Tabla de contenido
Durante el proceso de producción y fabricación, pueden surgir diversos problemas de calidad de doblado al doblar piezas de chapa metálica, lo que puede afectar la mejora de la eficiencia de producción y la estabilidad de la calidad del producto. Este artículo profundiza en los problemas de calidad de doblado y corte comunes en la práctica de producción, analiza las causas de los problemas y propone soluciones para proporcionar experiencia y referencia para problemas similares en la práctica de producción posterior.
Introducción
El doblado de chapa metálica es el proceso de utilizar un molde universal (o un molde especializado) equipado con un Máquina plegadora CNC Doblar láminas de metal en diversas formas geométricas transversales requeridas de piezas de trabajo. La racionalidad del proceso de doblado afecta directamente el tamaño de formación final y la apariencia del producto. La selección razonable de moldes de doblado es crucial para el conformado final de los productos.
En el proceso de producción real, debido a la incertidumbre del tamaño del producto y la diversidad de tipos de productos, a menudo nos encontramos con problemas como interferencias de tamaño y ángulos de molde no coincidentes durante el doblado de piezas de trabajo procesadas en frío, lo que trae grandes dificultades a la producción. Debido a la influencia de factores como el tamaño del producto, la forma, el material, el molde, el equipo y las instalaciones auxiliares durante el proceso de doblado, pueden ocurrir varios problemas de calidad, que afectan la eficiencia de la producción y la estabilidad de la calidad del producto. Por lo tanto, es particularmente importante abordar y evitar la aparición de estos problemas de calidad de doblado. Este artículo resume y describe principalmente los problemas de calidad comunes del doblado de chapa metálica en la práctica de producción, analiza las razones basadas en la experiencia de producción y propone soluciones.
Problemas comunes de calidad en el plegado
Doblado y agrietamiento
El agrietamiento por flexión se refiere al fenómeno en el que aparecen rebabas o pequeñas grietas en los bordes de los materiales después de cortarlos, cizallarlos o estamparlos, y la concentración de tensiones se forma fácilmente durante el doblado, lo que da lugar al agrietamiento. La ranura de refuerzo en forma de U de las piezas de locomotoras se agrieta en las esquinas después del doblado, como se muestra en la Figura 1.
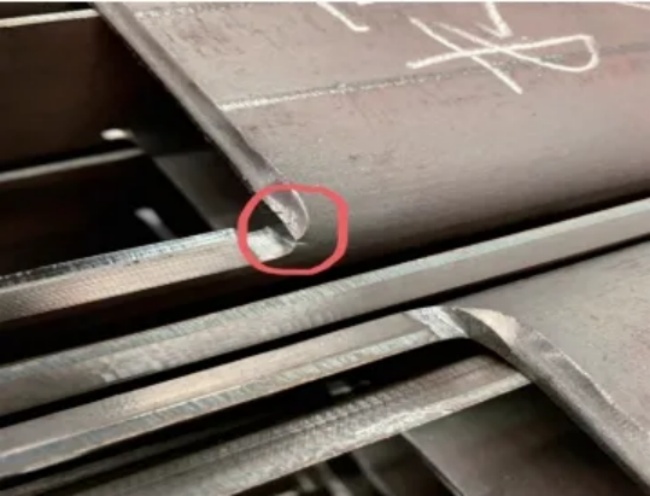
Figura 1. Flexión y agrietamiento.
Las principales causas de flexión y agrietamiento son:
- Rebabas sucias en los bordes de las piezas.
- La dirección de plegado es paralela a la dirección de laminado de la chapa.
- El radio de curvatura de la chapa es demasiado pequeño.
Durante el proceso de producción y fabricación, es necesario abordar los fenómenos de flexión y agrietamiento según las circunstancias específicas. Para el problema de flexión y agrietamiento de la Figura 1, se puede adoptar el método de agregar orificios o ranuras de proceso para resolverlo, como se muestra en la Figura 2.
