Table of Contents
Indonesian customers ordered a Servo Hybrid CNC Press Brake Machine WDK 200T 4000MM 6+1 ESA 860. The 200ton 4meter oil-electric hybrid press brake machine is a large bending machine commonly used in the metal processing industry, especially for bending heavy plates. Indonesia servo press brake combines oil pressure and electric drive systems, has high efficiency and precision, and is suitable for bending various metal plates.
Configuration of Indonesia servo press brake machine
- WDK hybrid series servo press brake
- 200 tons 4000 mm
- 6+1 axes
- ESA 860 CNC system
- With follow-up support
- Install electrical cabinet air conditioner
Technical features of servo hybrid press brakes
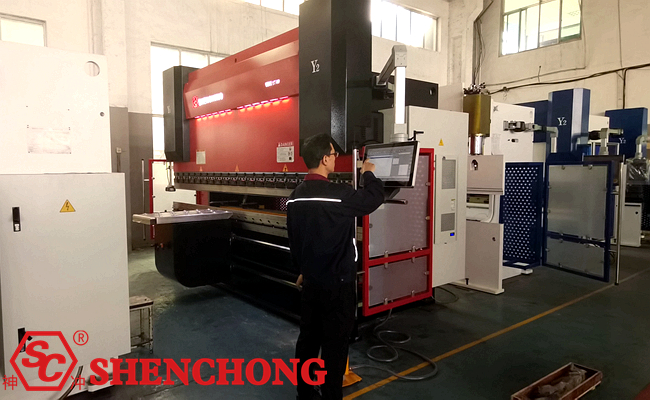
Hybrid drive:
Servo Hybrid CNC Press Brake Machine combines hydraulic and electric technologies. The electric drive system can improve the efficiency and response speed of the equipment, while the hydraulic system is responsible for providing high-pressure, large-tonnage bending force. This combination provides higher stability, precision and energy saving.
High-precision control:
Accurate bending angles and repeated positioning are achieved through the CNC system (CNC). The hydraulic system provides large-tonnage bending force, while the electric drive makes the stroke smoother and the control more precise.
Energy saving and environmental protection:
The electric drive part can adjust the working state according to needs, effectively reducing energy consumption, which is more energy-saving and environmentally friendly than traditional fully hydraulic bending machines.
Easy operation:
Equipped with an advanced CNC system, it can easily set and adjust the bending parameters, with a high degree of automation, reducing manual intervention, and improving work efficiency and processing accuracy.
Low noise and low vibration:
Due to the optimized design of the electric part, the noise and vibration of the equipment are reduced, which improves the comfort of operation.
Advantages of bending follow-up support
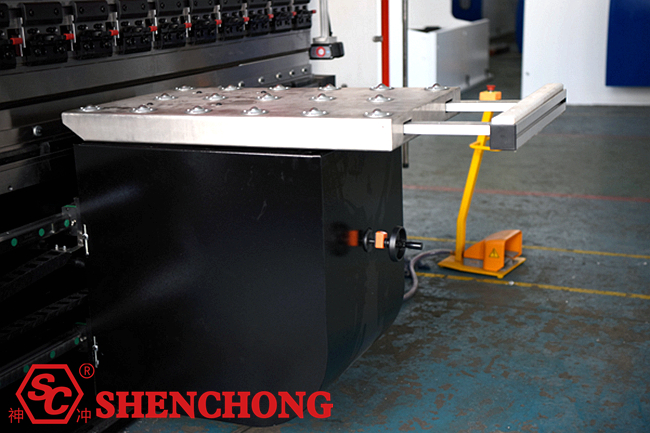
The advantages of Indonesia servo press brake with a follow-up support are mainly reflected in improving production efficiency, processing accuracy and operational safety. The follow-up support system usually refers to a device that can automatically adjust the position of the back gauge, automatically track and adjust according to the size of the plate or processing requirements, and ensure the positioning accuracy of the plate during the bending process.
The following are the main advantages of a bending machine equipped with a follow-up support system:
1) Improve production efficiency
Automatic adjustment:
The follow-up support system can automatically adjust the position of the back gauge according to the length of the plate and processing requirements, which means that the operator does not need to manually adjust the position of the back gauge each time, thereby reducing the time of manual operation and improving production efficiency.
Reduced manual intervention:
The operator only needs to set the basic parameters, and the subsequent adjustments will be automatically completed by the support system, which effectively reduces the intervention time of the operator, allowing the equipment to complete a series of identical or similar tasks faster, thereby improving the processing speed.
2) Ensure processing accuracy
Precisely control positioning:
The follow-up support system can accurately control the position and feed depth of the plate, avoid positioning deviations caused by improper manual adjustment or equipment errors, and ensure that each product can achieve the required bending accuracy.
