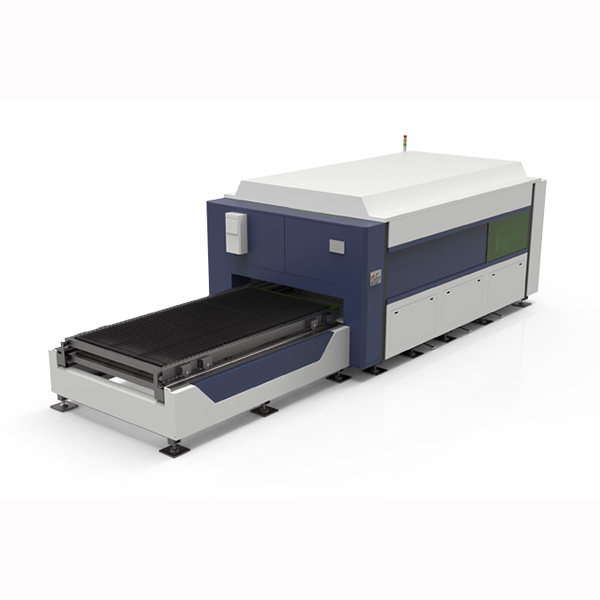
Laser welding machines adopt one of the most advanced welding technologies today. Laser welding uses high-energy laser pulses to locally heat materials in small areas. The energy radiated by the laser diffuses through the interior of the material through thermal conduction, melting the material and forming a specific molten pool. It is a new type of welding method mainly aimed at the welding of thin-walled materials and precision parts, which can achieve spot welding, butt welding, overlay welding, sealing welding, etc. It has a high aspect ratio, small weld width, small heat affected zone, small deformation, fast welding speed, smooth and beautiful weld, no or only simple processing after welding, high weld quality, no porosity, precise control, small focusing spot, high positioning accuracy, and easy automation.
Fiber laser welding is a highly advanced and versatile welding technique that offers unparalleled precision, speed, and cleanliness. With its ability to weld a wide variety of materials and unmatched speed, it is a cost-effective solution for small to large industrial applications.
laser welding offers a high degree of control over the welding process, allowing users to adjust welding parameters to suit their needs.
While a laser welding machine is more expensive to purchase than traditional welding methods, it offers high precision and consistency that can save money over time.
The laser welding process is very precise and is often used in applications where precision is critical, such as in the aerospace, automotive, and medical industries. Laser welding machines are versatile and can weld a variety of metals, including steel, aluminum, copper, and titanium. It can weld dissimilar materials, making it an excellent choice for joining dissimilar metals.
Handheld laser welding machine adopts fiber laser welding technology, a welding technology that creates a strong joint between several metal components with a fiber laser. This machine welds metal plates and metal tubes. Fiber laser produces a high-intensity beam concentrated into one spot. This concentrated heat source enables fine, deep welding with high welding speed.
SCHW laser welding machine is a high-configuration handheld fiber laser welding machine, including CW/pulse output mode, which can be used for welding stainless steel, iron, galvanized steel, and aluminum, and can completely change the standard argon arc welding and electric welding equipment. The advantages of the handheld laser welding machine are simple procedures, beautiful welding joints, fast welding speed, and no consumables.
1kw handheld lasr welder can weld 0.5-2mm steel
5kw handheld lasr welder can weld 0.5-3mm steel
2kw handheld lasr welder can weld 0.5-4mm steel, 0.5-3mm aluminum
The above data is based on the triangular light spot. Due to the plate and labor difference, please refer to the actual welding.
Model | SCHW-1000 | SCHW-1500 | SCHW-2000 | SCHW-3000 |
Laser Power | 1000W | 1500W | 2000W | 3000W |
Range of Adjustable Power | 1-100% | |||
Laser Wavelength | 1064nm | |||
Way of Workinging | Continuous/Modulation | |||
Speed Range | 0-120mm/s | |||
Repeat Precision | ±0.01mm | |||
Welding Gap Requirements | ≤0.5mm | |||
Cooling Water | Industrial thermostatic water tank |
The laser welding head is ergonomically designed, light in shape, comfortable to hold, and easy to control and operate. The hand-held welding head is easy to hold and can be operated at any angle, making welding more convenient and flexible.Operators can instantly switch between presets to accommodate many material thickness combinations.
