Inhaltsverzeichnis
Einführung zur Laserschneidqualität
Laserschneiden ist ein präzises und effizientes Verfahren, das in vielen Branchen weit verbreitet ist, von der Automobilindustrie über die Luft- und Raumfahrt bis hin zur Elektronik und Fertigung. Die Technik ermöglicht das präzise Schneiden von Materialien wie Metallen, Kunststoffen und Keramik mithilfe eines hochfokussierten Laserstrahls. Trotz der vielen Vorteile kann die Qualität lasergeschnittener Produkte je nach verschiedenen Faktoren variieren. Dieser Artikel untersucht die kritischen Faktoren, die die Qualität des Laserschneidens beeinflussen, und behandelt dabei Materialeigenschaften, Maschineneinstellungen, Lasertyp und äußere Bedingungen.
Hochmoderne Qualitätsmetriken
Zur Bewertung der Qualität des Laserschneidens werden häufig verschiedene Maßstäbe verwendet:
- Schnittbreite: Die Breite des Schnitts, der schmal und gleichmäßig sein sollte.
- Schlacke: Überschüssiges geschmolzenes Material, das an der Schnittkante haftet und minimiert werden sollte.
- Rauheit: Die Oberflächenstruktur der Schnittkante, wo glattere Kanten erwünscht sind.
- Wärmeeinflusszone (WEZ): Der Bereich um den Schnitt, der thermischer Belastung ausgesetzt ist, die so gering wie möglich sein sollte.
- Rechtwinkligkeit der Kanten: Die Rechtwinkligkeit der Schnittkante im Verhältnis zur Materialoberfläche.
Materialeigenschaften
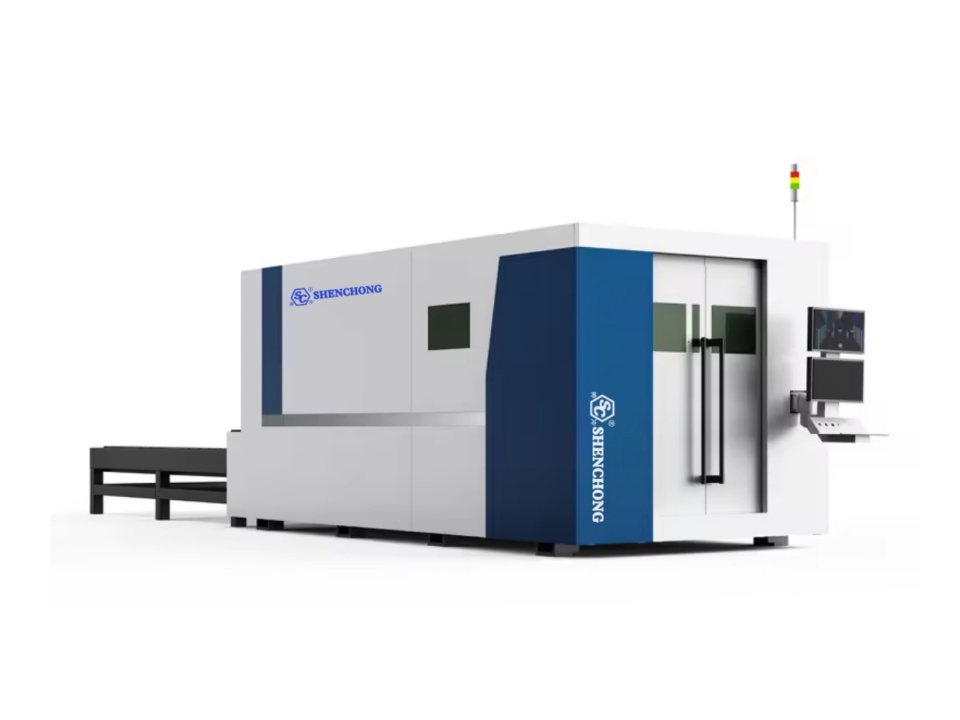
Materialtyp
Die Art des zu schneidenden Materials spielt eine wichtige Rolle bei der Bestimmung der Laserschnittqualität. Verschiedene Materialien reagieren aufgrund ihrer physikalischen und chemischen Eigenschaften unterschiedlich auf Laserstrahlen. Metalle wie Stahl, Aluminium und Kupfer sowie Nichtmetalle wie Kunststoffe, Keramik und Verbundwerkstoffe weisen unterschiedliche Absorptions- und Reflexionsgrade auf.
Metalle: Materialien wie Weichstahl sind ideal zum Laserschneiden, da sie die Laserenergie effizient absorbieren und bei relativ niedrigeren Temperaturen schmelzen. Andererseits erfordern stark reflektierende Materialien wie Kupfer und Aluminium spezielle Laser, wie etwa Faserlaser, um saubere Schnitte zu erzielen.
