Inhaltsverzeichnis
Einführung
Das automatische Be- und Entladesystem für Metall ist eine revolutionäre Ausrüstung zum automatischen Transport von Blechplatten von einer Maschine zur anderen. Die beliebteste Anwendung des automatischen Be- und Entladesystems ist die Laserschneidmaschine.
Laserschneidmaschinen haben die Fertigungsindustrie revolutioniert, indem sie Präzision, Geschwindigkeit und Vielseitigkeit beim Schneiden verschiedener Materialien bieten. Um die Fähigkeiten dieser Maschinen jedoch voll auszuschöpfen, sind effiziente Materialhandhabungssysteme von entscheidender Bedeutung. Lade- und Entladesysteme für Laserschneidmaschinen spielen eine entscheidende Rolle bei der Steigerung der Produktivität, der Reduzierung von Ausfallzeiten und der Gewährleistung der Sicherheit. Dieser Artikel befasst sich mit den verschiedenen Arten von Lade- und Entladesystemen, ihren Vorteilen, Anwendungen und zukünftigen Trends und bietet einen umfassenden Überblick über diese wesentlichen Komponenten bei Laserschneidvorgängen.
Die Bedeutung des automatischen Be- und Entladesystems für Metall
Be- und Entladesysteme sind für die Automatisierung der Versorgung der Laserschneidmaschine mit Rohmaterial und der Entnahme fertiger Teile konzipiert. Diese Systeme sind aus mehreren Gründen unverzichtbar:
- Höhere Produktivität: Automatisierte Systeme können den Zeitaufwand zum Be- und Entladen von Materialien erheblich reduzieren, sodass die Laserschneidmaschine kontinuierlich und effizient arbeiten kann.
- Reduzierte Arbeitskosten: Durch die Automatisierung dieser Prozesse können Hersteller den Bedarf an manueller Arbeit minimieren und so die Arbeitskosten und das Potenzial menschlicher Fehler reduzieren.
- Verbesserte Sicherheit: Automatisierte Systeme verbessern die Sicherheit am Arbeitsplatz, indem sie den Bedarf an menschlichen Eingriffen bei potenziell gefährlichen Vorgängen minimieren.
- Konsistenz und Qualität: Durch die Automatisierung wird eine konsistente Materialhandhabung gewährleistet, was zur Einhaltung hoher Qualitätsstandards im Schneidprozess beiträgt.
Anwendungen von Be- und Entladesystemen
1. Automobilindustrie
In der Automobilindustrie werden Be- und Entladesysteme zum Handling großer Bleche und komplexer Teile eingesetzt. Automatisierte Systeme gewährleisten gleichbleibende Qualität und hohe Produktivität und erfüllen damit die Anforderungen der Massenproduktion.
2. Luft- und Raumfahrtindustrie
In der Luft- und Raumfahrtindustrie sind Präzision und Konsistenz bei der Herstellung von Komponenten erforderlich. Automatisierte Be- und Entladesysteme tragen zur Erfüllung dieser Anforderungen bei, indem sie eine genaue Materialhandhabung gewährleisten und das Risiko von Defekten verringern.
3. Metallverarbeitung
Bei der Metallverarbeitung werden Metallteile geschnitten, geformt und zusammengebaut. Be- und Entladesysteme optimieren diese Prozesse, indem sie die Handhabung von Rohmaterialien und Fertigteilen automatisieren und so die Effizienz und Produktivität steigern.
4. Elektronikindustrie
In der Elektronikindustrie ist Präzision das A und O. Automatisierte Systeme gewährleisten die genaue Handhabung empfindlicher Materialien und Komponenten, minimieren das Risiko von Beschädigungen und gewährleisten eine qualitativ hochwertige Produktion.
5. Möbelherstellung
Die Möbelherstellungsindustrie profitiert von automatisierten Systemen zur Handhabung großer Platten aus Holz, Metall oder Verbundwerkstoffen. Diese Systeme steigern die Produktivität und gewährleisten eine gleichbleibende Qualität bei der Herstellung von Möbelkomponenten.
6. Herstellung medizinischer Geräte
Bei der Herstellung medizinischer Geräte gewährleisten automatisierte Be- und Entladesysteme eine präzise Handhabung von Materialien und Komponenten und erfüllen strenge Qualitäts- und Sicherheitsstandards.
