Laser cutting machine operation has become the significant working skill in metal processing industry since laser cutting technique as a high productivity and high precision cutting method has widely sued in all different industries and its develop trends is keeping expanding. The following are the main aspects of the development trend of laser cutting technology.
- High power and high-speed cutting: With the continuous progress of laser generator technology, the power and cutting speed of laser cutting machines are constantly improving, which can complete cutting tasks faster and improve production efficiency.
- Multi wavelength laser technology: The application of multi wavelength laser can achieve more precise cutting of different materials, expanding the application range of laser cutting.
- Intelligence and automation: The laser cutting machine is equipped with advanced control systems and sensor technology, which can achieve automated control and intelligent operation, improve production efficiency and quality.
- The promotion of fiber laser technology: Fiber laser technology has the advantages of small volume, high energy density, and good beam quality. It is gradually replacing traditional CO2 laser technology and becoming the mainstream laser cutting technology.
- Green and environmentally friendly cutting: Green and environmentally friendly cutting is an important trend in the current development of laser cutting technology. By optimizing cutting processes and material selection, environmental pollution and energy consumption have been reduced.
- Customization and flexible production: With the increasing trend of personalized and customized consumer demand, laser cutting technology can flexibly respond to the customized production needs of different products.
People who want to buy laser cutting machine often ask, “I bought a laser cutting machine and have received pre-training from the manufacturer. How do I use it?” Everyone who buy laser cutting machine should learn more about the specific laser cutting machine operation steps and methods to better apply them and better serve the production needs.
Preparation Before Operation
Firstly, users must make the following preparations before using the laser cutting machine:
Machine Preparation
Check if all connections of the laser machine (including power supply, PC, and exhaust system) are correct and inserted correctly.
- Before use, please check if the power supply voltage matches the rated voltage of the machine to avoid unnecessary damage.
- Check if there is an air outlet in the exhaust pipe to avoid obstructing air convection.
- Check if there are any other foreign objects on the machine to avoid affecting normal cutting operations.
- Check if the cooling water pressure and temperature of the chiller are normal.
- Ensure that the work area and optical components are clean, and clean them if necessary.
- Check if the cutting auxiliary gas pressure is normal.
- Visually inspect the condition of the laser machine. Ensure that all institutions have free mobility.
Safety Preparation
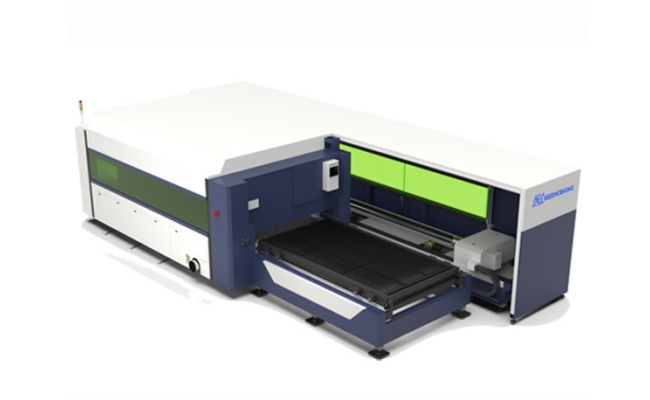
Safety Training And Education
All operators must receive comprehensive safety training and education before operating the laser cutting machine. The training content should include the basic principles, operating procedures, safety procedures, emergency response procedures, etc. of laser cutting machines. Through training, operators can understand the dangers of laser cutting machines and learn to use and maintain equipment correctly.
Equipment And Protective Measures
- Laser safety cover: must be installed on the laser cutting machine, which can effectively block the laser beam and prevent radiation damage.
- Personal protective equipment: Operators should be equipped with appropriate personal protective equipment, such as goggles, protective clothing, gloves, etc., to protect their safety.
- Safety interlock system: Ensure that the laser cutting machine can only start working in a safe position and that all protective devices are intact to prevent unauthorized personnel from entering the operating area.
Environmental Safety
- Ventilation system: The operating area should be equipped with a good ventilation system to timely eliminate harmful gases generated by laser cutting and protect the health of operators.
- Fire prevention measures: Fire extinguishers and other fire-fighting equipment should be installed around the equipment, and regular inspections and maintenance should be carried out to prevent fire accidents.
Laser Safety
- Do not look directly at the laser beam: Operators should not look directly at the laser beam and should always wear protective goggles to prevent eye damage from laser radiation and ensure that other personnel are not directly exposed to the laser beam.
