Table of Contents
Driven by the increasing demand for efficiency, precision, and automation, the industrial landscape is constantly evolving. Among numerous advancements, the sheet metal industry has undergone significant transformation, with intelligent storage systems playing a crucial role in modern manufacturing processes. These systems aim to simplify material handling, optimize space utilization, and improve overall operational efficiency.
As one of the top metal automatic storage system brands, SC SHENCHONG has already delivered metal intelligent storage towers for sheet metal processing workshops in various industries around the world, and we have rich experience for clients to design and produce sheet metal CNC storage system.
This article will delve into the complexity of metal plate intelligent storage systems, exploring their components, advantages, and applications in today’s manufacturing environment. This article also focuses on how these systems can improve productivity and profitability, and explores the technological and strategic aspects that make them indispensable in modern industry.
Understanding The Role Of Sheet Metal In Industry
Sheet metal is a fundamental material in various industries, including automotive, aerospace, construction, electronics, and furniture manufacturing. Its versatility, durability, and ability to be easily shaped into different forms make it a critical raw material for many products. Sheet metal typically comes in large, heavy sheets, which can pose significant storage and handling challenges in manufacturing environments.
Traditional storage methods for sheet metal involved large warehouses or storage racks that required manual intervention for loading, unloading, and inventory management. However, manual handling of sheet metal is not only labor-intensive but also prone to errors and safety risks. This is where intelligent storage systems come into play.
What Is An Intelligent Storage System?
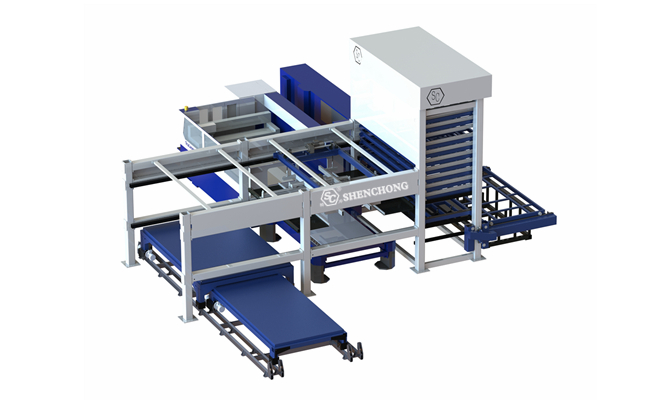
An intelligent storage system is an automated solution that is designed to store, organize, and retrieve materials, such as sheet metal, efficiently. These systems leverage advanced technologies like robotics, sensors, software, and machine learning algorithms to optimize storage and handling operations. They are typically integrated into larger manufacturing processes, helping companies reduce downtime, lower operational costs, and improve inventory management.
For sheet metal automation production, intelligent storage systems offer significant advantages by automating the movement of heavy and cumbersome sheets, reducing the need for manual labor and the potential for accidents. These systems can handle multiple types and sizes of sheet metal, organizing them in a way that maximizes space utilization while ensuring easy and quick retrieval when needed.
Applications of Sheet Metal Intelligent Storage Systems
- Automotive Industry: In the automotive industry, where precision and speed are critical, intelligent storage systems help manage the large volumes of sheet metal used in vehicle manufacturing. These systems ensure that the right materials are delivered to the production line on time, reducing the chances of delays and bottlenecks in the production process.
- Aerospace: The aerospace industry requires high-quality materials that are handled with extreme care to avoid defects. Intelligent storage systems help ensure that sheet metal used in aircraft production is stored and transported with precision, reducing the risk of damage and maintaining the integrity of the materials.
- Construction and Architecture: In construction, where sheet metal is used for everything from roofing to structural components, intelligent storage systems streamline the material handling process. These systems ensure that metal sheets are stored safely and delivered to construction sites as needed, improving project timelines and reducing material waste.
- Electronics Manufacturing: In electronics, sheet metal is often used for enclosures and components. Intelligent storage systems help manage the precise inventory levels required in this fast-paced industry, ensuring that materials are available for production without excess inventory taking up valuable space.
- Furniture Manufacturing: Furniture manufacturers that use sheet metal in their designs benefit from the space-saving and efficiency-enhancing capabilities of intelligent storage systems. These systems allow manufacturers to store large quantities of sheet metal in a compact space while ensuring quick and accurate retrieval when materials are needed for production.