Arten von Be- und Entladesystemen
1. Manuelles Be- und Entladen
Bei manuellen Systemen sind menschliche Bediener erforderlich, um Rohmaterial in die Laserschneidmaschine zu laden und fertige Teile zu entnehmen. Diese Systeme sind zwar einfach und kostengünstig, weisen jedoch mehrere Einschränkungen auf:
- Erhöhte Arbeitskosten: Manuelle Systeme erfordern einen erheblichen Arbeitsaufwand, der insbesondere in Produktionsumgebungen mit hohem Volumen kostspielig sein kann.
- Inkonsistenz: Menschliche Bediener können beim Be- und Entladevorgang zu Abweichungen führen, die die Qualität und Effizienz des Laserschneidvorgangs beeinträchtigen.
- Sicherheitsrisiken: Die manuelle Handhabung großer und schwerer Materialien kann Sicherheitsrisiken für die Bediener bergen.
2. Halbautomatisches Be- und Entladen
Halbautomatische Systeme kombinieren manuelle und automatisierte Prozesse. Normalerweise positioniert ein Bediener das Rohmaterial und das System lädt es automatisch in die Laserschneidmaschine. Ebenso entlädt das System fertige Teile, die der Bediener dann einsammelt. Diese Systeme bieten mehrere Vorteile:
- Reduzierter Arbeitsaufwand: Halbautomatische Systeme verringern den körperlichen Einsatz des Bedieners, verbessern die Ergonomie und verringern die Ermüdung.
- Verbesserte Effizienz: Die Automatisierung des Be- und Entladevorgangs beschleunigt den Vorgang im Vergleich zu vollständig manuellen Systemen.
- Verbesserte Sicherheit: Halbautomatische Systeme verbessern die Sicherheit am Arbeitsplatz, indem sie den Bedarf an manueller Materialhandhabung reduzieren.
3. Vollautomatisches Be- und Entladen
Vollautomatische Systeme übernehmen den gesamten Prozess des Ladens von Rohmaterialien und Entladens von Fertigteilen ohne menschliches Eingreifen. Diese Systeme sind mit fortschrittlichen Technologien wie Roboterarmen, Förderbändern und Sensoren ausgestattet, um ein hohes Maß an Automatisierung zu erreichen:
- Maximierte Produktivität: Vollautomatische Systeme können im Dauerbetrieb arbeiten, wodurch der Durchsatz der Laserschneidmaschine deutlich gesteigert wird.
- Konsistenz und Präzision: Durch Automatisierung wird eine konsistente Materialhandhabung gewährleistet, hohe Qualitätsstandards eingehalten und das Fehlerrisiko reduziert.
- Einsparungen bei den Arbeitskosten: Durch den Wegfall des Bedarfs an Handarbeit senken vollautomatische Systeme die Arbeitskosten und ermöglichen es den Bedienern, sich auf andere wertschöpfende Aufgaben zu konzentrieren.
- Sicherheit: Vollautomatische Systeme erhöhen die Sicherheit, indem sie die menschliche Interaktion mit Maschinen und Materialien minimieren.
Komponenten des Metallautomatisierungs-Be- und Entladesystems
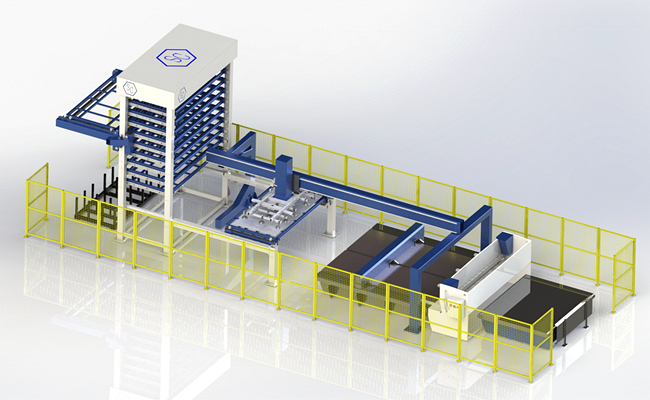
1. Materiallagerung
Das automatische Be- und Entladesystem für Metall verfügt über ein Metalllagersystem. Es verfügt über eine einfache Metallpalettierungsplattform oder kann mit dem automatisches Lagersystem aus Metall. Materiallagersysteme werden verwendet, um Rohmaterialien so zu organisieren und zu lagern, dass sie leicht zugänglich und handhabbar sind. Diese Systeme können einfache Regale oder moderne automatisierte Lager- und Abrufsysteme (AS/RS) sein, die in die Laserschneidmaschine integriert sind.
