Índice
Durante o processo de produção e fabricação, vários problemas de qualidade de dobra podem surgir ao dobrar peças de chapa metálica, o que pode afetar a melhoria da eficiência da produção e a estabilidade da qualidade do produto. Este artigo elabora problemas comuns de qualidade de dobra e corte na prática de produção, analisa as causas dos problemas e propõe soluções para fornecer experiência e referência para problemas semelhantes na prática de produção subsequente.
Introdução
A dobra de chapas metálicas é o processo de utilização de um molde universal (ou molde especializado) equipado com um Máquina dobradeira CNC para dobrar chapas de metal em várias formas geométricas transversais necessárias de peças de trabalho. A racionalidade do processo de dobra afeta diretamente o tamanho e a aparência da conformação final do produto. A seleção razoável de moldes de dobra é crucial para a conformação final dos produtos.
No processo de produção real, devido à incerteza do tamanho do produto e à diversidade de tipos de produtos, frequentemente encontramos problemas como interferência de tamanho e ângulos de molde incompatíveis durante a dobra de peças processadas a frio, o que traz grandes dificuldades à produção. Devido à influência de fatores como tamanho do produto, forma, material, molde, equipamento e instalações auxiliares durante o processo de dobra, vários problemas de qualidade podem ocorrer, afetando a eficiência da produção e a estabilidade da qualidade do produto. Portanto, é particularmente importante abordar e evitar a ocorrência desses problemas de qualidade de dobra. Este artigo resume e descreve principalmente os problemas de qualidade comuns da dobra de chapas metálicas na prática de produção, analisa as razões com base na experiência de produção e propõe soluções.
Problemas comuns de qualidade de dobra
Dobrando e rachando
Fissuras por flexão se referem ao fenômeno em que rebarbas ou pequenas fissuras frequentemente aparecem nas bordas dos materiais após corte, cisalhamento ou estampagem, e a concentração de tensão é facilmente formada durante a flexão, resultando em fissuras. A ranhura de reforço em forma de U das peças da locomotiva trinca nos cantos após a flexão, conforme mostrado na Figura 1.
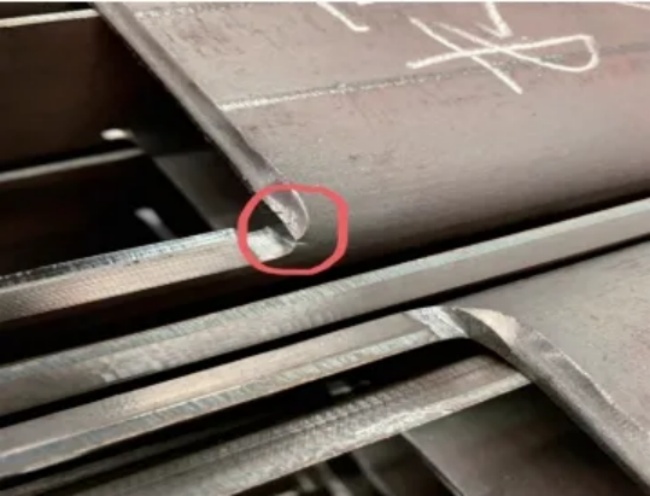
Figura 1 Flexão e fissuração
As principais causas de entortamento e rachaduras são:
- Rebarbas sujas nas bordas das peças.
- A direção de dobra é paralela à direção de laminação da chapa metálica.
- O raio de curvatura da chapa metálica é muito pequeno.
Durante o processo de produção e fabricação, é necessário lidar com fenômenos de flexão e rachadura de acordo com circunstâncias específicas. Para o problema de flexão e rachadura na Figura 1, o método de adicionar furos de processo ou ranhuras de processo pode ser adotado para resolvê-lo, conforme mostrado na Figura 2.