Nichtmetalle: Materialien wie Holz, Acryl und Kunststoffe können ebenfalls mit dem Laser geschnitten werden, ihre Reaktion auf Hitze kann jedoch je nach eingesetzter Energie zu Verbrennungen, Verkohlungen oder Schmelzen führen. Die Absorptionseigenschaften und Schmelzpunkte dieser Materialien bestimmen die Lasereinstellungen, die für eine optimale Laserschnittqualität erforderlich sind.
Materialstärke
Die Materialdicke ist einer der entscheidendsten Faktoren beim Laserschneiden. Dickere Materialien erfordern höhere Energieniveaus zum Eindringen, was zu langsameren Schnittgeschwindigkeiten führt. Dünne Materialien hingegen lassen sich zwar schnell schneiden, können aber verbrennen oder schmelzen, wenn zu viel Energie eingesetzt wird.
- Dünne Materialien (<1 mm): Erfordert niedrige Leistung und höhere Geschwindigkeiten, um eine übermäßige Wärmeansammlung zu vermeiden, die zu Verformungen oder thermischen Schäden führen kann.
- Dicke Materialien (>10 mm): Erfordern eine hohe Laserleistung und langsamere Geschwindigkeiten, um eine vollständige Durchdringung und saubere Kanten sicherzustellen, neigen jedoch bei fehlender Optimierung zu erhöhter Bartbildung (erstarrter Schlacke) und Rauheit an den Schnittkanten.
Oberflächenqualität des Materials
Die Oberflächenbeschaffenheit des Materials beeinflusst, wie gut es mit dem Laserstrahl interagiert. Saubere, glatte Oberflächen reflektieren den Laserstrahl in der Regel gleichmäßig, was zu einem gleichmäßigen Schnitt führt. Materialien mit Unregelmäßigkeiten wie Rost, Oxidation oder Beschichtungen können den Laserstrahl streuen, was zu einer ungleichmäßigen Energieabsorption und einer schlechten Schnittqualität führt.
- Saubere Oberflächen: Verbessert die Strahlabsorption und führt zu glatteren, saubereren Schnitten.
- Kontaminierte Oberflächen: Oxide, Öle oder Beschichtungen können die Effizienz des Lasers beeinträchtigen und zu unregelmäßigen Kanten oder erhöhter Schlackebildung führen.
Materialreflexion
Reflektierende Materialien wie Aluminium, Messing und Kupfer stellen beim Laserschneiden eine Herausforderung dar. Sie reflektieren einen erheblichen Teil der Laserenergie von der Schnittfläche weg, was die Effizienz verringert und zu Schnitten von schlechter Qualität führt. Speziallaser, wie Faserlaser mit kürzeren Wellenlängen, sind beim Schneiden reflektierender Materialien effektiver.
- Hohe Reflektivität: Erfordert spezielle Geräte oder Beschichtungsbehandlungen zur Verbesserung der Laserabsorption.
- Geringe Reflektivität: Verbessert die Energieabsorption, was zu saubereren und schnelleren Schnitten führt.
Laserparameter
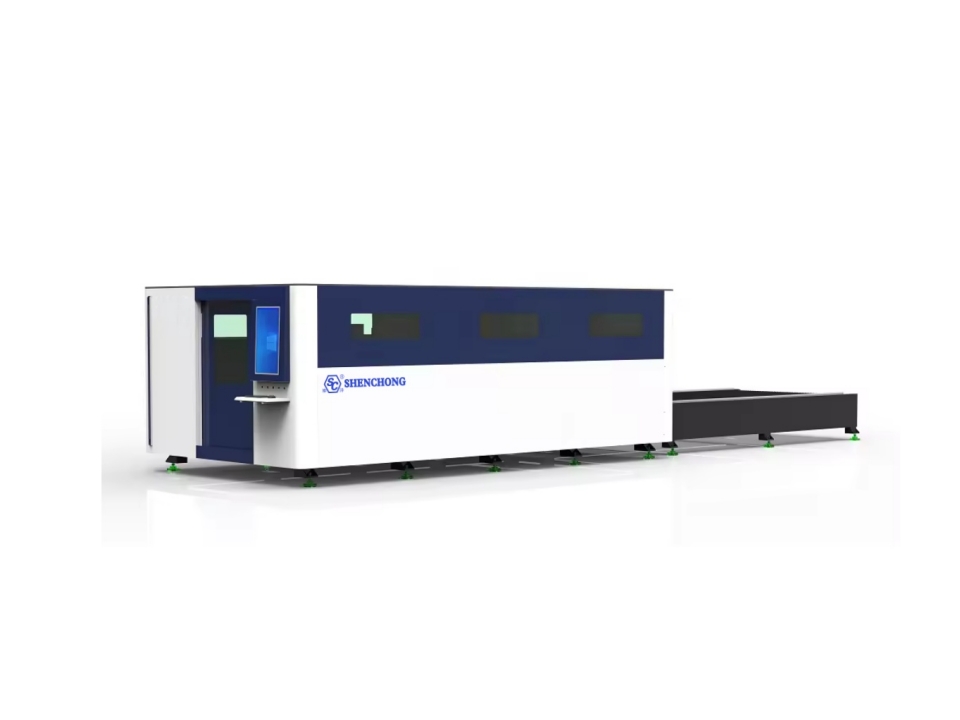
Laserleistung
Laserleistung des Laser-Schneide-Maschine wirkt sich direkt auf den Schneidvorgang aus, indem es bestimmt, wie viel Energie zum Schmelzen oder Verdampfen des Materials zur Verfügung steht. Höhere Leistung führt zu schnelleren und tieferen Schnitten, aber übermäßige Leistung kann übermäßige Wärmeeinflusszonen (WEZ) verursachen, was zu Verkohlen, Schmelzen oder Verformung des Materials führt.