- Gestelle und Regalsysteme: Grundlegende Speicherlösungen, die es Bedienern ermöglichen, Materialien manuell abzurufen.
- Automatisierte Lager- und Bereitstellungssysteme (AS/RS): Fortschrittliche Systeme, die Materialien automatisch entsprechend den Produktionsanforderungen lagern und abrufen und so Platz und Effizienz optimieren.
2. Materialtransportausrüstung
Materialtransportgeräte sind für den Transport von Rohmaterialien vom Lager zur Laserschneidmaschine und für den Transport fertiger Teile zu ihrem nächsten Bestimmungsort unerlässlich. Zu den gängigen Arten von Materialtransportgeräten gehören:
- Förderbänder: Band- oder Rollenförderer transportieren Materialien zwischen verschiedenen Phasen des Laserschneidprozesses.
- Roboterarme: Mit Greifern oder Vakuumsaugvorrichtungen ausgestattete Roboterarme handhaben Materialien präzise und ermöglichen so das automatisierte Be- und Entladen.
- Kräne und Hebezeuge: Wird zum Heben und Bewegen schwerer Materialien verwendet, insbesondere in großen Fertigungsumgebungen.
3. Lader und Entlader
Lader und Entlader sind Spezialmaschinen, die den Prozess des Einlegens von Rohmaterialien in die Laserschneidmaschine und des Entnehmens fertiger Teile automatisieren. Diese Systeme können mit anderen Automatisierungsgeräten integriert werden, um einen nahtlosen Materialhandhabungsprozess zu schaffen.
- Bogenlader: Laden Sie Materialbögen automatisch in die Laserschneidmaschine, wodurch der manuelle Aufwand reduziert und die Effizienz gesteigert wird.
- Teileentlader: Automatisches Entfernen fertiger Teile vom Schneidbett und gewährleistet so einen reibungslosen und kontinuierlichen Betrieb.
4. Kontrollsysteme
Steuerungssysteme steuern den Betrieb der Lade- und Entladevorrichtungen und sorgen für eine präzise und koordinierte Bewegung der Materialien. Diese Systeme können eigenständig oder in die CNC-Steuerung der Laserschneidmaschine integriert sein.
- Speicherprogrammierbare Steuerungen (SPS): SPS werden zur Steuerung des Betriebsablaufs in automatisierten Systemen verwendet und gewährleisten eine genaue und zuverlässige Leistung.
- Mensch-Maschine-Schnittstellen (HMIs): HMIs bieten den Bedienern eine benutzerfreundliche Schnittstelle zur Überwachung und Steuerung des Be- und Entladevorgangs.
Vorteile automatisierter Be- und Entladesysteme
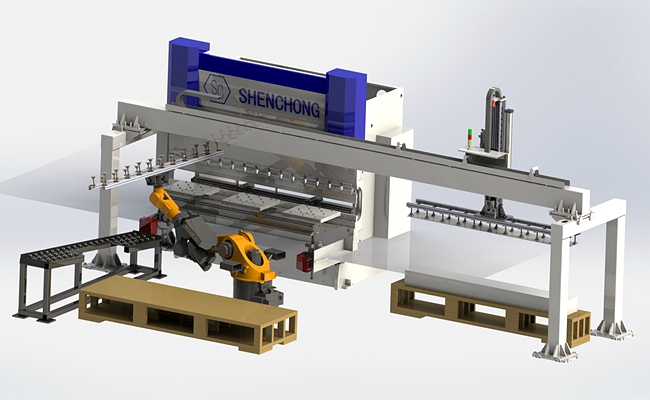
1. Verbesserte Produktivität
Automatisiertes Be- und Entladesystem für Bleche reduziert die zum Be- und Entladen von Materialien erforderliche Zeit erheblich und ermöglicht den Dauerbetrieb der Laserschneidmaschine. Diese gesteigerte Produktivität führt zu höherem Durchsatz und schnelleren Durchlaufzeiten.
