Table of Contents
Laser welding is a versatile and precise welding process used in various industries for joining metal parts. The process utilizes a concentrated laser beam to melt and fuse materials together, producing strong and high-quality welds. Laser welding machines are the equipment used to carry out this process, leveraging advanced laser technology to achieve precision and efficiency. This comprehensive article explores the various aspects of laser welding machines, including their operation, components, advantages, applications, types, maintenance, and future trends.
What Is Laser Welding?
Laser welding is a non-contact process that uses a high-intensity laser beam to create a weld between two materials. The laser beam is focused onto a small area, generating enough heat to melt the materials, which then solidify to form a strong joint. This process is known for its precision, speed, and ability to weld small and intricate parts with minimal distortion.
Laser Welding Working Principle
Laser welding is a welding method using high energy density laser beam as heat source, and its principle mainly includes the following aspects:
- Optical focusing: laser welding machines generate laser beams through lasers and focus them with optical elements such as lenses or mirrors to concentrate laser energy on solder joints.
- Heat transfer: when a laser beam strikes the surface of the work piece, the laser energy is absorbed and converted into heat energy. Heat is transmitted along the metal portion of the welded joint by heat transfer, raising the temperature of the metal.
- Melting and mixing: when the metal surface is heated high enough, the metal begins to melt and form a molten pool. Under the action of laser beam, the molten pool spreads and mixes rapidly to achieve the connection of metal joints.
- Cooling and freezing: after stopping the irradiation of the laser beam, the molten pool gradually cools and forms a welded joint during the freezing process. As it solidifies, metal molecules rearrange and crystallize to form strong solder connections.
- Laser welding has the advantages of high energy density, small heat input, fast welding speed and small heat affected zone, and is especially suitable for welding micro parts and parts with poor accessibility.
Components Of A Laser Welding Machine
Laser Source
- Types of Lasers:Common types include CO2 lasers, Nd(Neodymium-doped Yttrium Aluminum Garnet) lasers, and fiber lasers. Each type has its advantages, depending on the application.
- Function:The laser source generates the laser beam used for welding. It is a critical component that determines the machine’s power and efficiency.
Optics
- Lenses and Mirrors:Used to focus and direct the laser beam onto the workpiece. High-quality optics ensure precise control of the laser beam.
- Beam Delivery System:Includes components such as optical fibers and beam guides that transport the laser beam from the source to the welding area.
Workpiece Handling System
- Positioning Table:A platform where the workpiece is placed. It can be stationary or equipped with movement capabilities to align the workpiece with the laser beam.
- Clamping Mechanism:Secures the workpiece in place to prevent movement during welding.
Control System
- CNC Control:Computer Numerical Control (CNC) systems are often used to automate the welding process, allowing for precise control over the welding parameters and movement of the laser beam.
- Software Interface:Provides an interface for operators to input welding parameters and monitor the process.
Cooling System
- Water or Air Cooling:Laser welding generates significant heat, requiring a cooling system to prevent overheating of the laser source and optics.
Protective Enclosure
- Safety Measures:Enclosures protect operators from exposure to laser radiation and contain any harmful fumes or debris generated during welding.
Types of Laser Welding Machines
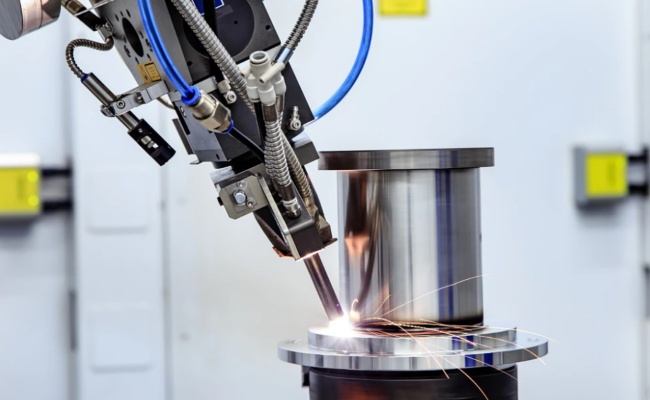
Fiber Laser Welding Machines
- Operation:Uses a fiber laser source, which delivers the laser beam through an optical fiber.
- Advantages:High beam quality, energy efficiency, and suitability for welding a wide range of materials.
CO2 Laser Welding Machines
- Operation:Uses a CO2 laser source, which generates a laser beam by electrically stimulating a gas mixture.
- Advantages:High power output and ability to weld thick materials.
ND Laser Welding Machines
- Operation:Uses a ND laser source, which produces a laser beam by doping a Yttrium Aluminum Garnet crystal with Neodymium.
- Advantages:High peak power and suitability for pulsed welding applications.
Diode Laser Welding Machines
- Operation:Uses a diode laser source, which generates a laser beam through semiconductor diodes.
