Table des matières
Introduction
Le système de chargement et de déchargement automatique des métaux est un équipement révolutionnaire pour déplacer automatiquement les plaques de tôle d'une machine à une autre. L'application la plus courante du système de chargement et de déchargement automatique est la machine de découpe laser.
Les machines de découpe laser ont révolutionné l'industrie manufacturière en offrant précision, rapidité et polyvalence dans la découpe de divers matériaux. Cependant, pour exploiter pleinement les capacités de ces machines, des systèmes de manutention efficaces sont essentiels. Les systèmes de chargement et de déchargement des machines de découpe laser jouent un rôle essentiel dans l'amélioration de la productivité, la réduction des temps d'arrêt et la garantie de la sécurité. Cet article se penche sur les différents types de systèmes de chargement et de déchargement, leurs avantages, leurs applications et les tendances futures, en offrant un aperçu complet de ces composants essentiels dans les opérations de découpe laser.
L'importance du système de chargement et de déchargement automatisé des métaux
Les systèmes de chargement et de déchargement sont conçus pour automatiser le processus d'approvisionnement en matières premières de la machine de découpe laser et d'enlèvement des pièces finies. Ces systèmes sont essentiels pour plusieurs raisons :
- Productivité accrue:Les systèmes automatisés peuvent réduire considérablement le temps nécessaire au chargement et au déchargement des matériaux, permettant à la machine de découpe laser de fonctionner en continu et efficacement.
- Coûts de main d'oeuvre réduits:En automatisant ces processus, les fabricants peuvent minimiser le besoin de travail manuel, réduisant ainsi les coûts de main-d’œuvre et le risque d’erreur humaine.
- Sécurité améliorée:Les systèmes automatisés améliorent la sécurité au travail en minimisant le besoin d’intervention humaine dans les opérations potentiellement dangereuses.
- Cohérence et qualité:L'automatisation garantit une manipulation uniforme des matériaux, ce qui contribue à maintenir des normes de qualité élevées dans le processus de découpe.
Applications des systèmes de chargement et de déchargement
1. Industrie automobile
Dans l'industrie automobile, les systèmes de chargement et de déchargement sont utilisés pour manipuler de grandes tôles et des pièces complexes. Les systèmes automatisés garantissent une qualité constante et une productivité élevée, répondant aux exigences de la production de masse.
2. Industrie aérospatiale
L'industrie aéronautique exige précision et régularité dans la fabrication des composants. Les systèmes de chargement et de déchargement automatisés permettent de répondre à ces exigences en garantissant une manutention précise des matériaux et en réduisant le risque de défauts.
3. Fabrication de métaux
La fabrication de métaux implique la découpe, le façonnage et l'assemblage de pièces métalliques. Les systèmes de chargement et de déchargement rationalisent ces processus en automatisant la manutention des matières premières et des pièces finies, augmentant ainsi l'efficacité et la productivité.
4. Industrie électronique
Dans l'industrie électronique, la précision est primordiale. Les systèmes automatisés garantissent la manipulation précise des matériaux et composants délicats, minimisant ainsi les risques de dommages et garantissant une production de haute qualité.
5. Fabrication de meubles
L'industrie de fabrication de meubles bénéficie de systèmes automatisés capables de traiter de grandes feuilles de bois, de métal ou de matériaux composites. Ces systèmes améliorent la productivité et garantissent une qualité constante dans la production des composants de meubles.
6. Fabrication de dispositifs médicaux
Dans la fabrication de dispositifs médicaux, les systèmes de chargement et de déchargement automatisés assurent la manipulation précise des matériaux et des composants, répondant à des normes de qualité et de sécurité strictes.
Types de systèmes de chargement et de déchargement
1. Chargement et déchargement manuels
Les systèmes manuels font appel à des opérateurs humains pour charger les matières premières sur la machine de découpe laser et retirer les pièces finies. Bien que ces systèmes soient simples et rentables, ils présentent plusieurs limites :
- Augmentation des coûts de main d'oeuvre:Les systèmes manuels nécessitent une quantité importante de travail, ce qui peut être coûteux, en particulier dans les environnements de production à volume élevé.
- Incohérence:Les opérateurs humains peuvent introduire de la variabilité dans le processus de chargement et de déchargement, affectant la qualité et l’efficacité de l’opération de découpe laser.
