Inhaltsverzeichnis
In der industriellen Produktion müssen häufig hochreflektierende Materialien wie Kupfer und Aluminium verarbeitet werden. Für viele Hersteller von Faserlaserschneidanlagen ist der Schneidprozess hochreflektierender Materialien jedoch oft eine Herausforderung und schwierig zu lösen. Viele Blechverarbeiter erkundigen sich häufig nach der Fähigkeit von Faserlaserschneidmaschinen, hochreflektierende Materialien wie Aluminium und Kupfer zu schneiden. In diesem Artikel wird untersucht, wie Faserlaserschneidmaschinen mit diesen reflektierenden Materialien umgehen, und einige fortschrittliche Technologien und bewährte Verfahren vorgestellt.
Was ist eine Laserschneidmaschine?
Eine Laserschneidmaschine ist ein mechanisches Gerät, das zum Schneiden einen Laserstrahl verwendet. Die Laserschneidmaschine fokussiert den Laserstrahl zu einem Strahl mit hoher Leistungsdichte und strahlt ihn auf die Oberfläche des Werkstücks, wodurch das Material seinen Schmelz- oder Siedepunkt erreicht. Gleichzeitig wird Hochdruckgas verwendet, um das geschmolzene oder verdampfte Metall wegzublasen, wodurch letztendlich eine Schnittnaht entsteht und der Schneidzweck erreicht wird.
Eigenschaften und Anwendung
Laserschneidmaschinen haben die folgenden Eigenschaften:
- Hohe Präzision: Der Durchmesser des Laserstrahls ist sehr klein, die Schnittgenauigkeit hoch und der Schnitt glatt.
- Hohe Geschwindigkeit: Das Laserschneiden ist schnell und hocheffizient.
- Nicht auf Muster beschränkt: Nicht auf herkömmliche Schnittmuster beschränkt, kann das Layout automatisch angepasst und Materialien gespeichert werden.
- Kleine Wärmeeinflusszone: Beim Schneidvorgang ist die Verformung der Platte gering und die Schnittnaht schmal.
- Keine mechanische Belastung: Der Schnitt weist keine mechanische Belastung und keine Schergrate auf.
- Niedrige Verarbeitungskosten: Geeignet für die Produktion im großen Maßstab, mit niedrigen Verarbeitungskosten.
- Laserschneidmaschinen werden hauptsächlich zum Schneiden von metallischen und nichtmetallischen Materialien verwendet und eignen sich besonders für die Präzisionsbearbeitung und anspruchsvolle Produktionsumgebungen.
Reflektierende Metallmaterialien verstehen
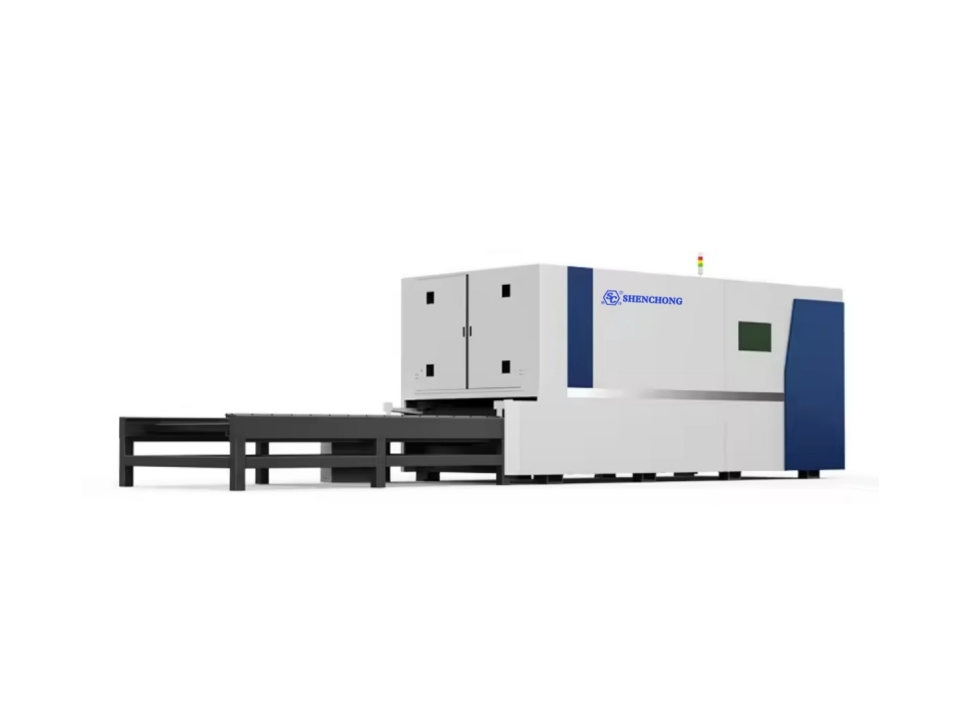
Warum ist das Laserschneiden hochreflektierender Metalle eine Herausforderung?
