Introduction
Table of Contents
Laser cleaning is a sophisticated and emerging technology that uses laser beams to remove contaminants, impurities, or coatings from various surfaces. It has gained considerable traction across numerous industries due to its precision, efficiency, and environmental benefits. However, like any technology, it has its set of advantages and disadvantages. This article delves into the detailed aspects of laser cleaning, providing an in-depth analysis of its benefits and drawbacks.
What Is Laser Cleaning?
Laser cleaning involves the use of laser beams to remove contaminants, such as rust, paint, oxides, oils, and other residues, from surfaces. The laser beam, typically generated by a fiber or solid-state laser, is directed at the target surface, where it interacts with the unwanted material and removes it through various mechanisms.
Historical Context
Laser cleaning technology has evolved significantly since the advent of lasers in the mid-20th century. Initially, lasers were primarily used in scientific research and medical applications. Over time, their use expanded to various industrial applications, including cutting, welding, and cleaning. The development of high-power and pulsed lasers has particularly accelerated the adoption of laser cleaning technology.
How Laser Cleaning Works
Laser cleaning involves directing a focused laser beam onto a surface to remove unwanted materials such as rust, paint, oxides, and other contaminants. The laser beam ablates the material through various mechanisms, including thermal, photomechanical, and photochemical interactions. The process can be fine-tuned by adjusting the laser’s wavelength, pulse duration, and energy to achieve the desired cleaning effect without damaging the substrate.
Laser cleaning works through a process called ablation, where the laser beam interacts with the material on the surface, causing it to vaporize, sublimate, or be ejected. The primary mechanisms involved in laser cleaning are:
- Thermal Ablation: The laser beam heats the contaminant, causing it to evaporate or burn off. This mechanism is effective for removing organic materials like oils and paints.
- Photo–mechanical Ablation: The laser pulses create rapid thermal expansion and contraction in the material, leading to mechanical stress that causes the contaminant to fracture and detach from the surface. This is particularly useful for removing oxides and rust.
- Photochemical Ablation: The laser energy induces chemical reactions in the contaminant, breaking down its molecular structure and facilitating its removal. This method is often used for cleaning delicate surfaces and in applications requiring minimal thermal impact.
Applications Of Laser Cleaning
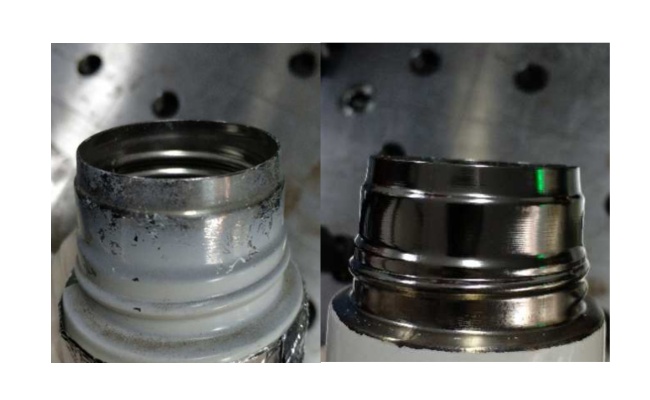
1. Industrial Manufacturing
Laser cleaning is extensively used in industrial manufacturing for removing rust, oxides, and other contaminants from metal surfaces. It is also employed in the preparation of surfaces for welding, bonding, and coating processes. The automotive, aerospace, and shipbuilding industries particularly benefit from the precision and efficiency of laser cleaning.
2. Heritage Conservation
The non-contact nature of laser cleaning makes it ideal for the conservation and restoration of historical artifacts, sculptures, and buildings. It can remove layers of dirt, pollutants, and old coatings without damaging the underlying material. This application is crucial for preserving cultural heritage and maintaining the aesthetic and structural integrity of valuable artifacts.
