Table of Contents
Flame cutting machine is a cutting equipment that uses gas with oxygen or gasoline with oxygen to cut metal materials. Flame cutting uses a mixture of oxygen and acetylene gas to cut metals. The flame heats the metal sheet to a high temperature, burns a small part, and forms a cut. Laser cutting machines use extremely powerful laser beams to accurately cut materials. Laser cutting is very suitable for complex and high-precision cutting, while flame cutting is more suitable for thicker materials. This article will explore the differences between laser cutting machines and flame cutting machines by introducing and analyzing their advantages and disadvantages.
What Is Flame Cutting?
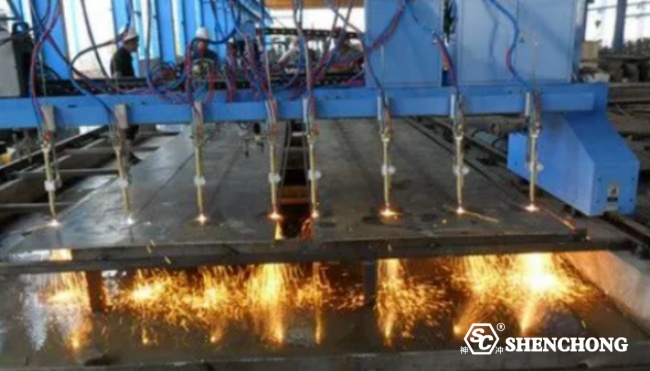
Principle Of Flame Cutting
Flame cutting is a common method for rough machining of steel plates. Flame cutting, also known as oxygen fuel cutting, uses an oxygen acetylene gas mixture to cut metals. The flame is directed onto the material, which is then heated to a high temperature and burned off. The design of the flame cutting torch provides sufficient oxygen for burning iron oxide to ensure a good cutting effect. This method can cut many types of metals, but it is most suitable for thicker materials. This process is quite simple and cost-effective, making it a popular choice for many sheet metal processing businesses.
Flame cutting devices typically include cutting torches, oxygen cylinders, and acetylene cylinders. Gas is transported to the cutting torch through a hose. The sparks emitted by the torch ignite oxygen and acetylene gases, which burn at a temperature sufficient to cause the metal to evaporate. The maximum temperature of this process is about 3500℃, which means even high melting point metals can be cut in this way.
Flame Cutting Machine
Flame cutting machine is composed of a cutting torch, a fixed length mechanism, and a cutting seam cleaning device that works similarly to a flame gun. There are mechanical, pulse, and photoelectric measuring mechanisms that can achieve automatic measuring. The cutting seam cleaning device is specifically designed to clean the residue adhered to the cutting seam to prevent affecting the surface quality of the steel during rolling. The cleaning method involves scraping off sticky residue with a scraper, as well as using a set of high-speed rotating sharp hammers to remove sticky residue and burrs. Flame cutting machines are often used as online cutting equipment for steel billets after continuous casting machines, cutting large section billets, slabs, and large tube billets. They are also used to cut finished steel plates with a thickness greater than 50mm.
CNC flame cutting machine is the earliest applied CNC cutting equipment. The introduction of CNC technology into flame cutting has achieved automation of the entire cutting process, significantly improving the cutting quality of steel plates (size amplitude and cutting quality, which can replace some mechanical processing), high production efficiency (continuous cutting, multi gun cutting), and high material utilization (nesting cutting).
Cutting Quality Of Flame Cutting Machine
The quality of cutting not only depends on the performance, flute degree, and reliability of CNC machine tools, but also closely related to the quality of gas used, the quality of cutting programs, and the quality of operators. The common problems of flame cutting machine in production are cutting deformation, rough surface of the cutting surface, and severe stains. To reduce cutting deformation, a reasonable switching process (cutting starting point, direction, and sequence) should be selected, and bridging (intermittent cutting) should be considered. The support bracket for the steel plate should be flat and stable, and the dryness of the steel plate should be improved. Improving the purity and pressure stability of oxygen and acetylene is the fundamental guarantee for improving the efficiency of CNC flame cutting machines and obtaining high-quality cutting surfaces. By using liquid oxygen cutting, the quality of the cutting surface is significantly improved due to stable pressure and purity of over 99.5%. There is very little slag hanging, and the cutting speed is greatly improved.
