Table of Contents
Press brake VS punch press, they are commonly used equipment in the metal processing industry. Although they are both used for processing metal sheets, their functions and uses are different. The following is a detailed comparison and analysis of press brake and punch press.
1. Difference between definition and function
Press brake:
- Function:
Used to bend metal sheets into specific angles or shapes (such as right angles, U-shaped, V-shaped, etc.).
- Application:
Widely used in sheet metal processing, metal structure manufacturing, automobile, aerospace and other industries.
- Features:
Metal sheet bending is achieved through the cooperation of upper and lower molds.
High precision, suitable for complex shapes and multi-angle bending.
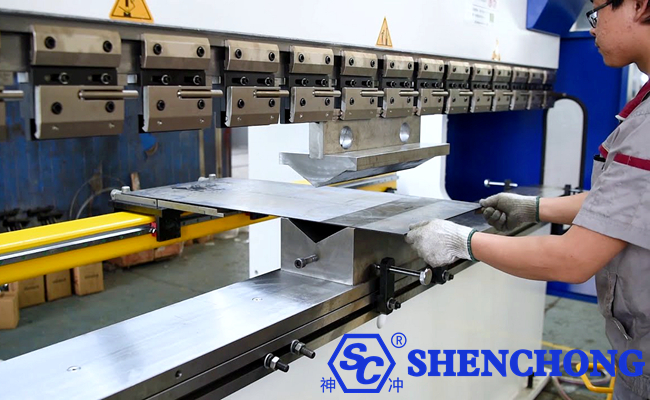
Punch press:
- Function:
Use stamping molds to punch, shear, blank, stretch, bend and other processing on metal sheets.
- Application:
Mainly used for mass production of metal parts processing, such as auto parts, home appliance housings, etc.
- Features:
Fast processing speed, suitable for mass production.
Various types of molds, wide range of applications.
Comparison Table: Press Brake VS Punch Press brake Definition And Functions:
Category | Bending machine | Punch press |
Definition | Equipment used to bend metal sheets into specific angles or shapes. | Equipment used for punching, cutting, blanking, stretching and other processing of metal sheets. |
Core functions | It can achieve precise bending of sheets and is suitable for processing multiple angles and complex shapes. | Quickly complete the punching, cutting and forming of sheets, suitable for mass production. |
2. Differences in working principles
Press brake:
Working principle:
Through hydraulic or mechanical drive, the upper die presses the sheet downward to form a bending angle with the lower die.
- Control method:
Manual bending machine: suitable for simple processing.
CNC press brake: The bending angle and position are controlled by the CNC system, with high precision, suitable for complex processing.
Punching machine:
- Working principle:
The metal sheet and the die are formed by quickly pressing down the punch.
- Drive method:
Mechanical punching machine: The punch is driven by a mechanical connecting rod.
Hydraulic punching machine: The punch is driven by a hydraulic system.
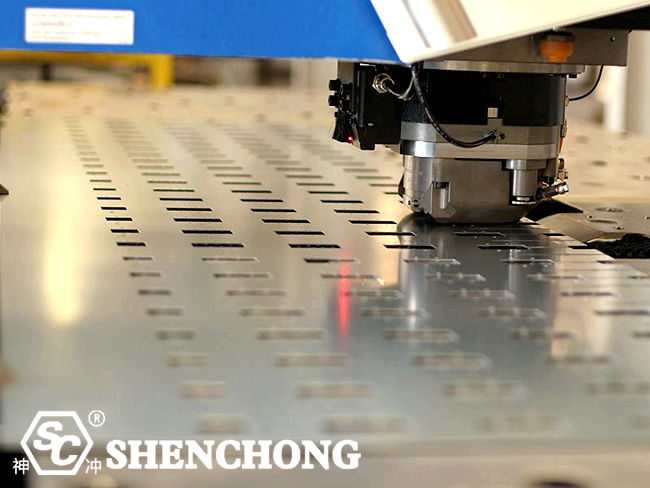
Working principle comparison table:
Press Brake | Punch Press |
The upper die applies downward pressure and cooperates with the lower die to bend the metal sheet into the desired angle or shape. | The punch presses down quickly and cooperates with the die to punch, shear or form metal sheets. |
Comparison table of drive modes:
item | Press Brake | Punch Press |
Driving method | Hydraulic, mechanical or CNC. | Mechanical or hydraulic drive. |
Operation mode | CNC operation is more precise and supports automated production. | Operation is simple and efficient after the mold is fixed. |
3. Comparison of processing characteristics between press brake and punch press
Press brake:
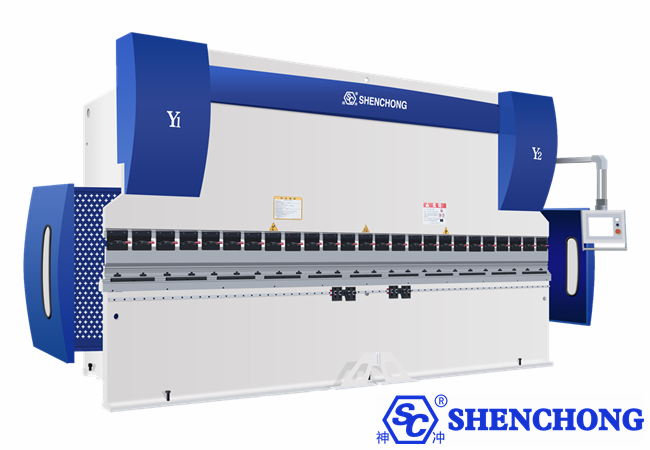
Advantages:
- High bending accuracy.