Key Components of Sheet Metal Intelligent Storage Systems
A sheet metal intelligent storage system is made up of several key components that work together to ensure seamless operation:
- Automated Storage and Retrieval Systems (AS/RS): The heart of any intelligent storage system is the AS/RS, which automates the storage and retrieval of sheet metal. The AS/RS typically includes cranes, lifters, and conveyors that are programmed to transport metal sheets from one location to another. These systems can be customized to handle sheets of different dimensions and thicknesses, ensuring flexibility in operations.
- Robotics and Automation: Robotics plays a critical role in modern intelligent storage systems. Robots equipped with grippers, sensors, and advanced control systems can handle and transport sheet metal without human intervention. These robots are capable of navigating the storage facility, picking up metal sheets, and delivering them to the designated production area with high precision.
- Material Handling Equipment: In addition to AS/RS and robotics, intelligent storage systems often incorporate a range of material handling equipment, such as cranes, forklifts, and conveyors. These machines are usually automated and synchronized with the system’s control software to ensure smooth transportation of sheet metal within the storage facility.
- Software Integration: The backbone of any intelligent storage system is the software that controls it. This software integrates with the facility’s Enterprise Resource Planning (ERP) or Warehouse Management System (WMS) to monitor and manage the storage operations. It ensures that the right sheet metal is stored or retrieved based on real-time production requirements, and it tracks inventory levels, helping to avoid stockouts or overstock situations.
- Sensors and IoT: Sensors are embedded throughout the intelligent storage system to collect real-time data on material movement, storage conditions, and equipment performance. These sensors provide valuable insights, enabling predictive maintenance and ensuring that the system runs smoothly. IoT (Internet of Things) connectivity allows the system to communicate with other machinery and software, ensuring seamless integration with the larger manufacturing process.
- Safety Features: Intelligent storage systems for sheet metal incorporate various safety features, including sensors to detect human presence, collision avoidance systems, and emergency stop mechanisms. These safety features are crucial in preventing accidents, particularly in environments where large and heavy sheets of metal are being handled.
Benefits of Sheet Metal Intelligent Storage Systems
Improved Space Utilization: Traditional storage methods for sheet metal often result in inefficient use of space, with large areas of the warehouse dedicated to storing metal sheets. Intelligent storage systems, on the other hand, are designed to optimize vertical space, allowing for more compact storage solutions. This frees up valuable floor space for other operations, reducing the overall footprint of the storage area.
Enhanced Efficiency: The automation of the metal intelligent storage tower significantly improves efficiency in material handling operations. Metal plates can be automatically retrieved and delivered to the production line without human intervention, reducing the time it takes to move materials from storage to production. This leads to faster production cycles and reduced downtime.
Reduced Labor Costs: One of the most significant advantages of an intelligent storage system is the reduction in manual labor. By automating the storage and retrieval process, companies can reduce the number of workers required for these tasks. This not only lowers labor costs but also reduces the risk of workplace injuries, as workers are no longer required to handle heavy and cumbersome metal sheets manually.
Inventory Control and Accuracy: Intelligent storage systems are equipped with advanced inventory management capabilities, ensuring that the right materials are always available for production. The software tracks inventory levels in real-time and can automatically reorder materials when stock levels fall below a certain threshold. This reduces the risk of stockouts and ensures that production is not interrupted due to a lack of materials.
Improved Safety: Handling large sheets of metal manually can be hazardous, with the risk of injury from lifting, bending, or mishandling the material. Intelligent storage systems mitigate these risks by automating the movement and storage of sheet metal, keeping workers out of harm’s way. Additionally, the built-in safety features of these systems, such as sensors and emergency stops, further enhance workplace safety.
Reduced Material Damage: Manual handling of sheet metal can result in damage to the material, either through mishandling or accidental collisions. Intelligent storage systems are designed to handle materials with care, using robotics and automation to move sheets smoothly and safely. This reduces the risk of scratches, dents, and other forms of damage, ensuring that the material is in pristine condition when it reaches the production line.
Scalability: As businesses grow and their storage needs increase, intelligent storage systems can be easily scaled to accommodate more materials. These systems are highly customizable, allowing companies to add more storage modules, cranes, or robots as needed. This scalability makes intelligent storage systems a future-proof investment that can grow with the business.