Zu den stark reflektierenden Metallmaterialien zählen Gold, Silber, Kupfer und Aluminium. Diese Materialien haben ein sehr hohes Reflexionsvermögen und werden häufig in Anwendungen eingesetzt, die ein hohes Reflexionsvermögen erfordern. Diese Materialien haben ein hohes Reflexionsvermögen und können dazu führen, dass der Strahl beim Laserschneiden zur Laserquelle zurückreflektiert wird, was möglicherweise zu Schäden am Gerät führt. Darüber hinaus können reflektierende Materialien auch die Effizienz und Qualität des Schneidens beeinträchtigen.
Was sind Metallmaterialien mit hoher Reflektivität?
Die Reflektivität von Gold, Silber und Kupfer ist sehr hoch, insbesondere die von Kupfer, das bei Lasern mit einer Wellenlänge von 1064 nm eine Reflektivität von bis zu 951 TP3T aufweist. Diese Materialien werden häufig zur Herstellung optischer Komponenten wie Spiegel verwendet, da sie die höchste Spiegelreflektivität aufweisen. Darüber hinaus kann Stahl nach der Schwärzungsbehandlung auch mehr als 801 TP3T Laserleistung absorbieren, was darauf hindeutet, dass die Oberflächenbehandlung des Materials einen erheblichen Einfluss auf seine Reflektivität hat.
Hochreflektierende Metallmaterialien haben ein breites Anwendungsspektrum in verschiedenen Bereichen. Beispielsweise können hochreflektierende Materialien in Bereichen wie Beleuchtung, Bildgebung, Luft- und Raumfahrt und Militär die Auflösung und Bildqualität optischer Systeme verbessern. Hochreflektierende Materialien können auch ideale optische Effekte in Gebäuden, Straßenbeleuchtung und Verkehrssignalen erzielen. Darüber hinaus werden hochreflektierende Beschichtungen auch auf Flugzeugtriebwerksdüsen und Satellitenantennen aufgebracht, um die Effizienz der Infrarot-Wärmestrahlung zu verbessern und die Tarnleistung zu steigern.
- Kupfer: Kupfer hat eine extrem hohe Wärmeleitfähigkeit und Reflektivität, wodurch es für die Laserenergie schwierig wird, sich im Schneidbereich zu konzentrieren. Kupfer hat eine niedrige Absorptionsrate für Laserstrahlen, normalerweise weniger als 30%, was 70% des reflektierten Lasers entspricht. Dies führt nicht nur zu Energieverlust und -verschwendung, sondern beschädigt auch leicht Komponenten wie Bearbeitungsköpfe, Linsen und Lasergeneratoren.
- Messing: Messing ist eine Legierung, die hauptsächlich aus Kupfer und Zink besteht. Aufgrund seines Zinkgehalts setzt es beim Schneiden jedoch giftigen Rauch frei und erfordert eine spezielle Behandlung. Messing ist ein hochreflektierendes Metallmaterial mit extrem geringer Absorptionsrate für Laser mit normaler Wellenlänge. Es hat auch eine gute Wärmeleitfähigkeit. Die absorbierte Wärme breitet sich schnell in die Umgebung der Verarbeitungszone aus und beeinträchtigt die Verarbeitungsqualität.