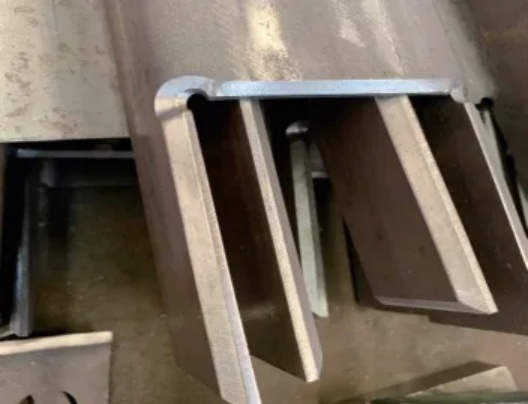
Figura 2: Adicionando furos de processo
Interferência de flexão
A interferência de flexão é principalmente direcionada a produtos com flexão secundária ou superior, onde a borda de flexão colide com o molde ou equipamento, resultando na incapacidade de formar adequadamente. A interferência de flexão é principalmente influenciada pela forma, tamanho e molde das peças, e é causada principalmente pela estrutura de design da própria peça dobrada, a sequência de flexão selecionada e o molde de flexão selecionado. Portanto, as principais soluções incluem:
- fazer novos moldes ou substituir moldes (como moldes para facas de dobrar).
- Transformação de moldes de dobra (como processamento mecânico de peças locais).
- Ajuste a sequência de dobra (como o método de deformação reversa).
- Altere o tamanho da curvatura das peças. Por exemplo, o suporte de instalação para o canal de acessórios do chassi da Linha 18 do Metrô de Xangai é feito de aço de canal em forma de U, com uma largura média de 100 mm, altura da borda de 80 mm e um raio de curvatura de 15 mm. Simule a curvatura com base nos moldes existentes na oficina para gerar interferência de curvatura.
Em resposta a esse fenômeno de interferência, um método de processamento mecânico local foi adotado para a matriz superior de dobra (veja a Figura 3). Um entalhe de 140 mm × 48 mm foi cortado ao longo da linha média da matriz superior de faca reta R15 mm existente (L=800 mm) (veja a Figura 4). A posição do entalhe foi determinada combinando-a com a posição de interferência de dobra simulada, sem afetar sua função original. Após modificar o molde de dobra, o problema de interferência de dobra foi resolvido com sucesso.
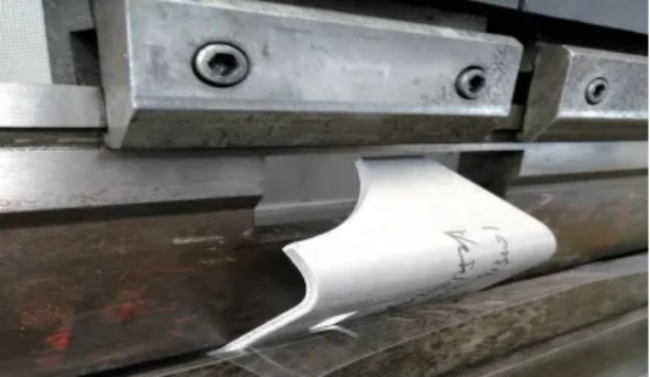
Figura 3: Dobramento após processamento do molde superior
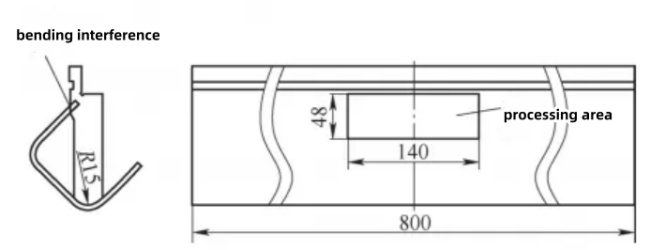
Figura 4: Interferência de flexão, determinando a área de processamento
Recuo de flexão
A indentação de dobra é um fenômeno no qual o atrito é gerado durante o processo de colocar gradualmente a chapa metálica em contato com a superfície interna da ranhura em forma de V do molde côncavo, resultando em marcas óbvias deixadas na superfície da chapa metálica. Para alguns acessórios com altos requisitos de superfície, a dobra tradicional não pode atender aos requisitos de qualidade do produto, e a indentação de dobra (veja a Figura 5) não pode atender aos requisitos do próximo processo.