Reduce errors:
Automatic adjustment can more accurately match the bending angle of the machine, the thickness of the plate, the bending requirements, etc., thereby reducing the deviation that may occur in the plate during the bending process and improving processing accuracy.
3) Enhance safety
Reduce human contact:
In the traditional manual operation process, the operator needs to adjust the back gauge frequently, which may cause danger to people approaching moving parts. The follow-up support system reduces manual intervention, reduces the contact between people and equipment, and improves operational safety.
Avoid plate sliding:
In some cases, the plate may slide or shift during bending, resulting in reduced processing accuracy. The follow-up support can adjust the position of the back gauge in real time to ensure that the plate remains stable throughout the bending process and is not prone to sliding.
4) Reduce equipment maintenance and wear
Reduce human operation errors:
Since there is no need to adjust the back gauge frequently, the excessive operation and wear of the equipment are reduced, the risk of damage caused by improper human operation is reduced, and the service life of the equipment is extended.
Maintain equipment stability:
The automated follow-up system performs well in accuracy and repeatability, which helps to reduce the vibration and load of the equipment during operation and improve the long-term stability of the equipment.
5) Optimize process flow
Precise coordination of multiple bends:
For some workpieces that require multiple bends, the follow-up support system can accurately control the positioning of each bend to ensure that each bend can be smoothly docked with the previous bend, and the finished product will not be unqualified due to the wrong position of the back gauge.
Improve workpiece consistency:
The automated adjustment process allows the bending processing of each workpiece to maintain consistency, especially for batch production, to ensure that the quality of each product is highly consistent.
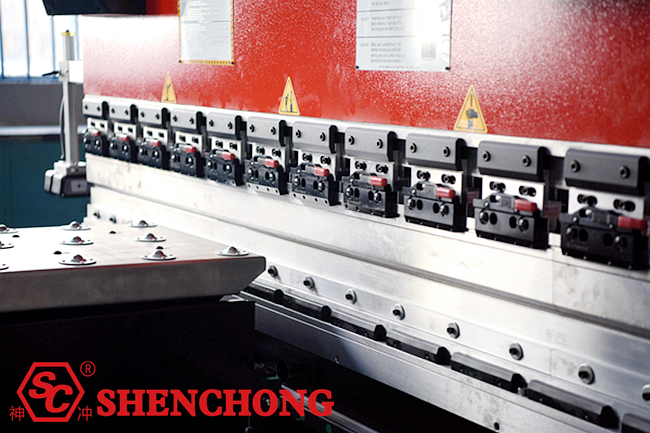
6) Easy operation
Reduce the complexity of manual operation:
The operator only needs to set the relevant parameters, and the support system will automatically adjust the position according to the size of the plate or the bending requirements, reducing cumbersome operation steps and improving the convenience of operation.
Lower technical requirements:
Even operators with low technical levels can complete precise processing operations through simple settings, reducing the requirements for operator skills.
7) Improve product quality
Reduce the impact of human factors:
Traditional manual adjustment of the back gauge is easily affected by human factors, such as judgment errors or improper operation, resulting in unstable product quality. The automatic adjustment of the follow-up support system ensures the consistency of the processing process and can greatly improve the overall quality of the product.
8) Improve competitiveness
Improve production efficiency and quality:
The improvement in production efficiency and product quality of the bending machine equipped with follow-up support enables enterprises to produce high-quality products that meet customer needs with higher efficiency, thereby improving market competitiveness.
9) Reduce the burden on operators
Reduce the workload of operators:
The automatic adjustment of the follow-up support system eliminates the need for operators to make frequent adjustments, reduces their workload, reduces operator fatigue, and improves work comfort.
The advantage of using follow-up support system is that it can greatly improve production efficiency, processing accuracy and equipment safety, reduce manual intervention, reduce errors, extend equipment life, and improve the overall automation of the production line. For companies that produce in large quantities or require high-precision processing, installing a follow-up support system will be an important measure to improve process level and competitiveness.
In addition to this follow-up device installed on the Indonesia servo press brake, SC Machinery can also provide customers with independent sheet bending follower devices, which can be used with mainstream CNC press brake machines on the market.
The role of adding electrical cabinet air conditioners
There are several very important roles in installing electrical cabinet air conditioners on bending machines, mainly to protect the electronic control system, extend the life of the equipment, and improve work efficiency.
