Table of Contents
Introduction
Plate punching machines are essential tools in various industries, including automotive, aerospace, metal fabrication, and construction. These machines are used to create holes, slots, and shapes in metal plates with high precision and efficiency. The cost of a plate punching machine can vary widely depending on several factors, such as the type of machine, its capacity, features, and the manufacturer. This comprehensive article will explore the different types of plate punching machines, the factors that influence their cost, typical price ranges, and additional considerations for purchasing and owning a plate punching machine.
Types of Plate Punching Machines
Plate punching machines come in various types, each designed for specific applications and offering different levels of complexity and functionality. Understanding the different types of plate punching machines is crucial for selecting the right equipment for your needs.
1. Mechanical Plate Punching Machines
Mechanical plate punching machine use a flywheel and crank mechanism to generate the punching force. These machines are known for their high-speed operation and are commonly used in mass production environments.
- Advantages: High speed, suitable for high-volume production, relatively simple design.
- Disadvantages: Limited to specific shapes and sizes, higher maintenance requirements due to mechanical parts.
2. Hydraulic Plate Punching Machines
Hydraulic plate punching machine uses hydraulic pressure to drive the punch through the material. These machines offer greater versatility and can handle thicker materials compared to mechanical punching machines.
- Advantages: High force, versatile, capable of punching thicker materials, smooth and controlled operation.
- Disadvantages: Slower cycle times compared to mechanical machines, higher initial cost.
3. CNC Plate Punching Machines
CNC (Computer Numerical Control) plate punching machine is equipped with computerized control systems that allow for precise and automated punching operations. These machines are ideal for complex and intricate punching tasks.
- Advantages: High precision, automation, ability to punch complex shapes, reduced manual intervention.
- Disadvantages: Higher initial cost, requires skilled operators and programming knowledge.
4. Turret Plate Punching Machines
Turret punch press machines feature a turret that holds multiple punches and dies, allowing for quick tool changes and versatility in punching different shapes. These machines are commonly used in sheet metal fabrication.
- Advantages: Quick tool changes, versatile, suitable for complex and varied punching tasks.
- Disadvantages: Higher initial cost, requires more space due to the turret design.
Factors Influencing The Plate Punching Machine Cost
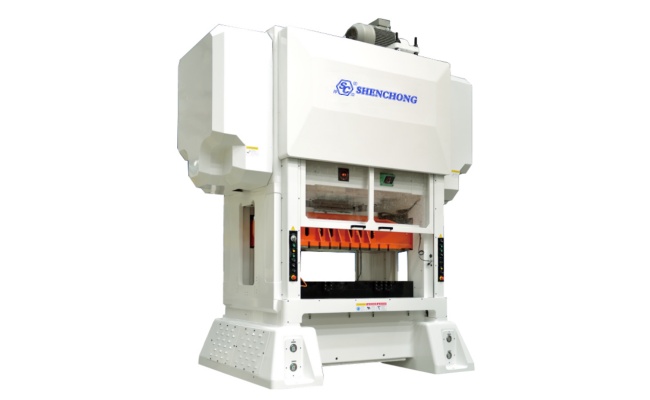
Plate punching machine cost can be influenced by several factors, including its type, capacity, features, brand, and geographic location. Understanding these factors can help you make an informed decision when purchasing a plate punching machine.
1. Type of Plate Punching Machine
As discussed earlier, the type of plate punching machine significantly influences its cost. Mechanical machines are generally less expensive than hydraulic, CNC, and turret machines due to their simpler design and lower capabilities. CNC and turret machines, with their advanced features and automation capabilities, tend to be more expensive.
2. Capacity and Force
The capacity of a plate punching machine, typically measured in tons, determines the maximum force it can exert. Machines with higher capacity and force are more expensive due to the additional engineering and materials required to handle the increased load. The capacity required depends on the thickness and type of material being punched.
- Low-Capacity Machines (1-30 tons): Suitable for light-duty tasks, generally less expensive.
