In recent decades, with the rapid development of laser cutting technology, the application of laser cutting machines in the manufacturing industry has become increasingly widespread. Laser cutting processing replaces traditional mechanical knives with invisible light beams, which have the characteristics of high accuracy, fast cutting, not limited to cutting pattern limitations, automatic layout saving materials, smooth cutting, and low processing costs. It will gradually improve or replace traditional metal cutting equipment. Laser cutting machine working principle leads the mechanical part of the laser blade has no touch with the workpiece and will not cause scratches on the working surface during operation. Laser cutting speed is fast, the incision is smooth and flat, and generally does not require subsequent processing. Cutting heat affected zone is small, plate deformation is small, and cutting seam is narrow. The incision has no mechanical stress and no shear burrs. Laser cutting machine has high machining accuracy, good repeatability, and no damage to the material surface, CNC programming can process any flat drawing, and can cut large whole boards without the need for molds, which is economical and time-saving.
Since laser cutting machines have so many advantages, more and more people want to purchase laser cutting machine. However, many people who have not been exposed to the laser equipment industry are still very unfamiliar with the principle and composition of laser cutting machines. Today in this article, we will popularize the relevant knowledge of laser cutting machines for everyone.
Table of Contents
Laser Cutting Machine Working Principle
Laser cutting machine uses a focused high-power density beam to work, allowing the irradiated material to quickly melt, evaporate, ablate or ignite, and to cut the workpiece by blowing away the molten material through a high-speed airflow coaxial with the beam.
When the laser beam interacts with the material, several processes occur. The strong heat generated by the laser beam rapidly increases the temperature of the material, causing it to melt, evaporate, or undergo chemical reactions. The specific interaction depends on the characteristics of the material, such as absorption coefficient and melting point, as well as laser parameters, such as power density and pulse duration.
For low melting point materials, such as plastics, the laser beam can melt the material during penetration. Then, the melted material is blown away by a gas jet, forming a cut (cut width). In the case of materials with higher melting points (such as metals), the laser beam directly evaporates the material, forming narrow and precise cutting.
Gas assisted cutting is commonly used in laser cutting to enhance the cutting process. Gas such as oxygen or nitrogen is blown onto the surface of the material through the nozzle of the cutting head. Gas helps to remove melted or evaporated materials from the cutting area, cools the material, and prevents the appearance of burrs or scum. The choice of gas depends on the material being cut and the required cutting quality.
The incision width or incision width is determined by several factors, including laser power, focal spot size, material thickness, and cutting speed. The width of the incision can be controlled by adjusting these parameters to achieve the desired cutting accuracy. In addition, laser cutting can cause a phenomenon called conicity, where the cutting has a slight taper. The cone angle depends on the material properties and laser parameters, and can be minimized by optimizing cutting conditions.
Basic Knowledge Of Laser
Laser (stimulated radiation amplification) is a device that generates coherent beams of light. It consists of three main components: active medium, energy source, and optical resonator. The active medium can be a solid, liquid, or gas, which emits photons when excited by an energy source. Optical resonators reflect photons back and forth through active media, amplifying and aligning light waves. This process leads to the formation of a powerful and coherent laser beam.