The following are the specific roles and reasons:
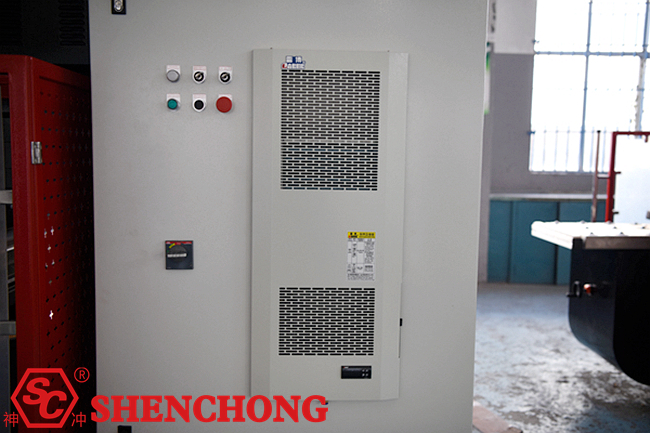
1) Reduce temperature and protect the electronic control system
The electronic control system is sensitive to temperature:
The electronic control system of the bending machine (such as PLC, inverter, contactor, etc.) usually uses electronic components, which are prone to overheating, damage or failure in high temperature environments. Excessive temperature in the electrical cabinet will cause the working stability of electrical components to decrease, and may even cause equipment shutdown or failure.
Air conditioning reduces temperature:
By adding air conditioning, the temperature in the electrical cabinet can be effectively reduced to ensure that the control system and electrical components work within a suitable temperature range, thereby avoiding equipment failure or damage caused by overheating.
2) Prevent moisture and dust
The hazards of moisture and dust:
In industrial environments, especially metal processing workshops, moisture and dust often cause damage to electrical control systems. Moisture may cause short circuits and corrosion of electrical components, while dust may accumulate on circuit boards and contactors, affecting the normal operation of equipment.
Air conditioning keeps things dry and clean:
Air conditioning helps reduce moisture in the air and keeps it dry by controlling the humidity in the electrical cabinet. At the same time, air conditioning can reduce the dust in the air from entering the electrical cabinet, thereby extending the service life of the equipment.
3) Improve the working efficiency and stability of electrical components
Stable operation:
The working efficiency of electrical components is closely related to temperature. Air conditioning helps keep the temperature of the electronic control system within a stable range, which can ensure the stability and working efficiency of each electrical component and avoid overcurrent or voltage fluctuations caused by overheating.
Avoid automatic protection power failure:
Most electrical equipment will automatically enter protection mode or shut down when overheating to prevent damage. Air conditioning helps prevent excessive temperatures and reduce protection shutdowns caused by abnormal temperatures.
4) Extend equipment life
Reduce the frequency of failures:
Temperature, humidity and dust will accelerate the aging and wear of electrical components. By maintaining a suitable working environment, air conditioning can reduce the damage of these factors to the electrical system, thereby extending the service life of the equipment.
Save maintenance costs:
By reducing the damage to electrical components, air conditioning helps reduce the frequency and cost of maintenance, thereby improving the operating efficiency of the equipment.
5) Improve production efficiency
Stable operating environment:
The equipment operates in an environment with suitable temperature, which can maintain a continuous and efficient working state and avoid production stagnation caused by equipment failure. Especially in high-intensity production, the stability and efficiency of the equipment are crucial.
Reduce downtime:
If the equipment has a shutdown problem caused by overheating, the production efficiency will be greatly reduced. Air conditioning can effectively avoid this situation and ensure the continuous operation of the equipment.
6) Follow industry standards and specifications
Meet industry requirements:
In some countries and regions, industrial equipment has clear requirements for the working environment of the electronic control system, including temperature and humidity control. By installing air conditioners, it is easier for equipment to meet relevant industry standards and safety specifications.
Improve the production standards of the company:
Some customers may require equipment to meet specific operating standards when selecting suppliers, especially in high temperature and high humidity environments. Installing air conditioners can also increase the market competitiveness of equipment.
7) Reduce energy consumption and improve energy efficiency
Energy efficiency advantages of air conditioners:
Modern industrial air conditioners usually have a high energy efficiency ratio (COP), which can maintain a stable temperature environment at a lower energy consumption, thereby reducing energy consumption, and indirectly improving the overall energy efficiency of the bending machine by optimizing the working state of electrical equipment.
The main purpose of installing an air conditioner in an electrical cabinet is to protect electrical components, reduce failure rates, extend service life, and improve equipment efficiency. Air conditioning plays a vital role, especially in hot, humid or dusty environments. For bending machines that need to run continuously and efficiently for a long time, the role of air conditioning is not only to improve the stability of the equipment, but also to help reduce maintenance costs and ensure the smooth operation of the production line.
This Indonesia servo press brake machine is suitable for applications that require high precision and large tonnage processing, especially for the processing of medium and thick plates. Combining the advantages of hydraulic and electric systems, it can provide higher work efficiency, lower energy consumption and better processing accuracy, and is widely used in multiple industries.