Table of Contents
The composition of the plate rolling machine is mainly composed of multiple core components, which work together to achieve the bending process of metal plates. The following are the main plate rolling machine components and their functional descriptions.
1. Roller system
The roller system of the plate rolling machine is an important component of the plate rolling machine, responsible for carrying and transmitting various torques and pressures. The plate rolling machine is generally used to deform metal plates (such as steel plates, aluminum plates, etc.) into the required curved surface or circular structure through rolling. The function and structure of its roller system are crucial to the performance and efficiency of the machine.
Composition of the roller system of the plate rolling machine
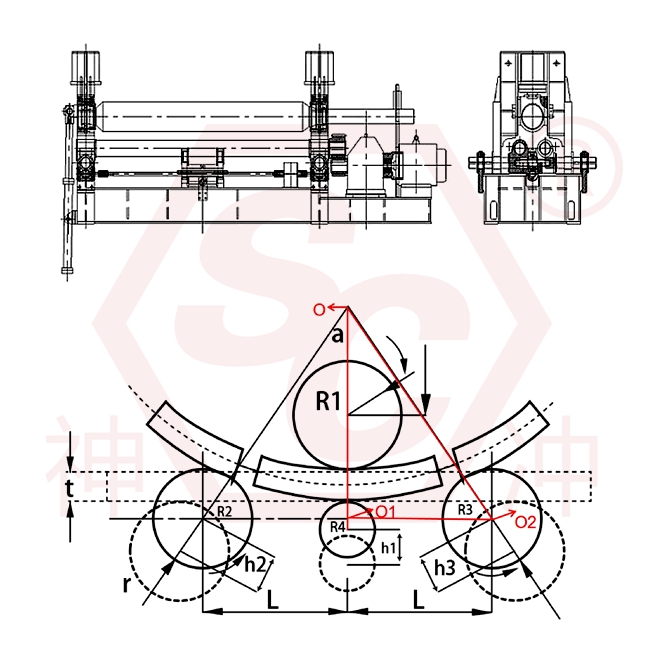
The roller system of the plate rolling machine mainly includes the following parts:
- Roller (or roller): usually made of high-strength material, plays the role of directly clamping and bending the plate. The size and shape of the roller need to be designed according to the thickness and width of the plate.
- Support bearing: bearings are usually set at both ends of the roller to support the rotation of the roller and ensure the precise docking between the roller and the frame.
- Drive device: including motors, reducers, etc., which provide power to the roller through a belt or gear transmission system to control its rotation speed and direction.
- Pressure system: Provide roller pressure through hydraulic or mechanical means to ensure that the sheet can enter the roller smoothly and undergo appropriate rolling.
- Adjustment device: In order to adapt to sheets of different thicknesses, the roller system often needs to have an adjustment device to adjust the gap and angle between the rollers.
- Safety device: In order to prevent abnormal conditions during operation, the roller system is usually equipped with safety devices, such as overload protection, temperature control system, etc.
Key technical parameters
- Material and hardness of rollers: need to meet certain strength and wear resistance requirements to ensure long-term stable operation of rollers.
- Adjustment accuracy: The adjustment accuracy of the roller system directly affects the effect of plate rolling and the quality of the product.
- Drive mode and power transmission: select the appropriate drive device and transmission system to ensure stability and adjustability during operation.
Common types of plate rolling machines
Three-roller and four-roller, etc. Different types of roller systems have slightly different designs to meet different production needs.
2. Drive system
The drive system of the plate rolling machine is a key component to ensure that the machine can roll smoothly and stably. Its main task is to provide power, control the movement of the roller shaft, and ensure the synchronization, accuracy and adjustability of the pressure between the roller shafts. The drive system of the plate rolling machine involves multiple parts, usually including motors, reducers, transmission devices, couplings, control systems, etc.
Composition of the plate rolling machine drive system
The plate rolling machine main components in drive system:
1) Motor
The motor is the core part of the drive system and provides the main power source.