SC Machinery provides high-performance, intuitive, and easy-to-use operating systems. It expands the tolerance range and weld width of machined parts and provides better weld formation results. The control system comes with a few modes: CW model and PWM model Arc model. The control screen directly digitally sets the parameters of the wire feeder. The system monitors the operating status in real-time and monitors and collects the active quality of the laser, chiller, and control board. Support Chinese, English, Korean, Japanese, Russian, French, Spanish, and Israeli language systems
SC Machinery is equipped with a fully automatic wire feeder and is integrated with welding software. 1000W and 1500W support 0.8mm 1.0mm 1.2mm wire, 2000W support 0.8mm to 1.6mm. Wire send and back speed adjust through the touch panel. If two weld metal gaps are more than 0.2mm, that needs filler wire.
3 function in one fiber laser welder cutter cleaner, machine standard can do laser weld and laser cutting work, after change laser head, user can also use it to do laser cleaning work on metal surface. One machine solve all welding, cutting, welding work.
With optional 1000w, 1500w, 2000w, 3000w power for choice. Laser cleaning machine also called laser rust removal cleaning machine, laser cleaner, mainly use to remove metal rust, painting, oil from metal surface.
Eliminating physical contact, fiber lasers prevent contamination and enable delicate welding tasks.
Smooth welding seam, no subsequent grinding needed.
360 degree flexible movement welder with no experience can do a good job.
Rapidly cleans surfaces, reducing downtime and increasing productivity. Increased by 2 to 10 times.
Dry process without chemicals, minimizing environmental impact and health risks.
Spare at least 2 welders 80% to 90% power saving.
Here is a comparison table between Fiber Laser Welding and Argon Arc Welding (TIG Welding) to help you understand the differences in terms of key aspects such as precision, cost, and efficiency:
Aspect | Fiber Laser Welding | Argon Arc Welding (TIG Welding) |
Heat Input | Low heat input, minimizing distortion and warping | Higher heat input, leading to more distortion |
Weld Speed | Very high welding speed, faster production | Slower welding speed |
Precision | Extremely high precision, suitable for fine, delicate work | Moderate precision, suitable for various metal thicknesses |
Material Thickness | Ideal for thin materials, limited for very thick materials | Better for thicker materials, can be used on thin materials but slower |
Penetration Depth | Limited by laser power, good for thin materials | Deeper penetration, suitable for thicker materials |
Weld Quality | Clean welds with minimal spatter, no need for post-processing | High-quality welds, but may require cleaning post-weld |
Energy Efficiency | Highly energy-efficient, especially with modern fiber lasers | Less energy-efficient compared to fiber lasers |
Consumables | Minimal consumables, mostly optics and assist gases | Requires regular replacement of electrodes and filler rods |
Shielding Gas | Often uses assist gas (e.g., Argon, Helium, or Nitrogen) | Uses Argon or Helium as a shielding gas |
Automation | Easily integrated into automated systems (CNC, robotics) | Less automation-friendly, more suited for manual welding |
Skill Requirement | Requires highly skilled operators for setup and maintenance | Requires skilled welders for manual operation |
Initial Equipment Cost | Very high initial cost, especially for high-power systems | Moderate initial cost, more affordable than laser systems |
Maintenance Costs | Relatively low ongoing maintenance, but expensive component replacement | Regular maintenance required for electrodes and torches, lower cost than lasers |
Weld Speed | Faster weld speeds due to focused energy | Slower compared to fiber laser welding |
Applications | Best for high-precision applications (e.g., electronics, medical devices, thin metals) | Versatile, used in a wide range of industries (e.g., automotive, aerospace) |
Post-Weld Processing | Minimal post-processing required | May require grinding, cleaning, or polishing |
Safety | Requires strict laser safety measures (e.g., eye protection, enclosures) | Moderate safety requirements, usual welding safety gear |
Environmental Impact | Low emissions, less noise, and fewer fumes | Produces more fumes, spatter, and waste |
Summary:
Each method has its strengths depending on the specific welding application.