- Medium-Capacity Machines (30-200 tons): Suitable for medium-duty tasks, moderate cost.
- High-Capacity Machines (200+ tons): Suitable for heavy-duty tasks, higher cost.
3. Features and Customization
Additional features and customization options can significantly impact the cost of a plate punching machine. Common features that influence pricing include:
- Automation: Machines with automation features such as automatic tool changers, robotic material handling, and programmable controls are more expensive.
- Precision Controls: Machines with advanced control systems for precise pressure, speed, and position adjustments are costlier.
- Tooling and Accessories: Specialized tooling, dies, and accessories required for specific applications can increase the overall cost.
- Safety Features: Enhanced safety features such as light curtains, safety interlocks, and emergency stop systems add to the cost but are essential for ensuring operator safety.
4. Brand and Manufacturer
The brand and reputation of the manufacturer play a significant role in the cost of a plate punching machine. Established brands with a history of producing high-quality and reliable equipment often command higher prices. Additionally, manufacturers offering comprehensive after-sales support, warranties, and service packages may charge a premium for their products.
5. Geographic Location
The geographic location of the manufacturer and the buyer can affect the cost of a plate punching machine. Factors such as import/export duties, shipping costs, and regional market conditions can influence pricing. Buyers in regions with a higher cost of living or stricter regulations may also face higher prices.
Typical Price Ranges For Different Types of Plate Punching Machine
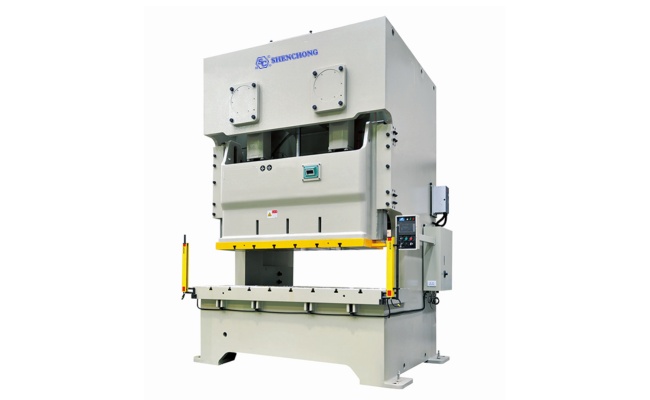
1. Mechanical Plate Punching Machines
- Low-Capacity (1-30 tons): $10,000 to $30,000
- Medium-Capacity (30-200 tons): $30,000 to $70,000
- High-Capacity (200+ tons): $70,000 to $150,000 or more
2. Hydraulic Plate Punching Machines
- Low-Capacity (1-30 tons): $20,000 to $50,000
- Medium-Capacity (30-200 tons): $50,000 to $100,000
- High-Capacity (200+ tons): $100,000 to $250,000 or more
3. CNC Plate Punching Machines
- Low-Capacity (1-30 tons): $50,000 to $100,000
- Medium-Capacity (30-200 tons): $100,000 to $200,000
- High-Capacity (200+ tons): $200,000 to $500,000 or more
4. Turret Plate Punching Machines
- Low-Capacity (1-30 tons): $70,000 to $150,000
- Medium-Capacity (30-200 tons): $150,000 to $300,000
- High-Capacity (200+ tons): $300,000 to $600,000 or more
Additional Costs and Considerations
1. Installation and Setup
The installation and setup of a plate punching machine can incur additional costs. This includes expenses related to transportation, rigging, and positioning of the machine, as well as any necessary modifications to the facility to accommodate the machine.
2. Maintenance and Repairs
Regular maintenance is essential to ensure the optimal performance and longevity of a plate punching machine. Costs for maintenance, repairs, and replacement parts should be factored into the overall investment. Manufacturers may offer maintenance contracts or service packages to cover these expenses.
