Punch Press Machines Introduction
Table of Contents
Punch press machines are multifunctional tools used for metal processing and manufacturing, which shapes or cuts materials by applying force through punches and molds, most commonly metal plates. Punching machines are operated by mechanical, hydraulic, or servo driven mechanisms to press the punch into the material, forming holes, embossing, or shaping the material into the required shape.
Punching machines are indispensable in various industries due to their ability to quickly and efficiently produce high-precision parts. Punching machines play a crucial role in modern manufacturing processes, from automotive and aerospace components to everyday consumer goods. Punch press has the ability to handle large-scale production with consistent quality makes them the backbone of mass production.
This article aims to explore in detail the history, types, working principles, applications, advantages and disadvantages, safety considerations, technological progress, and economic impact of punching machines. Whether you are an experienced professional machine tool operator or a purchaser about to purchase equipment, this comprehensive guide will provide you with detailed information about punching press machines.
History of Punch Press Machines
Early Development of Punch Press Technology
The concept of punching materials can be traced back to ancient times, when humans first began using sharp tools to punch holes in various materials for practical purposes such as making clothes, residences, or tools. Early civilizations used basic stamping methods to punch holes in leather, wood, and metal. These manual methods laid the foundation for developing more complex stamping techniques.
Evolution Of Punch Press Machines
The evolution of punch presses can be traced back to the emergence of mechanical engineering and the Industrial Revolution in the 18th and 19th centuries. The invention of steam engines and later electric motors enabled the development of mechanical punching machines, which can apply greater force more accurately than manual methods. The first mechanical punch press was a simple manual machine that required a large amount of manpower. However, with the advancement of technology, these machines have become more automated and capable of handling increasingly complex tasks.
Key Milestones In The Development Of Punching Press Machines
- 1795: James Watt’s steam engine led to the development of the first power mechanical punch press.
- In the 1890s, the introduction of hydraulic systems led to the invention of hydraulic presses.
- In the 1950s, the rise of numerical control (NC) and later computer numerical control (CNC) completely changed punch press technology, achieving higher precision and automation.
- In the 1980s, servo driven punch presses were introduced, providing enhanced control and energy efficiency.
- In the 21st century, intelligent technology, the Internet of Things, and artificial intelligence are integrated into punch pressmachines to further optimize efficiency and accuracy.
Operation Process Of Punch Press Machines
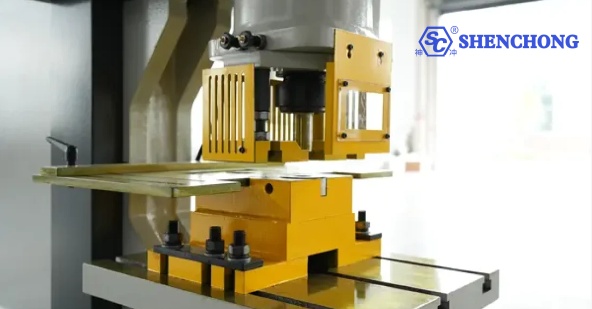
The operation process of a punching machine involves several steps, each of which is crucial for the successful operation of the machine.
Basic Operating Steps Of Punch Press Machine
- Material positioning: Place the material (usually a metal plate) on the press bed and align it with the mold assembly.
- Stamping: The punch moves downwards, driving the punch through the material and into the mold. This operation cuts materials to create holes or form specific shapes.
- Material ejection: After the stamping operation, the stamped workpiece (block) is ejected from the mold, and the material is repositioned for the next stamping.
- Gate Return: The gate returns to its starting position to prepare for the next cycle.
In mass production, this cycle will be repeated continuously, and the machine will automatically feed and align the material between each punch.
Detailed Explanation Of Punch Press Process
Shear: The punch cuts material by applying shear force. The material is first compressed, then fractured, and finally separated when the punch passes through.
Gap: The gap between the punch and the mold is crucial for achieving clean cutting. Too small a gap can cause excessive wear on the punch and mold, while too large a gap can result in poor edge quality and burrs.
Demoulding: After the punch passes through the material, it must be pulled out. The stripping action is the process of separating the punch from the material, usually assisted by a stripping plate or a spring-loaded device.
Function Of Press Machines Molds And Punches
The mold and punch are the core of the press machine. The punch attached to the punch is a tool used for actual cutting or forming. The mold fixed on the pressure machine provides the surface for the punch to work. They collectively determine the shape, size, and quality of the finished product.
Mold design: The design of the mold determines the shape and size of the punched holes or features. Molds can be simple (single station) or complex (multi station, such as progressive dies).