Laser Cutting Machine Types
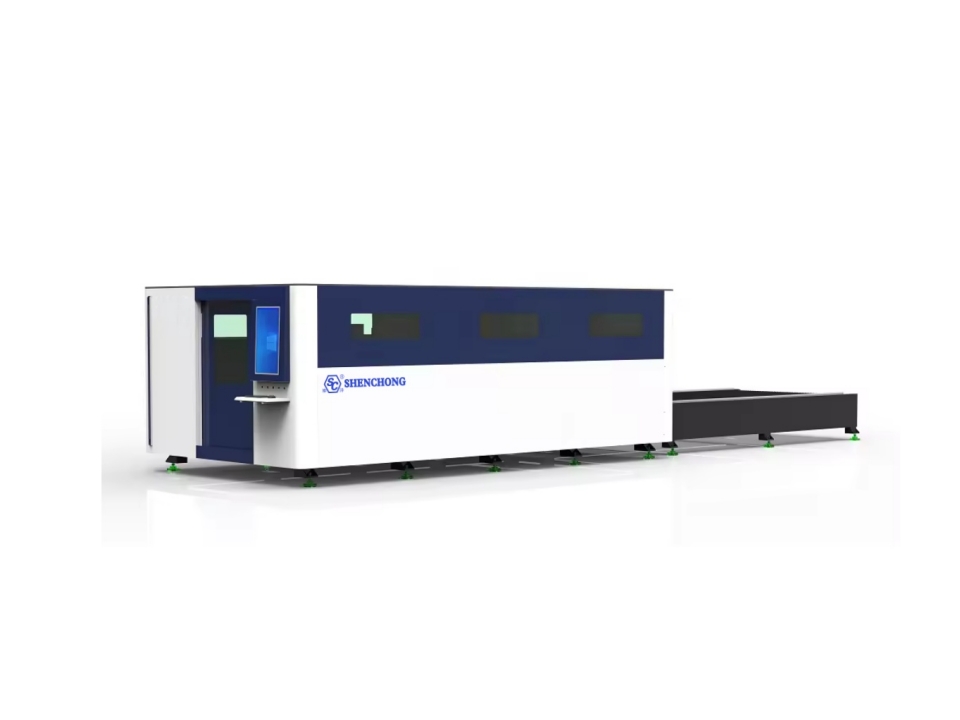
There are several types of lasers in laser cutting machines, including CO2 lasers, Nd: YAG lasers, and fiber lasers. CO2 laser is the most common type, using a mixture of carbon dioxide, nitrogen, and helium as the active medium. Nd: YAG lasers use solid-state crystals, such as neodymium doped yttrium aluminum garnet, as the active medium. On the other hand, fiber lasers use fibers doped with rare earth elements as the active medium. Each type of laser has its unique performance, suitable for specific cutting applications.
Currently, the mainstream lasers are CO2 and fiber lasers.
CO2 Laser
CO2 laser is one of the earliest and most popular types of lasers. Gas discharge is not entirely carbon dioxide. It contains carbon dioxide, nitrogen, hydrogen, xenon, and helium.
There are two options for CO2 laser cutting: using oxygen or nitrogen. Oxygen is preferred for laser cutting thicker materials. Nitrogen is preferred for laser cutting of thin plates. Use oxygen CO2 laser cutting to form an oxide layer on the cutting surface. To avoid this situation, pre-treatment processes such as sandblasting are carried out on the workpiece. CO2 laser cutting is commonly used to cut non-metallic materials, such as wood, plastic, glass, and textiles. It is also possible to cut metals such as low-carbon steel, stainless steel, and aluminum with the correct settings.
Fiber Laser Cutting
Fiber laser cutting machine working principle is to use solid laser to melt and penetrate metals, achieving precise and efficient cutting. The laser medium for this technology is fiber instead of gas or crystal. Laser is a type of concentrated light, and fiber optic is an active gain medium that can elevate the laser to a higher power state.
Fiber laser cutting is a thermal cutting method that uses a focused high-power laser beam as the main heat source. The fiber laser generator uses high-power fiber optic components to transmit strong beams of light. The laser beam is focused on the area, and the material rapidly melts and evaporates. Fiber laser cutting machine can cut most materials of different thicknesses according to the function of the equipment.
Fiber laser cutting machine is a laser cutting process that uses an optical laser generator to cut materials. It can accurately and high-quality cut various materials. Although the basic principle of fiber laser cutting machine is basically the same as that of other laser cutting machines, the main difference lies in how energy is transmitted and focused on the workpiece.
Emit a highly focused beam of light through a fiber laser generator. Then, the laser beam is guided to the cutting material by focusing on the lens. Focusing the laser beam will generate a small and strong heat source. After aligning the material surface, it can quickly melt and evaporate the material, achieving high-precision cutting.
