In modern sheet metal manufacturing, laser technology provides unparalleled accuracy and laser cutting speed in shaping various materials. As the industry continues to embrace the versatility of laser cutting technology, optimizing speed and efficiency has become increasingly important. From raw materials to the final product, the laser cutting process involves complex interactions of factors. It is crucial to fully understand the main factors that affect laser cutting speed and efficiency, from the inherent characteristics of materials to the complex configuration of cutting machines.
In this article, we comprehensively explore the main factors that affect laser cutting speed and efficiency, explaining the complexity of material properties, laser parameters, cutting conditions, machine configuration, and design considerations. This exploration provides valuable insights for users, enabling them to fully utilize the potential of laser cutting technology and drive innovation in metal manufacturing processes.
Table of Contents
Laser Cutting Speed And Efficiency
The cutting speed of laser cutting machines is a concern for many processing enterprises, as it determines production efficiency. In other words, the faster the speed, the higher the overall output. Laser cutting is a complex manufacturing technology that relies on the subtle balance of various factors to achieve optimal speed and efficiency. Material characteristics, such as composition, thickness, and surface conditions, can affect cutting parameters. Laser parameters, including power density, beam quality, and focal length, determine the accuracy and effectiveness of cutting. The selection of cutting conditions, such as speed and auxiliary gas, plays a crucial role in improving cutting efficiency. Machine factors, such as system configuration and maintenance, make a significant contribution to overall performance. In addition, design considerations such as geometric complexity and nested optimization can also affect cutting speed and efficiency. By comprehensively understanding and optimizing these factors, manufacturers can improve the speed, accuracy, and efficiency of laser cutting processes, thereby enhancing productivity and competitiveness.
Main Factors Affect Laser Cutting Speed
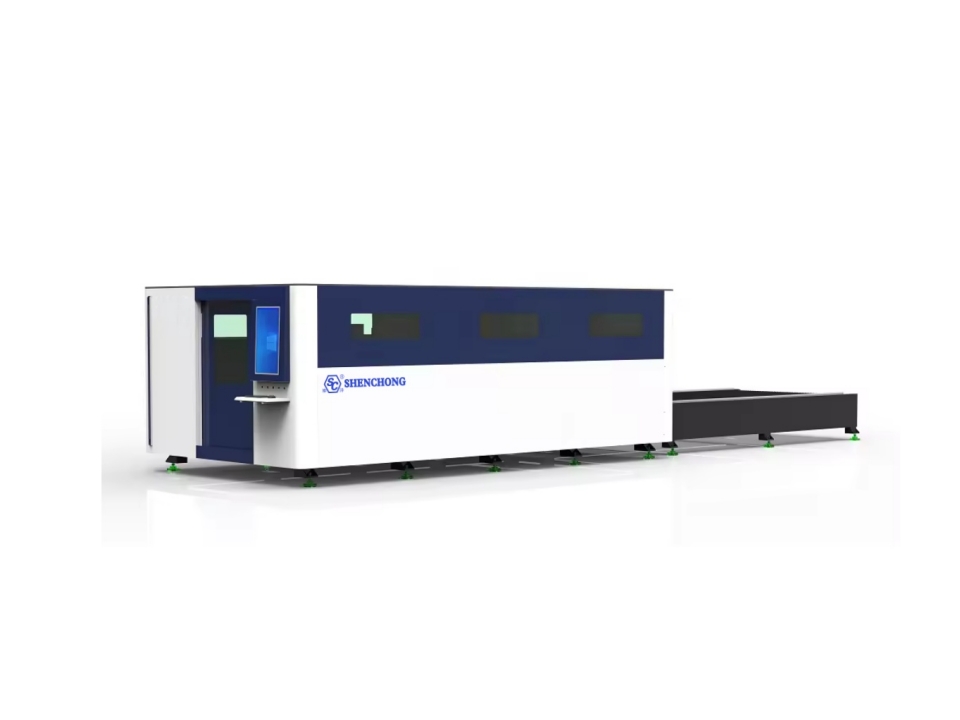
The powerful cutting process has driven the rapid development of the laser cutting industry, greatly improving the cutting quality and stability of laser cutting machines. During the processing, the laser cutting speed is influenced by factors such as process parameters, material quality, gas purity, and light speed quality. An in-depth study of the complexity of this change process reveals the comprehensive considerations that users must carefully respond to. Here, we explore the main factors that significantly affect the speed and efficiency of laser cutting.