- Advantages:Compact size, energy efficiency, and ability to weld small and delicate components.
Advantages and Disadvantages Of Laser Welding Machine
Laser Welding Machine Advantages
Laser welding machines offer numerous advantages that make them highly desirable for various industrial applications. These advantages include precision, speed, versatility, and overall quality, among others. Here’s an in-depth look at the advantages of laser welding machines:
Precision And Accuracy
- Tight Tolerances:Laser welding machines can achieve extremely tight tolerances, which is crucial for applications requiring high precision.
- Small Heat-Affected Zone (HAZ):The laser beam is highly focused, creating a small HAZ. This minimizes thermal distortion and reduces the risk of damaging adjacent materials.
High Welding Speed
- Increased Productivity:Laser welding can be performed at high speeds, significantly increasing productivity and reducing cycle times.
- Automation Capabilities:The process can be easily automated using CNC systems and robotics, further enhancing speed and consistency.
Versatility
- Material Compatibility:Laser welding is compatible with a wide range of materials, including various metals (steel, aluminum, titanium, etc.), alloys, and even some plastics.
- Complex Geometries:The process can weld intricate and complex geometries that are difficult to achieve with traditional welding methods.
Superior Weld Quality
- Strong Welds:Laser welding produces high-strength welds with excellent mechanical properties, ensuring durability and reliability.
- Clean and Aesthetic Welds:The welds are often clean and aesthetically pleasing, with minimal finishing required. This is especially important for applications where appearance matters, such as in the automotive and jewelry industries.
Minimal Distortion
- Reduced Thermal Stress:The concentrated heat source minimizes thermal stress and warping, maintaining the integrity of the workpiece.
- Precision Control:The precise control of the laser allows for minimal distortion even in thin materials.
Flexibility
- Non-Contact Process:Laser welding is a non-contact process, meaning there is no physical contact between the tool and the workpiece. This reduces wear and tear on the equipment and allows for welding in hard-to-reach areas.
- Adjustable Parameters:The process parameters (laser power, speed, focus, etc.) can be easily adjusted to accommodate different materials and thicknesses.
Energy Efficiency
- Efficient Energy Use:Laser welding machines, especially those using fiber lasers, are highly energy-efficient. They convert a high percentage of electrical energy into laser light.
- Reduced Operational Costs:The energy efficiency translates to lower operational costs over time.
Automation And Integration
- Seamless Integration:Laser welding systems can be seamlessly integrated into automated production lines, enhancing overall manufacturing efficiency.
- Robotic Welding:The precision and control of laser welding make it ideal for robotic welding applications, allowing for continuous operation and high throughput.
Reduced Consumables
- Minimal Consumable Use:Unlike traditional welding methods that require filler materials and electrodes, laser welding often requires minimal or no consumables.
- Cost Savings:Reduced use of consumables leads to cost savings and less frequent need for restocking.
Enhanced Safety and Cleanliness
- Safety Features:Modern laser welding machines are equipped with safety features such as protective enclosures and interlocks to protect operators from harmful laser radiation.
- Cleaner Process:The process generates fewer fumes and spatter compared to traditional welding methods, resulting in a cleaner working environment.
Environmental Benefits
- Eco-Friendly:The high efficiency and precision of laser welding reduce waste and energy consumption, making it an environmentally friendly option.
- Sustainable Manufacturing:Laser welding supports sustainable manufacturing practices by minimizing material waste and improving energy efficiency.
Disadvantages Of Laser Welding Machine
While laser welding machines offer numerous advantages, they also come with certain disadvantages that need to be considered. Here are some of the key disadvantages of laser welding machines:
High Initial Cost
- Expensive Machinery: Laser welding machines are generally more expensive than traditional welding equipment due to their advanced technology and components.
- Cost of Laser Sources: High-quality laser sources, such as fiber lasers and Ndlasers, add to the overall cost.
- Complex Installation: Setting up a laser welding system can be complex and requires specialized knowledge.
- Infrastructure Requirements: The installation may require additional infrastructure, such as cooling systems, protective enclosures, and advanced ventilation.
Technical Complexity
- Specialized Training: Operators need specialized training to handle and program laser welding machines.
- Complex Programming: Setting up and programming the CNC control system can be complex, requiring expertise in CAD/CAM software and welding parameters.
- Maintenance Expertise: Maintenance of laser welding machine requires specialized knowledge and skills.
- Regular Calibration: Frequent calibration and alignment of the laser system are necessary to maintain precision.
Sensitivity To Joint Preparation And Fit-Up
- Joint Preparation: Laser welding requires precise joint preparation and alignment. Even slight deviations can result in poor weld quality.
- Fit-Up Tolerance: The process has low tolerance for gaps and misalignment, necessitating precise fixturing and positioning.