Common types of motors are:
- AC motor (AC): has good stability and economy, suitable for most conventional plate rolling machines.
- DC motor (DC): due to its strong speed adjustability, it is used more in applications that require precise speed control.
- Variable frequency motor: used with a frequency converter, the speed of the motor can be adjusted as needed to provide more precise speed control.
2) Reducer
The function of the reducer is to reduce the speed of the motor and increase the output torque so that the roller shaft runs at a suitable speed. It is usually connected to an electric motor.
Common reducers include:
- Gear reducer: provides a large output torque and is suitable for high-load working environments.
- Worm gear reducer: suitable for occasions requiring a large reduction ratio and has a relatively compact structure.
- Planetary reducer: provides high efficiency and precise control, suitable for systems with high speed and torque requirements.
3) Transmission device
The transmission device is responsible for transmitting the power output by the reducer to the roller shaft.
Common transmission methods include:
- Gear transmission: Gear transmission is widely used in many large plate rolling machines and has high efficiency and load-bearing capacity.
- Chain transmission: suitable for small or medium-sized plate rolling machines and has a certain impact resistance.
- Belt transmission: commonly used in low-power machines, with good flexibility and buffering effect.
4) Coupling
The coupling is used to connect the drive device to the transmission shaft of the roller system to ensure the stability of rotation.
Common types of couplings include:
- Elastic coupling: has good shock absorption and buffering effects, and can reduce system vibration.
- Rigid coupling: suitable for applications with high precision requirements, which can ensure the synchronization of the transmission system.
- Universal coupling: suitable for systems that need to transmit power at a large angle.
5) Control system
The control system plays a vital role in the drive system of the plate rolling machine. It determines the control parameters such as the speed, direction and pressure of the roller.
Common control methods include:
- PLC control system: a system based on a programmable logic controller (PLC), which has a high level of automation and can realize complex control logic.
- Inverter: in conjunction with the motor, it can adjust the motor speed by adjusting the frequency, thereby controlling the speed of the roller.
- Hydraulic control system: used to adjust the pressure between the rollers to ensure the processing quality of the material.
6) Safety protection system
In order to ensure the safety of the plate rolling machine during operation, some safety protection devices are usually equipped, such as:
- Overload protection device: when the load exceeds the load range of the equipment, it will automatically stop working to avoid damage to the equipment.
- Temperature sensor: monitors the temperature of the motor and reducer to avoid overheating.
- Emergency stop device: in the event of a fault or dangerous situation, the power can be cut off immediately to ensure the safety of the operator.
Working principle of the drive system
The motor reduces the speed through the reducer and provides sufficient torque.
Transmission devices (such as gears, chains, belts) transmit power to the rollers.
The coupling effectively connects the power to ensure smooth operation of the rollers.
The control system monitors and adjusts various parameters, such as roller speed, pressure, etc., to ensure the working accuracy and efficiency of the plate rolling machine.
Common drive system types
Single motor drive: suitable for small plate rolling machines or low-load applications.
Dual motor drive: used for medium and large plate rolling machines that require greater power and stability, and better power distribution is achieved through two motors.
Hydraulic drive: commonly used in heavy plate rolling machines, the hydraulic system can provide strong power output.
Key technical requirements
- requirements of the plate rolling machine to avoid insufficient power or overload.
- Speed range: The speed range of the drive system should be able to cover the needs of the plate rolling machine under different working conditions.
- Synchronicity: Especially in multi-roller systems, the synchronization between rollers is particularly important to ensure a smooth and efficient working process.
The design and selection of the plate rolling machine drive system directly affects the working efficiency, performance and service life of the plate rolling machine. Therefore, when selecting the system, comprehensive consideration should be given to the specific application requirements, processing materials and production environment.