Other important components of the machine include the control of its software system and the components that guide and support cutting materials. In addition, fiber laser cutting machines can be equipped with many different sizes and power cutting heads. Based on your specific needs and customized laser cutting machine, it can achieve the expected performance and results.
Classification Of Laser Cutting Technology And Laser Cutting Machine Working Principle
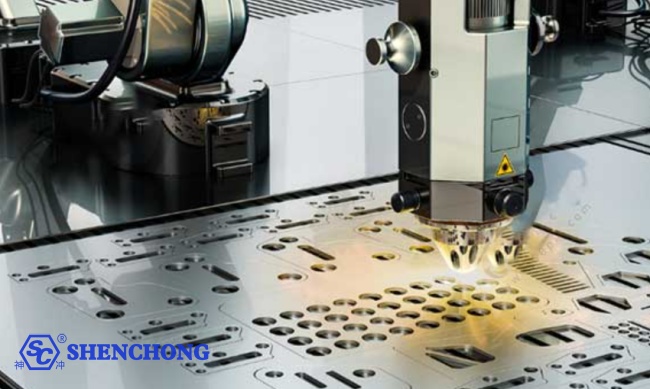
Laser Vaporization Cutting
The workpiece is heated by a high-energy density laser beam, and the temperature rises rapidly. The material reaches its boiling point in a short time, and it begins to evaporate to form steam. These vapors are ejected at high speeds and form narrow slits in the material as they are ejected. The evaporation heat of materials is usually high, so laser gasification cutting requires a higher power and power density.
Laser vaporization cutting is commonly used to cut very thin metal and non-metallic materials.
Laser Melting Cutting
When laser melting and cutting, the metal material is melted by laser heating, and then non oxidizing gas is sprayed through a nozzle coaxial with the beam of light. The liquid metal is discharged through the strong pressure of the gas to form a slit. Laser melting and cutting do not require complete evaporation of metal, and the required energy is only 1/10 of that of evaporation cutting.
Laser melting cutting is mainly used to cut some non oxidizable materials or active metals.
Laser Oxygen Cutting
The principle of laser oxygen cutting is similar to that of oxygen acetylene cutting. It uses laser as a preheating heat source and active gases such as oxygen as cutting gases. The injected gas reacts with the cutting metal on one hand, generating a large amount of oxidation heat. On the other hand, melted oxides and molten materials are blown out of the reaction zone, forming gaps in the metal. Due to the oxidation generated during the cutting process, a large amount of heat is generated, and the energy required for laser cutting oxygen is only half of that for melting and cutting, while the cutting speed is much faster than that for laser vaporization cutting and melting cutting. Laser oxygen cutting is mainly used by metal laser cutting machines to cut easily oxidized metal materials such as carbon steel, titanium steel, and heat-treated steel.
Fracture Controlled Cutting
Fracture controlled cutting is also known as thermal stress cracking. It is suitable for cutting brittle materials. When uncontrolled force or temperature is applied, brittle materials often fracture into fragments. Fracture control cutting focuses a very narrow laser beam on the surface of a small workpiece. It will generate a thermal gradient, causing cracks to appear in the workpiece at that location. Then, the laser moves in a very fast and controllable manner to propagate cracks along the incision.
When cutting glass and ceramics, fracture control cutting is usually used. The laser did not completely penetrate the material thickness. Only a portion of the thickness was cut, while the rest separated due to rupture.
Invisible Cutting
Invisible cutting is an advanced laser cutting technology used for cutting semiconductor chips. It works in two stages – laser irradiation stage and expansion stage. Laser does not melt the workpiece because it produces unwanted molten material. On the contrary, the irradiation stage uses a laser wavelength that completely passes through the workpiece.
However, this wavelength generates internal deformation and cracks in the workpiece. Then, the expansion stage generates expansion stress on the workpiece. This stress divides the workpiece into many blocks in the internal defect area. The final result is a clean cut wafer with no residue.