- Strong flexibility, suitable for processing of various shapes.
- Small damage to the surface quality of the plate.
Disadvantages:
- Slow processing speed.
- Not suitable for mass production.
Punch press:

Advantages:
- Fast processing speed, suitable for mass production.
- One punching can complete multiple processes (such as punching and forming).
Disadvantages:
- High mold cost.
- May cause certain damage to the surface of the plate.
Processing characteristics comparison table:
Features | Press Brake | Punch Press |
Processing accuracy | High precision, suitable for complex bending and multi-angle processing. | The precision is high, but it mainly depends on the mold accuracy. |
Flexibility | High flexibility, can process workpieces of various shapes and angles. | The flexibility is low, suitable for processing workpieces with fixed shapes. |
Production efficiency | Medium, suitable for small and medium batch production. | High, suitable for mass production. |
Processing range | Mainly used for bending processing of plates. | It can be used for punching, shearing, blanking, stretching and other processes. |
Surface quality | Little damage to the surface of the plate. | The surface of the sheet may be scratched or indented due to stamping. |
4. Scope of application: press brake vs punch press
Press brake:
Small batch, diversified production.
High-precision sheet metal processing.
Products that require multi-angle bending or complex shapes.
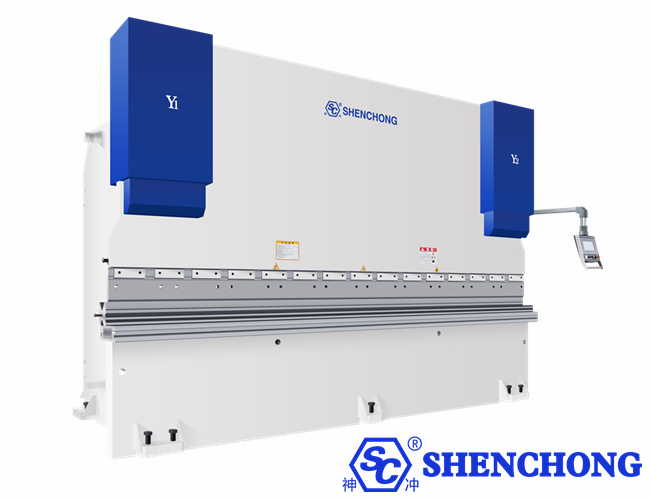
Punching press:
Massive production of metal parts.
The product shape is relatively fixed and has strong repeatability.
Suitable for punching, shearing, stretching and other processing.
Application scenario comparison:
Item | Press brake | Punch press |
Applicable scene | Small and medium batch, diversified, customized processing. | Large-volume, fixed-shape parts processing. |
Typical Application | Sheet metal processing, metal structural parts, aerospace, home appliance housing, etc. | Auto parts, punching parts, metal accessories for home appliances, etc. |
Mold cost comparison table:
Item | Press brake | Punch press |
Mold complexity | The mold is simple and low cost. | The mold is complex and the manufacturing cost is high. |
Mold replacement difficulty | It is easy to replace and suitable for small batch and multi-variety production. | It is complex to replace and is suitable for fixed batch production. |
5. How to choose?
Choose a press brake machine:
If high-precision bending is required.
The product has a complex shape and requires multi-angle processing.
The production batch is small and the product variety is large.
Suitable for sheet metal processing and customized parts manufacturing.
If large-scale production is required.
The product shape is fixed and the processing process is single or simple.
High processing speed requirements.
Advantages and disadvantages comparison table:
Item | Press brake | Punch press |
Advantages | High processing precision, suitable for complex shape processing. | High production efficiency, suitable for mass production. |
Strong flexibility, suitable for multi-variety small batch production. | There are many types of molds with various functions. | |
Disadvantages | The processing speed is slow and not suitable for mass production. | The mold cost is high and the flexibility is low. |
It requires high operating skills. | It may cause some damage to the surface of the plate. |
6. Conclusion
Press brake: high precision, strong flexibility, suitable for complex shapes and small and medium batch production.
Punch press: high efficiency, suitable for mass production, wide application range but low flexibility.
In summary, bending machine and punching machine have their own focus in metal processing, and the choice of which equipment needs to be determined according to specific production needs and processing requirements.
More other equipment comparison articles:
Hydraulic Press Brakes VS Hybrid Servo Press Brakes