Table of Contents
The relationship between laser welding speed, power, and material thickness is crucial for determining the quality and efficiency of the welding process. These three factors—welding speed, laser power, and the thickness of the material being welded—are interdependent and must be optimized to achieve strong, defect-free welds. Understanding how they interact is essential for industries like automotive, aerospace, and manufacturing, where precision and material integrity are paramount.
Laser Welding Machine Basic Introduction
Laser welding machines use high-energy laser pulses to locally heat materials in small areas, melting them through thermal conduction and achieving welding. Its working principle mainly involves the following aspects:
- Optical focusing: The laser welding machine uses the laser beam generated by the laser to focus the laser energy onto the welding point through optical components such as lenses or mirrors.
- Thermal conduction: When a laser beam is irradiated on the surface of a workpiece, the laser energy is absorbed and converted into thermal energy. Thermal energy is gradually transferred along the metal conductive part of the welded joint through thermal conduction, causing its temperature to rise.
- Melting and mixing: When the metal surface is subjected to sufficiently high temperatures, the metal begins to melt and form a molten pool. Under the action of the laser beam, the molten pool rapidly diffuses and mixes, achieving the connection of the metal joint.
- Cooling and solidification: After stopping the laser beam irradiation, the molten pool gradually cools and forms a welded joint during the solidification process. During the solidification process, metal molecules rearrange and crystallize, forming a strong welded connection.
Advantages Of Laser Welding Machines
- High precision: capable of achieving micron level welding accuracy, especially suitable for welding requirements of micro and complex structures.
- High speed: Especially in deep penetration welding mode, due to the concentration of laser energy, the molten pool is small and deep, resulting in fast welding speed and high production efficiency.
- Low deformation: Compared to traditional welding methods, laser welding has lower heat input and less impact on surrounding materials, which is beneficial for reducing deformation after welding.
- Small heat affected zone: can reduce thermal damage to surrounding materials and improve the quality of welded joints.
Laser Welding Power, Speed And Material Thickness
1. Laser Welding Power
Laser power is a critical factor in determining the depth of penetration and overall energy input into the material during the welding process. The power of the laser dictates the amount of heat available for melting the base metal and creating the weld pool. For thicker plates, higher laser power is generally required to achieve sufficient penetration, while for thinner materials, lower power can prevent excessive melting or burn-through.
- Higher Power: Enables deeper penetration, making it suitable for welding thicker materials. However, too much power on thinner plates can cause defects like keyhole instability, spatter, or even burn-through.
- Lower Power: Works better with thinner plates, offering greater control and preventing excessive heat from deforming or melting the material.
The laser power must be carefully selected based on the material thickness to ensure proper fusion without defects.
2. Welding Speed
Welding speed refers to how fast the laser moves along the joint being welded. It influences the heat input per unit length and is critical in determining the weld quality. There is a direct relationship between welding speed and laser power, as increasing one often requires adjustments to the other to maintain the desired weld properties.
- Higher Welding Speed: Reduces the heat input per unit length of the weld, which can be beneficial for thin materials to avoid overheating and distortion. However, if the speed is too high for the given power, the weld may lack penetration, resulting in weak joints or incomplete fusion.
- Lower Welding Speed: Increases the heat input, leading to more melting of the base material and deeper penetration. This is advantageous for thicker plates but can lead to overheating or excessive molten metal flow in thin materials.
Using the optimal welding speed is essential to balance the heat input and avoid common welding defects like porosity, cracking, or distortion.
3. Material Thickness
The thickness of the material being welded plays a significant role in determining both the required power and the allowable welding speed. Thicker plates require more heat to achieve full penetration, meaning the laser must operate at higher power levels, and the welding speed may need to be reduced to allow sufficient time for heat absorption. Conversely, thinner plates require less power and higher speeds to avoid excess heat input, which could lead to melting or burn-through.
- Thicker Plates: Demand more energy to achieve full penetration. The laser must deliver higher power, and welding speed must be slower to allow sufficient energy transfer to the material.
- Thinner Plates: Require less energy, so the laser power can be reduced, and the welding speed increased. Thin materials are more prone to heat-related distortions, making precise control over these variables essential.