Flame Cutting Machine Control System
The computer-aided programming nesting system is a supporting equipment for CNC cutting machines. It is the fundamental guarantee for quickly and correctly programming CNC programs and improving the utilization rate of steel plate materials. Computer assisted programming involves inputting part graphics. It consists of four major steps: slanting, cutting process, and post-processing. The quality of programming software is mainly reflected in the speed of graphic input and nesting, as these two parts occupy the most time of the entire programming work. It should have fast graphic input and convenient inspection and modification. The nesting has fully automatic multi-level nesting and manual layout functions, as well as strong part management and production management functions. It can automatically or manually determine the cutting process, and has convenient bridging functions.
Precautions For Using Flame Cutting Machines
During the process of using a CNC flame cutting machine for cutting, various cutting defects often occur. To improve cutting quality, here is a brief introduction to the key points of quality control in different cutting situations:
- Key points to pay attention to in forging cutting.
Due to the thick oxide skin on the surface of the forging, and the fact that the ignition point of the oxide skin is higher than the melting point, cutting interruption is prone to occur during cutting, resulting in a decrease in cutting quality and work efficiency. Therefore, when cutting forgings, the oxide skin on the upper and lower surfaces in the cutting area should be removed first before cutting to improve cutting speed and quality.
- Key points for preventing deformation during cutting of cold bed toothed plates for rolling square billets.
It is very important to control the deformation of the workpiece in cutting. For example, arranging the cutting route according to convention can cause deformation and deviation of the workpiece. Even if it is shaped, it is difficult to meet the size requirements, and ultimately the product will be scrapped. Therefore, arranging the gas cutting route reasonably is crucial.
- Key points to pay attention to in thick plate cutting.
In the cutting of thick steel plates, the temperature decreases from the top surface downwards. At the beginning of cutting, the oxygen pressure gradually increases and finally reaches consistency in the thickness direction of the steel plate. This causes inconsistent combustion in the thickness direction of the steel plate at the starting position of cutting, resulting in defects at the starting end of the workpiece cutting.
To avoid defects, the following methods can be used:
- Using circular arc feed to increase the length of the lead in line and avoid direct entry points. This method has good effectiveness and is widely used in production, but its disadvantage is the waste of materials.
- Use ignition rods. The method is to increase the thickness of the steel plate by one piece at the entry point, without any gaps. The cutting blade should be inserted from the ignition rod, which will guide the flame of the cutting tool to the bottom of the steel plate, so that the combustion speed of the steel plate is consistent, and the optimal cutting section surface is obtained. The ignition rod can be replaced with cut scraps. This method reduces the distance between the workpiece and the edge of the plate, reduces the generation of corner scraps, and effectively improves the utilization rate of the plate. The ignition rod is more practical in cutting ultra-thick steel plates.
What Is Laser Cutting?
