Introduction
Table of Contents
Shearing force plays a critical role in the design and manufacturing of sheet metal components. It is a fundamental concept in mechanical engineering, particularly in industries such as automotive, aerospace, and construction, where sheet metal is commonly used. Accurately calculating the shearing force is essential to ensure the structural integrity of metal plates and prevent failure during service. This article provides a detailed guide on how to calculate the shearing force of sheet metal plates, covering the basic principles, necessary formulas, and practical applications.
Basic Concepts of Shearing Force
Shearing force, commonly known as shear force, is a force that causes deformation of a material by sliding a portion of it relative to adjacent portions. It is the force applied parallel to the surface of the metal plate that causes shear stress within the material, leading to material deformation and eventual separation.
The required shear force depends on various factors, including the material properties of the metal plate (such as shear strength), the thickness of the plate, the cutting method, and the geometric shape of the cut.
In practice, when cutting metal plates, the shear force is usually provided by machine tools such as shear, punches, or blades. This tool applies the necessary force to deform the metal sheet and cut it along the desired path.
Understanding shear forces is crucial for analyzing the stability and integrity of structures, as if not properly considered in design and analysis, shearing forces may cause deformation or bending of metal sheets and fail to achieve the desired shear effect.
Factors Affecting Shearing Force

- Material type: The type of metal used in the sheet has a significant impact on its shear performance. Different metals, such as steel, aluminum, copper, and alloys, have different mechanical properties such as strength, hardness, and ductility, which in turn affect the required shear force.
- Thickness: Compared to thinner sheets, thicker sheets typically require greater shear forces. This is because thicker sheets provide more deformation resistance due to the increased volume of the sheared material.
- Tensile and Yield Strength: These properties provide insight into the material’s behavior under different loading conditions and are often used alongside shear strength in design calculations.
- Surface condition: The surface smoothness of the metal plate will affect its shear behavior. A smoother surface can reduce friction during the shearing process and require less force. On the contrary, the presence of rough surfaces or pollutants increases friction and requires more force.
- Grain structure: Many metal plate manufacturing processes produce grain structure. The direction and size of grains in a material can affect its strength and ductility, thereby affecting the required shear force. Compared to cutting grains horizontally, cutting along grains may require less force.
- Temperature: Like other materials, temperature can affect the performance of metal plates. Cold processing or cutting at low temperatures can increase the strength of materials, making them more brittle and requiring higher shear forces. Heating metal will reduce its strength, making it easier to shear.
- Lubrication: Using lubricants during the shearing process can reduce the friction between the metal plate and the cutting tool, thereby reducing the required shear force. Lubrication also helps to improve the surface smoothness of cutting edges and extend tool life.
- Tool clearance and shear angle: The clearance and shear angle between the cutting blades will affect the shear force. The optimal gap and shear angle can reduce the deformation of the metal plate and the force required for cutting.
- Geometric shape and conditions of cutting tools: The design and sharpness of cutting tools have a significant impact on the cutting process. Proper maintenance and sharp tools can ensure a clean cut and minimize deformation, thereby reducing the force required to shear metal plates.
Shearing Force Calculation
The shear force (F) required for cutting metal plates can be calculated using the following formula, where:
Fs=τ⋅AF_s = \tau \cdot AFs=τ⋅A
Where:
- FsF_sFs is the shearing force,
- τ\tauτ is the shear stress, and
- AAA is the area under shear.
Shear Strength
Shear strength is an important consideration in the manufacturing of metal plates, especially in processes such as cutting, bending, and forming. It represents the ability of a material to resist shear forces without permanent deformation or failure.
When cutting metal plates, the shear strength is influenced by various factors such as metal type, thickness, grain structure, and any surface treatment or coating. Generally, ductile metals such as aluminum and mild steel exhibit higher shear strength compared to certain types of brittle materials such as stainless steel.
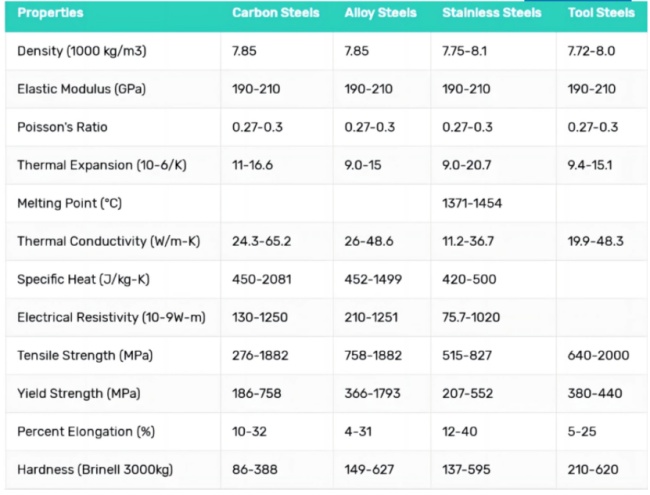
Understanding shear strength is crucial in various engineering disciplines, including civil engineering (e.g. designing structures capable of withstanding wind and earthquake loads), mechanical engineering (e.g. designing machine components), and materials science (e.g. determining material suitability for specific applications).