Environmental Benefits: By optimizing storage space and improving the efficiency of material handling, intelligent storage systems can contribute to reducing energy consumption. The automation of processes also reduces waste, both in terms of time and materials, which can have a positive impact on a company’s environmental footprint.
How To Choose A Sheet Metal Intelligent Storage System?
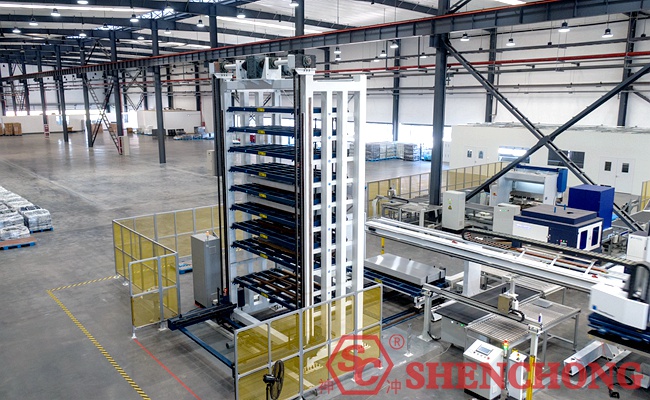
Selecting the right sheet metal intelligent storage system (SMISS) for your facility is a critical decision that can have a lasting impact on operational efficiency, safety, and profitability. Given the range of available options, choosing the ideal system requires a comprehensive evaluation of your specific business needs, technical requirements, and long-term goals.
This guide outlines key factors to consider when buying a sheet metal intelligent storage system to ensure the right fit for your operations.
1. Assess Your Storage Needs and Capacity
Understanding your current and future storage needs is the first and most crucial step when choosing an intelligent storage system for sheet metal. Begin by analyzing:
- Volume of Sheet Metal: Calculate the volume of sheet metal you handle daily, weekly, or monthly. Consider both current needs and expected future growth. If your company plans to scale, ensure that the system can accommodate additional storage without excessive modifications.
- Material Types and Sizes: Different systems cater to specific material dimensions. Determine the size, weight, and variety of sheet metal you handle—whether they are thin sheets, large plates, or custom-sized pieces. The system you choose should be able to efficiently store and retrieve materials of varying thicknesses and dimensions.
- Turnover Rate: High turnover rates (frequent access to materials) require fast, efficient systems that can quickly retrieve and transport sheet metal. A lower turnover rate may allow for a system with slower response times but higher capacity.
- Warehouse Space Constraints: Consider the available warehouse or facility space. If your floor space is limited, look for systems that optimize vertical storage. Many intelligent storage systems are designed to maximize cubic space, reducing the overall footprint of your storage area.
2. Automation and Integration Capabilities
When selecting a sheet metal intelligent storage system, the level of automation and its ability to integrate with your existing infrastructure are critical:
- Level of Automation: Decide how much automation you need based on your operations. Systems can range from semi-automated (requiring some manual intervention) to fully automated, where robots and conveyors handle all storage and retrieval processes. Full automation minimizes human labor and increases speed and precision, but it might come at a higher cost.
- Integration with Existing Systems: Your storage system should seamlessly integrate with existing Warehouse Management Systems (WMS) or Enterprise Resource Planning (ERP) software. Integration ensures that the storage system communicates with other parts of your operation, such as inventory control and production planning, ensuring real-time data flow and synchronization.
- Automation Flexibility: Some systems offer flexible automation, allowing you to adjust automation levels depending on changing production volumes. Look for systems that provide upgrade options to increase automation levels over time as your needs evolve.
- Machine Compatibility: Ensure that the storage system is compatible with other machines in your production chain, such as CNC cutting machines, lasers, or punch presses. Integrated systems will streamline production processes, ensuring that material handling is efficient from storage to fabrication.
3. System Speed and Efficiency
Efficiency is key in any intelligent storage system. The faster and more reliable the system, the more productivity gains you will experience:
- Retrieval Speed: Some intelligent storage systems prioritize retrieval speed, which is crucial if you need frequent and fast access to your sheet metal. High-speed systems that quickly locate, retrieve, and deliver materials can significantly reduce production lead times.
- Cycle Time Optimization: Assess the cycle time for material retrieval and delivery. The system should be able to handle high-demand periods and operate with minimal bottlenecks. This is especially important if you are operating in just-in-time (JIT) production environments.