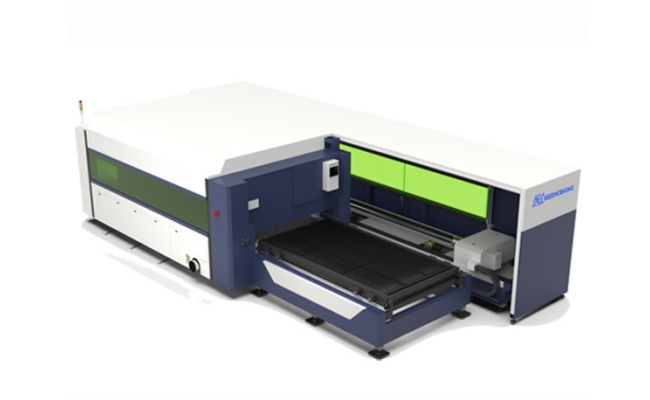
Principle Of Laser Cutting
Laser cutting is the use of laser to cut materials. Laser cutting processing replaces traditional mechanical knives with invisible beams of light. It has the characteristics of high precision, fast cutting, not limited to cutting pattern limitations, automatic layout saving materials, smooth cutting, and low processing costs. It will gradually improve or replace traditional metal cutting equipment. The laser beam is concentrated through a lens, which then focuses it on a specific area. This laser beam is very powerful and can cut materials with high precision and precision. Laser cutting has good effects on materials such as acrylic acid, wood, paper, and metal. The mechanical part of the laser blade does not come into contact with the workpiece, so it will not cause scratches on the surface of the workpiece during operation. Laser cutting speed is fast, the incision is smooth and flat, and generally does not require subsequent processing. Cutting heat affected zone is small, plate deformation is small, and cutting seam is narrow (0.1mm~0.3mm). The incision has no mechanical stress and no shear burrs. High machining accuracy, good repeatability, and no damage to the material surface. CNC programming can process any flat drawing, and can cut large whole boards without the need for molds, which is economical and time-saving. It can also allow you to create complex designs that are difficult or impossible to achieve with flame cutting.
Laser Cutting Machine
Laser cutting machines are complex and expensive machines, ranging from basic laser cutting machines to laser engraving machines. They usually require a cooling system and high-end power supply to function properly. Laser emitters typically move very precisely on materials under computer control. Specialized optical devices focus the laser beam and guide it along the cutting path.
Difference Between Laser Cutting Machine And Flame Cutting Machine
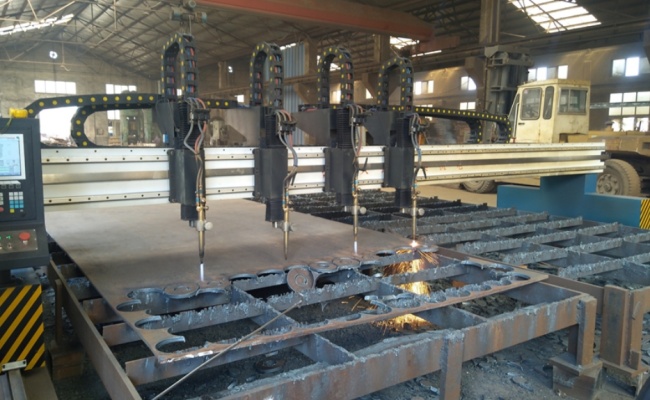
When comparing laser cutting and flame cutting, the following key factors need to be considered:
1. Universality
A Laser cutting machine is a more universal choice. Compared with traditional flame cutting machines, laser cutting machines have fast cutting speed, narrow cutting seams, small heat affected zone, good perpendicularity of cutting seam edges, smooth cutting edges, and a wide variety of materials that can be laser cut, including metal and non-metal. (Carbon steel, stainless steel, alloy steel, wood, plastic, rubber, cloth, quartz, ceramics, glass, composite materials, etc.). Due to the fact that laser cutting machines are pre programmed, it is easier to achieve automation in large-scale production operations. On the other hand, flame cutting machines can only cut metal materials.
2. Cutting Accuracy
The accuracy of laser cutting machines is far superior to that of flame cutting machines. The laser beam is focused into a very fine diameter and can achieve accuracy of up to 0.0005 inches (0.0127 millimeters). Flame cutting cannot achieve such accuracy, so laser cutting is the preferred choice for complex designs or precision tolerances.
The accuracy of a laser cutting machine is determined by the following factors.