Interplay Between Power, Speed, and Thickness
The relationship between laser welding speed, power, and plate thickness is a balancing act. For each thickness of material, there is an optimal combination of laser power and welding speed that ensures a high-quality weld with the correct depth of penetration and minimal defects.
For example, if welding a thick steel plate, increasing laser power without adjusting the welding speed could result in excessive heat input, causing defects like warping or an overly wide weld bead. On the other hand, reducing the welding speed without increasing power may lead to an excessively deep weld, possibly overheating the material. For thin materials, too much power combined with slow welding speed can cause the material to melt excessively or burn through.
Relationship Between Laser Welding Speed And Plate Thickness
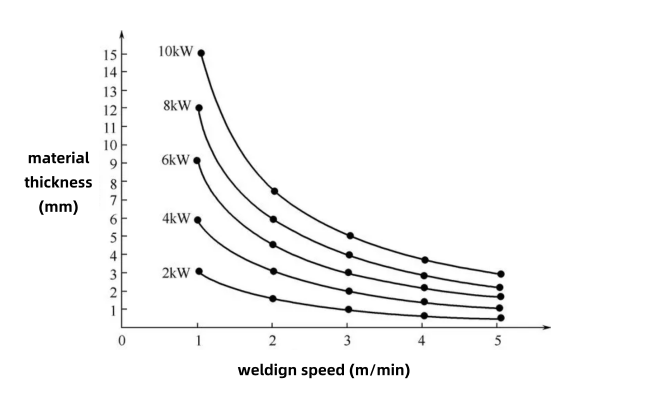
Thick Plates Require Slower Welding Speeds
When laser welding thicker plates, the material requires more heat to achieve complete penetration and good joint strength. Therefore, the welding speed must be reduced to allow sufficient time for the laser beam to transfer heat to the entire thickness of the material. If the welding speed is too fast, the laser energy cannot fully penetrate, which may lead to insufficient penetration depth, discontinuous welds, or insufficient joint strength.
- Thick plate (>6mm): The welding speed should be slow to ensure that the laser energy can fully penetrate the entire thickness of the plate, forming a stable and high-strength weld.
Thin Sheets Can Be Welded At A Faster Speed
Compared to thick plates, thin plate materials (<2mm) require less heat, making it easier for lasers to penetrate the entire thickness. At this point, a faster welding speed can effectively prevent the material from overheating or melting too much, avoiding welding deformation or burning through. In addition, higher welding speeds can also improve welding efficiency.
- Thin sheet metal (<2mm): The welding speed should be fast to reduce welding defects such as deformation and burn through caused by material overheating.
Influence Of Laser Power On Welding Speed And Plate Thickness
The laser power determines the energy input during the welding process, and high-power lasers can provide stronger heat, making them suitable for welding thicker materials; Low power lasers are more suitable for welding thinner materials. When selecting welding speed, the laser power and plate thickness must be matched to ensure sufficient penetration without causing material overheating.
High Power Laser Welding Of Thick Plates
When welding thicker plates, higher laser power is required to ensure sufficient heat transfer to the interior of the material, forming a stable molten pool. Combined with a slower welding speed, laser energy can uniformly heat the material over a longer period of time, ensuring penetration.
- 6kW power welding thick plate (10mm): The welding speed is usually between 0.5-1.2 m/min.
Low Power Laser Welding Of Thin Plates
In thin plate welding, lower power and faster speed help prevent overheating and weld deformation. Usually, when the laser power is within the range of 2-3kW, it can process plates with a thickness less than 2mm.
- 2kW power welding thin plate (1mm): The welding speed is usually between 5-10 m/min.
Comparison Chart Between Power And Speed Of Laser Welding Machine
The following is a comparison example of the power and welding speed of laser welding machines under different plate thickness conditions:
Material Thickness(mm) | Laser Power(kW) | Welding Speed(m/min) |
1.0 | 2.0 | 7.0 |
2.0 | 3.0 | 4.5 |
4.0 | 4.0 | 2.5 |
6.0 | 6.0 | 1.2 |
8.0 | 8.0 | 0.8 |
10.0 | 10.0 | 0.6 |
- Thin plate (1-2mm): The combination of low power (2-3kW) and high welding speed (5-10 m/min) is suitable for welding in this situation, ensuring fast operation without generating excessive heat.
- Medium thick plate (4-6mm): Medium power (4-6kW) combined with medium speed welding (1-3 m/min) can ensure penetration while avoiding excessive heat affected zone.
