Introduction
Table of Contents
Fiber laser cutting machine advantages and disadvantages are most important aspects for users to consider before they purchase the machine. Fiber laser cutting machines have revolutionized the manufacturing and fabrication industries with their precision, speed, and efficiency. These machines use fiber laser technology to cut through various materials with high accuracy, making them indispensable tools in many industrial applications. However, like any advanced technology, fiber laser cutting machines come with their own set of advantages and disadvantages. This article provides an in-depth exploration of these benefits and drawbacks, along with a detailed understanding of how fiber laser cutting machines work and their applications across different industries.
Fiber Laser Cutting Machine Overview
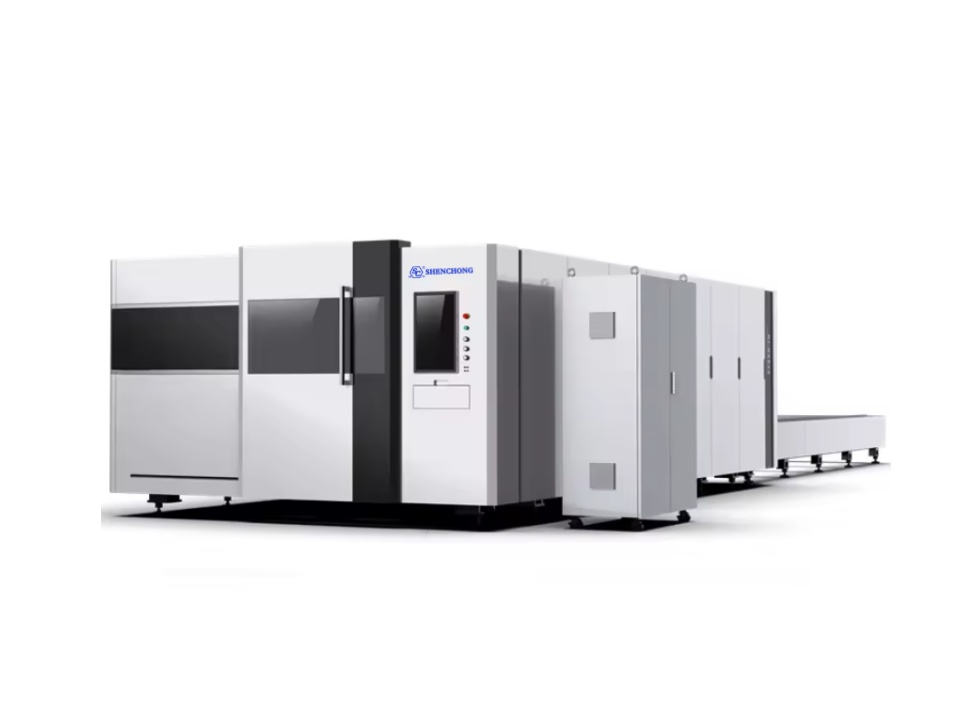
Historical Context
The development of fiber lasers can be traced back to the early 1960s, but it wasn’t until the late 1990s and early 2000s that fiber laser technology became commercially viable for industrial applications. The advancements in optical fiber technology, high-power diode lasers, and precision control systems paved the way for the modern fiber laser cutting machines we see today. These machines have since transformed numerous industries, from automotive and aerospace to electronics and metal fabrication.
How Fiber Laser Cutting Machines Work
Fiber laser cutting machine utilize a fiber laser, which is a type of solid-state laser. The laser beam is generated by a series of diodes and then transmitted through a flexible optical fiber. This fiber amplifies the beam, producing a highly concentrated and intense laser that is then directed onto the material to be cut. The interaction between the laser beam and the material results in the precise cutting, engraving, or marking of the material. Key components of a fiber laser cutting machine include:
- Laser Source: The source of the laser beam, typically composed of multiple diodes.
- Optical Fiber: Transmits and amplifies the laser beam.
- Cutting Head: Focuses the laser beam onto the material.
- CNC Controller: Controls the movement of the cutting head and the material, ensuring precise cutting.