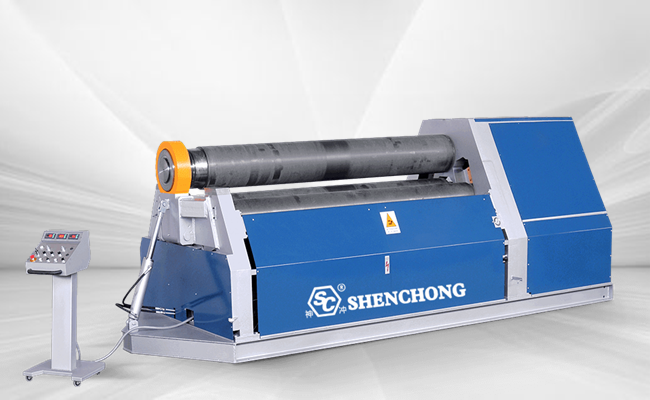
3. Hydraulic system
The hydraulic system of the plate rolling machine is an important part of the plate rolling machine, which is mainly responsible for adjusting and controlling the pressure of the rollers, the gap between the rollers, and the precise adjustment during operation. The hydraulic system can provide strong power to support the plate rolling machine to complete the high-pressure forming and bending operations of the metal sheet.
The role of the hydraulic system
The main role of the hydraulic system in the plate rolling machine includes:
- Adjusting the pressure between the rollers: ensuring that the plate can enter smoothly when passing through the rollers and perform precise bending processing.
- Adjusting the gap between the rollers: Plates of different thicknesses need to be adjusted by adjusting the gap between the rollers to meet the processing requirements. The hydraulic system can accurately control according to different thicknesses.
- Precise control of pressure and torque: The hydraulic system can provide higher pressure and can be adjusted very accurately to meet the different processing requirements of various materials.
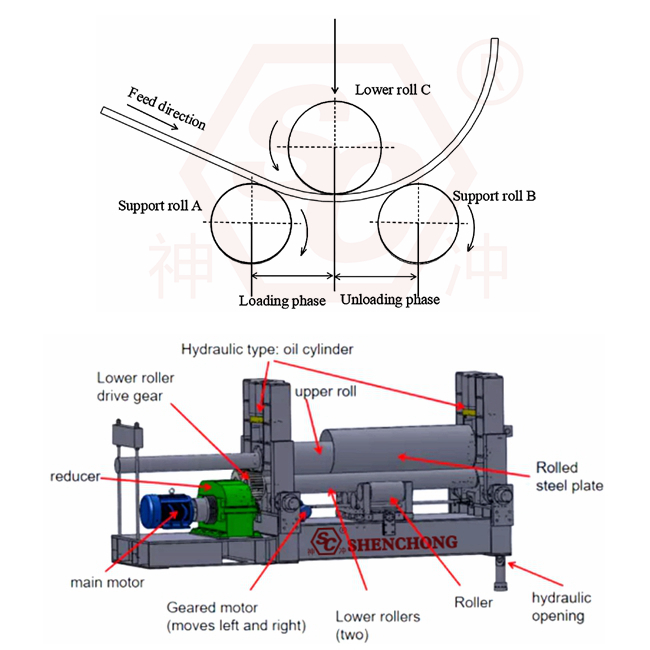
Composition of the hydraulic system of the plate rolling machine
The main components of the hydraulic system of the plate rolling machine:
1) Hydraulic pump
- Function:
The hydraulic pump is the core part of the hydraulic system, responsible for providing power for the flow of hydraulic oil and ensuring that the hydraulic oil in the system can effectively transmit pressure.
- Type:
Common hydraulic pumps include gear pumps, vane pumps, plunger pumps, etc. Different types of pumps are adapted to different working pressures and flow requirements.
2) Hydraulic cylinder
- Function:
The hydraulic cylinder is an actuator in the hydraulic system, which is used to convert hydraulic energy into mechanical energy and perform tasks such as roller pressure adjustment and roller clearance adjustment.
- Structure:
The hydraulic cylinder consists of a cylinder body, a piston, a piston rod, a seal, etc. When the hydraulic oil enters the hydraulic cylinder, it pushes the piston to move linearly, thereby driving the roller or other components to move accordingly.