In the manufacturing of metal plates, shear strength is particularly important in cutting operations such as shearing or punching. During these processes, the material will experience significant shear forces, and if the shear strength is exceeded, it can cause deformation or even fracture. Therefore, engineers and manufacturers must carefully consider the shearing strength of the metal plates to ensure that the selected manufacturing method is appropriate and that the final product meets the required performance and safety standards.
Let me break down some key points to help you better understand it.
Shear Stress
Shear stress is the force per unit area. When the force is parallel or tangential to the surface of the material, shear stress is generated, causing one layer of the material to slide over another layer.
Mathematically speaking, the shear stress (τ) is given by the following formula:
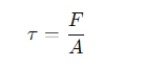
τ is the shear stress
F is the force applied parallel to the surface
A is the cross-sectional area of the applied force
Shear strain: Shear strain is a measure of deformation caused by shear stress. It is defined as the change in material shape divided by its original shape.
Failure criteria: When the applied shear stress exceeds the shear strength of the material, it will fail. Different materials have different shear strengths, which depend on factors such as material composition, microstructure, temperature, and loading conditions.
Shear modulus: Shear modulus (also known as stiffness modulus) is a material property that quantifies how much shear stress a material can withstand without permanent deformation.
Shearing Force Calculation Example
Consider a steel plate with a thickness of 5 mm and a shear stress of 200 MPa. The area AAA subjected to shear can be calculated by multiplying the thickness by the length of the plate being sheared. If the length is 100 mm, then:
A=5 mm×100 mm=500 mm2A = 5 \, \text{mm} \times 100 \, \text{mm} = 500 \, \text{mm}^2A=5mm×100mm=500mm2
The shearing force FsF_sFs would then be:
Fs=200 MPa×500 mm2=100,000 N=100 kNF_s = 200 \, \text{MPa} \times 500 \, \text{mm}^2 = 100,000 \, \text{N} = 100 \, \text{kN}Fs=200MPa×500mm2=100,000N=100kN
Shearing Force In Double Shear
In some scenarios, such as in bolted connections, the force may be distributed over two shear planes, resulting in a double shear condition. The formula for shearing force in a double shear scenario is:
Fs=P2×AF_s = \frac{P}{2 \times A}Fs=2×AP
Where PPP is the applied load and AAA is the area subjected to shear.
Practical Applications Of Shearing Force Calculations
Shearing force calculations are crucial in various industrial applications.
1. Plate Shearing Machine
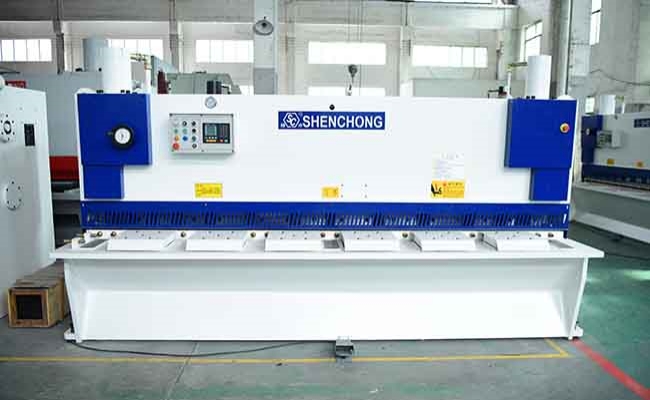
In plate shearing machine cutting process, precise control over shearing force is necessary to cut sheet metal accurately. The calculated shearing force helps in selecting appropriate tools and machine settings to avoid damaging the metal or the machine.
2. Stamping And Punching Processes
During stamping or punching, the shearing force determines the force required to create holes or cutouts in sheet metal. Incorrect calculations can lead to tool wear or failure, and even defects in the final product.
3. Welding And Fabrication
In welding processes, understanding shearing forces helps in designing joints that can withstand operational loads without failing. Shearing force calculations are used to determine the size and type of welds needed for a secure joint.
Advanced Considerations
1. Finite Element Analysis (FEA)
Finite Element Analysis (FEA) is a computational method used to simulate the behavior of sheet metal under various forces, including shear. FEA provides detailed insights into how the material will react to different shearing forces, allowing engineers to optimize designs before physical prototypes are made.
2. Experimental Methods
In addition to theoretical calculations, experimental methods such as shear testing can be used to measure the shearing force directly. This approach provides real-world data that can validate or refine theoretical models.
3. Design for Manufacture Ability and Assembly (DFMA)
When designing sheet metal components, it’s important to consider the manufacture ability of the design. Shearing force calculations play a crucial role in ensuring that the design can be efficiently and cost-effectively manufactured without compromising structural integrity.
Conclusion
Calculating the shearing force of sheet metal plates is a fundamental aspect of mechanical design and manufacturing. By understanding the basic principles of shear stress and shear strength, and applying the appropriate formulas, engineers can ensure that their designs are safe, efficient, and effective. Whether in CNC machining, stamping, or welding, accurate shearing force calculations are essential for successful sheet metal fabrication.