- Assist Gas System: Uses gases such as nitrogen or oxygen to enhance the cutting process by removing molten material and preventing oxidation.
Applications of Fiber Laser Cutting Machines
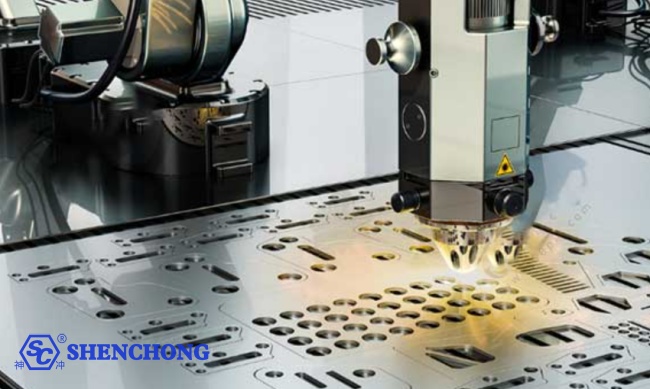
1. Automotive Industry
The automotive industry relies heavily on fiber laser cutting machines for precision cutting and shaping of various components, including body panels, engine parts, and interior elements. The high speed and accuracy of fiber lasers enhance production efficiency and quality control.
2. Aerospace Industry
In the aerospace sector, fiber laser cutting is used for manufacturing complex parts and assemblies with high precision and minimal material waste. The ability to cut lightweight and durable materials, such as titanium and aluminum, makes fiber lasers ideal for aerospace applications.
3. Metal Fabrication
Fiber laser cutting machines are extensively used in metal fabrication for cutting, engraving, and marking metals. Their versatility allows for the production of intricate designs and the efficient handling of both thin and thick metal sheets, catering to a wide range of fabrication needs.
4. Electronics and Electrical Industry
The electronics industry benefits from fiber laser cutting for producing precise and intricate components, such as circuit boards, connectors, and enclosures. The accuracy and repeatability of fiber lasers ensure the reliability and performance of electronic devices.
5. Medical Device Manufacturing
Fiber laser cutting is crucial in the medical device industry for producing intricate and precise components, such as surgical instruments, implants, and diagnostic equipment. The cleanliness and precision of laser cutting meet the stringent standards required for medical applications.
6. Jewelry and Fashion
The jewelry and fashion industries utilize fiber laser cutting machines to create intricate and detailed designs on various materials, including metals, leather, and fabrics. The precision and flexibility of fiber lasers enable designers to bring their creative visions to life with high-quality results.
7. Signage and Advertising
In the signage and advertising industry, fiber laser cutting machines are used to produce high-quality signs, displays, and promotional materials. The ability to cut and engrave various materials with precision and speed makes fiber lasers a popular choice for creating eye-catching and durable signage.
Fiber Laser Cutting Machine Advantages And Disadvantages Introduction
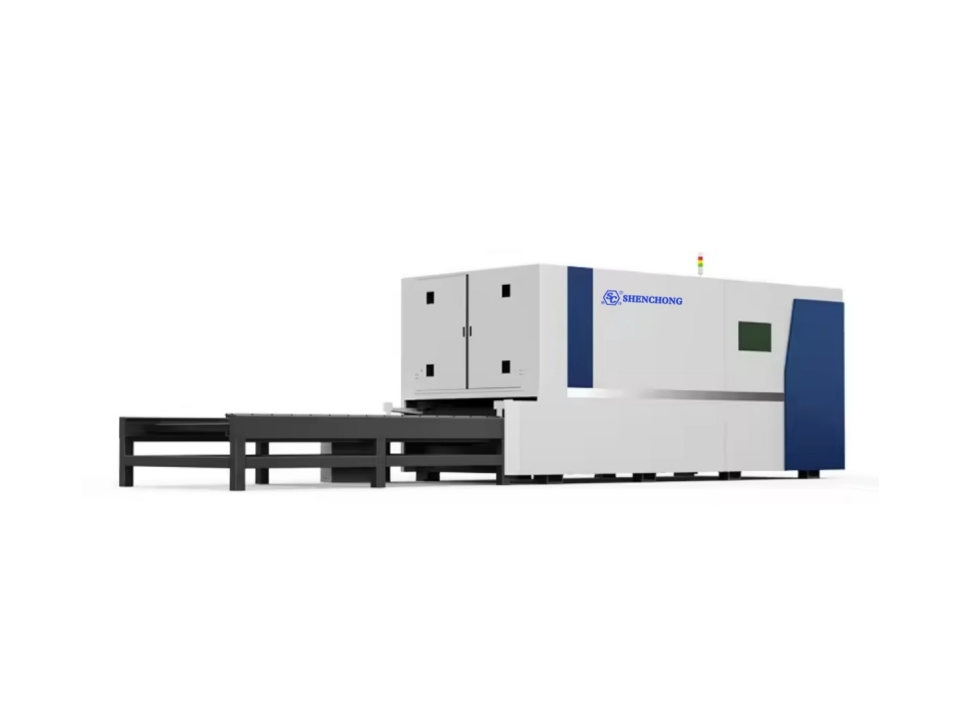
Advantages of Fiber Laser Cutting Machines
1. High Precision and Accuracy
Fiber laser cutting machines are renowned for their high precision and accuracy. The focused laser beam can cut complex shapes and intricate designs with minimal tolerance. This precision is particularly beneficial for industries requiring detailed work, such as electronics, jewelry, and medical device manufacturing.
2. Speed and Efficiency
One of the most significant advantages of fiber laser cutting machines is their cutting speed. These machines can cut through materials much faster than traditional cutting methods, such as mechanical cutting or CO2 lasers. This increased speed translates to higher productivity and shorter lead times, making fiber laser cutting machines ideal for high-volume production environments.