3) Hydraulic valve
- Function:
The hydraulic valve is used to control the flow direction, flow rate and pressure of the hydraulic oil. It is an important control element in the hydraulic system to ensure that the system can provide the correct pressure and flow rate as required.
- Type:
Common hydraulic valves include one-way valves, overflow valves, throttle valves, pressure regulating valves, reversing valves, etc. These valves help regulate the flow of hydraulic oil and ensure stable operation of the system.
4) Hydraulic oil tank
- Function:
The hydraulic oil tank is used to store hydraulic oil and provide cooling and filtration of the oil. The oil tank is usually designed with ventilation devices, oil level detection devices, filtering systems, etc. to ensure the cleanliness and normal operation of the hydraulic system.
- Hydraulic oil:
The selection of hydraulic oil is crucial and must have good lubricity, corrosion resistance, high temperature resistance and other characteristics.
5) Hydraulic pipeline system
- Function:
The hydraulic pipeline connects various components such as hydraulic pumps, hydraulic cylinders, hydraulic valves, etc. to ensure that the hydraulic oil can flow smoothly.
- Pipeline design:
Factors such as the flow resistance of hydraulic oil, the pressure resistance of pipelines and the risk of leakage should be considered during design.
6) Hydraulic control system
- Function:
The hydraulic control system is responsible for controlling the action of hydraulic components. It is usually used in conjunction with PLC (programmable logic controller) or dedicated hydraulic controller to accurately adjust hydraulic parameters through the automation system.
- Features:
Modern plate rolling machines are usually equipped with digital control systems, which can realize the refined management and adjustment of hydraulic systems and provide efficient and precise operation.
Working principle of plate rolling machine hydraulic system
The hydraulic oil is sucked in and pressurized by the hydraulic pump, and the pump delivers the hydraulic oil to various components of the system, such as hydraulic cylinders and hydraulic valves.
The hydraulic valve adjusts the flow, direction and pressure of the hydraulic oil according to the needs of the system to ensure that the hydraulic oil can be effectively transferred to the actuator (such as the hydraulic cylinder) for precise operation.
The hydraulic cylinder produces linear motion under the action of the hydraulic oil, such as adjusting the pressure between the rollers or adjusting the gap between the rollers. The hydraulic system can accurately adjust the pressure and position according to the thickness of the plate and the processing requirements.
After completing the task, the hydraulic oil returns to the tank, and the temperature and oil level in the system are monitored to ensure the stability of the hydraulic system.
Common types of hydraulic systems
Single-acting hydraulic cylinder system:
Suitable for occasions where only one direction is required to generate force, common in simple roller adjustment and pressure control.
Double-acting hydraulic cylinder system:
Can generate force in both directions, suitable for occasions that require precise adjustment and two-way control, widely used in roller adjustment and pressure adjustment of plate rolling machines.
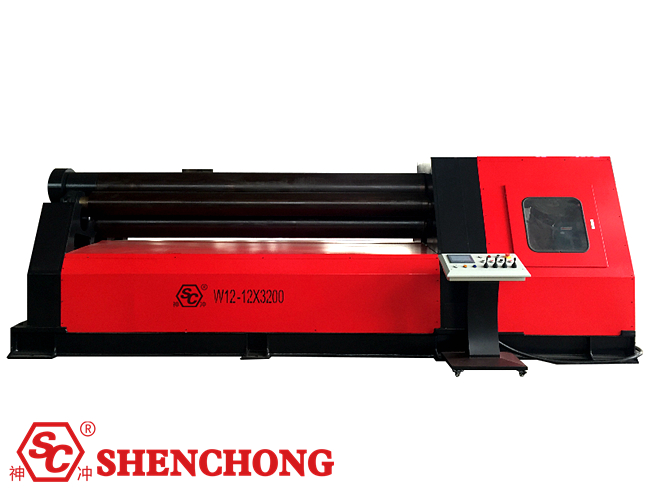
Advantages of plate rolling machine hydraulic system
- High efficiency: The hydraulic system can provide a higher power density and can provide sufficient power in a smaller space.