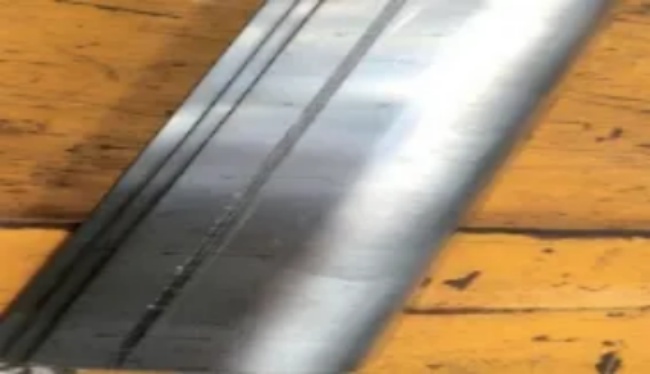
Figura 5: Recuo de flexão
A indentação de flexão é afetada principalmente pela dureza da chapa metálica e pela estrutura do molde inferior. Quanto maior a dureza da chapa, maior sua capacidade de resistir à deformação plástica, tornando mais difícil para o material sofrer deformação plástica e mais fácil produzir indentação. A probabilidade de indentação de flexão em materiais de chapa comumente usados é: alumínio > aço carbono > aço inoxidável. Quanto maior a largura da abertura da matriz de dobra, maior a largura da indentação de flexão e menor a profundidade da indentação. Quanto maior o tamanho R do ombro de abertura do molde inferior, menor a profundidade da indentação.
Além de melhorar a dureza do material e a estrutura inferior do molde, almofadas de borracha anti-indentação e moldes inferiores de dobra do tipo esfera também podem ser usados para resolver o problema de indentação de dobra. A almofada de borracha anti-indentação depende principalmente do isolamento físico para reduzir a ocorrência de indentação, conforme mostrado na Figura 6. A matriz de dobra do tipo esfera transforma o atrito de extrusão necessário para moldes de dobra tradicionais em atrito de rolamento, reduzindo o atrito e minimizando os danos ao produto, conforme mostrado na Figura 7.
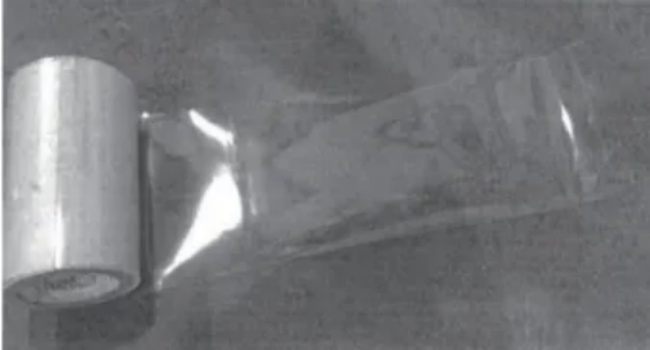
Figura 6: Almofada de borracha anti-indentação
Figura 7: Molde inferior de flexão de esferas
Dobrando o retorno elástico
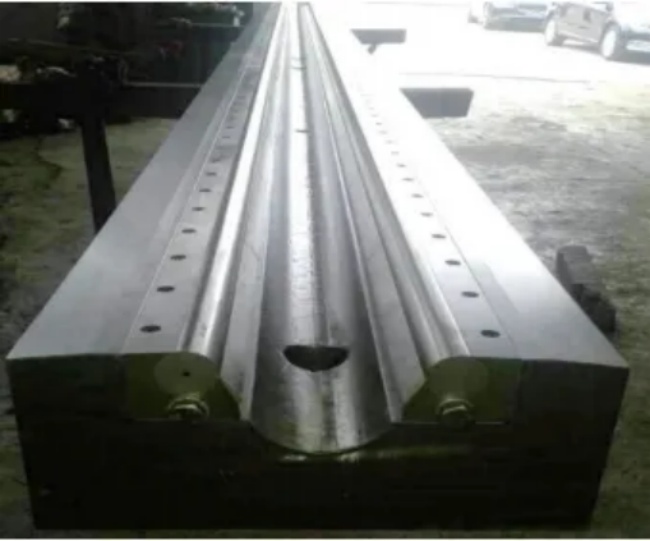
Durante o processo de dobra, os materiais sofrem deformação plástica e deformação elástica simultaneamente. Quando a peça de trabalho sai do molde de dobra, ocorre recuperação elástica, fazendo com que o formato e o tamanho da peça dobrada sejam inconsistentes com a carga, o que é chamado de rebote de dobra. Retorno elástico de flexão é uma das principais razões para ângulo de curvatura insuficiente. Os principais fatores que afetam o rebote são as propriedades mecânicas da chapa metálica e as condições de deformação da curvatura. A magnitude do valor do retorno elástico é diretamente proporcional à resistência ao escoamento da chapa metálica e inversamente