- Throughput Capabilities: The throughput refers to the amount of sheet metal the system can handle within a given timeframe. If your operations require constant movement of materials to and from storage, a system with higher throughput is necessary to keep pace with production demands.
4. Customization and Modularity
Different businesses have varying storage needs, and a one-size-fits-all solution rarely works well. Consider these aspects:
- Customizable Layouts: Look for storage systems that can be customized to your facility’s layout and workflow. Some intelligent systems allow for modular design, where racks, shelves, and robots can be arranged or expanded based on your facility’s specific configuration.
- Expandable Systems: Choose a system that can grow with your business. Modular systems allow for future expansions without needing to overhaul the entire infrastructure. This is important if your sheet metal handling needs increase over time.
- Custom Handling Features: Some systems offer custom handling features that accommodate unique sheet metal types or production processes. If your operation requires handling of fragile or coated sheets, for example, ensure that the system has soft-handling mechanisms to prevent material damage.
5. Safety and Ergonomics
Given the risks involved in handling large, heavy sheets of metal, safety should be a top priority:
- Safety Features: Intelligent storage systems should include comprehensive safety features such as sensors, cameras, collision avoidance systems, emergency stop buttons, and warning signals. These features prevent accidents and protect both workers and equipment.
- Ergonomics: Reducing physical strain on employees is essential. Automated systems minimize manual handling, but for systems with partial manual intervention, ergonomic design ensures that workers can safely and easily access sheet metal without risking injury.
- Compliance with Regulations: Ensure that the system complies with relevant safety standards and regulations, such as Occupational Safety and Health Administration (OSHA) guidelines in the U.S., or other applicable regional safety standards.
6. Cost Considerations
The cost of an intelligent storage system is a major factor in decision-making, but it should be weighed against long-term operational savings and benefits:
- Initial Investment: Determine the upfront cost of purchasing and installing the system, including any necessary infrastructure adjustments, such as reinforcement of floors for heavy metal storage or changes to your facility layout.
- Return on Investment (ROI): Calculate the potential ROI by considering the system’s impact on productivity, labor savings, reduced material damage, and operational efficiency. While the initial investment might be high, long-term savings in labor and efficiency typically justify the cost.
- Maintenance Costs: Regular maintenance is required to ensure that automated systems run smoothly. Consider the ease of maintenance and the cost of parts and service contracts. Systems that require frequent downtime for maintenance may not be ideal for high-demand operations.
- Energy Efficiency: Many intelligent storage systems incorporate energy-efficient features. Assess the system’s energy consumption and consider how it will impact your operational costs. Energy-efficient systems may have a higher initial cost but can reduce long-term energy expenses.
7. Vendor Reputation and Support
The company you purchase your intelligent storage system from should be a trusted partner. Look for the following in your vendor:
- Reputation and Experience: Research the vendor’s reputation and experience in the sheet metal storage industry. Vendors with a proven track record and expertise are more likely to provide reliable products and solutions.
- After-Sales Support: Consider the level of after-sales support, including installation, training, maintenance, and technical support. A vendor that offers comprehensive training for your team ensures that the system is used correctly and efficiently.
- Service Contracts and Warranties: Ensure that the system comes with a solid warranty and that the vendor offers service contracts for ongoing support. Reliable after-sales service is essential for minimizing downtime and maintaining system efficiency.
- Customization Services: Some vendors offer custom engineering solutions tailored to your facility’s specific requirements. If your storage needs are unique, choose a vendor with the capability to design and implement custom solutions.
Conclusion
Sheet metal intelligent storage systems represent a transformative advancement in material handling and storage within the manufacturing sector. By automating the storage and retrieval of sheet metal, these systems offer significant benefits, including improved efficiency, reduced labor costs, enhanced safety, and optimized space utilization. They are an essential component of modern manufacturing facilities, particularly in industries that rely heavily on sheet metal for production.
As industries continue to evolve and embrace automation, the role of intelligent storage systems will only grow in importance. With their ability to streamline operations, reduce waste, and improve overall productivity, these systems are a worthwhile investment for any company looking to enhance its manufacturing capabilities.
SC Machinery is a professional sheet metal intelligent storage system manufacturer. We has the strong design and manufacture ability for clients to produce the automatic storage system to meet the storage requirements. Please feel free to contact with us for more information about automatic metal storage tower.