- Risques de sécurité:La manutention manuelle de matériaux volumineux et lourds peut présenter des risques pour la sécurité des opérateurs.
2. Chargement et déchargement semi-automatiques
Les systèmes semi-automatiques combinent des processus manuels et automatisés. En général, un opérateur positionne la matière première et le système la charge automatiquement dans la machine de découpe laser. De même, le système décharge les pièces finies, que l'opérateur récupère ensuite. Ces systèmes offrent plusieurs avantages :
- Effort de travail réduit:Les systèmes semi-automatiques réduisent l’effort physique demandé aux opérateurs, améliorant ainsi l’ergonomie et réduisant la fatigue.
- Efficacité améliorée:L'automatisation du processus de chargement et de déchargement accélère l'opération par rapport aux systèmes entièrement manuels.
- Sécurité renforcée:En réduisant le besoin de manutention manuelle des matériaux, les systèmes semi-automatiques améliorent la sécurité au travail.
3. Chargement et déchargement entièrement automatiques
Les systèmes entièrement automatiques gèrent l'ensemble du processus de chargement des matières premières et de déchargement des pièces finies sans intervention humaine. Ces systèmes sont équipés de technologies avancées telles que des bras robotisés, des convoyeurs et des capteurs pour atteindre des niveaux d'automatisation élevés :
- Productivité maximisée:Les systèmes entièrement automatiques peuvent fonctionner en continu, augmentant considérablement le rendement de la machine de découpe laser.
- Cohérence et précision:L'automatisation garantit une manipulation cohérente des matériaux, le maintien de normes de qualité élevées et la réduction du risque d'erreurs.
- Économies sur les coûts de main d'œuvre:En éliminant le besoin de travail manuel, les systèmes entièrement automatiques réduisent les coûts de main-d’œuvre et permettent aux opérateurs de se concentrer sur d’autres tâches à valeur ajoutée.
- Sécurité:Les systèmes entièrement automatisés améliorent la sécurité en minimisant l’interaction humaine avec les machines et les matériaux.
Composants du système d'automatisation de chargement et de déchargement des métaux
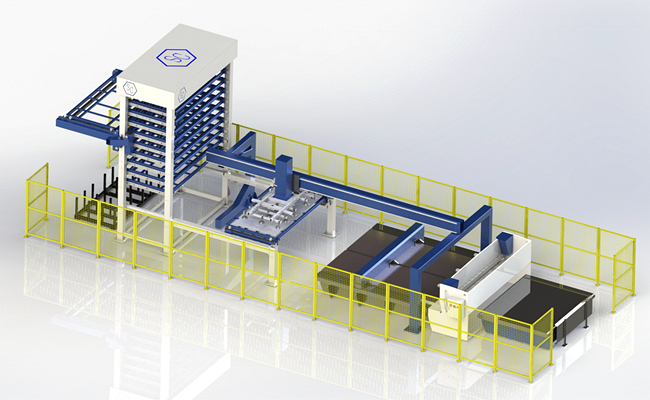
1. Stockage du matériel
Le système de chargement et de déchargement automatisé des métaux est doté d'un système de stockage des métaux. Il dispose d'une plate-forme de palettisation métallique simple ou peut se connecter à la système de stockage automatique de métalLes systèmes de stockage de matériaux sont utilisés pour organiser et stocker les matières premières de manière à faciliter l'accès et la manipulation. Ces systèmes peuvent être de simples racks ou des systèmes de stockage et de récupération automatisés avancés (AS/RS) qui s'intègrent à la machine de découpe laser.
- Étagères et rayonnages:Solutions de stockage de base qui permettent aux opérateurs de récupérer manuellement les matériaux.
- Systèmes automatisés de stockage et de récupération (AS/RS):Systèmes avancés qui stockent et récupèrent automatiquement les matériaux en fonction des exigences de production, optimisant l'espace et l'efficacité.
2. Équipement de manutention
Les équipements de manutention sont essentiels pour transporter les matières premières du stockage à la machine de découpe laser et pour déplacer les pièces finies vers leur prochaine destination. Les types courants d'équipements de manutention comprennent :
- Convoyeurs:Les convoyeurs à bande ou à rouleaux transportent les matériaux entre les différentes étapes du processus de découpe laser.