Laser Parameters
- Power density: The laser power density is determined by the power of the laser beam focused on a given area, which directly affects cutting speed and efficiency. A higher power density allows for faster cutting speeds, but careful calibration is required to prevent material damage.
- Beam quality: The quality of the laser beam, including factors such as divergence, mode, and wavelength, will affect cutting accuracy and efficiency. High quality beam ensures even energy distribution, enabling cleaner cutting and higher efficiency.
- Focal length: The focal length of a laser lens determines the size and depth of the light spot. The optimal focus selection ensures precise energy delivery to the cutting surface, maximizing efficiency without affecting quality.
Material Properties
- Material type: The type of material being cut plays an important role in determining the speed and efficiency of laser cutting. Soft materials are relatively easy to be laser cut, and the cutting speed is also relatively fast. Hard materials require longer processing time. Metals such as stainless steel, aluminum, and carbon steel have different thermal conductivity, melting points, and reflectivity, all of which can affect their response to laser cutting. For example, cutting steel plates is much slower than cutting aluminum plates.
- Thickness: The material thickness directly affects cutting speed and efficiency. Thicker materials require more energy and time to cut compared to thinner materials. In order to achieve the best results on different thicknesses, it is necessary to adjust the laser power, focal length, and cutting speed.
- Surface condition: Surface irregularities, such as rust, oxidation, or coating, can affect the quality and speed of laser cutting. For effective cutting, it may be necessary to prepare the material surface through cleaning or surface treatment.
Laser Cutter Machine Factors
- Laser system configuration: The design and functions of the laser cutting machine, including beam transmission system, motion control, and automation functions, will affect cutting speed and efficiency. The advancement of modern laser technology has improved processing speed and accuracy.
- Maintenance and calibration: Regular maintenance, calibration, and calibration of laser cutting equipment help ensure consistent performance and extend machine life. Neglecting maintenance may lead to reduced cutting efficiency, increased downtime, and high repair costs.
Cutting Conditions
- Cutting speed: The speed at which the laser beam passes through the material surface significantly affects cutting efficiency. Finding the right balance between cutting speed and power can help achieve the desired results and minimize processing time.
- Auxiliary gas selection: Auxiliary gases such as oxygen, nitrogen, or compressed air help with material removal and cooling during laser cutting. The selection of auxiliary gases depends on the material type, thickness, and required edge quality. The higher the pressure of the auxiliary gas, the higher the purity of the gas, the less impurities adhere to the material, and the smoother the cutting edge. Generally speaking, oxygen cutting speed is fast, nitrogen cutting effect is good, and cost is low. Different gases provide different levels of cutting efficiency and cleanliness.
- Nozzle design and alignment: Correct nozzle design and alignment help guide secondary airflow and maintain optimal separation distance. Improper alignment or nozzle wear can lead to reduced cutting efficiency and quality.
Environmental Factor
- Temperature and humidity: Environmental temperature and humidity levels can affect laser cutting performance. Extreme temperature or high humidity can cause material deformation or interfere with laser beam propagation, affecting cutting speed and quality.
- Air quality: Pollutants present in the air, such as dust or particles, may interfere with laser cutting operations. Maintaining clean air in the cutting environment helps prevent nozzle blockage and ensures consistent cutting efficiency.
Design Considerations
- Geometric complexity: Complex designs with sharp corners, small features, or tight tolerances may require slower cutting speeds to maintain accuracy and edge quality. Advanced CAD software can optimize cutting paths for complex geometric shapes, thereby improving overall efficiency.
- Nested optimization: By using nested optimization software to effectively utilize materials, it can minimize material waste, reduce cutting time, and ultimately improve overall process efficiency. Nested algorithms arrange parts in the most space efficient way, maximizing material utilization.
- Edge smoothness requirements: The required edge quality, whether smooth, rough, or free of burrs, will affect cutting parameters and speed. Adjustments may be necessary to meet specific surface finish standards to ensure that the final product meets quality standards.
- In the complex process of laser cutting, manufacturers must carefully consider and balance these factors in order to fully unleash the potential of this advanced technology. A detailed understanding of material interactions, laser dynamics, cutting conditions, machine configurations, environmental impacts, and design complexity can help achieve optimal laser cutting speed and efficiency in modern manufacturing.