Laser welding can be applied to various materials like titanium, nickel, tin, zinc, copper, aluminum, chromium, niobium, gold, silver, and other metals and their alloys, steel, Kovar, and other alloys. Various dissimilar metals are available, such as copper-nickel, nickel-titanium, titanium-molybdenum, brass-copper, and low-carbon steel-copper.
SCHW handheld fiber laser welding machines are widely used in kitchen cabinets, stair elevators, shelves, ovens, stainless steel doors, window guardrails, distribution boxes, medical equipment, communication equipment, battery manufacturing, craft gifts, home furnishing, and other industries.
A laser welding machine is a device that uses a concentrated beam of light (laser) to join materials together, typically metals or thermoplastics. The high-energy laser beam heats the material at the weld point, causing it to melt and fuse together as it cools. Laser welding is known for its precision, speed, and ability to create strong welds with minimal distortion, making it a popular choice in industries such as automotive, aerospace, medical device manufacturing, and electronics.
Key Features of a Laser Welding Machine:
Laser welding is commonly used for high-precision applications like the production of medical devices, electronic components, and in the automotive industry for body panels and frames.
While laser welding machines offer many advantages, they also come with several disadvantages. Here are some of the main drawbacks:
These disadvantages make laser welding more suitable for specific industries and applications where precision, speed, and automation are critical, despite the higher costs and technical complexity.
The operating costs of a laser welding machine can be broken down into several key components. While laser welding is known for being efficient, the initial setup and ongoing operational expenses can be significant. Here’s a breakdown of the main factors contributing to the operating costs:
1. Energy Consumption
2. Maintenance Costs
3. Consumables
4. Labor Costs
5. Wear and Tear on Equipment
6. Cooling System
7. Facility Costs
8. Depreciation and Amortization
Approximate Breakdown of Operating Costs:
Conclusion:
While operating costs vary based on the specific machine, application, and production environment, laser welding can be expensive compared to traditional welding methods. However, its speed, precision, and efficiency can lead to long-term savings, especially in automated or high-production environments.
Yes, laser welding often requires the use of gas, although the need and type of gas can depend on the specific application and material being welded. These gases, known as shielding gases or assist gases, serve several important purposes during the welding process:
Reasons for Using Gas in Laser Welding:
Common Types of Gases Used in Laser Welding:
Situations Where Gas May Not Be Needed:
However, for most practical applications, the use of gas is critical to ensure high weld quality, minimize defects, and protect the weld pool. The choice of gas depends on the material being welded and the specific requirements of the welding process.
Yes, laser welding is generally safe when appropriate safety measures and precautions are followed. However, it does come with several potential risks that need to be carefully managed to ensure a safe working environment. These risks are primarily related to the high-power laser, heat, and associated materials used during the welding process. Here are the key safety considerations and precautions for laser welding:
1. Laser Hazards
Eye Injuries: The laser beam is highly concentrated and can cause serious damage to the eyes, potentially leading to blindness. Direct exposure to the laser light, even from reflections, can be harmful.
Skin Burns: High-powered lasers can burn the skin upon contact, leading to injuries.
2. Heat and Fire Hazards
High Temperatures: The laser generates intense heat, which can cause burns or fire hazards in the work area.
3. Fumes and Gases
Harmful Emissions: Laser welding can produce fumes and gases, depending on the material being welded. Metals like stainless steel, zinc, or aluminum can generate hazardous fumes, which may pose health risks when inhaled.
4. Material Hazards
Reflective Materials: Certain reflective materials, like aluminum or copper, can reflect the laser beam, potentially posing a hazard to nearby personnel or equipment.
5. Electrical Hazards
High Voltage: Laser welding machines require significant electrical power and often operate at high voltages. This presents a risk of electrical shock or equipment malfunction.