- Pay attention to material compatibility: Some materials may release toxic and harmful gases during the cutting process. Protective and evacuation measures should be taken to avoid harm to personnel.
Emergency Maintenance
Develop emergency procedures: Establish and train operators on emergency procedures, including measures for handling various emergency situations such as machine malfunctions and fires, to ensure timely and effective responses to various emergency situations.
Machine Attendance
- Regular maintenance plan: Establish a regular maintenance plan, including cleaning, lubrication, inspection, and other items, replacing worn parts, etc., to ensure that the equipment is in optimal working condition and reduce the incidence of failures.
- Provide equipment maintenance and cleaning training to operators: Train operators on basic equipment maintenance and cleaning to extend equipment life and ensure operational safety.
Access Restrictions
Strictly enforce entry and exit restrictions and prohibit non staff from entering the operating area. At the same time, safety signs should be set up at appropriate locations to remind personnel to pay attention to hazardous areas and operating procedures.
Safety Signs And Safe Material Handling
- Install safety signs: Set up obvious safety signs in the operating area to remind personnel to pay attention to operating procedures and hazardous areas.
- Safe material handling: When loading and unloading materials, operators must be aware of the issue of safe material handling. Especially when dealing with toxic and harmful substances, appropriate protective measures must be taken to avoid pollution and harm to personnel and the environment.
During Laser Cutting Machine Operation
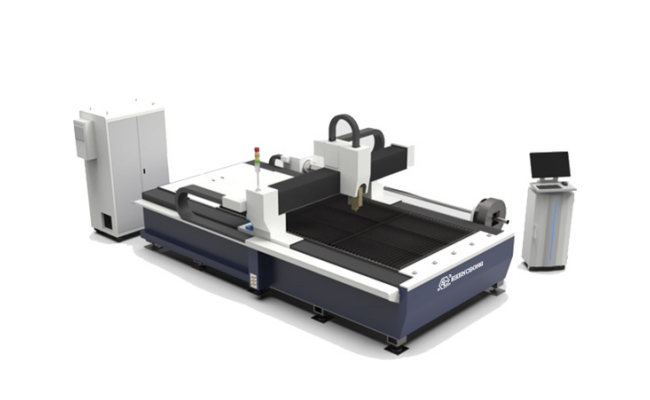
Power On Sequence
First, turn on the power switch, then start the control system, and finally turn on the cooling system and air source. Pay attention to ensuring that the purity and pressure of the gas source meet the equipment requirements.
Calibration
Before starting the laser cutting machine operation, it is necessary to calibrate the laser cutting machine. Calibration includes adjusting the focus, cutting head angle, and height to ensure cutting accuracy and effectiveness.
Adjustment Of Optical Path During Hardware Operation Of Laser Cutting Machine
The operation of the hardware part mainly focuses on the focusing part. This part of the work is very important. Although the manufacturer has adjusted the focal length of the laser cutting machine before leaving the factory, it is inevitable that the optical path will be misaligned during long-term operation, which will affect the cutting effect Only the perfect combination of laser tubes, reflective frames (A, B, C), focusing lenses, and corresponding adjustment devices can achieve the best results and produce the best products. This is the core part used in laser cutting machines. Therefore, it is very necessary to check the optical path and make regular adjustments.
Let’s take a look at the method of adjusting the optical path of the laser cutting machine:
- Adjustment of the first lamp: Use textured paper to stick it onto the dimming target hole of reflector A, manually tap the lamp (note that the power should not be too high at this time), fine tune the base reflector A and laser tube bracket of the first lamp, so that the light hits the center of the target hole, and be careful not to block the light.
- Adjust the second light, move the reflector B onto the remote control, use a piece of cardboard to emit light from near to far, and guide the light to the cross light target. Because the high beam is inside the target, the near end must be inside the target, and then adjust the near and far beam points to be the same, that is, how far the near end is and how far the far end is, so that the position of the cross is the same between the near and far beam points, that is, near (far), indicating that the optical path is parallel to the Y-axis guide rail
- Adjust the third lamp (note: the cross divides the spot equally on the left and right), move the reflector C to the remote control, guide the light to the light target, shoot once at the near end and once at the far end, and adjust the position. The position of the cross follows the same position as the cross at the near point, which means that the beam is parallel to the X-axis. At this point, when the light path enters or exits, it is necessary to loosen or tighten M1, M2, M3 on frame B until the left and right halves are reached.