How To Improve The Cutting Speed Of Laser Cutting Machines
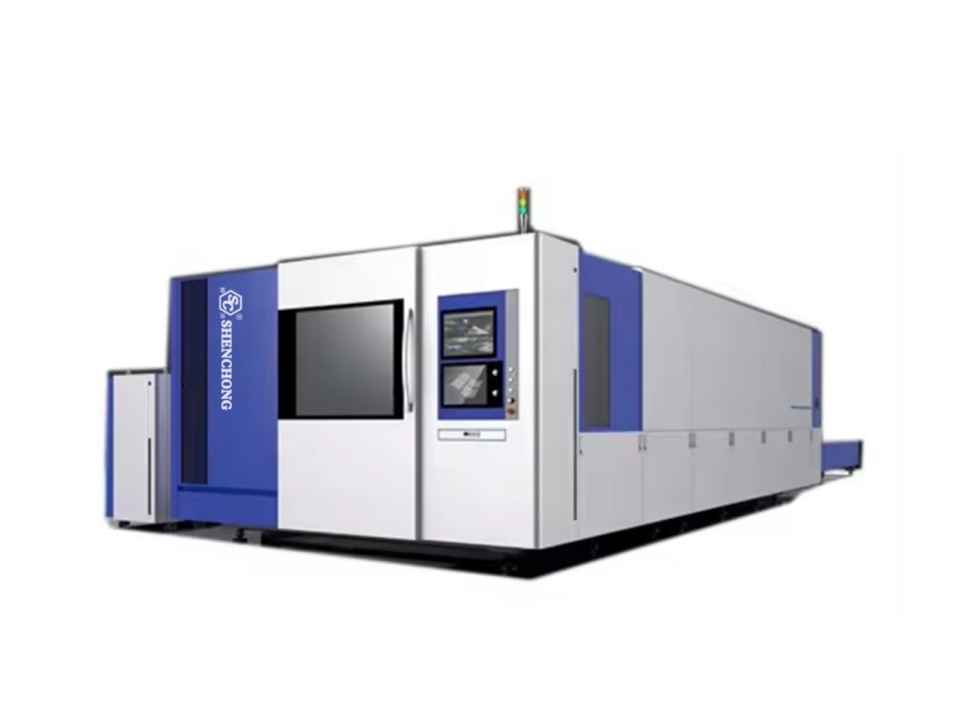
- Choose suitable materials
By selecting materials that are easier to cut, cutting efficiency can be improved.
- Adjust the laser power appropriately
The adjustment of laser power has a significant impact on the laser cutting speed. Therefore, for different materials and thicknesses, it is necessary to adjust the laser power appropriately to improve cutting speed.
- Use high-quality lasers
The quality of the laser also has a significant impact on the laser cutting speed. Using higher quality lasers can improve cutting efficiency and reduce cutting time.
- Maintenance equipment
Regular maintenance and upkeep of the laser cutting machine to keep the equipment in optimal working condition can help improve its cutting speed and efficiency.
Relationship Between Laser Power, Material Condition And Laser Cutting Speed
As we introduce the material properties and laser sources power are the factors affect the laser cutting speed. Below we will use charts to display the maximum cutting thickness and corresponding cutting speed of Raycus 1000W-15000W fiber lasers and IPG 1000W-12000W fiber lasers.