3. Electronics and Semiconductor Industry
In the electronics and semiconductor industry, laser cleaning is used for the precise removal of contaminants and residues from delicate components. It ensures the cleanliness of surfaces before processes such as lithography, soldering, and coating. The precision of laser cleaning is essential for maintaining the functionality and reliability of electronic devices.
4. Medical and Pharmaceutical Industry
Laser cleaning is applied in the medical and pharmaceutical industry for the sterilization and cleaning of equipment, tools, and surfaces. It effectively removes biological contaminants, residues, and coatings without the use of harsh chemicals. This application is crucial for ensuring the safety and hygiene of medical devices and facilities.
5. Nuclear Decontamination
Laser cleaning is employed in the nuclear industry for the decontamination of surfaces exposed to radioactive materials. It can remove radioactive contaminants without generating secondary waste, reducing the risk of spreading contamination. This application is vital for maintaining the safety and integrity of nuclear facilities.
Components Of A Laser Cleaning System
A typical laser cleaning system consists of several key components:
- Laser Source: This generates the laser beam. Common types include fiber lasers, solid-state lasers, and CO2 lasers.
- Optical Delivery System: This includes mirrors, lenses, and fiber optics to direct and focus the laser beam onto the target surface.
- Scanning System: This allows the laser beam to move across the surface, ensuring even and thorough cleaning. It can be controlled manually or integrated with automated systems.
- Control System: This manages the laser parameters, such as power, pulse duration, and repetition rate, to optimize the cleaning process for different materials and contaminants.
- Safety Enclosures and Protective Equipment: To ensure operator safety, laser cleaning systems are equipped with safety enclosures, interlocks, and protective gear like laser safety glasses.
Types Of Laser Cleaning Machine
Laser cleaning is a cleaning method that uses lasers of different wavelengths to react with different materials to remove pollutants without damaging the substrate material.
Although there are many laser wavelengths, there are currently only three types of lasers that are truly used for laser cleaning. Fiber laser with a wavelength of 1064nm, carbon dioxide laser with a wavelength of 10600nm, and ultraviolet laser with a wavelength of 355nm. They are divided into pulsed lasers and continuous lasers. Currently, fiber laser is the most widely used in the cleaning field because it is the cheapest and can be transmitted using flexible fiber optic cables, with a wide range of applications. However, fiber lasers mainly react with metallic materials, and laser welding and cutting all use fiber lasers, which have limited effects on non-metallic materials.
Carbon dioxide laser mainly reacts with non-metallic materials, and is used for laser paint removal, laser cutting of wood and leather, etc. However, it has a fatal disadvantage that it cannot be transmitted by fiber optic cables and can only be transmitted by bulky light guide arms. Currently, the price of light guide arms is too high, making it inconvenient to use and far less cost-effective than fiber optic lasers, which limits the application of carbon dioxide laser in the cleaning field. But in the field of removable small object paint removal, carbon dioxide laser still performs very well.
UV laser is a cold light source that generates almost no heat during the cleaning process. It reacts with all materials, whether metallic or non-metallic. But it is the most expensive among the three lasers, currently only used in high-end fields that are not price sensitive.
At present, the most commonly used lasers in the field of cleaning are continuous fiber lasers and pulsed fiber lasers.
Continuous Laser Cleaning Machine
The continuous laser, also known as a continuous-wave (CW) laser, is a type of laser that emits a constant and uninterrupted beam of light. Unlike pulsed lasers, which emit light in short bursts, continuous lasers provide a steady and continuous output of laser radiation. This continuous emission makes them ideal for applications that require consistent energy delivery over a prolonged period.
Pulse Laser Cleaning Machine
The pulse laser cleaning machine is an innovative solution for efficient and precise surface cleaning. This advanced technology uses high-intensity, ultra-short laser pulses to remove contaminants, rust, paint, and other unwanted materials from various surfaces without causing damage. Unlike traditional methods that involve harsh chemicals or abrasive techniques, the pulse laser cleaning machine is a non-contact, eco-friendly option that maintains the integrity of the underlying material.