Punch material: Punches are usually made of hardened tool steel or hard alloy to withstand the high forces and wear involved in the punching process.
Material Handling And Feeding System
Efficient material handling is crucial for large-scale punching press machine operations. Modern punching machines are equipped with automatic feeding systems that can move materials to the position of each punch.
Roller feeder: usually used for feeding metal plates, the roller feeder automatically advances the material between each punch cycle.
Clamp feeders: These systems use mechanical clamps to pull materials into place, typically for thicker or harder materials.
Automatic stacking and sorting: After punching, finished parts are usually automatically stacked or sorted for further processing or packaging.
Energy Transfer Mechanism
The efficiency and effectiveness of a punching machine depend on the degree to which it transfers energy from the power source to the punch. In a mechanical press, energy is stored in the flywheel and released during a powerful stroke. Hydraulic presses use fluid power to stably apply force, while servo driven presses use precise motor control to change force and speed as needed.
Advantages and Limitations of Press Machines
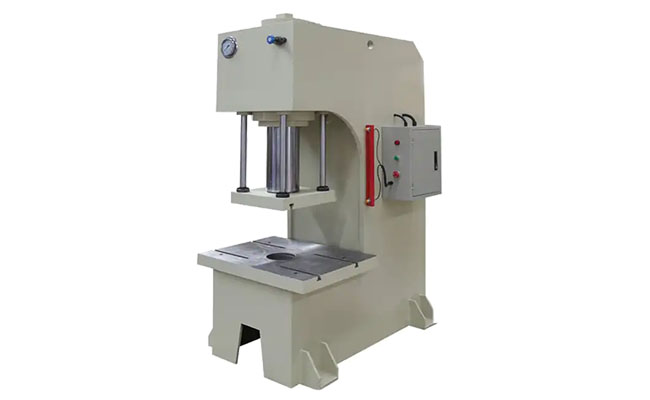
Press machines have several advantages that make them crucial in sheet metal manufacturing.
- Efficient and fast: Press machines can quickly and efficiently produce a large number of parts, making them an ideal choice for mass production.
- Accuracy and precision: Modern pressmachines, especially CNC and servo driven punch press machines, provide high precision and accuracy, ensuring that parts meet strict tolerances and quality standards.
- Diversity of materials and designs: pressmachines can process various materials, including metals, plastics, and composite materials, and can produce various shapes and features.
- The cost-effectiveness of large-scale production: press machines have high cost-effectiveness for large-scale production because they can produce parts at lower unit costs.
- Consistency and repeatability: punch press machines provide consistent and reproducible results, ensuring that each part is identical to the previous one.
- Low material waste: punching and pressing is a material efficient process because it generates the least amount of waste compared to other manufacturing methods.
Although punch press machines have many advantages, they also have some limitations:
- Initial cost and maintenance: The initial cost of purchasing a press machine may be high, and maintenance requirements may increase the overall cost of ownership.
- Noise and vibration: Especially for mechanical press machines, significant noise and vibration may be generated during operation, which may require additional measures to be taken to mitigate.
- Limitations of complex geometry: Although press machines have diverse functions, they may be difficult to handle extremely complex geometric shapes or parts that require multiple operations.
- Safety risks and requirements: punch press machines pose safety hazards to operators, and strict safety measures must be taken to prevent accidents from occurring.
- Dependence on skilled labor: Operating and maintaining punching machines requires skilled labor, especially for advanced CNC and servo drive press machine.
Application of Punch Press Machines
Punching press machines are multifunctional tools used in various industries. Their ability to efficiently produce high-precision parts makes them invaluable in modern manufacturing.
Sheet Metal Processing
The sheet metal processing industry is one of the largest users of punch press machines. Sheet metal manufacturing involves cutting, bending, and forming metal plates into various components and products. Punching machines are used to manufacture holes, slots, notches, and other features on metal plates, typically as part of large-scale assembly processes.
Common products manufactured:
- Automotive components: body panels, brackets, and structural parts.
- Electrical components: the shells, frames, and internal components of refrigerators, washing machines, and other electrical appliances.
- HVAC components: piping systems, ventilation openings, and other heating, ventilation, and air conditioning components.
- Electrical enclosure: cabinets and enclosures for electrical and electronic equipment.
Application Of Punch And Press Machines In Automotive Parts Manufacturing
The automotive industry heavily relies on press machines to mass produce various metal components. These machines are used to produce the following parts:
- Body panels: doors, hood, mudguards, and other external panels.