Vector Rating
Vector engraving is a laser cutting technique used for carving workpieces. Laser does not penetrate the entire thickness of the material. On the contrary, the laser will follow the direction specified by the vector.
By defocusing the laser beam, the thickness of the carving can be easily adjusted. The depth of carving can also be adjusted. Vector carving can create complex designs that are simple and straight.
Laser Cutting Machines Typically Consist Of The Following Components
- Laser: refers to a laser generator, electro-optical conversion, and equipment that emits laser energy.
- Cutting head: includes parts such as nozzle, focusing lens, and focusing tracking system software.
- Light transmission component: mapping reflective lenses to provide the necessary orientation for laser guidance.
- CNC system: Control the machine tool to achieve the movement of the X, Y, and Z axes, while also controlling the output power of the laser.
- Refrigeration system: a circulating cooling device used to cool the laser and cutting head, taking away unnecessary heat to maintain the normal operation of the equipment and ensuring smooth beam transmission quality.
- Voltage regulator: stabilizes the power supply voltage of laser cutting equipment, ensuring smooth operation and protective effect.
- Air compressor: During air cutting, it provides an air source device for the equipment to ensure the required pressure and flow rate.
- Gas storage tank: including material gas tank and auxiliary gas tank during laser cutting machine operation, used to fill the chemical gas caused by laser fluctuations and provide auxiliary gas for cutting heads.
- filtering device: used to provide clean dry gas to the laser generator and light channel to maintain the normal operation of the channel and reflector lens.
- Dust removal equipment: Extract the dust and smoke generated during production and processing, and filter them out.
On a laser cutting machine, the laser cutting head moves on the metal plate in the shape of the desired part, thereby cutting out the part from the plate. The capacitive height control system maintains a very precise distance between the nozzle end and the cut plate. This distance is important because it determines the position of the focus relative to the surface of the plate. The cutting quality may be affected by raising or lowering the focus from above, at or below the surface of the metal sheet.
The working principle of a laser cutting machine is to focus the laser beam on a piece of material. The laser power is so high that when focused, it will raise the temperature of the material to be cut to a sufficiently high temperature, thereby melting or evaporating the material in a small area where the beam is focused. Usually, auxiliary gases are used to help push molten materials out of the cutting area. This is especially true for cutting thick sheets such as metal or plywood.
To cut the shape, move the laser head and use some form of gantry to position the beam on the new material, thus cutting a line instead of a small pinhole. The types of motion systems include racks and pinions, ball screws, and linear motors. Linear motors are the most expensive, but they have the fastest speed and highest accuracy. The rack and pinion provide almost the same speed and accuracy, but at a lower price. Some small laser enthusiasts may also use timing belts and stepper motors to move their laser heads. In any case, a system with servo and encoder feedback can greatly improve the accuracy of the laser cutting system, and the rigid frame can also be isolated from vibration.
For laser cutting operations, it is important to choose a wavelength that is highly absorbent of the material to be cut.
When laser energy is directed to the surface of the material, the material absorbs so much energy that it quickly heats up beyond its melting temperature and reaches its degradation temperature.
At the degradation temperature, the material will decompose and decompose. When this situation occurs, smoke is usually released.
The edge of the incision may be heated to a lower level and actually melted and modified. This can actually be used as a useful sealing mechanism for fiber materials, such as preventing threads.
When the laser cutting machine is working, it is best to tilt the laser so that the smoke generated during the cutting process does not accumulate as soot on the laser optical components. In addition, when cutting (or welding) high reflective surfaces, it is important to prevent the laser beam from reflecting back from the surface to the laser optical components, which may damage them.