proporcional ao módulo de elasticidade. Quanto menor o raio de curvatura relativo (razão R/t do raio de curvatura para a espessura da chapa) da peça dobrada, menor o valor do retorno elástico de curvatura. O formato da peça dobrada também afeta a magnitude do valor do retorno elástico de curvatura. Geralmente, peças em formato de U têm um valor de retorno elástico menor do que peças em formato de V.
O principal método para superar o retorno elástico de flexão é o método de compensação de ângulo, que geralmente adota o método de fazer uma inclinação igual ao ângulo de retorno elástico no molde de flexão, o que pode equilibrar efetivamente o impacto do retorno elástico de flexão. Conforme mostrado na Figura 8, usar um molde de flexão com uma inclinação de 80° pode dobrar suavemente peças de trabalho com um ângulo de flexão de 90°.
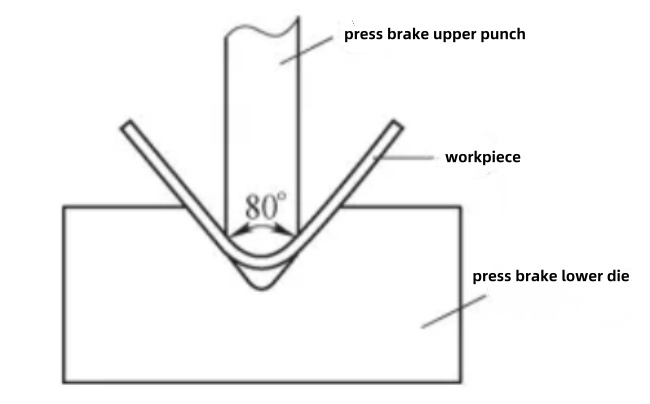
Figura 8: Compensação de retorno elástico de flexão
Devido aos muitos fatores que afetam o retorno elástico de flexão, é muito difícil calcular com precisão o valor do retorno elástico. Por meio da correção do molde de teste e do acúmulo de experiência, dominar a lei do retorno elástico, adotar a compensação apropriada e tomar medidas para superar o retorno elástico na estrutura do molde e outros aspectos são métodos eficazes para garantir a qualidade do produto.
Material de deslizamento de flexão
Deslizamento de dobra refere-se ao fenômeno em que a peça a ser dobrada não tem um ponto de apoio completo e eficaz na ranhura inferior da matriz, resultando na propensão da peça a escorregar e na incapacidade de posicionar corretamente a dobra.
As principais razões para a flexão de materiais deslizantes são as seguintes.
- Quando a largura do molde inferior é muito grande e o tamanho da curvatura é menor que a metade da largura do molde inferior, ocorre deslizamento.
- Quando a peça de trabalho é afetada por seu formato e tamanho, e o tamanho de posicionamento do gabarito é muito curto ou não há uma borda de posicionamento efetiva do gabarito, podem ocorrer fenômenos de flexão e deslizamento.
Existem dois métodos principais para resolver o problema de flexão e deslizamento de materiais.