- Structural components: chassis parts, brackets, and reinforcements.
- Internal components: dashboard frame, seat bracket, and other internal metal parts.
Specific Applications in Automotive Production:
- Cutting: Cutting large pieces of metal into smaller billets for further processing.
- Perforation: Create holes and slots on the body panels and other parts.
- Forming: Forming metal plates into complex three-dimensional parts.
Precision Component Manufacturing For Aerospace Industry
The aerospace industry requires highly precise and reliable components, many of which are produced using press machines. These machines are used to manufacture parts for aircraft, spacecraft, and other aerospace applications.
Special precautions in aerospace stamping:
- Material selection: Aerospace components are typically made of high-strength, lightweight materials such as aluminum, titanium, and advanced composite materials.
- Precision tolerance: Aerospace parts must meet strict tolerance and quality standards, requiring precision pressand careful inspection.
Electronic Component Production Project
Press machines are widely used in the production of electronic components, including:
- Circuit board frame: A metal frame used to secure and protect printed circuit boards (PCBs).
- Connectors: Metal connectors used in various electronic devices.
- Shell: The metal casing of electronic devices, such as computers, servers, and communication equipment.
The electronics industry requires high-precision punch press to create complex patterns and features in metal parts. CNC press machines are particularly suitable for this task as they can produce complex shapes with consistent precision.
Manufacturing Of Structural Components In The Construction Industry
In the construction industry, press machines are used to produce various structural components, such as:
- Steel beams and columns: structural elements used in buildings, bridges, and other infrastructure.
- Strengthening plate: A plate used to strengthen the connections between structural components.
- Bracket and support: Metal brackets and supports used in construction projects.
Application in construction and infrastructure projects
- Building frame: Punching pressmachines are used to create components for steel and concrete building frames.
- Bridge: The structural components of a bridge, including main beams, supports, and reinforcing plates.
- Infrastructure: Components of infrastructure projects, such as tunnels, pipelines, and power plants.
Customized Manufacturing
Punch press machines are also used for custom metal manufacturing, producing unique custom parts for various applications. These machines are highly valued for their versatility and ability to handle small batch production with high precision.
Types of Punching Press Machines
There are various types of punch press machines, each designed to meet specific manufacturing needs. The main types include mechanical, hydraulic, servo driven, and CNC press machines. Each type has its unique characteristics, advantages, and applications.
Mechanical Press Punch Machine
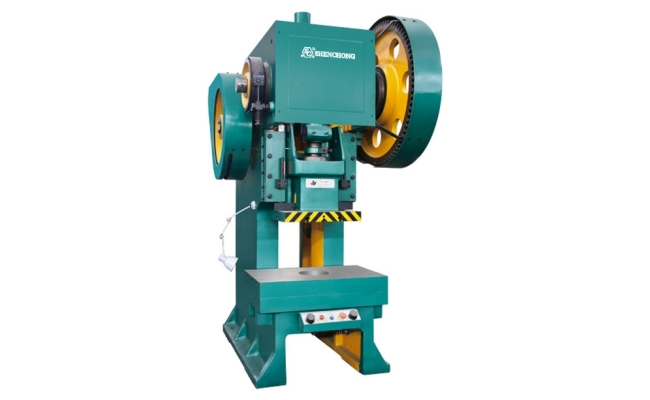
Mechanical punching machines use flywheels to operate, which store rotational energy and transmit it to the punch through a crankshaft or eccentric mechanism. Energy is released in a controlled manner to drive the punch through the material. The characteristic of mechanical punch machines is high-speed operation, which is very suitable for tasks that require repetitive and large-scale production.
Mechanical punch machines are commonly used in industries where speed is crucial, such as automotive manufacturing, where they produce components such as brackets, panels, and various structural parts. They are also used in the production of household appliances, electronic casings, and other metal products that require high-speed punching.
Advantages Of Mechanical Punching Machines:
- Fast production speed.
- The structure and operation are relatively simple.
- High cost-effectiveness, suitable for large-scale production.
Disadvantages Of Mechanical Punching Machines:
- Limited ability to handle thick or hard materials.
- Higher noise level and vibration.
- Low flexibility in stroke length and force control.
Hydraulic Press Machine
Hydraulic press machines use hydraulic oil to generate force. The press is composed of a hydraulic cylinder and a piston, and fluid is pumped into the hydraulic cylinder to move the piston and apply force to the punch. Hydraulic systems allow for precise control of impulse force and speed, making them suitable for various materials and applications.