Differences Between Continuous Laser Cleaning Machine And Pulse Laser Cleaning Machine
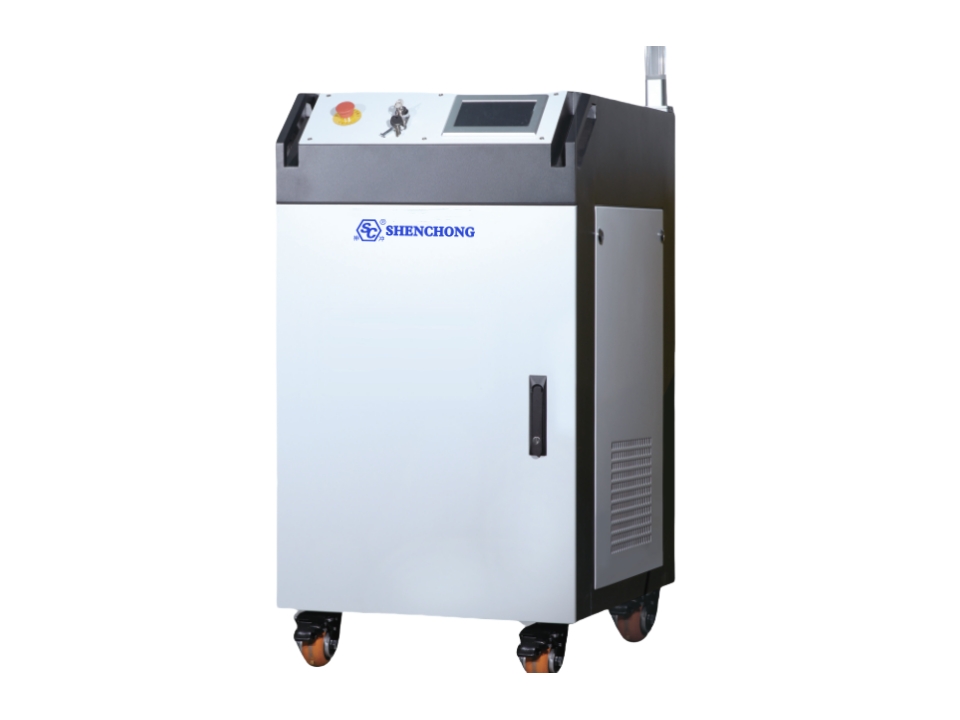
Emission Mode
Pulse Laser: Emits light in short, intense bursts or pulses. Each pulse lasts for a very short duration, typically ranging from femtoseconds to milliseconds.
Continuous Laser: Emits a continuous, unbroken beam of light. The output is steady and uninterrupted over time.
Energy Delivery
Pulse Laser: Delivers energy in concentrated, high-power bursts. This is useful for applications requiring high peak power, such as material ablation, medical procedures, and precise cutting.
Continuous Laser: Delivers energy at a constant, lower power level. This is ideal for applications needing uniform energy distribution over a period, such as continuous cutting, welding, and surface cleaning.
Heat Management
Pulse Laser: Generates less heat overall because the energy is delivered in short bursts, allowing cooling between pulses. This reduces thermal effects on the material being processed.
Continuous Laser: Generates more heat due to the constant energy output. Effective cooling systems are often required to manage the heat and prevent damage to the material.
Peak Power
Pulse Laser: Can achieve extremely high peak powers during each pulse, even if the average power is relatively low.
Continuous Laser: The power output is consistent and generally lower than the peak power of a pulsed laser.
Applications
Pulse Laser: Used in applications requiring high precision and minimal thermal impact, such as micromachining, medical treatments (e.g., laser eye surgery), and scientific research.
Continuous Laser: Suited for applications where continuous energy application is needed, such as industrial cleaning, continuous welding, and long-term material processing.
The choice between a pulse laser and a continuous laser depends on the specific requirements of the application, including the need for precision, power, and heat management.
