Table of Contents
When using a press brake machine, please pay attention to the safety of operation and the correct use of the machine. How to use press brake? The bending operation process includes the complete process from preparation, setting, bending to inspection and cleaning.
Each step must be strictly controlled to ensure that the bent workpiece meets the design requirements, ensure the safety of the operator, and avoid production accidents. The following are some basic steps.
1. Preparation work of press brake operation
The preparation work before using CNC hydraulic press brake is the key to ensure operational safety, improve work efficiency and bending quality. What are the preparations for using the bending machine? The following are some necessary preparations:
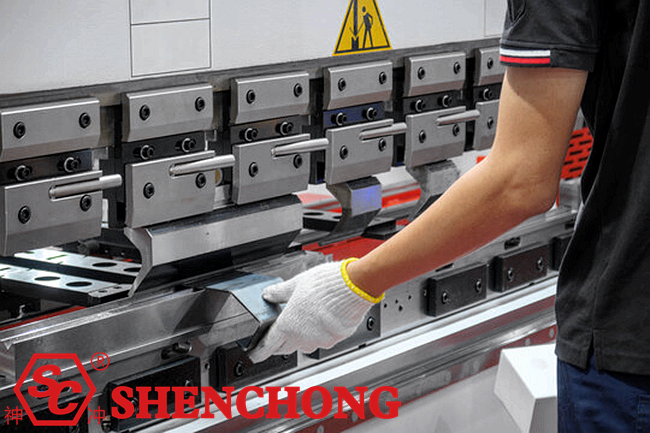
1) Check the equipment status
- Machine inspection: Make sure the bending machine is in good condition and all parts (such as upper die, lower die, hydraulic system, electrical system, etc.) are operating normally.
- Mold inspection: Check whether the mold is intact, make sure the mold has no cracks, wear or other damage, and make sure it matches the size and requirements of the workpiece.
2) Environmental inspection
- Workplace cleanliness: Make sure the work area is tidy and avoid debris or tools that hinder operation.
- Ventilation and lighting: Make sure the work area has sufficient lighting and a good ventilation system, especially when heat or gas is generated during the bending process.
3) Material preparation
- Choose suitable materials: According to the design requirements, select materials suitable for bending machine processing (such as steel, aluminum, copper, etc.), and ensure that the thickness and width of the material meet the processing capacity of the machine.
- Material inspection: Check whether the material is damaged and whether the surface is flat and clean. If there is oil or rust on the surface of the material, it should be cleaned to avoid affecting the bending effect.
4) Select and install the mold
- Choose the appropriate mold according to the material type and bending angle. Common molds include V-type molds, U-type molds, rectangular molds, etc.
- Install the mold: According to the requirements of the machine, correctly install the upper and lower molds, and ensure that the molds are correctly positioned and firmly installed.
5) Set parameters
- Bending angle: Set the bending angle according to the product design requirements. The bending angle directly affects the appearance and performance of the product.
- Bending force: Adjust the pressure setting of the bending machine according to the type and thickness of the material. Too much pressure may cause the material to deform, and too little pressure may not complete the bending.
- Gap adjustment: According to the thickness of the material, adjust the gap between the upper and lower molds to ensure that the material can be bent smoothly without damage.
6) Safety check before press brake bending operation
- Protective equipment: Ensure that the operator wears safety protection equipment, such as protective glasses, earmuffs, gloves, etc.
- Safety check: Check whether the safety devices of the machine (such as protective covers, emergency stop buttons, etc.) are working properly to ensure that they can be stopped in time in case of problems.
- Test run: Before the formal operation, an empty car test can be performed to check the operation of the equipment to ensure that there is no abnormal sound or abnormal operation.
7) Operator preparation
- Familiar with the operation process: Ensure that the operator is familiar with the machine’s operating manual and safety specifications, and understands all control buttons and operating steps.
- Operator training: Ensure that the operator has sufficient experience in using the bending machine or has received relevant training to avoid accidents or defective products due to improper operation.
8) Production process and process confirmation
- Confirm the process flow and bending sequence, especially in the case where multiple bending steps are required, and follow the correct order.
- Confirm whether the auxiliary tools required for the bending machine (such as support frames, clamps, etc.) are ready.
Through these preparations, problems in operation can be effectively reduced, ensuring that the bending machine can complete the task efficiently and accurately.
2. Parameter setting of press brake machines
Setting the parameters of the bending machine is very important, which is related to the accuracy, surface quality and safety of the final bending workpiece. When setting the parameters, it is necessary to adjust them according to the characteristics of the material, the bending requirements and the performance of the machine.