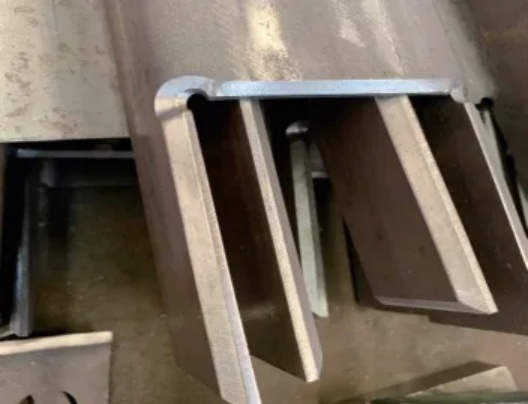
Figura 2: Adición de orificios de proceso
Interferencia de flexión
La interferencia de flexión está dirigida principalmente a productos con flexión secundaria o superior, donde el borde de flexión choca con el molde o el equipo, lo que da como resultado la incapacidad de formarse correctamente. La interferencia de flexión está influenciada principalmente por la forma, el tamaño y el molde de las piezas, y es causada principalmente por la estructura de diseño de la propia pieza doblada, la secuencia de doblado seleccionada y el molde de doblado seleccionado. Por lo tanto, las principales soluciones incluyen:
- Fabricación de moldes nuevos o reemplazo de moldes (como moldes para doblar cuchillos).
- Transformación de moldes de doblado (como procesamiento mecánico de piezas locales).
- Ajuste la secuencia de flexión (como el método de deformación inversa).
- Modificar el tamaño de curvatura de las piezas. Por ejemplo, el soporte de instalación de la canaleta de accesorios del chasis de la línea 18 del metro de Shanghái está fabricado con acero de canal en forma de U, con un ancho medio de 100 mm, una altura de borde de 80 mm y un radio de curvatura de 15 mm. Simular la curvatura basándose en los moldes existentes en el taller para generar interferencias de curvatura.
En respuesta a este fenómeno de interferencia, se adoptó un método de procesamiento mecánico local para la matriz superior de doblado (ver Figura 3). Se cortó una muesca de 140 mm × 48 mm a lo largo de la línea media de la matriz superior de cuchilla recta existente de R15 mm (L = 800 mm) (ver Figura 4). La posición de la muesca se determinó combinándola con la posición de interferencia de doblado simulada, sin afectar su función original. Después de modificar el molde de doblado, se resolvió con éxito el problema de la interferencia de doblado.
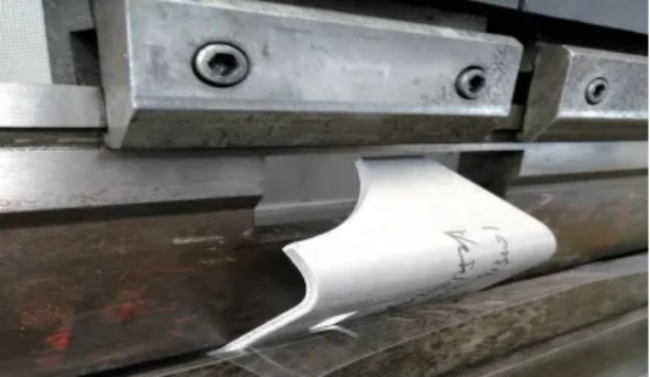
Figura 3: Doblado después del procesamiento del molde superior
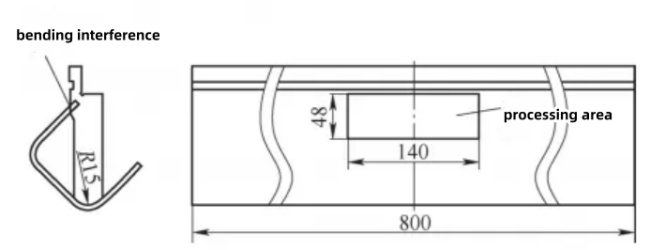
Figura 4: Interferencia de flexión, determinación del área de procesamiento
Sangría de flexión
La indentación por flexión es un fenómeno en el que se genera fricción durante el proceso de poner gradualmente la chapa metálica en contacto con la superficie interior de la ranura en forma de V del molde cóncavo, lo que da como resultado marcas evidentes en la superficie de la chapa metálica. Para algunos accesorios con altos requisitos de superficie, el plegado tradicional no puede cumplir con los requisitos de calidad del producto, y la indentación por flexión (consulte la Figura 5) no puede cumplir con los requisitos del siguiente proceso.
