Table of Contents
In the context of increasingly fierce market competition and rising labor costs, the market has higher requirements for efficient, energy-saving, and environmentally friendly sheet metal manufacturing equipment. Reducing product production and manufacturing costs is a problem that enterprises have to face, and “energy conservation, consumption reduction, and green environmental protection” have become their preferred themes. The power consumption of equipment has become an important part of production costs for enterprises, and reducing the energy consumption of bending machines has become one of the effective ways for enterprises to reduce costs and improve product competitiveness. With the continuous development of industrial technology and increasingly fierce market competition, traditional electro-hydraulic CNC press brake machines have become more and more prominent in terms of throttling, heating, and high reactive power consumption due to barriers in control principles. Hybrid servo press brake machines will become the most popular bending machine types in the market. This article will introduce the hybrid servo press brake machine advantages and compare this series with the traditional hydraulic press brakes.
Introduction to Electric Servo Hybrid Press Brake
The hybrid servo press brake machine is equipped with two independent stainless steel oil tanks, which are simple and compact in structure, easy to clean, and reduce secondary pollution of hydraulic oil. To achieve efficient and stable bending efficiency, the main oil cylinder adopts a special acceleration cylinder structure design. The CNC system drives the oil cylinder through two servo power units and controls the synchronous operation of the bending machine oil cylinder through the detection and feedback of the grating ruler (or magnetic grating ruler), achieving high-precision machining of the workpiece. The servo hybrid press brake machine has the characteristics of high speed, energy saving, low noise and environmental protection.
Servo Hybrid Press Brake Vs Electro-Hydraulic Synchronous CNC Press Brake
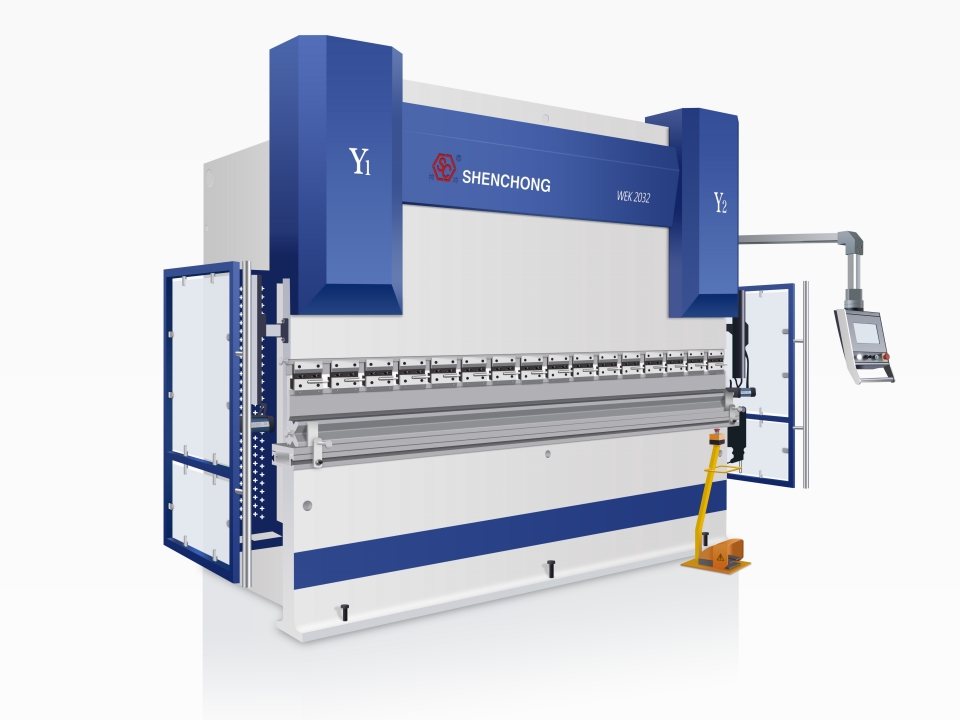
Control Principle And Comparison
Principle And Existing Problems Of Electro Hydraulic Synchronous System (Valve Control)
The structure of the CNC hydraulic press brake is controlled by a regular three-phase asynchronous motor to control a quantitative hydraulic pump. The flow rate through the proportional pressure valve is throttled by an overflow valve to achieve dual cylinder synchronization and ultimately meet the precision requirements of bending processing, which is called “valve control”. This technology has the drawbacks of energy loss and excessive heat generation. The energy loss of the hydraulic system can cause a decrease in the overall efficiency of the system, an increase in oil temperature, and deterioration of the oil, leading to the failure of the press brake machine.