- Edelstahl: Obwohl Edelstahl eine geringere Reflektivität als Aluminium und Kupfer aufweist, weist er nach dem Polieren reflektierende Eigenschaften auf. Seine Oberflächenglätte und Oxidschicht können das Schneiden erschweren und leicht zu Problemen wie Blechverbrennungen führen.
- Aluminium: Aufgrund seiner hohen Reflektivität und Wärmeleitfähigkeit ist Aluminium beim Laserschneiden schwer zu verarbeiten. Reines Aluminium ist aufgrund seines niedrigen Schmelzpunkts und seiner hohen Wärmeleitfähigkeit schwieriger zu schneiden als eisenbasierte Metalle. Durch Beschichten oder Legieren können die Schneideffektivität, Effizienz und Sicherheit verbessert werden.
Herausforderungen beim Schneiden reflektierender Materialien
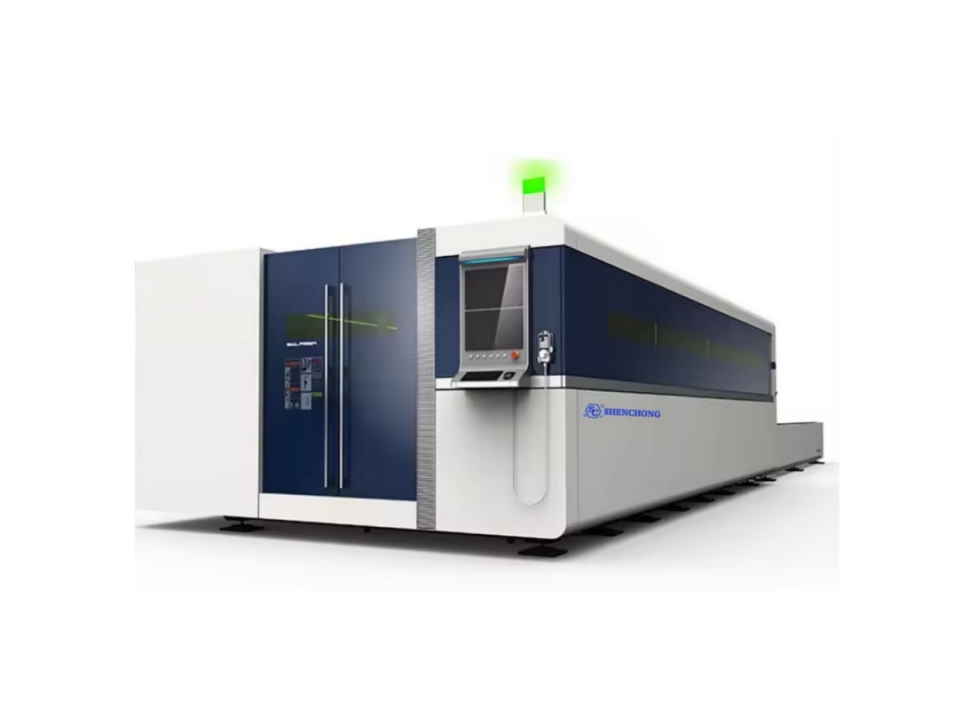
Herausforderung 1: Strahlreflexion
Reflektierende Materialien wie Aluminium und Edelstahl haben ein hohes Reflexionsvermögen. Sie reflektieren einen Teil des Laserstrahls zurück zur Laserquelle, was nicht nur die Schneidleistung verringert, sondern auch den Lasergenerator, insbesondere die Laserlinse und das Reflektorsystem, beschädigt.
Lösung
- Wählen Sie eine Faserlaserschneidmaschine mit Selbstschutzsystem. Wenn eine Laserstrahlreflexion erkannt wird, kann die Laserquelle automatisch abgeschaltet werden, um Geräteschäden zu vermeiden. Im Vergleich zu CO2-Laserschneidmaschinen verwenden Faserlaserschneidmaschinen optische Fasern zur Übertragung der Laserstrahlen, wodurch komplexe Reflexionssysteme reduziert und somit das Risiko einer Strahlreflexion verringert wird.