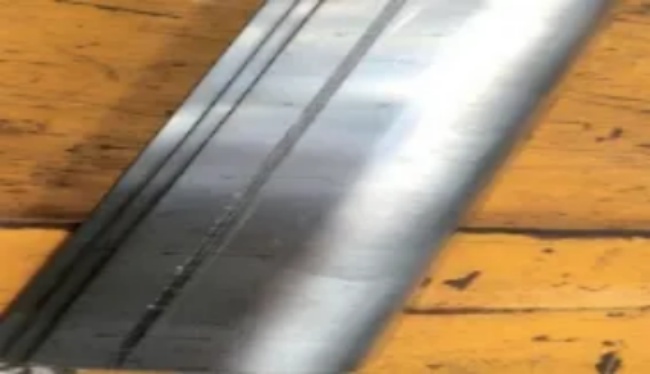
Figura 5: Sangría de flexión
La indentación por flexión se ve afectada principalmente por la dureza de la chapa y la estructura del molde inferior. Cuanto mayor sea la dureza de la chapa, mayor será su capacidad para resistir la deformación plástica, lo que dificulta que el material sufra una deformación plástica y facilita la producción de indentación. La probabilidad de indentación por flexión en los materiales de chapa de uso común es: aluminio > acero al carbono > acero inoxidable. Cuanto mayor sea el ancho de la abertura de la matriz de doblado, mayor será el ancho de la indentación por flexión y menor será la profundidad de la indentación. Cuanto mayor sea el tamaño R del hombro de la abertura del molde inferior, menor será la profundidad de la indentación.
Además de mejorar la dureza del material y la estructura del molde inferior, las almohadillas de goma anti-indentación y los moldes inferiores de flexión de tipo bola también se pueden utilizar para resolver el problema de la indentación por flexión. La almohadilla de goma anti-indentación se basa principalmente en el aislamiento físico para reducir la aparición de indentación, como se muestra en la Figura 6. La matriz de flexión de tipo bola transforma la fricción de extrusión requerida para los moldes de flexión tradicionales en fricción de rodadura, lo que reduce la fricción y minimiza el daño al producto, como se muestra en la Figura 7.
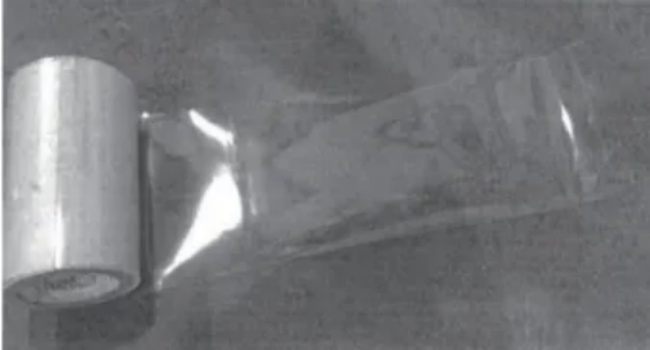
Figura 6: Almohadilla de goma anti-hendiduras
Figura 7: Molde inferior de flexión de bolas
Recuperación elástica por flexión
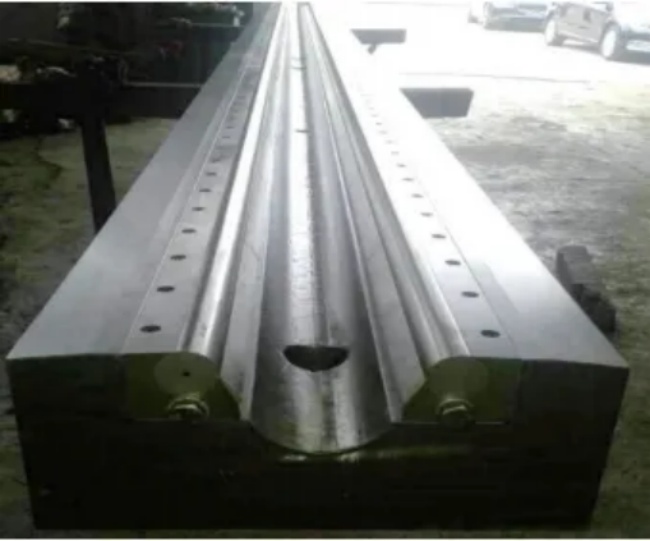
Durante el proceso de doblado, los materiales sufren simultáneamente deformación plástica y deformación elástica. Cuando la pieza de trabajo sale del molde de doblado, se produce una recuperación elástica, lo que hace que la forma y el tamaño de la pieza doblada sean inconsistentes con la carga, lo que se denomina rebote de doblado. Recuperación elástica por flexión es una de las principales razones de un ángulo de flexión insuficiente. Los principales factores que afectan al rebote son las propiedades mecánicas de la chapa metálica y las condiciones de deformación por flexión. La magnitud del valor de recuperación elástica es directamente proporcional a la resistencia a la fluencia de la chapa metálica e inversamente proporcional al módulo elástico. Cuanto