Raycus Cutting Speed - Carbon Steel
Fiber Laser Cutting Thickness And Speed Parameters (Raycus/Carbon Steel/1000w-4000w)
Material | Laser Power | 1000W | 1500W | 2000W | 3000W | 4000W |
Thickness | Speed | Speed | Speed | Speed | Speed | |
(mm) | (m/min) | (m/min) | (m/min) | (m/min) | (m/min) | |
Carbon Steel (O2/N2/Air) | 1 | 5.5/10 | 6.7/20 | 7.3/25 | 10/35 | 28-35 |
2 | 4 | 5 | 5.2/9 | 5.5/20 | 12-15 | |
3 | 3 | 3.6 | 4.2 | 4 | 4-4.5 (1.8KW)/8-12 | |
4 | 2.3 | 2.5 | 3 | 3.5 | 3-3.5 (2.4KW) | |
5 | 1.8 | 1.8 | 2.2 | 3.2 | 2.5-3 (2.4KW) | |
6 | 1.4 | 1. 5 | 1.8 | 2.7 | 2.5-2.8 (3KW) | |
8 | 1.1 | 1.2 | 1.3 | 2.2 | 2-2.3 (3.6KW) | |
10 | 0.8 | 1 | 1.1 | 1.5 | 1.8-2 (4KW) | |
12 |
| 0.8 | 0.9 | 1 | 1-1.2 (1.8-2.2KW) | |
14 |
| 0. 65 | 0.8 | 0.9 | 0.9-1 (1.8-2.2KW) | |
16 |
| 0.5 | 0.7 | 0.75 | 0.7-0.9 (2.2-2.6KW) | |
18 |
|
| 0.5 | 0.65 | 0.6-0.7 (2.2-2.6KW) | |
20 |
|
| 0.4 | 0.6 | 0.55-0.65 (2.2-2.6KW) | |
22 |
|
|
| 0.55 | 0.5-0.6 (2.2-2.8KW) | |
25 |
|
|
|
| 0.5 (2.4-3KW) |
Fiber Laser Cutting Thickness and Speed Parameters (Raycus/Carbon Steel/6000W-15000W)
Laser Power | 6000W | 8000W | 10000W | 12000W | 15000W |
Thickness | Speed | Speed | Speed | Speed | Speed |
(mm) | (m/min) | (m/min) | (m/min) | (m/min) | (m/min) |
1 | 30-45 | 35-45 | 40-45 | 50-60 | 50-60 |
2 | 20-25 | 30-35 | 35-40 | 40-45 | 45-48 |
3 | 3.5-4.2 (2.4KW)/12-14 | 20-25 | 25-30 | 30-35 | 30-38 |
4 | 3.3-3.8 (2.4KW)/7-8 | 15-18 | 18-20 | 20-26 | 26-29 |
5 | 3-3.6 (3KW)/5-6 | 10-12 | 13-15 | 15-18 | 20-23 |
6 | 2.7-3.2 (3.3KW)/4.5-5 | 8-9 | 10-12 | 10-13 | 17-19 |
8 | 2.2-2.5 (4.2KW) | 2.3-2.5 (4KW)/5-5.5 | 7-8 | 7-10 | 10-12 |
10 | 2.0-2.3 (5.5KW) | 2.3 (6KW) | 2-2.3 (6KW)/3.5-4.5 | 2-2.3 (6KW)/5-6.5 | 2-2.3 (6KW) /7-8 |
12 | 1.9-2.1(6KW) | 1.8-2(7.5KW) | 1.8-2(7.5KW) | 1.8-2(7.5KW) | 1.8-2(7.5KW)/5-6 |
14 | 1.4-1.7(6KW) | 1.6-1.8(8KW) | 1.6-1.8(8.5KW) | 1.6-1.8(8.5KW) | 1.6-1.8(8.5KW)/4.5-5.5 |
16 | 1.2-1.4(6KW) | 1.4-1.6(8KW) | 1.4-1.6(9.5KW) | 1.5-1.6(9.5KW) | 1.5-1.6(9.5KW)/3-3.5 |
18 | 0.8(6KW) | 1.2-1.4(8KW) | 1.3-1.5(9.5KW) | 1.4-1.5(10KW) | 1.4-1.5 (10KW) |
20 | 0.6-0.7(6KW) | 1-1.2(8KW) | 1.2-1.4(10KW) | 1.3-1.4(12KW) | 1.3-1.4(12KW) |
22 | 0.5-0.6(6KW) | 0.6-0.65(8KW) | 1.0-1.2(10KW) | 1-1.2(12KW) | 1.2-1.3(15KW) |
25 | 0.4-0.5(6KW) | 0.3-0.45(8KW) | 0.5-0.65(10KW) | 0.8-1(12KW) | 1.2-1.3(15KW) |
30 |
| 0.2-0.25 (8KW) | 0.3-0.35 (10KW) | 0.7-0.8 (12KW) | 0.75-0.85 (15KW) |
40 |
| 0.1-0.15 (8KW) | 0.2 (10KW) | 0.25-0.3 (12KW) | 0.3-0.35 (15KW) |