3. Versatility In Material Handling
Fiber lasers can cut a wide variety of materials, including metals (such as steel, aluminum, brass, and copper), plastics, ceramics, and composites. This versatility makes them suitable for diverse applications across different industries. Additionally, fiber lasers can handle both thin and thick materials, further expanding their range of uses.
4. Low Maintenance and Operational Costs
Compared to CO2 lasers, fiber laser cutting machines have lower maintenance requirements. The absence of mirrors and the robustness of the fiber optic delivery system reduce the need for regular adjustments and replacements. Moreover, fiber lasers are more energy-efficient, consuming less power and generating less heat, which results in lower operational costs.
5. Enhanced Safety Features
Fiber laser cutting machines come with advanced safety features, including enclosed cutting areas and interlock systems, to protect operators from laser exposure. The automated nature of these machines also reduces the risk of human error and accidents, making them safer to use in industrial settings.
6. Minimal Material Waste
The high precision of fiber laser cutting minimizes material waste. The narrow kerf (cut width) ensures that less material is removed during the cutting process, which is especially important when working with expensive materials. This efficiency leads to cost savings and more sustainable manufacturing practices.
7. High Beam Quality and Stability
Fiber lasers produce a high-quality beam with a consistent and stable output. This quality results in clean and smooth cuts with minimal post-processing required. The stability of the laser output also ensures reliable and repeatable cutting performance, crucial for maintaining product quality.
Disadvantages of Fiber Laser Cutting Machines
1. High Initial Investment
The initial cost of acquiring a fiber laser cutting machine can be substantial. High-power fiber lasers and the sophisticated components required for precise control and operation contribute to the high price. This significant capital investment can be a barrier for small and medium-sized enterprises (SMEs) considering adopting this technology.
2. Limited Material Thickness
While fiber lasers are effective at cutting thin and moderately thick materials, they may struggle with very thick materials. For extremely thick metals, alternative cutting methods, such as plasma or waterjet cutting, may be more suitable. This limitation requires manufacturers to assess their material cutting needs carefully before investing in a fiber laser cutting machine.
3. Reflective Material Challenges
Highly reflective materials, such as copper and brass, can pose challenges for fiber laser cutting. The laser beam can reflect back into the machine, potentially causing damage to the laser source and optics. Although advancements in laser technology and protective measures have mitigated this issue to some extent, it remains a consideration for manufacturers working extensively with reflective materials.