2. Einsparungen bei den Arbeitskosten
Durch die Automatisierung von Materialhandhabungsprozessen können Hersteller die Abhängigkeit von manueller Arbeit reduzieren. Dies senkt nicht nur die Arbeitskosten, sondern minimiert auch das Risiko menschlicher Fehler und gewährleistet eine konsistente und qualitativ hochwertige Produktion.
3. Verbesserte Sicherheit
Automatisierte Be- und Entladesysteme erhöhen die Sicherheit am Arbeitsplatz, da sie den menschlichen Kontakt mit schweren und potenziell gefährlichen Materialien reduzieren. Dadurch wird das Risiko von Unfällen und Verletzungen minimiert und eine sicherere Arbeitsumgebung geschaffen.
4. Konsistenz und Qualität
Durch Automatisierung wird eine gleichmäßige Handhabung der Materialien gewährleistet, was für die Einhaltung hoher Qualitätsstandards im Laserschneidprozess von entscheidender Bedeutung ist. Automatisierte Systeme können Materialien präzise positionieren, wodurch die Wahrscheinlichkeit einer Fehlausrichtung verringert und genaue Schnitte gewährleistet werden.
5. Platzoptimierung
Moderne Lager- und Bereitstellungssysteme können die Nutzung des verfügbaren Platzes optimieren, sodass Hersteller mehr Materialien auf kleinerem Raum lagern können. Dies ist insbesondere in Umgebungen mit begrenztem Platzangebot von Vorteil.
6. Flexibilität
Automatisierte Systeme können so programmiert werden, dass sie mit unterschiedlichen Materialarten und Teilegrößen umgehen können, was für Flexibilität in der Produktion sorgt. Diese Anpassungsfähigkeit ist für Hersteller, die eine Vielzahl von Produkten herstellen oder häufig Produktionsläufe ändern, von entscheidender Bedeutung.
Fallstudien
1. Automobilhersteller
Ein Automobilhersteller implementierte ein vollautomatisches Be- und Entladesystem für seine Laserschneidmaschinen. Das System umfasste Roboterarme, Förderbänder und ein modernes Lager- und Abrufsystem. Das Ergebnis war eine Produktivitätssteigerung von 40%, eine Senkung der Arbeitskosten von 30% und eine verbesserte Sicherheit für die Bediener.
2. Zulieferer von Luft- und Raumfahrtkomponenten
Ein Zulieferer von Luft- und Raumfahrtkomponenten integrierte automatisierte Lade- und Entladesysteme in seine Laserschneidmaschinen. Die Systeme wurden mit Sensoren und KI-Algorithmen zur Echtzeitüberwachung und -optimierung ausgestattet. Diese Integration führte zu einer Reduzierung der Rüstzeiten um 501 TP3T, einer Steigerung des Produktionsdurchsatzes um 251 TP3T und einer verbesserten Qualitätskontrolle.
3. Elektronikhersteller
Ein Elektronikhersteller führte für seine Laserschneidvorgänge ein halbautomatisches Be- und Entladesystem ein. Das System verfügte über automatisierte Werkzeugwechsler und Förderbänder für die Materialhandhabung. Die Implementierung führte zu einer Reduzierung der Materialhandhabungszeit um 35%, verbesserter Genauigkeit und gleichbleibender Qualität bei der Herstellung elektronischer Komponenten.
Vor dem Kauf zu beachtende Punkte
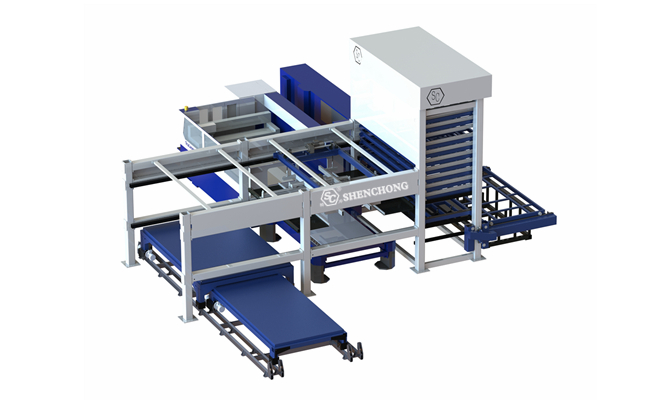
Beim Kauf eines automatischen Be- und Entladesystems für Metalle müssen Sie verschiedene Faktoren sorgfältig berücksichtigen, um sicherzustellen, dass das System Ihren Produktionsanforderungen und langfristigen Anforderungen entspricht. Hier sind die wichtigsten Punkte, die Sie bewerten sollten.