In order to maintain the thermal balance of the oil, the method of increasing the amount of hydraulic oil is usually adopted, but at the same time, it brings about the problem of increased cost of waste oil treatment and possible pollution impact on the environment. Moreover, the noise of the electro-hydraulic synchronous CNC press brake machine is relatively high, which brings certain noise pollution to the surrounding environment.
Principles of Oil Electric Hybrid Numerical Control System (Pump Control)
The hybrid oil electric CNC (pump controlled) press brake machine includes a power unit and a control valve group connected to the CNC system. The power unit includes a servo motor, a unidirectional quantitative pump connected to the servo motor, and an independent fuel tank. The control valve group includes overflow valve, unloading valve, one-way valve, reversing valve, back pressure valve, lifting valve, safety valve, and filling valve.
By controlling the speed of the servo motor of the power unit through a numerical control system, the displacement of the oil pump connected to it can be controlled, thereby achieving displacement speed control of the actuator (oil cylinder). By setting the torque of the servo motor through the numerical control system, the output force of the left and right actuator components (oil cylinder) can be controlled.
The displacement readings of the left and right actuators (oil cylinders) are fed back to the CNC system through displacement sensors (grating rulers or magnetic grating rulers). After comparison, the CNC system controls the left and right power units to achieve closed-loop control of synchronization and positioning of the left and right actuators (oil cylinders). The displacement sensor forms an internal feedback loop to improve the control accuracy of the system.
Unique Growth Cylinder Structure
The traditional electro-hydraulic synchronous CNC press brake machine has a single acting piston cylinder as the main oil cylinder, which mainly relies on the self weight of the slider to achieve fast downward movement, making it difficult to further achieve high operating speed. By changing the internal design structure of the single acting piston cylinder to a speed increasing cylinder, high-speed downward movement of the cylinder can be achieved without being constrained by the weight of its slider, greatly improving bending efficiency.
The hybrid servo press brake has better synchronization, true energy efficiency, simple structure, and faster speed. The application of one-way quantitative pump and speed increasing cylinder in the dual servo oil electric hybrid CNC (pump control) system is the biggest feature of the SHENCHONG dual servo oil electric hybrid system. A one-way quantitative pump has better economy than a two-way quantitative pump, while a speed increasing cylinder exhibits stable and efficient characteristics.
CNC Hybrid Servo Press Brake Machine Advantages (Pump Control)
- Efficiency: The equipment runs at 90% load for 2 hours, increasing efficiency by 30% to 50%.
- Energy saving: The equipment runs at 90% load for 2 hours, resulting in a 28% to 54% increase in energy savings.
- Accuracy: The equipment runs at 90% load for 2 hours, with small Y-axis walking error and an average improvement of 5 times in accuracy at any position.
- Low noise: The equipment runs at 90% load for 2 hours, reducing noise by 10-12 dB and greatly optimizing the working environment.
- Environmental protection: The equipment runs at 90% load for 2 hours, reducing hydraulic oil volume by 50% to 80%.
- Temperature control: The equipment runs at 90% load for 2 hours, with superior oil temperature control, which is beneficial for the overall operation of the machine.
- Appearance: The installation is simple, elegant, and beautiful, with no external pipelines.
By comparing the above two control methods, we can clearly see that the hybrid oil electric numerical control (pump control) system has the characteristics of high efficiency, energy saving, low noise, and environmental protection.
Conclusion
With the accumulation of more and more application experience, technological improvement and optimization, the oil electric hybrid CNC press brake machine produced and manufactured by Wuxi Shenchong Forging Machine Co.,Ltd has been widely used in sheet metal production and manufacturing enterprises, mainly serving industries such as shipbuilding, rail transit, electrical switch gear, building decoration, 5G communication, etc.
The hybrid oil electric CNC press brake machine belongs to energy-saving and environmentally friendly products, and its technological superiority has been fully reflected in practical production applications. It not only responds to the call of the country to build an energy-saving and environmentally friendly green social environment, but also meets the increasingly high-precision and efficient production needs of enterprises, and is highly praised by users. In the future, there will be a trend of partially replacing traditional CNC bending brake machines, and the market prospects are very broad.