4. Operator Training and Skill
Operating a fiber laser cutting machine requires specialized training and skills. While modern machines are equipped with user-friendly interfaces and automation features, understanding the nuances of laser parameters, material properties, and maintenance procedures is essential for optimal performance. Investing in operator training is crucial but adds to the overall cost and time required to implement the technology.
5. Potential Heat-Affected Zones
Laser cutting involves high temperatures that can create heat-affected zones (HAZ) on the material being cut. While fiber lasers produce less heat compared to other laser types, there is still a risk of thermal distortion or changes in material properties near the cut edges. This issue is particularly relevant for sensitive materials that require precise mechanical or structural integrity.
6. Environmental and Safety Concerns
Despite their advantages, fiber laser cutting machines can still pose environmental and safety concerns. The process generates fumes and particulates that may require proper ventilation and filtration systems to ensure a safe working environment. Additionally, the high-intensity laser beams necessitate strict safety protocols to prevent accidental exposure and injuries.
Fiber Laser Cutting Machine Compares With Other Cutting Methods
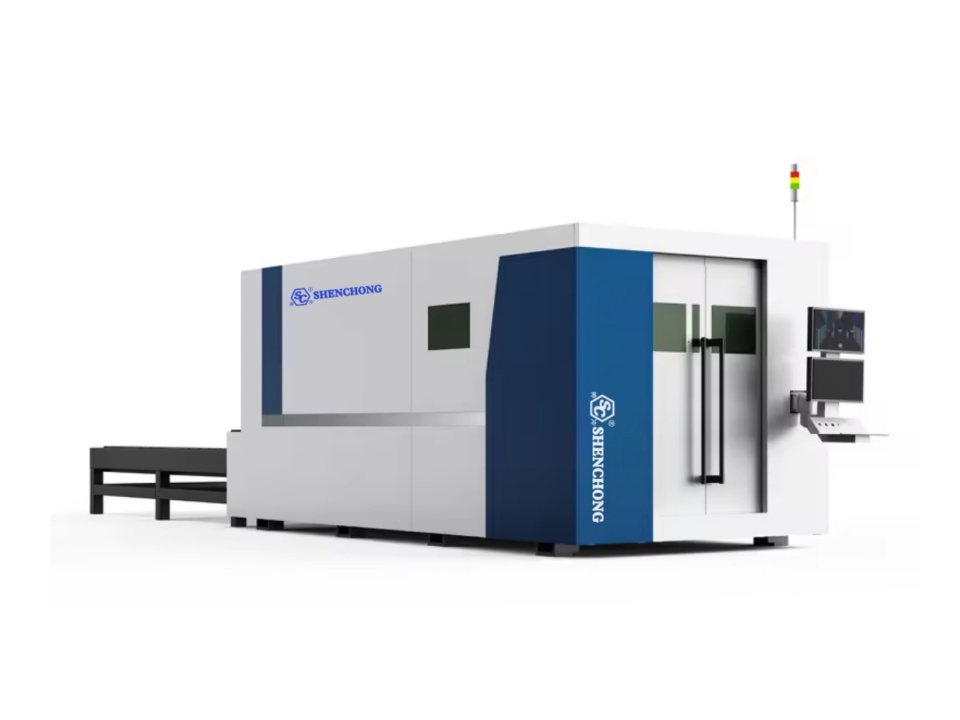
A. Fiber Laser Cutting Machine vs. CO2 Laser Cutting Machine
Comparison Project | Fiber Laser Cutting Machine | C02 Laser Cutting Machine |
Cutting accuracy | High precision, suitable for cutting complex shapes and details. | High precision, but not as good as fiber laser in fine structure and small hole processing |
Cutting materials | The most suitable for cutting metal materials such as stainless steel, carbon steel, aluminum, etc | Capable of cutting various materials, including metal and non-metal (such as wood, plastic, glass, etc.) |
Cutting thickness | Best suited for thin to medium thickness materials (0.5mm to 20mm) | Good performance when cutting thick metal sheets, especially for materials exceeding 10mm |
Cutting speed | The cutting speed for thin metal sheets is very fast | Slow cutting speed, especially on thin metal materials |
Cutting quality | Smooth cutting edge, small heat affected zone | The cutting edge has high quality, but the heat affected zone is relatively large |
Equipment cost | The initial equipment investment is relatively high, but the long-term operating cost is low | The initial equipment investment is relatively low, but the maintenance and operation costs are high |
Running cost | High energy efficiency and low operating costs, especially in metal processing | High energy consumption, especially in terms of cooling system and laser maintenance costs |
Maintain demand | Low maintenance requirements and long equipment lifespan | High maintenance requirements, optical components such as lenses and resonant cavities require frequent maintenance |
Operational complexity | The operation is relatively complex and requires professional technical personnel | The operation is relatively complex, especially in adjusting the optical system |
Applicable scenarios | Suitable for high-precision and large-scale metal processing | Suitable for cutting a wide range of materials, especially non-metallic materials |
Thermal impact | Small heat affected zone, suitable for cutting heat sensitive materials | The heat affected zone is relatively large, which may cause material deformation |
B. Fiber Laser Cutting Machine vs. Plasma Cutting Machine