1. Materialhandhabungsfähigkeiten
- Metallart: Stellen Sie sicher, dass das System mit den spezifischen Metallen kompatibel ist, mit denen Sie arbeiten (z. B. Stahl, Aluminium usw.).
- Gewicht und Größe: Stellen Sie sicher, dass das System das Gewicht, die Größe und die Dicke der zu verarbeitenden Materialien verarbeiten kann.
- Blech-/Teileabmessungen: Stellen Sie sicher, dass das System den für Ihren Betrieb erforderlichen Größenbereich abdeckt.
2. Automatisierungsgrad
- Manuell, halbautomatisch oder vollautomatisch: Bestimmen Sie, ob Sie eine Vollautomatisierung benötigen oder ob ein halbautomatisches System ausreichen würde.
- Robotik-Integration: Beurteilen Sie, ob Roboterarme oder andere automatisierte Technologien für Ihre spezifische Anwendung erforderlich sind.
- Workflow-Effizienz: Überlegen Sie, wie stark der Prozess automatisiert sein sollte, um Ihrer Produktionsgeschwindigkeit zu entsprechen und Ausfallzeiten zu reduzieren.
3. Kapazität und Durchsatz
- Lade-/Entladegeschwindigkeit: Überprüfen Sie, ob das System den für Ihr Produktionstempo erforderlichen Durchsatz bewältigen kann.
- Zykluszeit: Analysieren Sie die Zykluszeiten der Lade- und Entladevorgänge, um sicherzustellen, dass sie mit Ihrem gesamten Produktionszeitplan übereinstimmen.
- Batch- oder kontinuierliches Laden: Bestimmen Sie je nach Produktionsumfang, ob ein Batch-System oder ein kontinuierliches Ladesystem besser geeignet ist.
4. Systemkompatibilität und Integration
- CNC/Pressen-Integration: Stellen Sie sicher, dass sich das System gut in Ihre CNC-Maschinen, Laser oder andere Schneide- und Biegemaschinen integrieren lässt.
- Softwarekompatibilität: Prüfen Sie, ob das System mit Ihrer vorhandenen Produktionsmanagementsoftware oder Ihren ERP-Systemen kompatibel ist.
- Automatisierungssteuerung: Überprüfen Sie die Benutzeroberfläche und die Steuerungssysteme auf Benutzerfreundlichkeit und Integration mit anderen Maschinen im Arbeitsablauf.
5. Platz und Layout
- Fußabdruck: Bedenken Sie den Platz, den das System einnehmen wird. Stellen Sie sicher, dass es in Ihren Produktionsbereich passt, ohne den Arbeitsablauf zu stören.
- Zugänglichkeit: Stellen Sie sicher, dass das System für Wartungsarbeiten, das Beladen mit Rohstoffen und das Entladen fertiger Teile leicht zugänglich ist.
6. Anpassungsoptionen
- Modulares Design: Suchen Sie nach Systemen mit modularen Konfigurationen, die eine zukünftige Erweiterung oder Anpassung an sich entwickelnde Produktionsanforderungen ermöglichen.
- Maßgeschneiderte Lösungen: Prüfen Sie, ob der Lieferant Anpassungsoptionen basierend auf Ihren spezifischen Material- oder Betriebsanforderungen anbietet.
7. Sicherheitsfunktionen
- Sicherheitssensoren und Schutzvorrichtungen: Stellen Sie sicher, dass das System über robuste Sicherheitsmechanismen wie Not-Aus-Schalter, Sensoren und physische Schutzvorrichtungen zum Schutz der Bediener verfügt.