- The size of laser condensation in the laser generator. If the light spot is very small after aggregation, the cutting accuracy is very high, and if the gap after cutting is also very small. This indicates that the precision of the laser cutting machine is very high, while the quality is very high. But the beam emitted by the laser is conical, so the gaps cut out are also conical. Under these conditions, the thicker the workpiece, the lower the accuracy, resulting in a larger cutting seam.
- The accuracy of the workbench. If the accuracy of the workbench is very high, it will also improve the cutting accuracy. Therefore, the accuracy of the workbench is also a very important factor in measuring the accuracy of the laser generator.
- The laser beam condenses into a cone. When cutting, the laser beam is conical downwards. If the thickness of the workpiece being cut is very large, the cutting accuracy will decrease, and the gaps will be very large.
- The different materials used for cutting can also affect the accuracy of the laser cutting machine. In the same situation, the accuracy of cutting stainless steel and aluminum will be very different. The cutting accuracy of stainless steel will be higher, and the cutting surface will also be smoother.
3. Cutting Quality
The laser beam forms a clean, smooth surface without burrs or sharp edges. This is particularly useful when using materials such as acrylic and wood that may require a smooth finish. On the other hand, the focus of the flame cutting machine is not very precise, which can cause some melted materials to solidify at the edges, ultimately leaving a rough surface.
Generally speaking, the quality of laser cutting can be measured by the following six standards.
- Cutting surface roughness
- Cutting slag size
- Trimming verticality and slope
- Cutting edge fillet size
- Stripe drag amount
- Flatness
4. Cutting Waste
The material waste generated by laser cutter is very small because the laser beam is very precise. In contrast, flame cutting machines melt much more material at once and may also produce imperfect edges that may need to be flattened later. Overall, more metal materials will be lost as a result.
5. Cost
Due to the complexity of laser cutting machines and the cost of laser equipment and supplies, a laser cutting machine is more expensive than a flame cutting machine.
Machine Purchase Cost
The price of laser cutting machines ranges from $25800 to $122000, while the price of flame cutting machines ranges from $2800 to $3500.
Operation Cost
The operation cost of a flame cutting machine mainly comes from cheap consumables such as gas, mechanical transmission electricity, and cutting nozzles. Compared to lasers, it is quite cheap.
The operating costs of laser cutting include:
- Electricity cost (mainly including the electricity consumption of the laser+the electricity consumption of the water cooler+the electricity consumption of the machine tool+the electricity consumption of the air compressor).
- The cost of maintenance. Laser cutting machines are different from flame cutting machines and require regular maintenance. Usually, it takes one to two times a year, or even more.
- There are two types of gases, one is laser gas and the other is auxiliary gas (auxiliary gas includes oxygen and nitrogen).
- The cost of consumables. Although there are not many consumables for laser cutting machines, the usage cycle is relatively long. But the unit price is relatively expensive.
6. Impacts On The Working Environment During The Cutting Process
The working process of laser cutter is relatively quiet and safe, and there is less gas or smoke emitted during the cutting process. On the other hand, flame cutting is a noisy and potentially dangerous process that involves flammable gases and open flames.
7. Is Laser And Flame Cutting Safe To Use?
Yes, laser cutting and flame cutting operations are safe if appropriate safety protocols are followed. Operators using laser cutting machines must wear protective goggles, protective clothing, and respirators to protect them from laser radiation and harmful smoke. For flame cutting, operators must ensure that the area is well ventilated, free of any flammable materials, and must also wear protective clothing and respirators to protect them from harmful smoke. Ultimately, if safety protocols are followed and equipment is properly maintained, both laser cutting and flame cutting are safe.
When Choose Laser Cutting Or Flame Cutting?