Limitations In Material Thickness
- Limited Thickness Range: Laser welding is more suitable for thin to moderately thick materials. Welding very thick materials may require multiple passes or preheating.
- Heat Dissipation: Managing heat dissipation becomes challenging with thicker materials, potentially affecting weld quality.
Safety Concerns
- Exposure Risk: Laser welding poses a risk of exposure to harmful laser radiation, which can cause severe eye and skin injuries.
- Protective Measures: Comprehensive safety measures, such as protective enclosures, safety goggles, and laser safety protocols, are essential.
- Harmful Fumes: The process can generate harmful fumes and particulates, requiring effective ventilation and fume extraction systems.
- Debris: High-intensity laser beams can create debris and spatter, posing additional safety hazards.
Limited Material Compatibility
- Reflectivity Issues: Highly reflective materials, such as aluminum and copper, can reflect the laser beam, making welding more difficult and less efficient.
- Special Coatings: Special coatings or surface treatments may be required to improve the weldability of reflective materials.
- Alloy Sensitivity: Some alloys may have specific challenges related to cracking, porosity, or metallurgical changes during laser welding.
While laser welding machines offer significant advantages in terms of precision, speed, and versatility, they also present several challenges. The high initial cost, technical complexity, sensitivity to joint preparation, and safety concerns are some of the primary disadvantages that need to be addressed. Additionally, the limitations in material thickness, material compatibility issues, and environmental requirements must be considered when deciding to implement laser welding technology.
Applications Of Laser Welding Machines
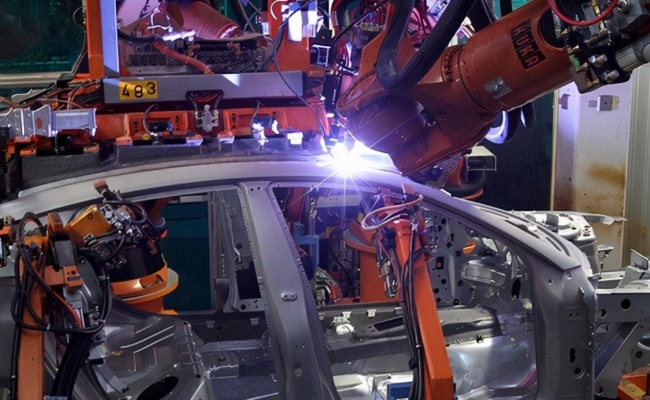
Automotive Industry
- Component Welding:Used for welding various automotive components such as engine parts, transmission components, and exhaust systems.
- Body Construction:Laser welding is employed in the construction of car bodies, providing strong and lightweight joints.
Aerospace Industry
- Aircraft Components:Used for welding critical aircraft components, including turbine blades, fuel tanks, and structural parts.
- Precision:The high precision of laser welding ensures the integrity and performance of aerospace components.
Electronics Industry
- Micro-Welding:Laser welding is ideal for micro-welding applications in electronics, such as connecting tiny wires and assembling delicate components.
- Battery Manufacturing:Used in the production of batteries, ensuring strong and reliable connections.
Medical Device Industry
- Implants and Instruments:Laser welding is used to manufacture medical implants and surgical instruments, providing precise and clean welds.
- Bio-compatibility:The process ensures that welds are bio-compatible and meet stringent medical standards.
Jewelry And Watchmaking
- Fine Welding: Laser welding is used for fine welding applications in jewelry and watchmaking, allowing for intricate designs and repairs.
- Aesthetic Quality: Produces high-quality welds that enhance the aesthetic appeal of jewelry and watches.
Energy Industry
- Solar Panels: Used in the production of solar panels, ensuring durable and efficient connections.
- Wind Turbines: Laser welding is employed in the manufacture of wind turbine components, providing strong and reliable joints.
Operation Of A Laser Welding Machine
Setup
- Preparation:The workpiece is cleaned and prepared for welding to ensure good weld quality.
- Positioning:The workpiece is placed on the positioning table and secured with clamps.
Programming
- Input Parameters: Operators input specific welding parameters such as laser power, speed, pulse duration, and focal position into the control system.
- Path Programming: The welding path is programmed, often using CAD/CAM software, to guide the laser beam along the desired weld seam.
Welding Process
- Beam Generation: The laser source generates the laser beam, which is directed through the optics to the welding area.
- Melting and Fusing: The focused laser beam melts the material at the joint, creating a molten pool that solidifies to form a weld.
- Movement Control: The CNC system controls the movement of the laser beam and/or the workpiece to follow the programmed welding path.
Post-Welding
- Cooling: After welding, the joint is allowed to cool and solidify completely.
- Inspection: The weld is inspected for quality, checking for defects such as porosity, cracks, or incomplete fusion.