- Einhaltung von Standards: Überprüfen Sie, ob das System den lokalen und internationalen Sicherheitsnormen, wie etwa den ISO- oder OSHA-Vorschriften, entspricht.
8. Kosten und ROI
- Anschaffungskosten: Analysieren Sie die Vorabinvestition und vergleichen Sie sie mit den erwarteten Vorteilen, wie z. B. einer höheren Produktivität oder geringeren Arbeitskosten.
- Instandhaltungskosten: Berücksichtigen Sie die langfristigen Wartungskosten und die Ersatzteilverfügbarkeit.
- Kapitalrendite: Berechnen Sie den ROI des Systems basierend auf seiner Fähigkeit, den Arbeitsaufwand zu reduzieren, die Effizienz zu steigern oder komplexere Aufgaben zu bewältigen.
9. Wartung und Support
- Serviceverträge: Bewerten Sie die vom Hersteller bereitgestellte Garantie und Serviceunterstützung.
- Wartungsanforderungen: Prüfen Sie, wie einfach die Wartung des Systems ist, wie viele Ersatzteile verfügbar sind und wie häufig Wartungsarbeiten erforderlich sind.
- Schulung und Installation: Stellen Sie sicher, dass der Lieferant Ihrem Team ausreichend Schulungen anbietet und Sie bei der Installation und Einrichtung unterstützt.
10. Ruf des Anbieters und Referenzen
- Lieferantenerfahrung: Informieren Sie sich über die Erfahrung des Anbieters mit der Bereitstellung von Automatisierungssystemen für Ihre Branche.
- Kundenrezensionen: Erwägen Sie, aktuelle Benutzer des Systems nach Referenzen zu fragen, um die Zuverlässigkeit und Leistung in realen Anwendungen beurteilen zu können.
- Kundendienst: Bewerten Sie die Qualität des Kundendienstes, einschließlich technischem Support, Reaktionszeit und Verfügbarkeit von Ersatzteilen.
11. Umweltauswirkungen
- Energieaufnahme: Analysieren Sie die Energieeffizienz des Systems, um die Betriebskosten niedrig zu halten und die Umweltbelastung zu minimieren.
- Geräuschpegel: Erwägen Sie den Einsatz von Geräuschreduzierungsfunktionen, wenn in Ihrer Produktionsumgebung Einschränkungen hinsichtlich des Geräuschpegels gelten.
Durch die sorgfältige Bewertung dieser Faktoren können Sie ein System auswählen, das Ihren Produktionsanforderungen entspricht, die Effizienz steigert und langfristigen Mehrwert bietet.
Preisspanne für Blechlade- und Entladesysteme
Die Preisspanne für automatisierte Be- und Entladesysteme für Metalle kann je nach Faktoren wie Größe, Kapazität, Automatisierungsgrad, Marke und spezifischen Funktionen des Systems (z. B. CNC-Integration, Robotertechnik und erweiterte Sicherheitsfunktionen) stark variieren. Im Allgemeinen fallen diese Systeme in die folgenden Preisspannen:
- Basissysteme: Für kleinere oder weniger komplexe Setups liegen die Preise normalerweise zwischen $20.000 bis $50.000.
- Mittelklasse-Systeme: Systeme mit moderaten Fähigkeiten, besserer Automatisierung und Integrationsoptionen kosten im Allgemeinen zwischen $50.000 und $150.000.
- High-End-Systeme: Hochentwickelte Systeme mit Funktionen wie Vollautomatisierung, integrierter Robotik und größeren Kapazitäten reichen von $150.000 bis $500.000 oder mehr.
Anpassungen und zusätzliche Funktionen wie Softwareintegration oder zusätzliche Sicherheitsmechanismen können sich ebenfalls auf den Preis auswirken. Um ein konkretes Angebot zu erhalten, wenden Sie sich an die Lieferanten, um einen genaueren, auf Ihre Bedürfnisse zugeschnittenen Preis zu erhalten.