- Bedecken Sie die Oberfläche des reflektierenden Materials mit einer speziellen Beschichtung. Diese Beschichtungen können Laserstrahlen absorbieren und Laserstrahlreflexionen reduzieren.
Herausforderung 2: Qualität des Laserschnitts
Aufgrund ihrer hohen Reflektivität können reflektierende Metallmaterialien die Schnittgenauigkeit und -qualität bis zu einem gewissen Grad beeinträchtigen.
Lösung
- Verwenden Sie beim Schneidvorgang geeignete Hilfsgase und Schneidparameter.
- Wählen Sie eine hochpräzise Faserlaserschneidmaschine, um die Schnittgenauigkeit und -qualität durch die genaue Steuerung des Fokus und der Bewegungsbahn des Laserstrahls zu verbessern.
Herausforderung 3: Wärmeableitung
Materialien mit hoher Wärmeleitfähigkeit, wie beispielsweise Kupfer, leiten die Wärme beim Laserschneiden schnell ab, wodurch es für die Laserenergie schwierig wird, sich im Schnittbereich zu konzentrieren, was eine unzureichende Schnitttiefe oder eine verringerte Schnittgeschwindigkeit zur Folge hat.
Lösung
Optimieren Sie die Parameter des Laserschneidens, z. B. durch Erhöhen der Laserleistung, Reduzieren der Schnittgeschwindigkeit usw., um sicherzustellen, dass ausreichend Laserenergie im Schnittbereich konzentriert wird.
Verwenden Sie zum Schneiden Hilfsgase (wie Stickstoff, Argon usw.). Diese Gase können nicht nur dazu beitragen, geschmolzenes Metall wegzublasen, sondern auch die Wärmeleitung bis zu einem gewissen Grad reduzieren.
Wärmen Sie das Material vor dem Schneiden vor, um seine Wärmeleitfähigkeit zu verringern und den Wärmeverlust zu minimieren. Dadurch kann sich die Laserenergie leichter im Schneidbereich konzentrieren und die Schneideffizienz verbessern.
Einsatz von Kurzpuls- bzw. Ultrakurzpuls-Lasertechnologie zur Reduzierung der Wärmestauung und Verbesserung der Schnittqualität.
Herausforderung 4: Oxidation und Oberflächenverschmutzung
Aluminium und andere Materialien neigen zur Oxidation und bilden Verbindungen wie Aluminiumoxid, die an der Materialoberfläche und an der Schneide haften bleiben und die Schneidwirkung beeinträchtigen können.
Lösung
Behandeln Sie das Material vor dem Schneiden vor, um Oxide und Oberflächenverunreinigungen zu entfernen und so die Schneideffizienz zu verbessern.
Beim Schneidvorgang werden Inertgase (z. B. Stickstoff) als Schutzgase eingesetzt, um das Auftreten von Oxidationsreaktionen zu verringern.
Wählen Sie Schneidparameter und Prozessmethoden mit antioxidativen Eigenschaften, wie zum Beispiel das gepulste Laserschneiden.
Schneidtechnologie für reflektierendes Metallmaterial
Hilfsgas
- Sauerstoff: Beim Schneiden von Stahl und anderen Metallen kann Sauerstoff als Hilfsgas verwendet werden, um die Schnittgeschwindigkeit zu erhöhen. Sauerstoff reagiert chemisch mit Hochtemperaturmetallen und erzeugt einen exothermen Oxidationseffekt, der den Schneidprozess des Materials weiter beschleunigt.
- Stickstoff: Stickstoff ist sehr nützlich beim Schneiden leicht oxidierbarer Materialien wie Aluminium. Es kann verhindern, dass das Material während des Schneidvorgangs oxidiert, und so die Glätte und Genauigkeit der Schneide aufrechterhalten. Darüber hinaus kann Stickstoff auch die Emission von Rauch und schädlichen Gasen während des Schneidvorgangs reduzieren.
- Argongas: Argongas eignet sich zum Schneiden von Materialien wie Messing. Es ist gut inert und kann das Material während des Schneidvorgangs vor Oxidation schützen. Gleichzeitig kann Argongas auch die Entstehung von Rauch und schädlichen Gasen während des Schneidvorgangs reduzieren und so die Arbeitsumgebung verbessern.