- Bras robotisés:Les bras robotisés équipés de pinces ou de dispositifs d'aspiration sous vide manipulent les matériaux avec précision, permettant un chargement et un déchargement automatisés.
- Grues et palans:Utilisé pour soulever et déplacer des matériaux lourds, en particulier dans les environnements de fabrication à grande échelle.
3. Chargeurs et déchargeurs
Les chargeurs et déchargeurs sont des machines spécialisées conçues pour automatiser le processus de placement des matières premières sur la machine de découpe laser et de retrait des pièces finies. Ces systèmes peuvent être intégrés à d'autres équipements d'automatisation pour créer un processus de manutention des matériaux transparent.
- Chargeurs de feuilles:Chargez automatiquement les feuilles de matériau sur la machine de découpe laser, réduisant ainsi l'effort manuel et augmentant l'efficacité.
- Déchargeurs partiels:Retirez automatiquement les pièces finies du lit de coupe, garantissant un fonctionnement fluide et continu.
4. Systèmes de contrôle
Les systèmes de contrôle gèrent le fonctionnement des équipements de chargement et de déchargement, garantissant un mouvement précis et coordonné des matériaux. Ces systèmes peuvent être autonomes ou intégrés à la commande CNC de la machine de découpe laser.
- Contrôleurs logiques programmables (PLC):Les PLC sont utilisés pour contrôler la séquence d'opérations dans les systèmes automatisés, garantissant des performances précises et fiables.
- Interfaces homme-machine (IHM):Les IHM fournissent aux opérateurs une interface conviviale pour surveiller et contrôler le processus de chargement et de déchargement.
Avantages des systèmes de chargement et de déchargement automatisés
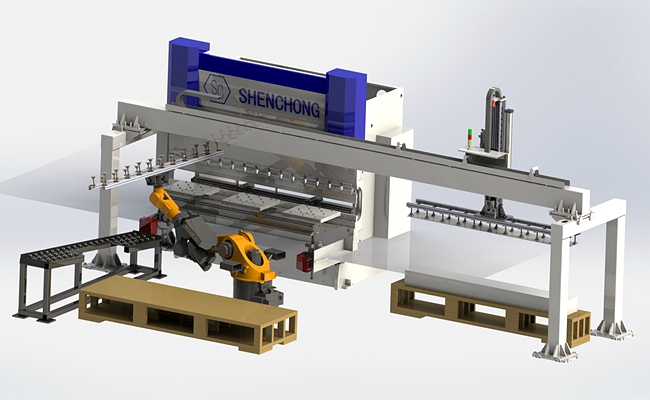
1. Productivité accrue
Système automatisé de chargement et de déchargement de tôles Le temps de chargement et de déchargement des matériaux est considérablement réduit, ce qui permet à la machine de découpe laser de fonctionner en continu. Cette productivité accrue se traduit par un rendement plus élevé et des délais d'exécution plus rapides.
2. Économies sur les coûts de main-d'œuvre
En automatisant les processus de manutention, les fabricants peuvent réduire leur recours au travail manuel. Cela permet non seulement de réduire les coûts de main-d'œuvre, mais aussi de minimiser le risque d'erreur humaine, garantissant ainsi une production constante et de haute qualité.
3. Sécurité améliorée
Les systèmes de chargement et de déchargement automatisés améliorent la sécurité sur le lieu de travail en réduisant le besoin d'interaction humaine avec des matériaux lourds et potentiellement dangereux. Cela minimise le risque d'accidents et de blessures, créant ainsi un environnement de travail plus sûr.
4. Cohérence et qualité
L'automatisation garantit une manipulation homogène des matériaux, ce qui est essentiel pour maintenir des normes de qualité élevées dans le processus de découpe laser. Les systèmes automatisés peuvent positionner les matériaux avec précision, réduisant ainsi le risque de désalignement et garantissant des coupes précises.
5. Optimisation de l'espace
Les systèmes de stockage et de récupération avancés peuvent optimiser l'utilisation de l'espace disponible, permettant aux fabricants de stocker davantage de matériaux dans un espace réduit. Cela est particulièrement avantageux dans les environnements où l'espace est limité.
6. Flexibilité
Les systèmes automatisés peuvent être programmés pour gérer différents types de matériaux et tailles de pièces, offrant ainsi une certaine flexibilité dans la production. Cette adaptabilité est essentielle pour les fabricants qui fabriquent une grande variété de produits ou qui modifient fréquemment les cycles de production.