6. Mechanical Hazards
Automated Systems: Many laser welding systems are integrated with CNC or robotic arms, which can pose risks of mechanical injury if proper safety protocols are not followed.
7. Noise
High Noise Levels: Some laser welding processes, particularly when combined with high-speed automation, can generate significant noise.
8. Environmental Safety
9. Operator Training
Summary of Safety Precautions:
Conclusion:
Laser welding can be safe when the correct safety procedures and precautions are in place. The main risks—laser radiation, heat, fumes, and electrical hazards—are well understood, and many safety protocols have been developed to mitigate these dangers. Proper training, protective equipment, and adherence to safety standards are key to ensuring a safe laser welding environment.
Maintaining a laser welding machine is crucial for ensuring optimal performance, longevity, and safety. Regular maintenance can prevent costly breakdowns and extend the machine’s lifespan. Here’s a breakdown of the key maintenance tasks required for a laser welding machine:
1. Laser Source Maintenance
Cleaning the Optics (Lenses and Mirrors): The laser’s lenses, mirrors, and other optical components are essential for directing and focusing the laser beam. Over time, these can accumulate dust, debris, or material residues, reducing the machine’s efficiency.
Laser Alignment: Over time, the laser beam’s alignment may shift, causing inconsistent weld quality. Checking and adjusting the beam alignment ensures the laser hits the material at the correct point.
Laser Source Replacement: Different types of laser sources (e.g., fiber, CO2, Nd) have varying lifespans and will eventually degrade, causing reduced power output.
2. Cooling System Maintenance
Checking and Refilling Coolant: Laser welding machines often use a cooling system (water or air-cooled) to maintain optimal temperatures during operation. Low coolant levels or contaminated coolant can lead to overheating.
Cleaning Filters and Heat Exchangers: Cooling systems often have filters or heat exchangers that remove heat from the laser system. These components can become clogged with dirt or debris, reducing cooling efficiency.
3. Assist Gas System Maintenance
Inspecting Gas Lines: Laser welding often uses assist gases (e.g., argon, helium, nitrogen) to protect the weld and improve weld quality. Leaks in the gas lines can affect weld performance.
Check Gas Supply Pressure: Inconsistent gas pressure can lead to poor welding results.
4. Electrical System Maintenance
Inspecting Electrical Components: Over time, electrical connections, cables, and components can wear down, leading to malfunctions or reduced performance.
Checking Power Supply: Laser welding machines require a stable power supply. Voltage fluctuations can affect performance and damage components.
5. Mechanical System Maintenance
Lubricating Moving Parts: If the machine has moving parts (e.g., CNC or robotic arms), these need regular lubrication to prevent wear and ensure smooth operation.
Inspecting Motion Control Systems: Machines with robotic or automated features require regular inspection of gears, motors, and control systems to avoid failures.
6. Safety System Maintenance
Checking Safety Interlocks: Laser welding machines are often equipped with safety interlocks to prevent accidental exposure to the laser beam. These systems must function properly to ensure operator safety.
Inspecting Protective Barriers and Shields: Any barriers or shields designed to protect operators from the laser beam should be inspected for wear or damage.
7. Software and Firmware Updates
Updating Control Software: Many modern laser welding machines use software or firmware for precise control. Manufacturers often release updates to improve performance or add features.
Backing Up System Settings: Regular backups of machine settings ensure that configurations can be restored in case of failure.
8. General Cleaning
Wiping Down the Machine: Regular cleaning of the machine’s external surfaces and workspace helps prevent dust, debris, and contaminants from affecting its performance.
9. Preventive Maintenance Checks
Scheduled Inspections: Routine inspections by qualified technicians are important for identifying potential issues before they become major problems.
Summary of Maintenance Tasks and Frequency:
Conclusion:
Regular maintenance of a laser welding machine ensures that it operates efficiently, safely, and with high weld quality. Preventive maintenance can minimize downtime and extend the lifespan of the equipment, making it a critical part of machine operation.
Can you pls tell us your plate thickness and length? Our sales will recommend machine model for you.