Hydraulic punching press machines are used in industries that require more controllable and precise punching operations. They are very suitable for tasks involving thicker materials, complex shapes, or situations where different levels of force are required at different stages of the stamping process. Common applications include heavy vehicle components, aerospace components, and large structural components in buildings.
Advantages Of Hydraulic Press Machine:
- Greater combat power and flexibility.
- Suitable for various materials, including thick and hard metals.
- Compared to mechanical presses, it operates quietly.
Disadvantages Of Hydraulic Press Machine:
- Compared to mechanical presses, the operating speed is slower.
- Hydraulic components result in higher maintenance requirements.
- Higher purchase and maintenance costs.
Servo Punch Press Machine
Servo driven press machines combine the advantages of mechanical and hydraulic systems with advanced servo motor technology. The servo motor controls the movement of the punch with high precision, allowing for variable stroke length, speed, and force. This flexibility makes servo punch press machines an ideal choice for tasks that require high precision and customization.
Servo driven punch press machines are used in industries that require precise control of the press process, such as electronics, aerospace, and medical device manufacturing. They are particularly suitable for producing small and complex parts with strict tolerances.
Advantages Of Servo Punch Press Machine:
- High precision and flexibility.
- Energy saving operation.
- Low noise and vibration levels.
Disadvantages Of Servo Punch Press Machine:
- The initial cost is relatively high.
- Requires skilled operators and maintenance personnel.
- For simplerhigh-capacity tasks, it may not be necessary.
CNC Punch Press Machine
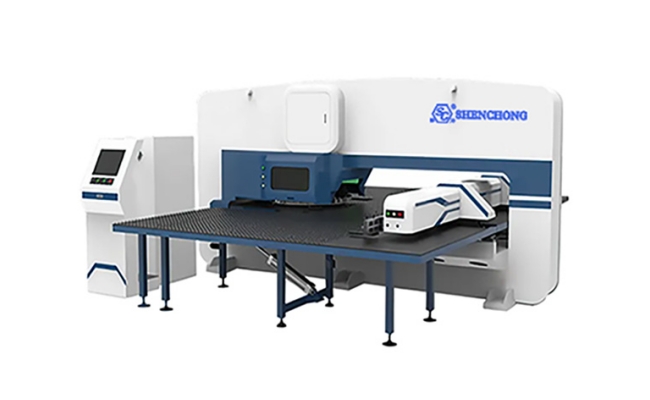
CNC (Computer Numerical Control) punching machines represent the pinnacle of automation and precision in stamping technology. These machines are controlled by a computer program that guides the movement of the punch and mold, allowing for the creation of complex shapes and patterns with minimal human intervention. CNC punching press machines can perform multiple operations in one setup, greatly reducing production time.
CNC press machines are used in industries that require high precision and complex design, such as aerospace, automotive, electronics, and custom metal manufacturing. They are capable of producing complex parts of consistent quality, making them an ideal choice for small batch prototypes and large-scale production.
Advantages of CNC Press Machine:
- High precision and repeatability.
- Capable of performing complex operations with minimal settings.
- Reduce labor costs and improve efficiency.
Disadvantages of CNC Press Machine:
- High initial investment and maintenance costs.
- Professional programming and operational skills are required.
- For simple or low capacity tasks, this may be redundant.
Key Components Of Punch Press Machine
Understanding the key components of a stamping machine is crucial for mastering its operation and maintenance. Each component plays a crucial role in ensuring the correct and efficient operation of the machine.
Frame
The frame is the pillar of the press machine, providing structural support and stability. It must be strong enough to withstand the forces generated during the punching and press process without deforming. The frame is usually made of heavy-duty steel or cast iron, designed to minimize vibration and ensure precise stamping.
Ram (sliding)
A ram, also known as a slider, is a part of a punch press machine used to fix and move the punch. The movement of the ram is guided by the driving mechanism of the machine, which provides the force required to push the punch into the metal sheets. The accuracy and stability of the ram movement is crucial for maintaining the precision of the press process.
Punch And Molds
The mold set consists of two parts: the punch and the mold. The punch is connected to the punch and moves downwards into the mold installed on the press base. The material to be stamped is placed between the punch and the mold, and when the punch descends, it will shear the material to form the desired shape. The design of the mold group determines the shape and size of the punching or features.
Drive Mechanism
The driving mechanism is responsible for converting input energy (from motors, hydraulic pumps, or servo systems) into mechanical force to drive the punch. According to the type of punch press machine, the driving mechanism may include a flywheel (mechanical press), a hydraulic cylinder (hydraulic press), or a servo motor (servo driven press). The efficiency and reliability of the driving mechanism are key factors affecting the performance of the punching machine.