menor sea el radio de curvatura relativo (relación R/t del radio de curvatura al espesor de la chapa) de la pieza doblada, menor será el valor de recuperación elástica por flexión. La forma de la pieza doblada también afecta a la magnitud del valor de recuperación elástica por flexión. Generalmente, las piezas en forma de U tienen un valor de recuperación elástica menor que las piezas en forma de V.
El método principal para superar la recuperación elástica por flexión es el método de compensación de ángulo, que generalmente adopta el método de hacer una pendiente igual al ángulo de recuperación elástica en el molde de doblado, lo que puede equilibrar eficazmente el impacto de la recuperación elástica por flexión. Como se muestra en la Figura 8, el uso de un molde de doblado con una pendiente de 80° puede doblar suavemente piezas de trabajo con un ángulo de doblado de 90°.
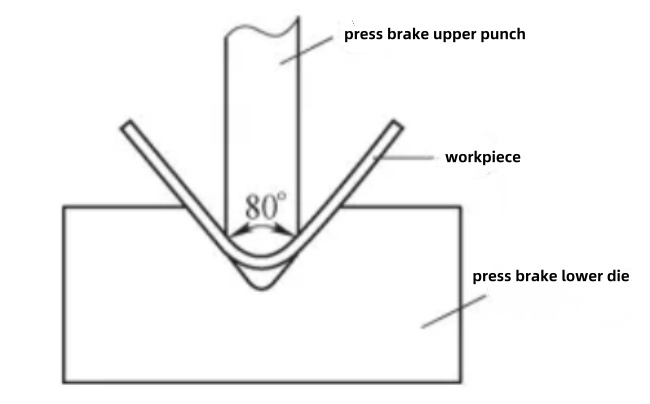
Figura 8: Compensación de la recuperación elástica por flexión
Debido a los muchos factores que afectan la recuperación elástica por flexión, es muy difícil calcular con precisión el valor de recuperación elástica. Mediante la corrección del molde de prueba y la acumulación de experiencia, el dominio de la ley de recuperación elástica, la adopción de la compensación adecuada y la adopción de medidas para superar la recuperación elástica en la estructura del molde y otros aspectos son métodos eficaces para garantizar la calidad del producto.
Material de deslizamiento de flexión
El deslizamiento de doblado se refiere al fenómeno en el cual la pieza de trabajo que se va a doblar no tiene un punto de apoyo completo y efectivo en la ranura de la matriz inferior, lo que da como resultado que la pieza de trabajo sea propensa a deslizarse y que el doblado no pueda posicionarse correctamente.
Las principales razones por las que se doblan los materiales deslizantes son las siguientes.
- Cuando el ancho del molde inferior es demasiado grande y el tamaño de curvatura es menor que la mitad del ancho del molde inferior, se produce un deslizamiento.
- Cuando la pieza de trabajo se ve afectada por su forma y tamaño, y el tamaño de posicionamiento de la plantilla es demasiado corto o no hay un borde de posicionamiento de plantilla efectivo, pueden ocurrir fenómenos de flexión y deslizamiento.
Hay dos métodos principales para resolver el problema de los materiales que se doblan y se deslizan.