50 |
|
|
|
| 0.2-0.25(15KW) |
60 |
|
|
|
| 0.18-0.2 (15KW) |
IPG Cutting Speed - Carbon Steel
Fiber Laser Cutting Thickness And Speed Parameters (IPG//1000W-4000W)
Material | Laser Power | 1000W | 1500W | 2000W | 3000W | 4000W |
Thickness | Speed | Speed | Speed | Speed | Speed | |
(mm) | (m/min) | (m/min) | (m/min) | (m/min) | (m/min) | |
Carbon Steel (O2/N2/Air) | 1 | 45547 | 45547 | 9-11/18-22 | 9-12/25-30 | 9-11/40-50 |
2 | 4.5-5 | 4.9-5.5 | 5-6 | 5-6/12-15 | 5-6/18-22 | |
3 | 3-3.3 | 3.4-3.8 | 3.7-4.2 | 4-4.5 | 4-4.5/15-18 | |
4 | 2.1-2.4 | 2.4-2.8 | 2.8-3.5 | 3.2-3.8 | 3.2-3.8/8-10 | |
5 | 1.6-1.8 | 2.0-2.4 | 2.5-2.8 | 3.2-3.4 | 3-3.5/4-5 | |
6 | 1.3-1.5 | 1.6-1.9 | 2.0-2.5 | 3-3.2 | 2.8-3.2 | |
8 | 0.9-1.1 | 1.1-1.3 | 1.2-1.5 | 2-2.3 | 2.3-2.6 | |
10 | 0.7-0.9 | 0.9-1.0 | 1-1.2 | 1.5-1.7 | 2-2.2 | |
12 |
| 0.7-0.8 | 0.9-1.1 | 0.8-1 | 1-1.5 | |
14 |
| 0.6-0.7 | 0.7-0.9 | 0.8-0.9 | 0.85-1.1 | |
16 |
|
| 0.6-0.75 | 0.7-0.85 | 0.8-1 | |
20 |
|
|
| 0.65-0.8 | 0.6-0.9 | |
22 |
|
|
|
| 0.6-0.7 |
Fiber Laser Cutting Thickness And Speed Parameters (IPG/Carbon Steel/6000W-12000W)
Material | Laser Power | 6000W | 8000W | 10000W | 12000W |
Thickness | Speed | Speed | Speed | Speed | |
(mm) | (m/min) | (m/min) | (m/min) | (m/min) | |
Carbon Steel (O2/N2/Air) | 1 | 10-12/45-60 | 10-12/50-60 | 10-12/50-80 |
|
2 | 5-6/26-30 | 5.5-6.8/30-35 | 5.5-6.8/38-43 |
| |
3 | 4-4.5/18-20 | 4.2-5.0/20-25 | 4.2-5.0/28-30 |
| |
4 | 3.2-3.8/13-15 | 3.7-4.5/15-18 | 3.7-4.5/18-21 |
| |
5 | 3-3.5/7-10 | 3.2-3.8/10-12 | 3.2-3.8/13-15 |
| |
6 | 2.8-3.2 | 2.8-3.6/8.2-9.2 | 2.8-3.6/10.8-12 |
| |
8 | 2.5-2.8 | 2.6-3.0/5.0-5.8 | 2.6-3.0/7.0-7.8 |
| |
10 | 2.0-2.5 | 2.1-2.6/3.0-3.5 | 2.1-2.6/3.8-4.6 | 2.2-2.6 | |
12 | 1.8-2.2 | 1.9-2.3 | 1.9-2.3 | 2-2.2 | |
14 | 1-1.8 | 1.1-1.8 | 1.1-1.8 | 1.8-2.2 | |
16 | 0.85-1.5 | 0.85-1.2 | 0.85-1.2 | 1.5-2 | |
20 | 0.75-1.0 | 0.75-1.1 | 0.75-1.1 | 1.2-1.7 | |
22 | 0.7-0.8 | 0.7-0.85 | 0.7-0.85 | 0.7-0.85 | |
25 | 0.6-0.7 | 0.6-0.8 | 0.6-0.8 | 0.6-0.8 | |
30 |
|
|
| 0.4-0.5 | |
35 |
|
|
| 0.35-0.45 | |
40 |
|
|
| 0.3-0.4 |
As shown in the chart, we can see the thickness and speed parameters of 1000W, 1500W, 2000W, 3000W, 4000W, 6000W, 8000W, 10000W, 12000W and 15000W fiber laser cutting.
Taking carbon steel as an example, a 1000W Raycus fiber laser cutting machine is used to cut carbon steel with a thickness of 3mm. The maximum cutting speed is 3m per minute.