3. Energy Consumption
Plate punching machines can be energy-intensive, particularly high-capacity models. The cost of energy consumption should be considered, especially in regions with high electricity rates. Energy-efficient models may have higher upfront costs but can result in long-term savings.
4. Training and Labor
Operators and maintenance personnel may require training to effectively use and maintain the plate punching machine. Training costs, as well as the labor costs for operating the machine, should be included in the overall budget.
5. Safety Compliance
Ensuring that the plate punching machine complies with local safety regulations and standards is crucial. This may involve additional costs for safety equipment, certifications, and modifications to the machine.
Leading Punching Machine Manufacturers and Their Pricing
1. Trumpf
Trumpf is a global leader in industrial machine tools, including plate punching machines. Their products are known for their precision, reliability, and advanced automation capabilities. Trumpf’s punching machines are typically on the higher end of the price range due to their high quality and innovative features.
2. Amada
Amada is a renowned manufacturer of metalworking machinery, including punching machines. Their products are known for their versatility, precision, and advanced technology. Amada’s punching machines are competitively priced, offering a range of options for different budgets and applications.
3. Prima Power
Prima Power is a leading manufacturer of laser and sheet metal working machinery, including punching machines. Their products are known for their flexibility, automation, and integration with other processes such as bending and laser cutting. Prima Power’s punching machines are typically mid to high range in terms of pricing.
4. Salvagnini
Salvagnini specializes in flexible automation systems for sheet metal processing, including punching machines. Their products are designed for high productivity and quality, with advanced automation and robotic integration. Salvagnini’s punching machines are on the higher end of the price spectrum.
5. LVD Group
LVD Group is a leading manufacturer of sheet metalworking machinery, including punching machines. Their products are known for their precision, reliability, and advanced technology. LVD Group’s punching machines are competitively priced, offering a range of options for different applications.
6. Murata Machinery (Muratec)
Murata Machinery, commonly known as Muratec, is a leading manufacturer of industrial machinery, including punching machines. Their products are known for their high precision, speed, and automation capabilities. Muratec’s punching machines are typically mid to high range in terms of pricing.
7. Boschert
Boschert is a renowned manufacturer of sheet metalworking machinery, including punching machines. Their products are known for their precision, reliability, and advanced technology. Boschert’s punching machines are competitively priced, offering a range of options for different applications.
8. Tailift
Tailift is a leading manufacturer of industrial machinery, including punching machines. Their products are known for their high precision, speed, and automation capabilities. Tailift’s punching machines are typically mid range in terms of pricing.
9. Euromac
Euromac is a leading manufacturer of sheet metalworking machinery, including punching machines. Their products are known for their precision, reliability, and advanced technology. Euromac’s punching machines are competitively priced, offering a range of options for different applications.
10. SC SHENCHONG
SC Machinery is a leading manufacturer of machine tools and production systems, including punching machines. Their products are known for their high precision, reliability, and advanced technology. SHENCHONG punching machines are typically mid to high range in terms of pricing.
Case Studies: Cost Analysis Of Plate Punching Machine Purchases
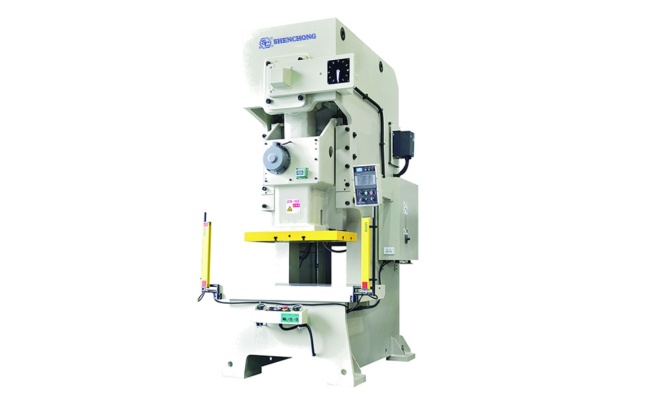
1. Automotive Manufacturer
An automotive parts manufacturer required a high-capacity plate punching machine for producing metal components. After evaluating several options, they selected a 300-ton hydraulic plate punching machine with advanced automation features. The total cost, including installation, training, and a three-year maintenance contract, was approximately $250,000. The investment resulted in a 35% increase in production efficiency and a 20% reduction in labor costs.