Comparison Project | Fiber Laser Cutting Machine | Plasma Cutting Machine |
Cutting accuracy | High precision, suitable for cutting complex shapes and details | Low precision, especially when cutting thinner materials |
Cutting materials | Suitable for various metal materials such as stainless steel, carbon steel, aluminum, etc | Mainly used for cutting conductive materials such as steel, aluminum, etc |
Cutting thickness | Best suited for thin to medium thickness materials (0.5mm to 20mm) | Can cut thicker materials (up to several centimeters), especially in heavy industrial applications |
Cutting speed | The cutting speed for thin sheets is very fast | Fast cutting speed for thick sheets, slightly slower cutting speed for thin sheets |
Cutting quality | Smooth edges, small heat affected zone | The edge quality is relatively poor and may require secondary processing, resulting in a larger heat affected zone |
Equipment cost | High initial investment | The initial investment is relatively low |
Running cost | High energy efficiency and low operating costs | The operating cost is relatively high, especially considering the cost of electricity consumption and consumables |
Operational complexity | The operation is relatively complex and requires professional technical personnel | Easy to operate, with less training demand |
Flexibility | High flexibility, suitable for complex and delicate cutting tasks | Relatively low flexibility, but significant advantage in cutting thick sheets |
Maintain demand | Low maintenance requirements and long equipment lifespan | High maintenance requirements, requiring regular replacement of electrodes and nozzles |
Thermal impact | Generate fewer heat affected zones, suitable for cutting heat sensitive materials | The large heat affected zone can easily cause material deformation |
C. Fiber Laser Cutting Machine vs. Plate Shearing Machine
Comparison Project | Fiber Laser Cutting Machine | Plate Shearing Machine |
Cutting accuracy | High precision, suitable for cutting complex shapes and details | Only suitable for linear cutting, with relatively low accuracy |
Cutting materials | Capable of cutting various metal materials, including stainless steel, carbon steel, aluminum, etc | Mainly used for cutting thin sheet metal, with limited material types |
Cutting thickness | Suitable for materials ranging from thin to medium thickness (typically 0.5mm to 20mm) | Suitable for thick metal plates (usually 6mm to 50mm), also suitable for thin plates |
Cutting speed | The cutting speed for thin sheets is very fast | Fast cutting speed, especially on thick sheets, with obvious advantages |
Operational complexity | The operation is complex and requires professional technical personnel | Relatively easy to operate, suitable for mass production and simple cutting tasks |
Equipment cost | The initial investment is relatively high, and the maintenance cost is relatively low | The initial investment is relatively low, but the cost of shearing equipment for thicker materials is high |
Running cost | High energy efficiency and low operating costs, especially in large-scale production | Low operating costs, mainly consisting of electricity and regular maintenance expenses |
Flexibility | High flexibility, capable of cutting complex shapes and diverse materials | Low flexibility, can only perform linear cutting |
Maintain demand | Low maintenance requirements and long service life | Low maintenance requirements, but tools need to be replaced regularly to ensure cutting quality |
Thermal impact | A small amount of heat affected zone is generated during the cutting process, which is suitable for processing heat sensitive materials | No thermal impact, as the shearing process does not involve heat |