1500W fiber laser cutting machine is used to cut 3mm thick carbon steel with a maximum cutting speed of 3.6m per minute.
Using the IPG chart above, we can compare the parameters of different laser-cutting machines when cutting the same kind of material. For example:
A 1000W laser cutting machine can cut 3mm-thick carbon steel at a maximum speed of 3.3m/min.
A 1500W laser cutting machine can cut 3mm-thick carbon steel at a maximum speed of 3.9m/min.
Raycus Cutting Speed - Stainless Steel
Fiber Laser Cutting Thickness And Speed Parameters (Raycus/Stainless Steel/1000W-4000W)
Material | Laser Power | 1000W | 1500W | 2000W | 3000W | 4000W |
Thickness | Speed | Speed | Speed | Speed | Speed | |
(mm) | (m/min) | (m/min) | (m/min) | (m/min) | (m/min) | |
stainless steel(N2) | 1 | 13 | 20 | 28 | 28-35 | 30-40 |
2 | 6 | 7 | 10 | 18-24 | 15-20 | |
3 | 3 | 4.5 | 5 | 7-10 | 10-12 | |
4 | 1 | 3 | 3 | 5-6.5 | 6-7 | |
5 | 0.6 | 1.5 | 2 | 3-3.6 | 4-4.5 | |
6 |
| 0.8 | 1.5 | 2-2.7 | 3-3.5 | |
8 |
|
| 0.6 | 1-1.2 | 1.5-1.8 | |
10 |
|
|
| 0.5-0.6 | 1-1.2 | |
12 |
|
|
|
| 0.8 |
Fiber Laser Cutting Thickness And Speed Parameters (Raycus/Stainless Steel/6000W-15000W)
Material | Laser Power | 6000W | 8000W | 10000W | 12000W | 15000W |
Thickness | Speed | Speed | Speed | Speed | Speed | |
(mm) | (m/min) | (m/min) | (m/min) | (m/min) | (m/min) | |
Stainless Steel(N2) | 1 | 30-45 | 40-50 | 45-50 | 50-60 | 50-60 |
2 | 25-30 | 30-35 | 35-40 | 40-45 | 45-50 | |
3 | 15-18 | 20-24 | 25-30 | 30-35 | 35-38 | |
4 | 10-12 | 12-15 | 18-20 | 23-27 | 25-29 | |
5 | 7-8 | 9-10 | 12-15 | 15-18 | 18-22 | |
6 | 4.5-5 | 7-8 | 8-9 | 13-15 | 15-18 | |
8 | 3.5-3.8 | 4-5 | 5-6 | 8-10 | 10-12 | |
10 | 1.5-2 | 3-3.5 | 3.5-4 | 6.5-7.5 | 8-9 | |
12 | 1-1.2 | 2-2.5 | 2.5-3 | 5-5.5 | 6-7 | |
16 | 0.5-0.6 | 1-1.5 | 1.6-2 | 2-2.3 | 2.9-3.1 | |
20 | 0.2-0.35 | 0.6-0.8 | 1-1.2 | 1.2-1.4 | 1.9-2.1 | |
22 |
| 0.4-0.6 | 0.7-0.9 | 0.9-1.2 | 1.5-1.7 | |
25 |
| 0.3-0.4 | 0.5-0.6 | 0.7-0.9 | 1.2-1.4 | |
30 |
| 0.15-0.2 | 0.25 | 0.25-0.3 | 0.8-1 | |
35 |
|
| 0.15 | 0.2-0.25 | 0.6-0.8 | |
40 |
|
|
| 0.15-0.2 | 0.4-0.5 | |
45 |
|
|
|
| 0.2-0.4 |
IPG Cutting Speed - Stainless Steel
Fiber Laser Cutting Thickness And Speed Parameters (IPG/Stainless Steel/1000W-4000W)
Material | Laser Power | 1000W | 1500W | 2000W | 3000W | 4000W |
Thickness | Speed | Speed | Speed | Speed | Speed | |
(mm) | (m/min) | (m/min) | (m/min) | (m/min) | (m/min) | |
Stainless Steel (N2) | 1 | 12-15 | 16-20 | 20-28 | 30-40 | 40-55 |
2 | 4.5-5.5 | 5.5-7.0 | 7-11 | 15-18 | 20-25 | |
3 | 1.5-2 | 2.0-2.8 | 4.5-6.5 | 8-10 | 12-15 | |
4 | 1-1.3 | 1.5-1.9 | 2.8-3.2 | 5.4-6 | 7-9 | |
5 | 0.6-0.8 | 0.8-1.2 | 1.5-2 | 2.8-3.5 | 4-5.5 | |
6 |
| 0.6-0.8 | 1-1.3 | 1.8-2.6 | 2.5-4 | |
8 |
|
| 0.6-0.8 | 1.0-1.3 | 1.8-2.5 | |
10 |
|
|
| 0.6-0.8 | 1.0-1.6 | |
12 |
|
|
| 0.5-0.7 | 0.8-1.2 | |
16 |
|
|
|
| 0.25-0.35 |
Fiber Laser Cutting Thickness And Speed Parameters (IPG/Stainless Steel/6000W-12000W)
Material | Laser Power | 6000W | 8000W | 10000W | 12000W |