Advantages And Disadvantages Of Laser Cleaning Machine
Advantages Of Laser Cleaning Machine
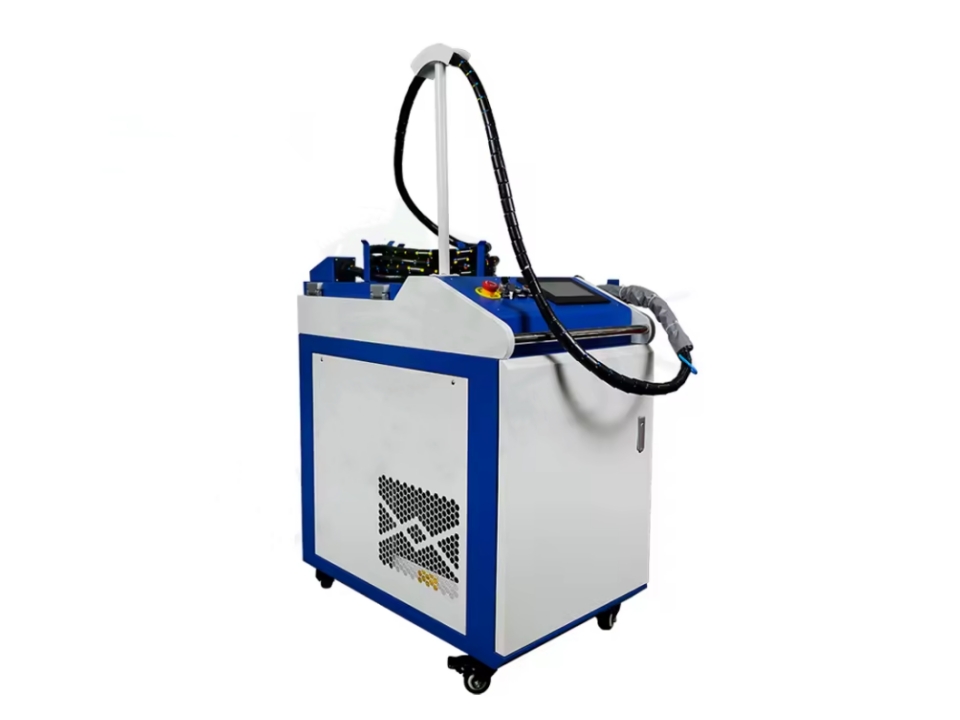
1. Precision and Selectivity
One of the most significant advantages of laser cleaning is its precision. Laser beams can be finely controlled to target specific areas, allowing for selective cleaning. This precision is particularly beneficial in applications requiring the removal of contaminants from delicate or intricate surfaces, such as in the aerospace and electronics industries.
2. Non-Contact Process
Laser cleaning is a non-contact process, meaning the laser beam does not physically touch the surface being cleaned. This reduces the risk of mechanical damage to delicate surfaces and makes the process suitable for cleaning sensitive materials, such as historical artifacts, artworks, and electronic components.
3. Environmentally Friendly
Laser cleaning is an environmentally friendly process compared to traditional cleaning methods like chemical cleaning or abrasive blasting. It does not require the use of hazardous chemicals or produce harmful waste. The process generates minimal secondary waste, usually in the form of fine particles that can be easily contained and disposed of.
4. Versatility
Laser cleaning is highly versatile and can be used on a wide range of materials, including metals, plastics, ceramics, and composites. This versatility makes it applicable across various industries, from automotive and aerospace to heritage conservation and semiconductor manufacturing.
5. Cost-Effectiveness
While the initial investment in laser cleaning equipment can be high, the long-term cost savings are substantial. The reduced need for consumables, minimal waste disposal costs, and lower maintenance requirements contribute to the overall cost-effectiveness of laser cleaning.
6. Improved Surface Quality
Laser cleaning often results in improved surface quality compared to traditional methods. It can remove contaminants without roughening the surface, preserving the integrity of the underlying material. This is particularly important in applications requiring high-quality surface finishes, such as in precision manufacturing and coating preparation.