Études de cas
1. Constructeur automobile
Un constructeur automobile a mis en place un système de chargement et de déchargement entièrement automatisé pour ses machines de découpe laser. Le système comprenait des bras robotisés, des convoyeurs et un système de stockage et de récupération avancé. Le résultat a été une augmentation de 40% de la productivité, une réduction de 30% des coûts de main-d'œuvre et une amélioration de la sécurité pour les opérateurs.
2. Fournisseur de composants aérospatiaux
Un fournisseur de composants aéronautiques a intégré des systèmes de chargement et de déchargement automatisés à ses machines de découpe laser. Les systèmes ont été équipés de capteurs et d'algorithmes d'IA pour une surveillance et une optimisation en temps réel. Cette intégration a permis de réduire de 50% les temps de configuration, d'augmenter de 25% le débit de production et d'améliorer le contrôle qualité.
3. Fabricant d'électronique
Un fabricant de composants électroniques a adopté un système de chargement et de déchargement semi-automatique pour ses opérations de découpe au laser. Le système comprenait des changeurs d'outils et des convoyeurs automatisés pour la manutention des matériaux. La mise en œuvre a permis de réduire le temps de manutention des matériaux, d'améliorer la précision et d'assurer une qualité constante dans la production de composants électroniques.
Points à considérer avant d'acheter
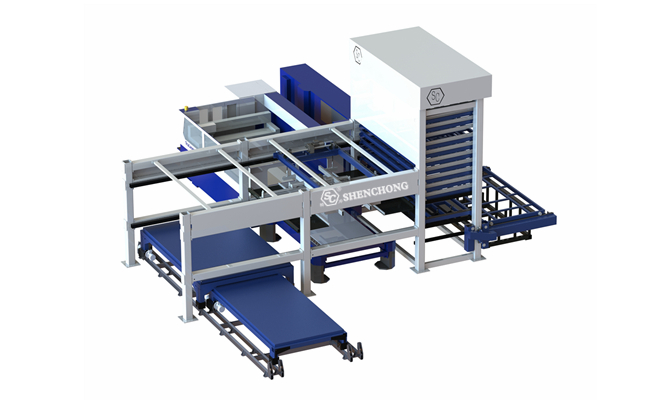
Lors de l'achat d'un système d'automatisation de chargement et de déchargement de métaux, il est essentiel de prendre en compte soigneusement divers facteurs pour garantir que le système répond à vos exigences de production et à vos besoins à long terme. Voici les points clés à évaluer.
1. Capacités de manutention des matériaux
- Type de métal: Assurez-vous que le système est compatible avec les métaux spécifiques avec lesquels vous travaillez (par exemple, l’acier, l’aluminium, etc.).
- Poids et taille:Confirmez que le système peut gérer le poids, la taille et l’épaisseur des matériaux à traiter.
- Dimensions de la feuille/pièce: Assurez-vous que le système s’adapte à la gamme de dimensions requises par votre opération.
2. Niveau d'automatisation
- Manuel, semi-automatisé ou entièrement automatisé:Déterminez si vous avez besoin d’une automatisation complète ou si un système semi-automatisé suffirait.
- Intégration robotique:Évaluez si des bras robotisés ou d’autres technologies automatisées sont nécessaires pour votre application spécifique.
- Efficacité du flux de travail:Réfléchissez au degré d’automatisation du processus qui doit correspondre à votre vitesse de production et réduire les temps d’arrêt.
3. Capacité et débit
- Vitesse de chargement/déchargement:Vérifiez que le système peut gérer le débit requis pour correspondre à votre rythme de production.
- Durée du cycle:Analysez les temps de cycle des opérations de chargement et de déchargement pour vous assurer qu'ils correspondent à votre calendrier de production global.
- Chargement par lots ou en continu:En fonction de votre échelle de production, déterminez si un système de chargement par lots ou continu est plus approprié.
4. Compatibilité et intégration du système
- Intégration CNC/Presse: Assurez-vous que le système s’intègre bien à vos machines CNC, lasers ou autres machines de découpe et de pliage.
- Compatibilité logicielle:Vérifiez si le système est compatible avec votre logiciel de gestion de production ou vos systèmes ERP existants.