Thickness | Speed | Speed | Speed | Speed | |
(mm) | (m/min) | (m/min) | (m/min) | (m/min) | |
Stainless Steel (N2) | 1 | 60-80 | 60-80 | 60-80 | 70-80 |
2 | 30-35 | 36-40 | 39-42 | 42-50 | |
3 | 19-21 | 21-24 | 25-30 | 33-40 | |
4 | 12-15 | 15-17 | 20-22 | 25-28 | |
5 | 8.5-10 | 10-12.5 | 14-16 | 17-20 | |
6 | 5.0-5.8 | 7.5-8.5 | 11-13 | 13-16 | |
8 | 2.8-3.5 | 4.8-5.8 | 7.8-8.8 | 8-10 | |
10 | 1.8-2.5 | 3.2-3.8 | 5.6-7 | 6-8 | |
12 | 1.2-1.5 | 2.2-2.9 | 3.5-3.9 | 4.5-5.4 | |
16 | 1.0-1.2 | 1.5-2.0 | 1.8-2.6 | 2.2-2.5 | |
20 | 0.6-0.8 | 0.95-1.1 | 1.5-1.9 | 1.4-6 | |
22 | 0.3-0.4 | 0.7-0.85 | 1.1-1.4 | 0.9-4 | |
25 | 0.15-0.2 | 0.4-0.5 | 0.45-0.65 | 0.7-1 | |
30 |
| 0.3-0.4 | 0.4-0.5 | 0.3-0.5 | |
35 |
|
|
| 0.25-0.35 | |
40 |
|
|
| 0.2-0.25 |
Now, let’s take a closer look at the parameters of for cutting stainless steel.
With a 1000W fiber laser cutting machine, you can cut 3mm thick stainless steel at a maximum speed of 3m per minute.
If you use a 1500W fiber laser cutting machine, you can cut 3mm thick stainless steel at a maximum speed of 4.5m per minute.
For 5mm thick stainless steel, a 1000W fiber laser cutting machine can achieve a maximum cutting speed of 0.6m per minute, while a 1500W laser cutting machine can achieve a maximum cutting speed of 1.5m per minute.
By comparing these parameters, it is clear that higher power allows for faster cutting speeds when working with the same type and thickness of materials.
The Influence Of Cutting Speed Of Laser Cutting Machine On Cutting Quality
- When the cutting speed is too fast, the gas coaxial with the beam cannot completely blow away the cutting residue, and the molten materials on both sides gather and solidify at the bottom edge, forming difficult to clean hanging slag. Cutting too fast can also cause the material to not be completely cut through, and there will be a certain thickness of adhesion at the bottom, which is usually very small and requires manual hammering to fall off.
- When the cutting speed is appropriate, the quality of the incision can be improved, the cutting seam is small and flat, the cutting surface is smooth without burrs, the overall workpiece is not deformed, and the workpiece can be put into use without treatment.
- When the cutting speed is too slow, the high-energy laser beam stays in various places for too long, and the thermal effect is obvious, which can lead to obvious over melting phenomenon on the opposite side of the cutting. There will be obvious over melting phenomenon at the top of the cutting, and obvious slag hanging at the bottom, resulting in very poor cutting quality.
Conclusion
Laser cutting speed affect the laser cutting efficiency and cutting quality and so manufacturers should understand the factors that influence the laser cutting speed. By learning more about laser cutting speed, operators can improve the speed, accuracy, and efficiency of laser cutting processes, thereby enhancing productivity and competitiveness.