D. Fiber Laser Cutting Machine vs. Water Jet Cutting Machine
Comparison Project | Fiber Laser Cutting Machine | Waterjet Cutting Machine |
Cutting accuracy | High precision, suitable for cutting complex shapes and details | High precision, especially suitable for cutting materials without thermal deformation |
Cutting materials | The most suitable for cutting metal materials such as stainless steel, carbon steel, aluminum, etc | Capable of cutting almost all materials, including metal, plastic, glass, ceramics, composite materials, etc |
Cutting thickness | Best suited for thin to medium thickness materials (0.5mm to 20mm) | Capable of cutting very thick materials (up to several hundred millimeters), suitable for cutting ultra thick materials |
Cutting speed | The cutting speed for thin metal sheets is very fast | The cutting speed is relatively slow, especially on thick materials |
Cutting quality | Smooth cutting edge, small heat affected zone | High cutting quality, smooth edges and no heat affected zone |
Equipment cost | The initial equipment investment is relatively high, but the long-term operating cost is low | The initial equipment investment is high, especially the cost of high-pressure pumps and abrasive systems |
Running cost | High energy efficiency, low operating costs, especially suitable for large-scale metal processing | High operating costs, including water, electricity, abrasive consumption, and maintenance costs |
Maintain demand | Low maintenance requirements and long equipment lifespan | High maintenance requirements, requiring regular replacement of nozzles and high-pressure pump components, and high abrasive consumption |
Operational complexity | The operation is relatively complex and requires professional technical personnel | Complex operation, especially in abrasive management and water pressure regulation |
Applicable scenarios | Suitable for high-precision and large-scale metal processing | Suitable for cutting materials that require no thermal deformation, as well as cutting heavy or composite materials |
Thermal impact | Small heat affected zone, suitable for cutting heat sensitive materials | No thermal impact, very suitable for cutting heat sensitive and flammable materials |
E. Fiber Laser Cutting Machine vs. CNC Machining
Aspect | Fiber Laser Cutting Machine | CNC Machining |
Material Shape | Typically creates 2D profiles | Can create complex 3D geometries |
Efficiency | High efficiency for suitable materials | Tool changes and maintenance reduce efficiency |
Versatility | Best suited for specific material types | High versatility in material types |
Setup Time | Quick setup for repetitive jobs | Lengthier setup times for complex parts |
Material Waste | Less waste due to precision cutting | More waste due to cutting tool path |
Advantages | Much greater flexibility in design;No tool wear or replacement;Ability to quickly switch between different designs without tooling changes | Often lower initial investment;Can be faster for simple, high-volume cuts;No heat-affected zone |
Future Prospects of Fiber Laser Cutting Machines
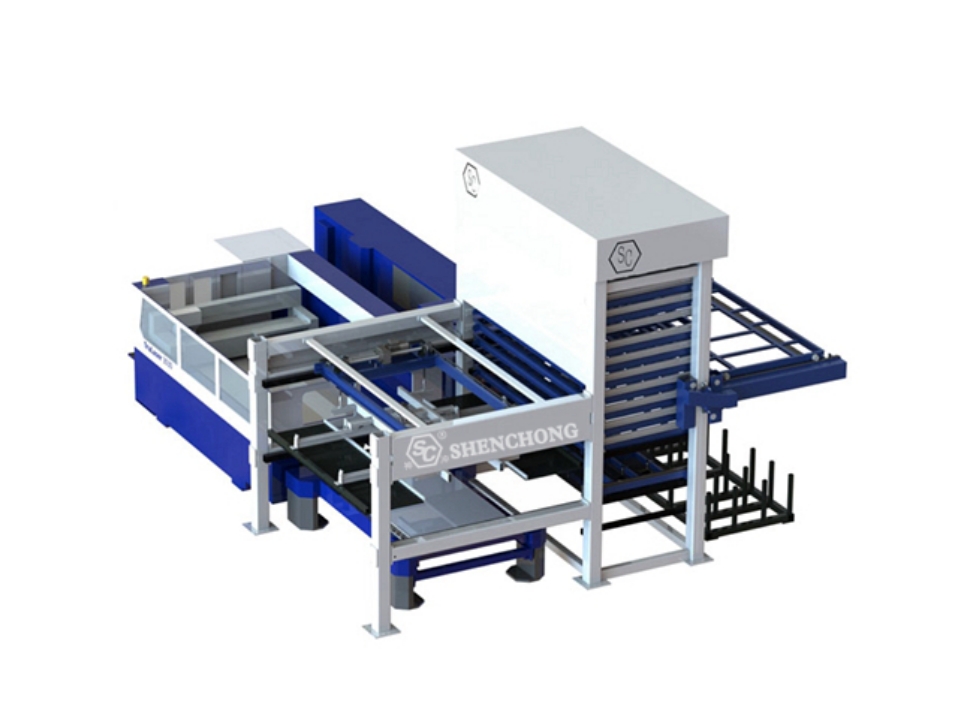
The future of fiber laser cutting machines looks promising, with continuous advancements in laser technology and automation poised to enhance their capabilities and applications. Some key trends and developments to watch for include:
Increased Power and Efficiency: Ongoing research and development efforts are focused on increasing the power and efficiency of fiber lasers, enabling them to handle thicker materials and achieve even faster cutting speeds.