- Contrôles d'automatisation:Revoyez l’interface utilisateur et les systèmes de contrôle pour faciliter l’utilisation et l’intégration avec d’autres machines dans le flux de travail.
5. Espace et aménagement
- Empreinte: Tenez compte de l'espace physique que le système occupera. Vérifiez qu'il s'intègre dans votre zone de production sans perturber le flux de travail.
- Accessibilité: Assurez-vous que le système est facilement accessible pour la maintenance, le chargement des matières premières et le déchargement des pièces finies.
6. Options de personnalisation
- Conception modulaire:Recherchez des systèmes avec des configurations modulaires qui permettent une extension ou une personnalisation future en fonction de l’évolution des besoins de production.
- Solutions sur mesure:Vérifiez si le fournisseur propose des options de personnalisation en fonction de vos besoins matériels ou opérationnels spécifiques.
7. Caractéristiques de sécurité
- Capteurs et protections de sécurité: Assurez-vous que le système dispose de mécanismes de sécurité robustes tels que des boutons d’arrêt d’urgence, des capteurs et des protections physiques pour protéger les opérateurs.
- Conformité aux normes: Vérifiez que le système est conforme aux normes de sécurité locales et internationales, telles que les réglementations ISO ou OSHA.
8. Coût et retour sur investissement
- Coût initial:Analysez l’investissement initial et comparez-le aux avantages attendus, tels qu’une productivité accrue ou une réduction des coûts de main-d’œuvre.
- Coûts d'entretien:Tenez compte des coûts de maintenance à long terme et de la disponibilité des pièces de rechange.
- Retour sur investissement:Calculez le retour sur investissement du système en fonction de sa capacité à réduire la main-d'œuvre, à augmenter l'efficacité ou à gérer des tâches plus complexes.
9. Maintenance et support
- Contrats de service:Évaluez la garantie et le service d’assistance fournis par le fabricant.
- Exigences d'entretien:Vérifiez la facilité d’entretien du système, la disponibilité des pièces de rechange et la fréquence de la maintenance requise.
- Formation et installation: Assurez-vous que le fournisseur offre une formation adéquate à votre équipe et fournit une assistance lors de l'installation et de la configuration.
10. Réputation et références du fournisseur
- Expérience du fournisseur: Examinez l’expérience du fournisseur en matière de fourniture de systèmes d’automatisation pour votre secteur.
- Avis des clients:Envisagez de demander des références aux utilisateurs actuels du système pour évaluer la fiabilité et les performances dans les applications du monde réel.
- Assistance après-vente:Évaluer la qualité du service après-vente, y compris le support technique, le temps de réponse et la disponibilité des pièces de rechange.
11. Impact environnemental
- Consommation d'énergie:Analyser l’efficacité énergétique du système pour maintenir les coûts d’exploitation bas et minimiser l’impact environnemental.
- Niveaux de bruit:Envisagez des fonctionnalités de réduction du bruit si votre environnement de production présente des contraintes de niveau de bruit.
Une évaluation minutieuse de ces facteurs vous aidera à sélectionner un système qui répond à vos besoins de production, augmente l’efficacité et offre une valeur à long terme.
Gamme de prix des systèmes de chargement et de déchargement de tôles
La fourchette de prix des systèmes d'automatisation de chargement et de déchargement des métaux peut varier considérablement en fonction de facteurs tels que la taille du système, sa capacité, son niveau d'automatisation, sa marque et ses fonctionnalités spécifiques (par exemple, l'intégration CNC, la robotique et les fonctionnalités de sécurité avancées). En général, ces systèmes se situent dans les fourchettes de prix suivantes :
- Systèmes de base:Pour les configurations plus petites ou moins complexes, les prix varient généralement de $20 000 à $50 000.
- Systèmes de milieu de gamme:Les systèmes dotés de capacités modérées, d'une meilleure automatisation et d'options d'intégration coûtent généralement entre $50 000 et $150 000.
- Systèmes haut de gamme:Les systèmes très avancés dotés de fonctionnalités telles que l'automatisation complète, la robotique intégrée et des capacités plus importantes peuvent aller de $150 000 à $500 000 ou plus.
La personnalisation et les fonctionnalités supplémentaires telles que l'intégration de logiciels ou des mécanismes de sécurité supplémentaires peuvent également influer sur les prix. Pour un devis spécifique, contactez les fournisseurs pour obtenir un chiffre plus précis et adapté à vos besoins.