Control System
The control system controls the operation of the stamping machine to ensure that it operates according to the required parameters. In CNC stamping machines, the control system includes a computer that runs a program to control the movement of the punch, mold, and material handling system. For mechanical and hydraulic presses, the control system may include timers, sensors, and relays that coordinate machine operation.
Security Mechanism
Safety is a key consideration in the press machines operation, and machines are equipped with various safety mechanisms to protect operators and prevent accidents from occurring. These may include:
- Protective devices and barriers: physical barriers that prevent entry into the punch and mold areas during operation.
- Emergency stop button: a button that immediately stops the operation of the machine in an emergency situation.
- Light curtain: an optional configurationthat detects when an object (such as a hand) enters a dangerous area and automatically stops the machine.
- Dual hand control: a safety designthat requires the operator to start the machine with both hands to prevent accidental start-up.
Progress And Innovation In Stamping Technology
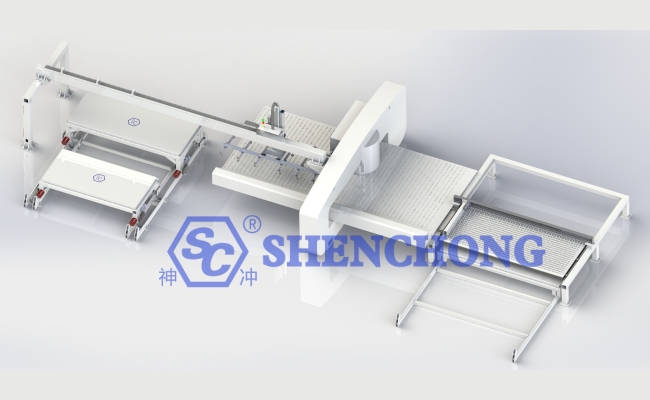
In recent years, the stamping machine industry has made significant progress and innovation:
Introduction To Numerical Control And Automation
The emergence of numerical control technology has completely changed punch press machines, achieving higher precision, automation, and flexibility. CNC punching press machines can produce complex shapes with minimal human intervention, reducing labor costs and improving efficiency.
Progress in Materials and Mold Technology
New materials and mold technology have improved the durability and performance of machines. Advanced tool steel and coatings extend the lifespan of punches and molds, while new mold designs improve operations to become more complex and precise.
Intelligent Automatic Manufacturing
Punch press machines are increasingly integrated with intelligent manufacturing systems and the Internet of Things (IoT). This allows for real-time monitoring of machine performance, predictive maintenance, and improved quality control. SC Machinery is a professional punch press automatic production line manufacturer, please feel free to contact with us to get the automation solutions.
Energy Efficiency And Sustainability
Manufacturers are developing more energy-efficient punch press machines to reduce the environmental impact of their manufacturing operations. Especially servo driven presses can significantly save energy compared to traditional mechanical or hydraulic presses.
Future Trends And Forecasts
The future of punching press machine technology may further integrate with artificial intelligence and machine learning to achieve higher levels of automation and optimization. In addition, advances in materials science and additive manufacturing may bring new applications and capabilities to press machines.
What Are The Alternative Machines?
Press Brake Machine
Compared with punch press machine can cut and form different shapes, press brake machine can only bend angles. Press brake focus on forming different angles and can be more flexible to form sheet metals.
Stamping Press
While punch presses are ideal for producing larger quantities of intricate designs, stamping presses are better suited for massive production of simpler parts.
Conclusion
Press machines are a key component of modern metal manufacturing, offering a range of benefits from high efficiency and precision to multi-functionality and cost-effectiveness. Although they do have some limitations, technological advancements are constantly expanding their functionality and applications. Different types of punch press machines: mechanical, hydraulic, servo driven, and CNC press machines have their unique advantages and are suitable for different applications.
With the continuous advancement of automation, artificial intelligence, materials science, and energy efficiency, these developments will further enhance the capabilities of punch press machines, making them an indispensable part of modern manufacturing. It is crucial for equipment operators and buyers to understand the latest developments in press machine technology. Investing in machines, training technicians, and adopting best practices will ensure that machine users can leverage the advantages of stamping machines and maintain a competitive edge in the global market.
SC Machinery provides all types of punch press machines and sheet metal automatic production line solutions to help solve the different forming problems. Welcome to contact with us and we are willing to provide the technical proposal based on your needs.