícios, aplicações e tendências futuras desses sistemas, as empresas podem tomar decisões informadas e alavancar todo o potencial de suas operações de corte a laser.