Integration with Industry 4.0: The integration of fiber laser cutting machines with Industry 4.0 technologies, such as the Internet of Things (IoT), artificial intelligence (AI), and machine learning, will enable real-time monitoring, predictive maintenance, and optimized cutting processes.
Enhanced Automation and Robotics: The continued development of automation and robotics will lead to more advanced and flexible fiber laser cutting systems, capable of handling complex tasks with minimal human intervention. Laser cutting machine can connect with automatic loading unloading system or automatic sheet metal storage system to improve the sheet metal cutting automation level.
Sustainability and Environmental Impact: As industries prioritize sustainability, the focus will be on developing fiber laser cutting machines that are more energy-efficient and environmentally friendly, with reduced emissions and waste generation.
Broader Material Compatibility: Research into new laser wavelengths and beam delivery systems aims to improve the compatibility of fiber lasers with a wider range of materials, including highly reflective and challenging substrates.
FAQs
1. What are the main benefits of fiber laser cutting over traditional cutting methods?
Fiber laser cutting machine offers several key benefits over traditional cutting methods, including higher precision, faster cutting speeds, and greater flexibility in terms of the materials that can be cut. Additionally, fiber laser cutting is a non-contact process, which reduces the risk of material contamination and tool wear.
2. Can fiber laser cutting machine be used for mass production?
Yes, laser cutting machine is well-suited for mass production. Its high precision, cutting speed, and repeatability make it ideal for producing large quantities of parts with consistent quality. Especially to connect with the automatic loading unloading system, the automation capabilities of laser cutting machines also reduce the need for manual intervention, further enhancing efficiency and productivity.
3. Are there any health risks associated with laser cutting?
Yes, there are potential health risks associated with laser cutting, primarily related to the fumes and gases that can be emitted when certain materials are cut. Proper ventilation and fume extraction systems are essential to mitigate these risks. Additionally, operators must follow safety protocols to avoid direct exposure to the laser beam, which can cause burns or other injuries.
Conclusion
Fiber laser cutting machines offer numerous advantages, including high precision, speed, versatility, and low operational costs. These benefits make them indispensable tools in various industries, from automotive and aerospace to electronics and medical device manufacturing. However, they also come with certain disadvantages, such as high initial investment, material limitations, and the need for specialized training and safety measures.
Despite these challenges, the future of fiber laser cutting machines is bright, with ongoing advancements poised to enhance their capabilities and broaden their applications. As industries continue to seek efficient, sustainable, and high-quality manufacturing solutions, fiber laser cutting machines are set to play a pivotal role in shaping the future of industrial fabrication and production.
This comprehensive overview should provide a solid understanding of the fiber laser cutting machine advantages and disadvantages, along with their applications and future prospects.