Maintenance Of Laser Welding Machines
Regular Cleaning
- Optics: Clean the lenses, mirrors, and other optical components to ensure optimal laser beam quality.
- Work Area: Keep the work area clean and free of debris to prevent contamination of the laser beam and workpiece.
Cooling System Maintenance
- Check Coolant Levels: Regularly check and refill coolant levels to prevent overheating of the laser source and optics.
- Inspect Cooling System: Inspect the cooling system for leaks and ensure it is functioning properly.
Calibration And Alignment
- Laser Calibration: Periodically calibrate the laser source to ensure it is delivering the correct power and beam quality.
- Optical Alignment: Check and adjust the alignment of the optical components to maintain precise beam delivery.
Software Updates
- Update Control Software: Keep the CNC control software up to date to ensure access to the latest features and improvements.
- Backup Programs: Regularly back up welding programs to prevent data loss and ensure quick recovery in case of software issues.
Future Trends Of Laser Welding
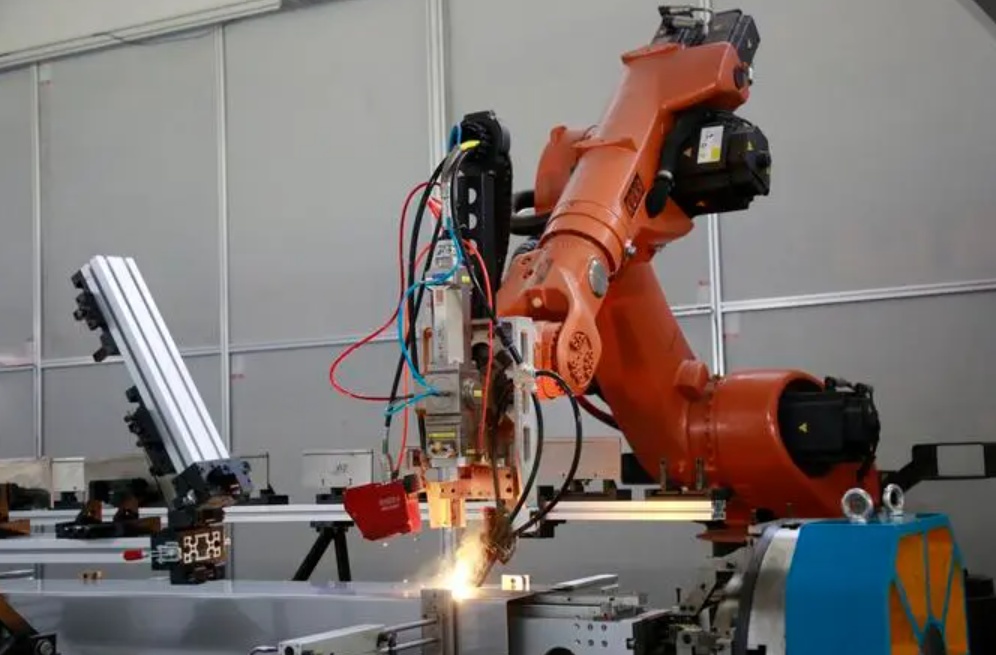
Advancements In Laser Technology
- Higher Power Lasers: Development of higher power laser sources for welding thicker and more challenging materials.
- Improved Beam Quality: Advances in laser technology to enhance beam quality and precision.
Industry 4.0 Integration
- IoT Connectivity: Integration of IoT (Internet of Things) for real-time monitoring and control of laser welding processes.
- Data Analytics: Use of data analytics to optimize welding parameters and improve quality and efficiency.
Automation and Robotics
- Robotic Integration: Increased use of robotic systems for automated laser welding, reducing manual labor and increasing productivity.
- Collaborative Robots: Development of collaborative robots (cobots) that can work alongside human operators in laser welding applications.
Sustainability
- Energy Efficiency: Continued focus on improving the energy efficiency of laser welding machines to reduce environmental impact.
- Green Manufacturing: Adoption of sustainable manufacturing practices, including the use of eco-friendly materials and processes.
Conclusion
Laser welding machines are a cornerstone of modern manufacturing, offering precision, speed, and versatility in joining metal parts. Their advanced technology and automation capabilities make them indispensable in various industries, from automotive and aerospace to electronics and medical devices. Proper maintenance and staying abreast of future trends ensure that laser welding machines continue to meet the evolving needs of the manufacturing industry. As technology advances, laser welding will undoubtedly play an even more significant role in shaping the future of manufacturing.
SC Machinery is a rich experienced laser cutting machine and automatic sheet metal production line manufacturer, which has already offered hundreds of sheet metal automation solutions to clients around the world. If you need laser cutting or laser welding machine or production line solution, please feel free to contact with us.