- Método 1. Elija una matriz de doblado adecuada, generalmente eligiendo un ancho de matriz de 4 a 6 veces el espesor de la placa a doblar.
- Método 2. Mediante el método de agregar plantillas o bordes de proceso, se puede resolver el problema del deslizamiento del material causado por un posicionamiento deficiente debido al plegado. En general, el plegado se posiciona mediante un borde recto de la pieza de trabajo, lo que requiere que dos caras de los extremos estén en contacto con la plantilla de plegado para el posicionamiento. Sin embargo, en el proceso de producción real, existen situaciones en las que el borde de la plantilla del producto es demasiado corto o no hay un borde de posicionamiento efectivo, lo que da como resultado la incapacidad de completar el posicionamiento del plegado. Las soluciones son:
- Cuando el espesor de la placa t ≤ 6 mm, se debe agregar un borde de proceso para el posicionamiento, y la posición del borde de proceso que se extiende debe estar al mismo nivel que el borde final del accesorio. Se debe utilizar corte por láser en la unión para facilitar el pulido y la eliminación después de que se complete la operación de doblado.
- Cuando el espesor de la placa t es mayor a 6 mm, se puede cortar una plantilla para posicionarla, y el espesor de la plantilla puede ser igual o ligeramente menor que el espesor de la pieza de trabajo. Ambos métodos de posicionamiento pueden resolver el problema de doblar y deslizar materiales.
Doblado de arco grande
Durante el proceso de producción y fabricación, es común encontrar situaciones en las que el radio de curvatura de la pieza de trabajo es grande y no hay un molde de arco grande correspondiente en el taller. En este caso, el ciclo de producción de moldes de conformado integral o moldes de arco grande es más largo y el costo es demasiado alto, mientras que el uso de la tecnología de conformado de plegado de múltiples pasadas de arco pequeño tiene un costo menor y una aplicabilidad más amplia. Por ejemplo, en el proyecto Super Bus 2.0, hay un componente con una placa vertical y tres placas verticales, con un radio de curvatura de 125 mm y un ángulo de curvatura de 90 °, como se muestra en la Figura 9. Debido a la falta de moldes de doblado correspondientes en el taller, se pueden utilizar múltiples procesos de doblado. En primer lugar, se utilizó un software 3D para modelar el diseño y el doblado en la posición R125 mm. Después del modelado, el software desplegó automáticamente el diagrama de placa plana 2D. Al ingresar un radio de curvatura de 45 mm en el software y comparar múltiples datos ingresados, se confirmó que el segmento de arco circular se podía garantizar doblando con 8 cortes. Luego, se generaron los datos de curvatura (ángulo de curvatura, longitud de la posición de la línea de curvatura) para cada corte, como se muestra en la Figura 10. Finalmente, se realizó una prueba de curvatura en el sitio en función de los datos de curvatura, como se muestra en la Figura 11.