2. Aerospace Supplier
A supplier of aerospace components needed a precision plate punching machine for producing titanium parts. They opted for a 150-ton CNC plate punching machine with automated tool changers and robotic material handling. The total investment, including installation and operator training, was $200,000. The machine provided the required precision and consistency, leading to a 25% improvement in product quality and a 15% reduction in material waste.
3. Metal Fabrication Shop
A metal fabrication shop required a versatile plate punching machine for various punching tasks. They chose a 50-ton mechanical plate punching machine with manual controls and basic safety features. The total cost, including delivery and setup, was $40,000. The machine met the shop’s needs, providing reliable performance and contributing to a 20% increase in productivity.
Future Trends In Plate Punching Machine Technology And Pricing
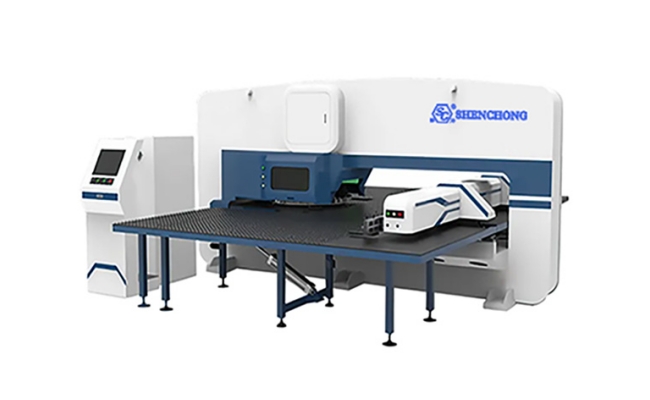
1. Automation and Industry 4.0 Integration
The integration of automation and Industry 4.0 technologies is driving advancements in plate punching machines. Features such as IoT connectivity, real-time monitoring, and predictive maintenance are becoming more common, enhancing efficiency and reducing downtime. While these technologies may increase the upfront cost, they offer long-term benefits and cost savings.
2. Energy Efficiency and Sustainability
Manufacturers are increasingly focusing on energy-efficient designs to reduce the environmental impact and operational costs of plate punching machines. Innovations such as servo-hydraulic systems, which combine hydraulic power with electric servo motors, are gaining popularity. These systems offer precise control and lower energy consumption, resulting in cost savings over the machine’s lifespan.
3. Customization and Flexibility
The demand for customized plate punching machine solutions tailored to specific applications is growing. Manufacturers are offering more flexible and modular designs that can be adapted to different tasks and production requirements. While customized machines may have higher initial costs, they provide greater value and efficiency for specialized operations.
4. Enhanced Safety Features
Advancements in safety technology are leading to the development of plate punching machines with improved safety features. Innovations such as light curtains, advanced interlock systems, and real-time safety monitoring enhance operator safety and reduce the risk of accidents. These features, while adding to the cost, are essential for ensuring compliance with safety regulations and protecting workers.
Conclusion
Plate punching machine cost can vary widely based on factors such as type, capacity, features, manufacturer, and geographic location. Understanding these factors and considering additional costs such as installation, maintenance, energy consumption, and training is crucial for making an informed investment.
Plate punching machines offer significant benefits, including high precision, speed, and versatility, making them indispensable in various industries. As technology continues to advance, plate punching machines are becoming more efficient, automated, and customizable, offering greater value to manufacturers.
By carefully evaluating the specific needs of their operations and selecting the right plate punching machine, businesses can enhance productivity, improve quality, and achieve long-term cost savings. The insights provided in this comprehensive article aim to guide buyers in making informed decisions and maximizing the benefits of their investment in plate punching machine technology.