How to set the parameters of the cnc press brake machine? The following are common bending machine parameters and their setting methods:
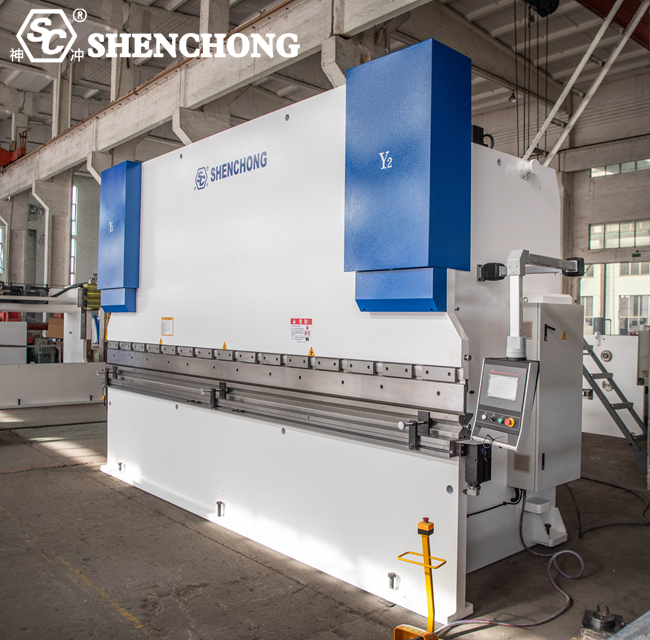
1) Bending angle
Setting method:
The bending angle refers to the angle formed by the workpiece during the bending process, which is generally set by the angle adjustment device on the machine.
Setting principle:
The bending angle is set according to the design requirements and process requirements. It can usually be determined by referring to the process drawings or samples.
Notes:
When setting, make sure that the contact area between the mold and the workpiece is consistent with the angle setting. Too large an angle will cause cracks on the workpiece surface, and too small an angle will not achieve the expected bending effect.
2) Bending force
Setting method:
Bending force refers to the pressure applied to the material during the bending process. The magnitude of the bending force depends on the type, thickness, width and required bending angle of the material.
Setting principle:
The bending force can be adjusted by the hydraulic system of the machine. When setting, the appropriate force value needs to be calculated according to the thickness of the material. Generally speaking, the greater the thickness, the greater the bending force required.
Calculation formula:
Bending force (N) can be roughly estimated by the following formula: F=(K×W×T2)/L
Where:
- F is the bending force (N).
- K is a constant, usually the value of common materials.
- W is the width of the workpiece (mm).
- T is the thickness of the material (mm).
- L is the effective working length of the bending machine (mm).
Press Brake Tonnage Calculator
Note:
Bending force that is too high or too low will affect the bending quality. If the force is not set properly, it may cause material deformation or mold damage.
3) Die gap
Setting method:
The die gap refers to the distance between the upper die and the lower die, which directly affects the bending effect of the material.
Setting principle:
The die gap should usually be 6%-10% of the material thickness. For example, if the material thickness is 6mm, the die gap should be set between 0.36mm and 0.6mm. If this gap is too small, it may make the material difficult to bend, and if it is too large, it will affect the bending accuracy and surface quality.
Notes:
The die gap of different materials is different. For example, soft materials such as aluminum require a larger gap than hard materials such as steel.
4) Bending speed
Setting method:
The bending speed affects the stress distribution and deformation of the material during the bending process. Generally, when the bending speed is slower, the deformation of the material can be reduced and the bending quality can be improved.
Setting principle:
The bending speed is related to the hardness and thickness of the material. Thicker materials or materials with higher hardness require lower speeds; thinner materials or softer materials can use higher speeds.
Notes:
Too high a bending speed may cause cracks or uneven bending of the workpiece, and too low a speed will affect production efficiency.
5) Lower die position
Setting method:
The position of the lower die can be adjusted according to the requirements of the workpiece and the actual situation of the machine. Adjust the position of the lower die to ensure that the workpiece can be evenly stressed during bending.
Setting principle:
Under normal circumstances, ensure that the pressure on both ends of the workpiece is uniform to avoid deviation or uneven bending of the workpiece.
Note:
If the lower die position is incorrect, it may cause uneven bending of the workpiece or other defects.
6) Return speed
Setting method:
The return speed is the speed at which the mold returns to its original position after the bending machine completes the bending action. Too fast a return speed may cause damage to the workpiece or mold, and too slow a return speed will waste time.
Setting principle:
According to the model and working conditions of the bending machine, set a reasonable return speed to ensure safety and smoothness.
7) Positioning device
Setting method:
Some bending machines are equipped with a positioning device for accurately positioning the workpiece. When setting, ensure that the workpiece is accurately aligned to obtain the accurate bending angle and size.
Setting principle:
Ensure the alignment of the workpiece to prevent dimensional errors caused by inaccurate positioning.
8) Pre-bending
Setting method:
In some cases, especially for thick materials, pre-bending may be required, that is, a small bend is performed first, and then the final bend is performed.
Setting principle:
Pre-bending usually sets a smaller angle, and then the main bend is performed.
9) Inspection and adjustment
Check setting:
Before starting formal processing, you can check whether the set parameters are appropriate by performing several test bends to ensure that the bending effect meets the design requirements.
Adjustment:
According to the actual bending results, adjust parameters such as pressure, angle, etc. in time to ensure the final product quality.