Tendances futures des systèmes de chargement et de déchargement
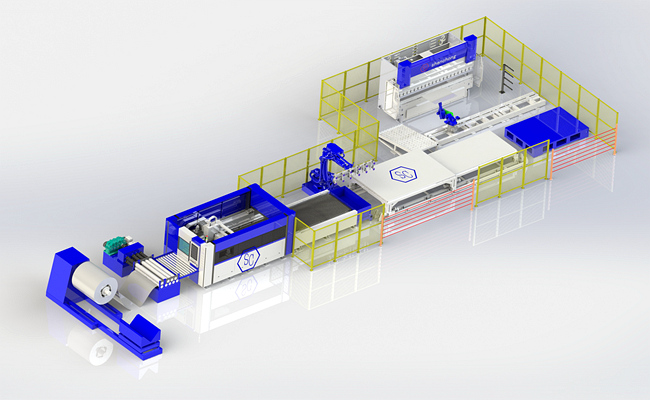
1. Intégration avec l'Industrie 4.0
L'intégration des systèmes de chargement et de déchargement avec les technologies de l'industrie 4.0, telles que l'Internet des objets (IoT), l'intelligence artificielle (IA) et l'apprentissage automatique, est sur le point de révolutionner la manutention des matériaux. Ces technologies permettent une surveillance en temps réel, une maintenance prédictive et une prise de décision basée sur les données, améliorant ainsi l'efficacité et la fiabilité des systèmes automatisés. Pour se connecter à d'autres unités d'automatisation telles que le système de stockage automatique des métaux, presse plieuse robotisée, machine de découpe laser de déroulement et de nivellement, l'usine de traitement de tôle peut intégrer lignes de production automatisées de tôlerie.
2. Robotique avancée
Les progrès de la robotique favorisent le développement de systèmes automatisés plus sophistiqués et plus performants. Les robots collaboratifs (cobots) qui peuvent travailler aux côtés d'opérateurs humains et les robots mobiles autonomes (AMR) qui naviguent et transportent des matériaux de manière autonome sont de plus en plus répandus.
3. Flexibilité améliorée
Les futurs systèmes de chargement et de déchargement automatiques de tôles offriront une plus grande flexibilité, permettant aux fabricants de passer facilement d'un matériau à l'autre et d'une taille de pièce à l'autre. Les systèmes modulaires et reconfigurables permettront une adaptation rapide aux exigences changeantes de la production.
4. Efficacité énergétique
La durabilité devenant une priorité, les systèmes de chargement et de déchargement des métaux seront conçus dans un souci d'efficacité énergétique. Des innovations telles que des moteurs à haut rendement énergétique, des systèmes de freinage régénératif et une gestion intelligente de l'énergie réduiront l'impact environnemental de la manutention automatisée des matériaux.
5. Interfaces utilisateur améliorées
Des interfaces conviviales et des systèmes de contrôle intuitifs amélioreront la facilité d'utilisation et l'accessibilité des systèmes de chargement et de déchargement automatisés. Des IHM avancées et des interfaces de réalité augmentée (AR) fourniront aux opérateurs des informations et des conseils en temps réel, améliorant ainsi l'efficacité globale.
Conclusion
Les systèmes de chargement et de déchargement des machines de découpe laser sont des composants essentiels qui améliorent la productivité, réduisent les coûts de main-d'œuvre et améliorent la sécurité dans les environnements de fabrication. Des systèmes manuels aux systèmes entièrement automatisés, ces technologies offrent une gamme de solutions pour répondre aux divers besoins des différentes industries. Alors que les progrès de la robotique, de l'IA et des technologies de l'industrie 4.0 continuent d'évoluer, l'avenir de la manutention automatisée des matériaux semble prometteur, offrant une efficacité, une flexibilité et une durabilité encore plus grandes.
Les fabricants qui investissent dans des systèmes de chargement et de déchargement avancés peuvent s'attendre à des améliorations significatives de leurs processus de production, leur permettant de rester compétitifs sur un marché de plus en plus exigeant. En comprenant les avantages, les applications et les tendances futures de ces systèmes, les entreprises peuvent prendre des décisions éclairées et exploiter tout le potentiel de leurs opérations de découpe laser.