- Adjust the fourth lamp and stick a piece of textured paper on the light outlet, leaving a circular mark on the adhesive paper for the lamp hole. Light the lamp, remove the adhesive paper, observe the position of the lamp hole, and adjust the frame according to the situation. M1, M2, and M3 are on C until the point becomes round and straight.
Software Operation Process Of Laser Cutting Machine
In the software part of the laser cutting machine, different parameters need to be set due to the different materials and sizes being cut. These parameter settings usually require professional personnel to set, and may require a lot of time to explore on your own. Therefore, the parameter settings should be recorded during the manufacturer’s training.
Trial Cutting
Before conducting formal cutting, it is recommended to conduct a trial cutting operation. Trial cutting can check the operation status of the equipment, determine cutting parameters, and verify cutting effects.
- Fix the material to be cut on the workbench of the laser cutting machine.
- Adjust the equipment parameters accordingly based on the material and thickness of the metal sheet.
- Try cutting the material, and after the material is cut, check the perpendicularity, roughness, and presence of burrs and slag on the cutting surface.
- Analyze the cutting situation and adjust the cutting parameters accordingly until the sample cutting process meets the standards.
Formal Cutting
After successful trial cutting, formal cutting operations can begin. Operators need to set corresponding control parameters based on the desired cutting shape and size, such as laser power, cutting speed, air pressure, etc. During the operation, there must be staff present to carefully observe the cutting situation. If there is an emergency situation that requires quick response, press the emergency stop button. After cutting, check the cutting quality and accuracy of the first sample.
Turn Off Sequence
After completing the cutting operation, the machine needs to be shut down in the order of first turn off the laser, then shutting down the control system and gas source. Finally, turn off the power switch.
Why Is It Important To Follow The Standard Operating Procedures Of Laser Cutting Machines
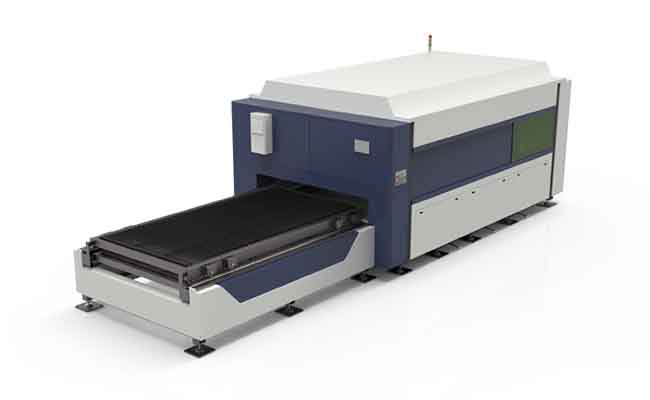
The safe operation of laser cutting machines is crucial for both operators and equipment. The following are several aspects of its importance.
Importance To Operators
- Personal safety: The operation of laser cutting machines involves high-energy laser beams and complex mechanical systems. If operated improperly, operators may be injured by direct laser beams, hot melt splashes, and other injuries.
- Occupational health protection: Long term exposure to laser radiation and harmful gases may affect the health of operators, such as eye injuries, respiratory diseases, etc. Therefore, safe operation can protect the occupational health of operators.
- Reduce accidents: Implementing safety operation procedures and measures can effectively reduce the incidence of accidents and minimize casualties in work.
- Improving work efficiency: Reasonable safety operation procedures and training can help operators better master equipment operation skills, improve work efficiency and production quality.
The Importance Of Equipment
- Extending equipment lifespan: Safe operation can avoid equipment damage and malfunctions caused by operational errors, and extend the service life of laser cutting machines.
- Protecting equipment integrity: Safe operating procedures and measures can reduce accidental damage and wear of equipment, protecting its integrity and stability.
- Saving maintenance costs: Safe operation can reduce repair and replacement costs caused by operational errors, and lower the company’s production costs.
- Maintaining production continuity: Safe operation can avoid production interruptions caused by equipment failures or accidents, ensuring production continuity and stability.
Summary
In summary, the laser cutting machine operation is of great significance for ensuring the safety and health of operators, extending equipment life, reducing production costs, and maintaining production continuity. Therefore, enterprises and operators should attach great importance to safe operations and strictly implement safety regulations and measures. SC Machinery is a professional laser cutting machine manufacturer, welcome to contact with us for more machine details.