The Working Process Of CNC Laser Cutting Machine
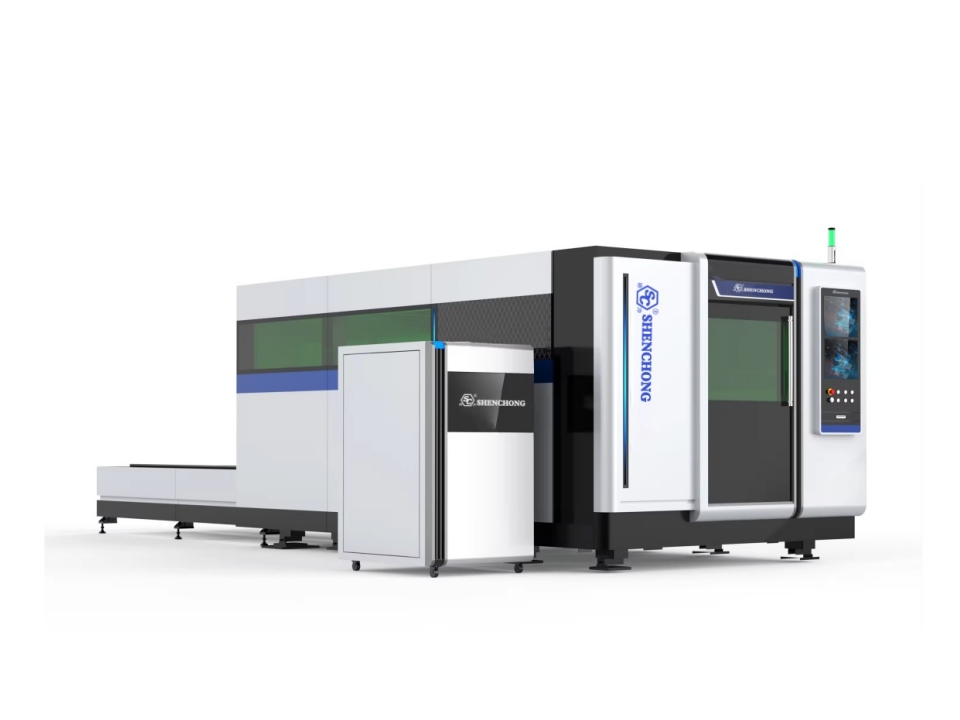
Laser processing technology provides many different functions for different industries. Regardless of the characteristics of these machines, their basic workflow is the same. The following are the working steps of a CNC laser machine:
Load G code
When the operator loads the G code onto the system, the machine starts working. The G code indicates the direction of movement of the laser cutting machine.
Generation Of Laser Beam
Once the machine starts working, the laser resonator will generate a beam of light. For various types of lasers, the process of laser generation can be different. The color of the laser can also be different. For example, in a CO2 laser, the laser generator emits infrared light. This type of laser beam is completely visible to the human eye.
Guide Laser
The directional system turns the laser beam towards the focusing system. A series of mirrors can change direction. A dedicated beam bending device can also bend the generated laser into the focusing area.
Laser Focusing
The focusing system reduces the width of the laser beam and increases its power. This is accomplished using a laser focusing head and a focusing lens. The focusing system also ensures that the focused laser beam is completely circular and free of stray light. The laser beam is shot out of the machine through a nozzle.
Material Cutting
The focused laser beam is guided to the workpiece material. The contact point is exposed to the laser beam for a sufficient amount of time to melt the material. The exposure time varies depending on the thickness and type of material.
Cutting Head Movement
The mechanical system moves the laser head in the desired shape according to the instructions in the G code. The movement speed varies depending on the specific job.
Conclusion
CNC laser cutting technology is at the forefront of the manufacturing industry, providing unparalleled accuracy, speed, and versatility. By understand the laser cutting machine working principle can help users to learn what type of laser cutting machine they should purchase. With the development of technology, companies like SC are leading the trend by providing innovative solutions to meet the constantly changing needs of the industry. Not only we provide single set of metal sheet fiber laser cutting machine for sale but also we can design and produce loading unloading system for laser cutting machine to meet clients’ automation requirements. Whether you are a small business owner, hobbyist, or industrial manufacturer, investing in CNC laser cutting machines can change your operations, opening up new possibilities for design, prototyping, and production.