- Método 1. Escolha uma matriz de dobra adequada, geralmente escolhendo uma largura de matriz de 4 a 6 vezes a espessura da placa a ser dobrada.
- Método 2. Usando o método de adicionar modelos ou bordas de processo, o problema de deslizamento do material causado por posicionamento ruim devido à dobra pode ser resolvido. Em geral, a dobra é posicionada por uma borda reta da peça de trabalho, o que requer que duas faces finais estejam em contato com o modelo de dobra para posicionamento. No entanto, no processo de produção real, há situações em que a borda do modelo do produto é muito curta ou não há borda de posicionamento eficaz, resultando na incapacidade de concluir o posicionamento da dobra. As soluções são:
- Quando a espessura da placa t ≤ 6 mm, adicione uma borda de processo para posicionamento, e a posição da extensão da borda de processo deve estar nivelada com a borda final do acessório. O corte a laser deve ser usado na junção para facilitar a retificação e a eliminação após a conclusão da operação de dobra.
- Quando a espessura da placa t for maior que 6 mm, um modelo pode ser cortado para posicionamento, e a espessura do modelo pode ser igual ou ligeiramente menor que a espessura da peça de trabalho. Ambos os métodos de posicionamento podem resolver o problema de dobrar e deslizar materiais.
Grande arco de flexão
Durante o processo de produção e fabricação, é comum encontrar situações em que o raio de curvatura da peça de trabalho é grande e não há um molde de arco grande correspondente na oficina. Nesse caso, o ciclo de produção de moldes de conformação integral ou moldes de arco grande é mais longo e o custo é muito alto, enquanto o uso da tecnologia de conformação de dobra de múltiplas passagens de arco pequeno tem menor custo e aplicabilidade mais ampla. Por exemplo, no projeto Super Bus 2.0, há um componente com uma placa vertical e três placas verticais, com um raio de curvatura de 125 mm e um ângulo de curvatura de 90 °, conforme mostrado na Figura 9. Devido à falta de moldes de curvatura correspondentes na oficina, vários processos de curvatura podem ser usados. Primeiramente, um software 3D foi usado para modelar o layout e a curvatura na posição R125 mm. Após a modelagem, o software desdobrou automaticamente o diagrama de placa plana 2D. Ao inserir um raio de curvatura de 45 mm no software e comparar múltiplas entradas de dados, foi confirmado que o segmento de arco circular poderia ser garantido pela curvatura com 8 cortes. Então, os dados de curvatura (ângulo de curvatura, comprimento da posição da linha de curvatura) para cada corte foram gerados, como mostrado na Figura 10. Finalmente, a curvatura de teste no local foi conduzida com base nos dados de curvatura, como mostrado na Figura 11.