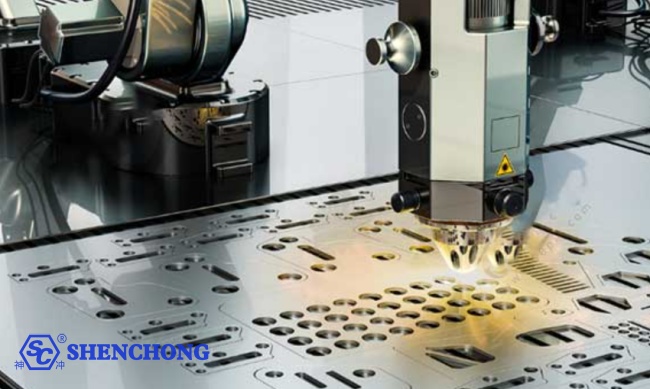
The choice between laser cutting and flame cutting depends on the materials to be cut and the cutting accuracy requirements. Due to its versatility, precision, and economy in large-scale production, laser cutting is more commonly chosen for cutting workpieces with high precision and waste reduction requirements. Meanwhile, flame cutting is more suitable for cutting thick plates with less important accuracy. Ultimately, it is important to evaluate the project at hand and consider both options to determine which one is more cost-effective and efficient.
Choose Flame Cutting Machine
The advantages of flame cutting machines are large thickness cutting and low cost. There is a significant efficiency advantage compared with laser cutter, especially to cut the sheet metal plate thickness exceeds 50mm. Flame cutting machine can even cut metal sheets up to 200mm thick. Flame cutting machines are generally used for cutting common metals such as low-carbon steel, copper, and aluminum. However, it cannot cut high carbon steel, stainless steel, cast iron, etc., and has a large heat affected zone, severe deformation of thick plates, and high operational difficulty.
Choose Laser Cutter
The cutting range of laser cutting is very wide, whether it is metal or non-metal. Laser cutting machine has narrow cutting width, high accuracy, excellent cutting surface roughness, and fast cutting speed. It is especially suitable for cutting thin sheets, such as cutting thicknesses below 25mm. However, its equipment cost is high, and the efficiency of thick plate cutting is significantly reduced.
Can Laser Cutting Be Used To Cut Thick Materials?
Yes, lasers can penetrate thick materials as long as they have sufficient power. High power usually means a larger laser head. Laser cutting of thick materials may also require additional laser head passes, which will reduce the overall cutting speed and make the operation more expensive. At present, the competition in the laser cutting machine industry is very fierce in the market, and various laser cutting machine manufacturers are pursuing higher power. China has already produced 120000 watts laser cutting machines.
What Materials Can Be Laser Cut?
There are several materials that can be laser cut, including metal, plastic and glass. Although the materials that can be laser cut will depend on the type of laser used. For example, some laser cutting machines can only cut certain materials, while others can cut multiple materials. If a CO2 laser cutting machine is used, it can cut various materials, including wood, plastic, glass, and metal. On the other hand, fiber laser cutting machines can cut stainless steel, aluminum, and brass.
What Materials Cannot Be Cut With Laser?
Materials that cannot be laser cut include high reflective materials such as mirrors, thin materials that are prone to bending or melting, and materials that are hazardous for cutting, such as asbestos or explosives.
What Is The Difference Between Flame, Plasma, And Laser Cutting?
The main difference between flame cutting and plasma cutting lies in the type of energy used. Flame cutting uses an oxygen acetylene torch, while plasma cutting uses an accelerated jet of hot plasma. Flame cutting is slower and less precise than plasma cutting, but it can be operated on thicker materials. On the other hand, plasma cutting is faster and more precise, but its maximum cutting depth is smaller than flame cutting.
- The flame cutting machine has a significant advantage in efficiency and the lowest cost when cutting metal sheets with a thickness exceeding 50mm.
- Plasma cutting machines have high cutting efficiency when processing metal sheets with a thickness of 6-40mm.
- Laser cutting machines are currently widely used for processing metal sheets ranging from 6-40mm. Due to the decrease in prices of laser cutting machines in recent years, laser cutting machines have basically replaced the role of plasma cutting machines.
Summary
This article introduces the principles and concepts of laser cutting and flame cutting, and discusses their processing scope, applications, advantages and disadvantages.