Hilfsgas verstärkt zweifelsohne die Schneidwirkung.
Durch die chemische Reaktion zwischen Hilfsgas und Metallmaterial wird die Schneidfähigkeit verbessert.
Hilft dem Gerät, die Schlacke aus dem Schneidbereich wegzublasen, um den Schlitz zu reinigen.
Kühlt den Bereich um den Schnitt und schützt die Fokussierlinse.
Beim Laserschneiden von Kupfer reagiert die Einführung eines Hilfsgases bei hohen Temperaturen mit dem Metall, um die Schneidgeschwindigkeit und -wirksamkeit zu verbessern. Die Verwendung von O₂ kann die Verbrennung unterstützen und die Effizienz verbessern. Bei Laserschneidgeräten ist N₂ ein übliches Hilfsgas, um die Schneidwirkung zu verbessern. Für Kupferplatten unter 1 mm wird zum Schneiden und Bearbeiten natürlich kein Hilfsgas benötigt. Wenn die Kupferdicke jedoch 2 mm erreicht, kann N₂ nicht mehr die erwartete Bearbeitungswirkung erzielen. In diesem Fall muss Sauerstoff verwendet werden, um das Kupfer zu oxidieren und einen glatten Schnitt zu erzielen.
Antireflex-Lösung
Schutzbeschichtung: Das Vorbeschichten der Oberfläche hochreflektierender Materialien mit einer Schicht Antireflexbeschichtung kann die Reflektivität des Laserstrahls erheblich verringern, sodass mehr Laserenergie vom Material absorbiert werden kann, was wiederum die Schneidleistung und -effektivität verbessert. Diese Beschichtung muss gute Eigenschaften aufweisen, wie z. B. hohe Temperaturbeständigkeit und Korrosionsbeständigkeit, um die Stabilität während des Laserschneidprozesses zu gewährleisten.
Strahlschneiden: Die Strahlschneidetechnologie unterbricht den optischen Weg des Laserstrahls, bevor er zur Laserquelle reflektiert wird, und verhindert so wirksam Schäden am Lasergenerator durch reflektiertes Licht. Durch die Installation einer Strahlfalle kann reflektiertes Licht eingefangen werden, um sicherzustellen, dass die Laserenergie hauptsächlich auf das Material einwirkt, wodurch die durch Reflexion verursachten Schäden an der Ausrüstung verringert werden.
Hochleistungs-Lasergenerator
Beim Schneiden von stark reflektierenden Materialien ist die Einstechtechnik entscheidend. Um die Leistungsdichte zu maximieren und die Schmelzgeschwindigkeit zu beschleunigen, sollte der Brennpunkt so nah wie möglich an der Materialoberfläche positioniert werden. Dadurch wird die Anzahl der Wechselwirkungen zwischen dem Strahl und der Materialoberfläche minimiert, sodass der Strahl das Material effektiver schmelzen kann.
Kupfer (Cu) und Silber (Ag) sind hochreaktive Materialien für 1070 nm-Faserlaser mit niedriger Absorptionsrate, die viel niedriger ist als die von Eisen (Fe) und Stahl. Bei Festkörperlasern sind ihre Absorptionsraten jedoch relativ höher. Daher kann die Wahl des richtigen Lasertyps das Schneiden hochreflektierender Materialien erleichtern.
Verbesserung der Leistungsabgabe: Die Verwendung eines Lasergenerators mit höherer Leistung ist eine direkte Methode zur Bearbeitung stark reflektierender Materialien. Höhere Leistung bedeutet stärkere Durchdringung und größere Schnitttiefe, wodurch die Reflektivität des Materials effektiver überwunden werden kann.
Leistungsmodulation: Durch dynamisches Anpassen der Leistungsabgabe des Lasers kann eine präzise Steuerung basierend auf der Reflektivität des Materials und den Schneidanforderungen erreicht werden. Diese Anpassung stellt sicher, dass die Laserenergie während des gesamten Schneidvorgangs optimal bleibt, was die Schnittqualität und -effizienz verbessert.