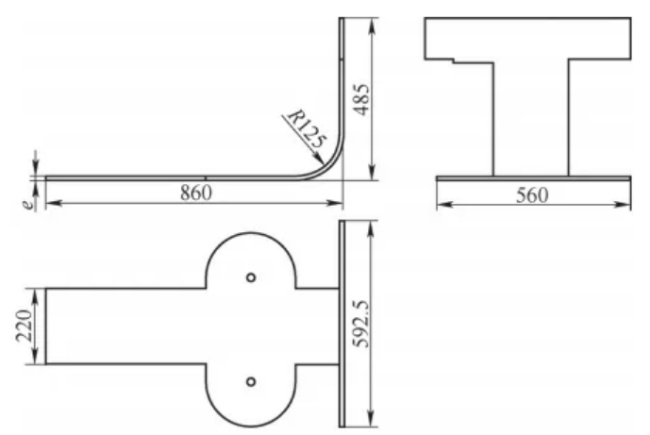
Figura 9: Piezas de trabajo en forma de arco
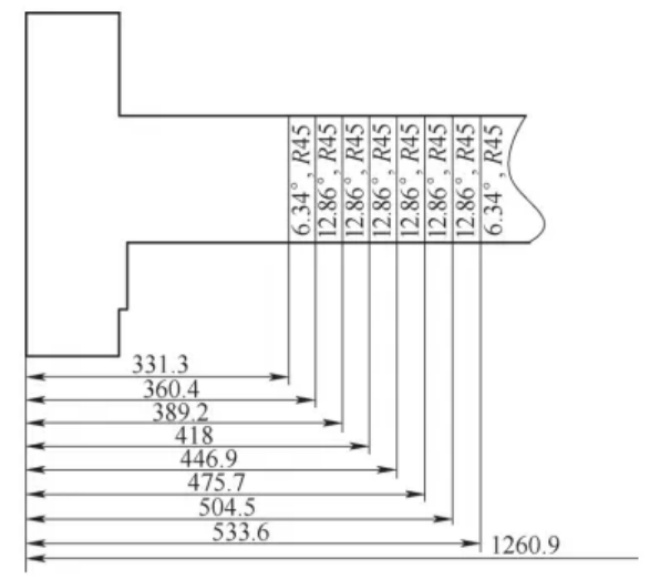
Figura 10: Diagrama de despliegue y posición de la línea de plegado

Figura 11: Prueba de doblado del molde en el sitio
Protrusión de flexión
La protuberancia por flexión se refiere al fenómeno en el que el material metálico sobresale en ambos lados de la esquina doblada de la chapa metálica debido a la compresión del material, lo que da como resultado un ancho mayor que el tamaño original. El tamaño de la protuberancia por flexión generalmente está relacionado con el grosor de la placa auxiliar y el radio de curvatura. Cuanto más gruesa sea la placa, menor será el radio de curvatura y más obvia será la protuberancia.
Para evitar este problema de calidad de doblado, se pueden agregar muescas de proceso en ambos lados de la línea de doblado durante el dibujo del diagrama de desplegado de doblado, como se muestra en la Figura 12. El espacio de proceso generalmente tiene la forma de un arco circular, con un diámetro de al menos 1,5 veces el espesor de la pieza de trabajo, para compensar la protuberancia de doblado y resolver eficazmente el problema de la protuberancia de doblado. Para piezas de trabajo que ya han producido protuberancias de doblado, generalmente se utiliza el pulido manual para el procesamiento.
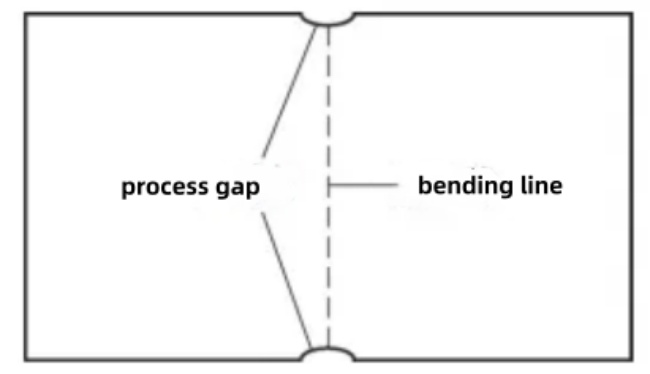
Figura 12: Brecha de proceso
Conclusión
Cabe señalar que los problemas comunes de calidad de doblado y corte enumerados anteriormente en la práctica de producción no han tenido en cuenta el impacto de los factores humanos o del equipo (como dimensiones de desplegado incorrectas, selección incorrecta de parámetros de doblado y envejecimiento del equipo). En la práctica de producción, los parámetros de proceso de doblado adecuados deben seleccionarse en función del rendimiento del equipo, el tamaño del producto y las características del material, y ejecutarse estrictamente de acuerdo con las especificaciones operativas. No solo necesitamos considerar exhaustivamente el impacto de varios factores como el progreso del proyecto, el costo y la calidad, y adoptar métodos apropiados para resolver los problemas de calidad de doblado, sino que también necesitamos acumular experiencia para predecir la aparición y el impacto de los problemas de doblado en la etapa de análisis del proceso, y tomar medidas específicas para prevenirlos. Este artículo enumera varios problemas comunes de calidad de doblado y sus soluciones, con la esperanza de proporcionar alguna referencia y orientación para los colegas de la industria.