- Precise control: The hydraulic system can control pressure, speed and position very accurately, and adapt to plates of different thicknesses and materials.
- Quick response: The hydraulic system has a fast response speed and can quickly adjust the pressure and clearance of the rollers to improve production efficiency.
- High reliability: The hydraulic system has a simple structure, stable operation, and usually has a strong load capacity.
Maintenance and precautions of the hydraulic system
- Selection of hydraulic oil: Make sure to use the appropriate hydraulic oil and check the quality of the oil regularly to avoid oil contamination or deterioration.
- Regularly check the oil circuit: Check the pipeline, valves and connectors to avoid leakage and blockage to ensure the efficient operation of the system.
- Check the working status of the hydraulic cylinder and pump: Regularly check the sealing of the hydraulic cylinder and the working condition of the hydraulic pump, and repair or replace the faulty parts in time.
The role of the hydraulic system in the plate rolling machine is crucial. It not only affects the working performance of the machine, but also has a direct impact on production efficiency and product quality.
4. Control system
The control system is the core of the plate rolling machine, which is used to adjust the movement and working state of each component.
According to the degree of automation, the control system is divided into:
- Manual control: directly adjust the roller position and pressure through a mechanical handle or button.
- Semi-automatic control: equipped with a simple electronic control device, which can preset some parameters.
- CNC system (CNC): programmable control, automatic operation is achieved by inputting parameters (such as plate thickness, bending radius), suitable for processing complex shapes.
5. Frame and base
The frame and base are the main supporting structure of the plate rolling machine to ensure the stability and precision of the equipment. Its features include:
- High-strength design: usually cast steel or welded steel structure, which can withstand high loads.
- Good rigidity: reduce vibration and deformation during equipment operation.
- Stable base: provide installation and fixing foundation for equipment.
6. Feeding and unloading device
The feeding and unloading device is used to assist the loading of plates and the removal of finished products, reduce manual operations and improve efficiency.
- Feeding device: includes a conveyor belt or roller to facilitate the feeding of plates into the plate rolling machine.
- Unloading device: Some plate rolling machines are equipped with automatic unloading systems to facilitate the removal of finished products.
7. Limiting and correction devices
- Limiting device: used to control the position of the plate to prevent the plate from shifting during processing.
- Correction device: adjust the initial position of the plate to ensure bending accuracy.
8. Lubrication and cooling system
The lubrication and cooling system is used to protect the running parts of the equipment and extend its service life.
- Lubrication system: regularly provide lubricating oil to key components such as rollers and gears to reduce friction.
- Cooling system: dissipate heat through coolant or fan to prevent overheating of the hydraulic system and motor.
9. Safety protection device
In order to ensure the safety of operators and equipment, the plate rolling machine is equipped with a variety of protection devices, including:
- Emergency stop button: quickly stop the equipment in an emergency.
- Protective cover: covers dangerous parts to prevent operators from contacting.
- Overload protection: automatically shuts down when the equipment load exceeds the design range.
10. Additional functional devices
Depending on specific needs, the plate rolling machine may be equipped with some additional devices, such as:
- Conical rolling device: specially used for the processing of conical parts.
- Measuring system: real-time monitoring of the bending radius and shape of the plate.
- Automatic centering system: ensures that the plate is always centered during processing.

11. Summary
The plate rolling machine components mainly include roller system, drive system, hydraulic system, control system, frame and base, feeding and unloading device, as well as safety protection and lubrication and cooling system.
All parts work together to ensure that the equipment can efficiently and accurately complete the bending process of metal plates. Different types of plate rolling machines may differ in specific composition, but the basic principles and functions remain the same.
Related Articles About Rolling Machine:
- What Is Metal Plate Rolling Machine? Definition &Working Principle
- Top 12 Plate Rolling Machine Brands Ranking
- Introduction To Plate Rolling Machine Faults