When setting the parameters of the bending machine, it is necessary to comprehensively consider factors such as the material properties, thickness, bending angle, mold gap, etc., and make detailed adjustments. Reasonable parameter settings can effectively improve the bending quality, reduce the scrap rate and ensure the safety of operation. Testing the specimen after each adjustment is an effective way to ensure the quality of the machine and the workpiece.
3. Press Brake Bending Process
The bending process of the press brake machine is the key to ensure the quality of the bent workpiece and production efficiency. After ensuring that the above preparations are completed and the bending machine is set up and debugged, we can start the bending process. How to use press brake?
1) Place the workpiece
Inspect the material:
Make sure the workpiece material is free of defects, oil stains, rust, etc., and meets the bending requirements.
Workpiece alignment:
Place the workpiece on the bending machine workbench and ensure that both ends of the workpiece are aligned with the mold. A positioning device can be used to help the workpiece to be accurately positioned.
Ensure the stability of the workpiece: Ensure that the workpiece is placed stably and not offset, and confirm that its position matches the bending angle.
2) Perform the bending operation
Start the bending machine:
Press the start button to start the machine. Observe the movement of the machine to ensure that the machine runs smoothly without abnormal noise or vibration.
Control the bending process:
During the bending process, the upper mold is gradually pressed down to apply the bending force. During the bending process, ensure that the workpiece is evenly stressed to avoid uneven bending or cracks.
Multiple bending:
If multiple bending steps are required, the angle, position, etc. can be adjusted according to the process requirements to gradually complete all bending operations.
3) Complete bending and check
Stop the machine:
After bending, release the control button to stop the movement of the bending machine.
Remove the workpiece:
Carefully remove the bent workpiece from the machine to avoid damaging the surface or scratching it.
Check the bending quality:
- Check whether the bending angle meets the design requirements.
- Check whether there are defects such as cracks, creases, scratches, etc. on the surface of the workpiece.
- Use measuring tools (such as angle rulers, calipers, etc.) to check the accuracy of the bending to ensure that the workpiece size is within the allowable error range.
Adjust and optimize (if necessary):
If the bending angle or workpiece size does not meet the requirements, the parameters of the bending machine can be adjusted according to the inspection results to reprocess the workpiece.
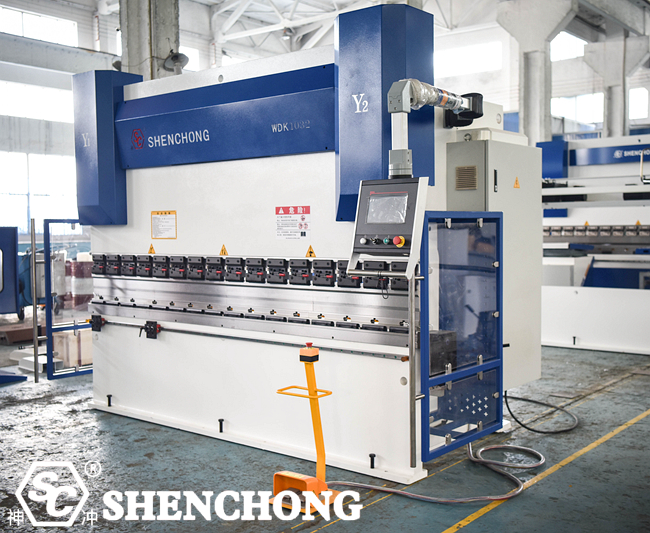
4. Arrangement and maintenance
Clean equipment:
After the bending operation is completed, clean up metal chips, oil stains and other debris on the workbench, mold and machine in time to avoid affecting the accuracy and normal operation of the machine.
Inspect equipment:
Regularly check the hydraulic system, CNC system, electrical system, etc. to ensure that all parts of the machine are in good working condition. Check whether the bending machine needs maintenance or repair. According to production requirements, perform machine maintenance regularly, such as refueling, cleaning filters, etc.
Record data:
Record production data, such as the number of workpieces, quality inspection results, equipment usage, etc., for future reference and analysis.
5. Safety precautions for press brake operation
Wear protective equipment:
Be sure to wear protective equipment such as safety glasses, earmuffs, gloves, etc. when operating the bending machine to prevent accidental injuries.
Ensure no interference:
There should be no debris or tools around the bending machine to avoid interference with the operation of the equipment during operation.
Avoid direct contact with the mold:
During the bending process, avoid putting your hands or other parts of your body close to the moving mold and workpiece to prevent pinching.
Ensure a clear operating area:
Ensure a clear line of sight during operation to avoid accidental contact with the machine.
Be careful:
During the entire bending process, always keep an eye on the machine and workpiece, detect abnormalities in time and take action.
6. Summary
How to use press brake? The operation process of a bending machine includes every step from preparation, setting parameters to actual bending and subsequent inspection. Each step must be cautious and meticulous to ensure that the bent workpiece meets the design requirements.
When using a CNC press brake machine, you need to fully understand the machine’s operating procedures, parameter settings, and programming methods. Ensure that while setting the correct parameters and performing precise operations, pay attention to safety and equipment maintenance to complete the bending task efficiently and safely. Through reasonable operation, you can maximize production efficiency and ensure the bending quality of the workpiece.