Zukünftige Trends bei Be- und Entladesystemen
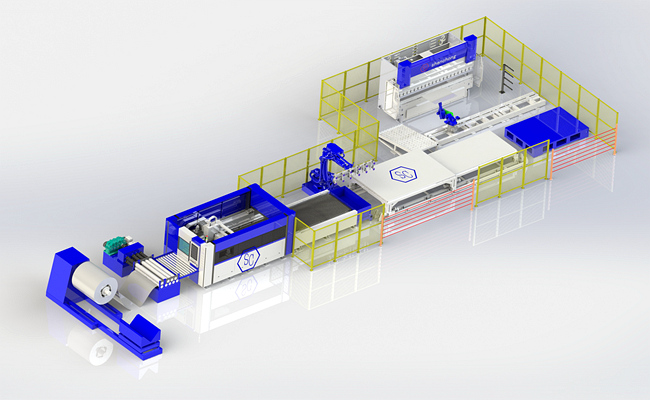
1. Integration mit Industrie 4.0
Die Integration von Be- und Entladesystemen mit Industrie 4.0-Technologien wie dem Internet der Dinge (IoT), künstlicher Intelligenz (KI) und maschinellem Lernen wird die Materialhandhabung revolutionieren. Diese Technologien ermöglichen Echtzeitüberwachung, vorausschauende Wartung und datengesteuerte Entscheidungsfindung und verbessern so die Effizienz und Zuverlässigkeit automatisierter Systeme. Zur Verbindung mit anderen Automatisierungseinheiten wie automatischen Metalllagersystemen, Roboter-Abkantpresse, Laserschneidmaschine zum Abwickeln und Nivellieren, Blechverarbeitungsfabrik kann integrieren Produktionslinien zur Blechautomatisierung.
2. Fortgeschrittene Robotik
Fortschritte in der Robotik treiben die Entwicklung immer ausgefeilterer und leistungsfähigerer automatisierter Systeme voran. Kollaborative Roboter (Cobots), die Seite an Seite mit menschlichen Bedienern arbeiten können, und autonome mobile Roboter (AMRs), die selbstständig navigieren und Materialien transportieren, werden immer häufiger eingesetzt.
3. Verbesserte Flexibilität
Zukünftige automatische Be- und Entladesysteme für Bleche werden eine größere Flexibilität bieten, sodass Hersteller problemlos zwischen verschiedenen Materialien und Teilegrößen wechseln können. Modulare und rekonfigurierbare Systeme ermöglichen eine schnelle Anpassung an sich ändernde Produktionsanforderungen.
4. Energieeffizienz
Da Nachhaltigkeit immer mehr an Bedeutung gewinnt, werden Be- und Entladesysteme für Metalle unter Berücksichtigung der Energieeffizienz entwickelt. Innovationen wie energieeffiziente Motoren, regenerative Bremssysteme und intelligentes Energiemanagement werden die Umweltauswirkungen der automatisierten Materialhandhabung verringern.
5. Verbesserte Benutzeroberflächen
Benutzerfreundliche Schnittstellen und intuitive Steuerungssysteme verbessern die Benutzerfreundlichkeit und Zugänglichkeit automatisierter Lade- und Entladesysteme. Fortschrittliche HMIs und Augmented Reality (AR)-Schnittstellen versorgen die Bediener mit Echtzeitinformationen und Anleitungen und verbessern so die Gesamteffizienz.
Abschluss
Metallautomatisierung Lade- und Entladesysteme für Laserschneidmaschinen sind entscheidende Komponenten, die die Produktivität steigern, Arbeitskosten senken und die Sicherheit in Fertigungsumgebungen verbessern. Von manuellen bis hin zu vollautomatischen Systemen bieten diese Technologien eine Reihe von Lösungen, um den unterschiedlichen Anforderungen verschiedener Branchen gerecht zu werden. Da sich die Fortschritte in den Bereichen Robotik, KI und Industrie 4.0-Technologien weiterentwickeln, sieht die Zukunft der automatisierten Materialhandhabung vielversprechend aus und bietet noch mehr Effizienz, Flexibilität und Nachhaltigkeit.
Hersteller, die in moderne Be- und Entladesysteme investieren, können mit erheblichen Verbesserungen ihrer Produktionsprozesse rechnen und so in einem zunehmend anspruchsvollen Markt wettbewerbsfähig bleiben. Durch das Verständnis der Vorteile, Anwendungen und zukünftigen Trends dieser Systeme können Unternehmen fundierte Entscheidungen treffen und das volle Potenzial ihrer Laserschneidvorgänge ausschöpfen.