- Thick plate (>6mm): High power (8-10kW) combined with slow welding (0.5-1 m/min) is used for thick plates to ensure sufficient heat penetration into the material and form high-strength joints.
Laser Welding Power, Thickness & Speed Chart
Laser welding is a precision connection technology that can provide high-speed and high-quality welds for various metal thicknesses. The relationship between laser power, material thickness, and welding speed is crucial for achieving optimal results. This is a comprehensive chart that details these parameters of common materials.
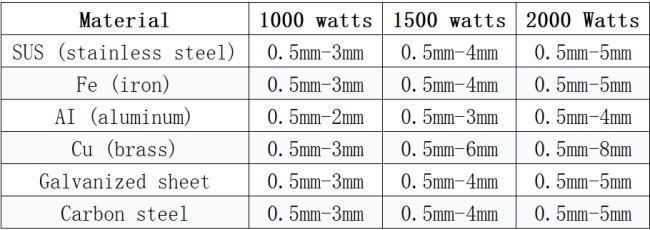
Mild Steel
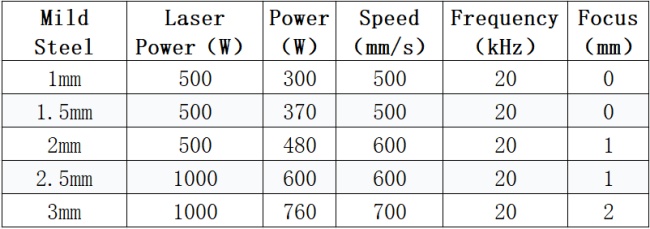
Stainless Steel
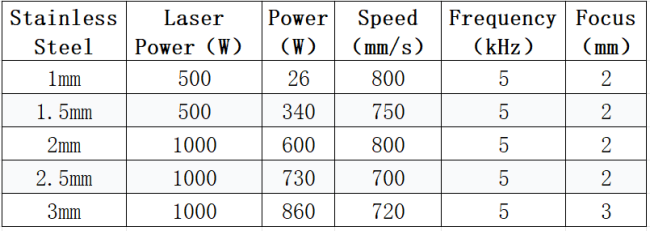
Aluminum
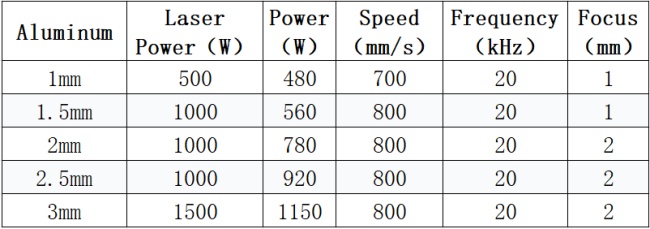
Copper
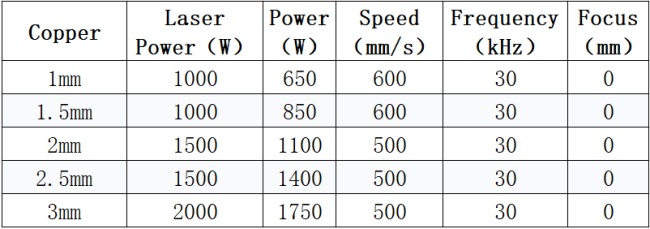
Brass
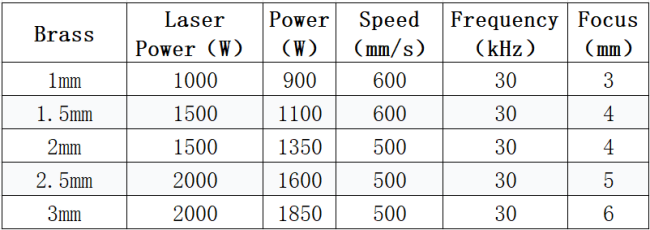
Galvanized Sheet

Conclusion
In summary, thicker plates generally require higher power and slower speeds, while thinner materials require lower power and faster welding speeds. This delicate balance ensures efficient energy use and high weld quality. Understanding the interplay between these variables allows manufacturers to optimize their processes for specific applications, materials, and thicknesses, resulting in stronger, more reliable welds with minimal defects.