7. Automation and Integration
Laser cleaning systems can be easily integrated into automated manufacturing processes. They can be combined with robotic arms and CNC machines to achieve high-speed, consistent, and repeatable cleaning. This automation enhances productivity and reduces labor costs.
Disadvantages of Laser Cleaning
1. High Initial Investment
The initial cost of acquiring laser cleaning equipment can be prohibitive for some businesses. High-power laser systems and their associated components, such as optics, cooling systems, and control units, represent a significant capital expenditure. This high upfront cost can be a barrier to entry, particularly for small and medium-sized enterprises.
2. Energy Consumption
Laser cleaning can be energy-intensive, especially for high-power applications. The energy requirements can lead to higher operational costs and may not be sustainable in areas with limited access to reliable power sources. Additionally, the need for effective cooling systems to manage the heat generated during the process can further increase energy consumption.
3. Safety Concerns
Laser cleaning involves high-intensity laser beams, which pose potential safety risks. Direct exposure to laser beams can cause severe injuries to the eyes and skin. Ensuring proper safety measures, such as protective eyewear, safety enclosures, and adherence to safety protocols, is crucial to mitigate these risks. The implementation of these safety measures can add to the overall cost and complexity of the process.
4. Surface Compatibility
While laser cleaning is versatile, it may not be suitable for all surfaces. Certain materials, particularly those with low thermal conductivity or high reflectivity, may not respond well to laser cleaning. For instance, some plastics and reflective metals can be challenging to clean effectively without causing damage. This limitation necessitates careful assessment and testing before adopting laser cleaning for specific applications.
5. Process Optimization
Achieving optimal cleaning results requires precise control of various parameters, such as laser wavelength, pulse duration, energy density, and scanning speed. This complexity demands a thorough understanding of the material properties and the cleaning requirements. Fine-tuning these parameters for each application can be time-consuming and may require specialized expertise.
6. Limited Accessibility
Laser cleaning systems can be bulky and require significant setup space, limiting their accessibility in certain environments. Portable laser cleaning solutions are available, but they may not offer the same power and effectiveness as their stationary counterparts. This limitation can restrict the use of laser cleaning in confined or hard-to-reach areas.
7. Potential Surface Damage
While laser cleaning is generally gentle on surfaces, there is a risk of surface damage if not properly controlled. Excessive laser power or prolonged exposure can lead to material ablation, melting, or thermal damage. Ensuring the appropriate settings and conducting preliminary tests are essential to prevent unintended damage.
Future Prospects of Laser Cleaning
The future of laser cleaning technology looks promising, with ongoing advancements aimed at enhancing its efficiency, versatility, and affordability. Researchers are exploring new laser sources, such as ultrafast lasers and high-power fiber lasers, to improve the precision and effectiveness of the cleaning process. Additionally, the integration of artificial intelligence and machine learning algorithms is expected to optimize process parameters and enable real-time monitoring and control.
As industries continue to prioritize sustainability and environmental responsibility, the demand for laser cleaning is likely to increase. The technology’s ability to provide a clean, efficient, and non-polluting solution aligns with the growing emphasis on green manufacturing practices. Furthermore, the development of compact and portable laser cleaning systems will expand its accessibility and applicability in various fields.
Conclusion
Laser cleaning is a revolutionary technology that offers numerous advantages, including precision, environmental friendliness, versatility, and cost-effectiveness. Its applications span a wide range of industries, from manufacturing and heritage conservation to electronics and healthcare. However, it also presents challenges such as high initial costs, energy consumption, safety concerns, and the need for process optimization.
Despite these challenges, the future of laser cleaning looks promising, with ongoing innovations poised to enhance its capabilities and broaden its applications. As industries strive for cleaner, more efficient, and sustainable solutions, laser cleaning is set to play a pivotal role in shaping the future of surface treatment and contamination removal.