Pulsmodulation
Steuerbarer Puls: Mithilfe der steuerbaren Pulstechnologie kann ein kontinuierlicher Laserstrahl in eine Reihe kurzer und starker Pulse aufgeteilt werden. Dieser Pulsmodus kann die Wärmeansammlung im Material verringern, Verformungen oder Schmelzen durch Überhitzung verhindern und so die Schnittgenauigkeit und Kantenqualität verbessern.
Kurzpuls: Kurzpulslaser haben eine höhere Spitzenleistung und eine kürzere Dauer, wodurch Materialien schneller erhitzt und verdampft werden können und ein präziseres Schneiden möglich ist. Gleichzeitig können Kurzpulse auch die Wärmeeinflusszone reduzieren und die umgebenden Strukturen des Materials vor Beschädigungen schützen.
Fortschrittliche Technologie der Faserlaserschneidmaschine
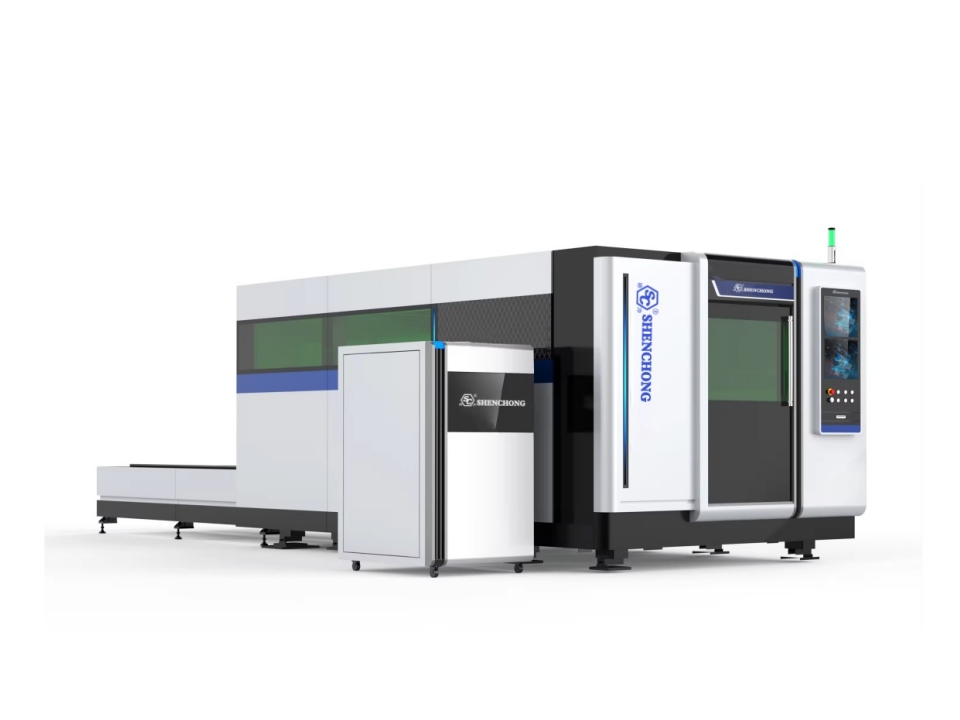
Echtzeitüberwachung
- Prozesskontrolle: Mithilfe der Echtzeitüberwachungstechnologie können während des Schneidvorgangs verschiedene Parameter (wie Temperatur, Geschwindigkeit, Leistung usw.) in Echtzeit erfasst und dynamisch entsprechend den voreingestellten Prozessanforderungen angepasst werden, um die Stabilität und Steuerbarkeit des Schneidvorgangs sicherzustellen.
- Qualitätssicherung: Durch die Überwachung des Schneideffekts in Echtzeit (wie Schlitzbreite, Rauheit usw.) können mögliche Qualitätsprobleme rechtzeitig erkannt und korrigiert werden, um die Qualität der geschnittenen Produkte sicherzustellen.