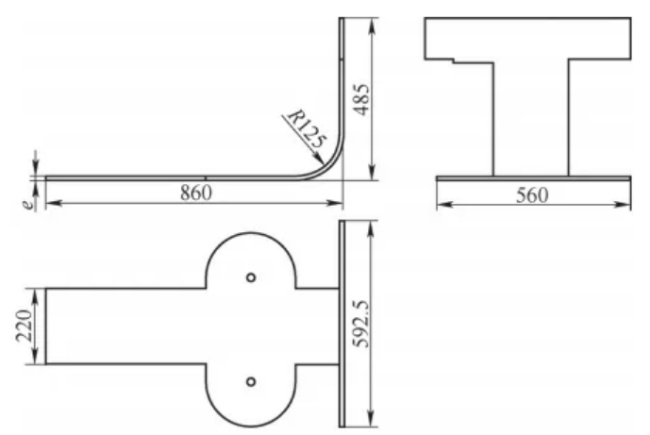
Figura 9: Peças em forma de arco
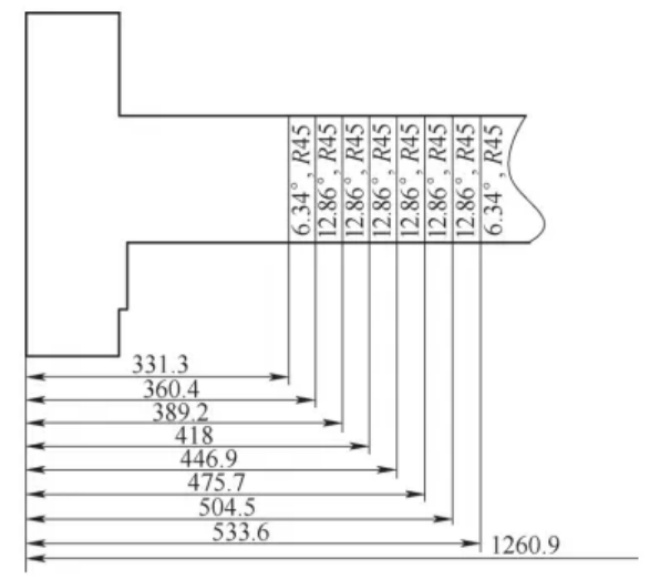
Figura 10: Diagrama de desdobramento e posição da linha de dobra

Figura 11: Teste de dobra do molde no local
Protrusão de flexão
Protrusão de curvatura refere-se ao fenômeno em que o material metálico se projeta em ambos os lados do canto dobrado da chapa metálica devido à compressão do material, resultando em uma largura maior do que o tamanho original. O tamanho da protrusão de curvatura geralmente está relacionado à espessura da placa acessória e ao raio de curvatura. Quanto mais espessa a placa, menor o raio de curvatura e mais óbvia a protrusão.
Para evitar esse problema de qualidade de dobra, entalhes de processo podem ser adicionados em ambos os lados da linha de dobra durante o desenho do diagrama de desdobramento de dobra, conforme mostrado na Figura 12. A lacuna do processo geralmente tem a forma de um arco circular, com um diâmetro de pelo menos 1,5 vezes a espessura da peça de trabalho, para compensar a saliência de dobra e resolver efetivamente o problema da saliência de dobra. Para peças de trabalho que já produziram saliências de dobra, o polimento manual é geralmente usado para processamento.
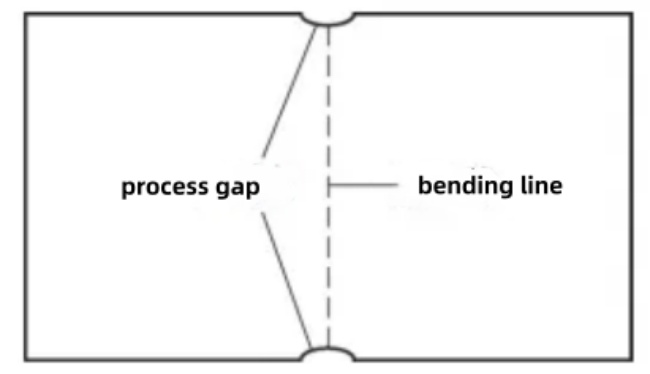
Figura 12: Lacuna de processo
Conclusão
Deve-se notar que os problemas comuns de qualidade de dobra e corte listados acima na prática de produção não levaram em consideração o impacto de fatores humanos ou de equipamentos (como dimensões de desdobramento incorretas, seleção incorreta de parâmetros de dobra e envelhecimento do equipamento). Na prática de produção, os parâmetros apropriados do processo de dobra devem ser selecionados com base no desempenho do equipamento, tamanho do produto e características do material, e executados rigorosamente de acordo com as especificações operacionais. Não precisamos apenas considerar de forma abrangente o impacto de vários fatores, como progresso do projeto, custo e qualidade, e adotar métodos apropriados para resolver problemas de qualidade de dobra, mas também precisamos acumular experiência para prever a ocorrência e o impacto de problemas de dobra no estágio de análise do processo e tomar medidas direcionadas para preveni-los. Este artigo lista vários problemas comuns de qualidade de dobra e suas soluções, na esperança de fornecer alguma referência e orientação para colegas da indústria.