- Die Echtzeitüberwachungstechnologie überwacht den gesamten Schneidprozess durch in Faserlaserschneidmaschinen integrierte Sensoren und Überwachungssysteme und sorgt so für eine automatische Anpassung der Parameter während des Schneidprozesses und eine stabile Qualität. Diese Technologie kann Fehlbedienungen verhindern, die Schnittgenauigkeit aufrechterhalten und die Gesamtproduktionseffizienz verbessern.
Adaptive Optik
- Automatische Fokussierung: Durch die Optimierung des Fokussierungssystems kann die adaptive Optiktechnologie die Fokussierungsgenauigkeit und Energiedichte von Laserstrahlen deutlich verbessern und so die Schnittqualität und Effizienz steigern.
- Echtzeitanpassung: Die adaptive Optiktechnologie kann den Fokussierungszustand des Laserstrahls in Echtzeit überwachen und basierend auf Rückkopplungssignalen Echtzeitanpassungen vornehmen, um sicherzustellen, dass sich der Laserstrahl immer im optimalen Fokussierungszustand befindet.
Das adaptive Optiksystem optimiert den Fokus des Laserstrahls dynamisch, indem es das optische System in Echtzeit anpasst und so eine bessere Anpassung an Materialien unterschiedlicher Dicke oder Reflexion während des Schneidvorgangs gewährleistet. Diese Anpassung kann den Reflexionsverlust des Laserstrahls verringern und die Schneidgenauigkeit und -effizienz verbessern.
Strahlformung
Mithilfe der Strahlformungstechnologie kann das Laserstrahlprofil an unterschiedliche Schneidanforderungen angepasst werden. Dadurch wird die Energieverteilung des Laserstrahls optimiert und die Schneidleistung und -qualität verbessert.
Verbessern Sie die Energienutzung: Durch die Formung von Laserstrahlen können die Absorptionseigenschaften von Schneidmaterialien besser angepasst werden, die Nutzung der Laserenergie wird verbessert und Energieverschwendung reduziert.
Die Strahlformungstechnologie ermöglicht die individuelle Gestaltung der Form von Laserstrahlen. Der Laserstrahl wird durch spezielle optische Elemente (wie Strahlformer, Mikrolinse usw.) geformt, um ihn von der ursprünglichen Gaußschen Verteilung in die gewünschte Form (wie Kreis, Rechteck, Quadrat usw.) umzuwandeln. Anpassung an unterschiedliche Schneidanforderungen. Diese Technologie kann die Energieeffizienz verbessern, insbesondere bei der Verarbeitung hochreflektierender Materialien, und zwar mit erheblichen Auswirkungen, was zur Verbesserung der Verarbeitungseffizienz und -qualität beiträgt.
Zusammenfassend lässt sich sagen, dass Faserlaserschneidmaschinen durch den Einsatz dieser fortschrittlichen Technologien die Herausforderungen beim Schneiden reflektierender Materialien wirksam bewältigen und die Schneideffizienz, -genauigkeit und -qualität verbessern können.
Alternative Schneidemethoden
Obwohl Faserlaserschneidmaschinen viele Lösungen bieten, um reflektierende Materialien mit hoher Präzision zu schneiden, möchten viele Benutzer die Laserschneidmaschine dennoch nicht als erste Wahl zum Schneiden dieser Materialien verwenden. Die Verwendung der Faserlaserschneidmaschine zum Schneiden einiger stark reflektierender Materialien kann zu einer Verschlechterung des Materials führen. In diesem Fall entscheiden sie sich normalerweise für die traditionelle Plattenschneidemethode, nämlich eine Plattenschere.
SC-Maschinen hat die automatische Frontplattenschermaschine speziell zum Schneiden großer Mengen von Kobaltplatten, Nickelplatten und Kupferplatten entwickelt.
Abschluss
In diesem Artikel geben wir Einblicke in die Verwendung von Laserschneiden zum Schneiden reflektierender Metalle. Laserschneidmaschinen eignen sich besonders für die präzise und effiziente Bearbeitung hochreflektierender Metalle wie Messing, Aluminium und Silber. Laserschneiden wird auch weiterhin die gute Wahl für die Bearbeitung hochreflektierender Metalle sein und der Metallverarbeitung in der Fertigungsindustrie mehr Komfort und Vorteile bringen.