- Einstellungen für niedrigen Stromverbrauch: Am besten geeignet für dünne oder empfindliche Materialien, bei denen es auf Präzision ankommt und übermäßige Hitze zu Schäden führen kann.
- Hohe Leistungseinstellungen: Erforderlich zum Schneiden dickerer Materialien oder von Materialien, die zum effizienten Schneiden viel Energie erfordern, wie z. B. Metalle.
Fokusposition
Der Brennpunkt des Laserstrahls muss genau auf die Materialoberfläche ausgerichtet sein, um einen präzisen Schnitt zu gewährleisten. Ist der Brennpunkt zu hoch oder zu niedrig, kann dies zu einem Verlust der Energieeffizienz führen und zu Graten, rauen Kanten oder unvollständigen Schnitten führen.
- Optimaler Fokus: Erzeugt einen schmalen Schnittschnitt (Schnittbreite) und glatte Kanten.
- Falsch ausgerichteter Fokus: Verursacht Unregelmäßigkeiten, eine größere Schnittbreite und eine raue Oberflächenbeschaffenheit.
Strahlqualität (Modus)
Die Strahlqualität, die durch den Lasermodus gekennzeichnet ist, ist ein weiterer wichtiger Faktor, der die Schneidleistung beeinflusst. Der Lasermodus bezieht sich auf die Verteilung der Laserenergie innerhalb des Strahls.
- Singlemode-Laser: Erzeugen Sie hochwertige, konzentrierte Strahlen, die sauberere Schnitte und höhere Präzision ergeben, insbesondere bei dünnen Materialien.
- Multimode-Laser: Haben eine stärker gestreute Energieverteilung, was beim Schneiden dickerer Materialien von Vorteil sein kann, aber zu raueren Kanten führen kann.
Schnittgeschwindigkeit
Die Schnittgeschwindigkeit hängt direkt von der Laserleistung und dem Materialtyp ab. Bei einer niedrigeren Geschwindigkeit hat der Laser mehr Zeit, in das Material einzudringen, aber es besteht auch die Gefahr eines Hitzestaus, der zu einem breiteren Schnitt und möglichen Verformungen führt.
- Optimale Geschwindigkeit: Gleichgewicht zwischen schnell genug, um übermäßige Hitzeansammlung zu vermeiden, und langsam genug, um einen sauberen Schnitt zu gewährleisten.
- Zu schnell: Kann zu unvollständigen Schnitten, gezackten Kanten und erhöhter Bartbildung führen.
- Zu langsam: Kann zu übermäßiger Wärmezufuhr führen und so zum Schmelzen, Verformen oder Verbrennen führen.
Hilfsgasparameter
Hilfsgase wie Sauerstoff, Stickstoff oder Druckluft werden normalerweise verwendet, um geschmolzenes Material wegzublasen und den Schneidvorgang zu verbessern.
Gasart
Die Art des verwendeten Hilfsgases kann die Schnittqualität erheblich beeinflussen:
- Sauerstoff (O₂): Erhöht die Energie des Schneidprozesses, indem es als Katalysator bei der Oxidation von Metallen wirkt, was zu schnelleren Schnittgeschwindigkeiten und einer raueren, oxidierten Kante führt.
- Stickstoff (N₂): Inertgas, das Oxidation verhindert und zu saubereren Schnitten mit minimaler Verfärbung führt, insbesondere bei Edelstahl und Aluminium. Im Vergleich zu Sauerstoff erzeugt es auch glattere Kanten.
- Druckluft: Eine kostengünstige Alternative, die zum Schneiden dünnerer Materialien verwendet werden kann, im Vergleich zu Stickstoff oder Sauerstoff jedoch zu einer schlechteren Schnittqualität führen kann.
Gasdruck
Auch der Druck des Hilfsgases beeinflusst die Qualität des Schnitts. Ein höherer Gasdruck kann geschmolzenes Material effizienter entfernen und die Bildung von Schlacke verhindern. Zu hoher Druck kann jedoch Turbulenzen verursachen, die zu rauen Kanten oder übermäßigem Materialausblasen führen.
- Hochdruck: Bei dicken Materialien erforderlich, um geschmolzenes Material wegzublasen und Schlacke zu verhindern.
- Niederdruck: Besser geeignet für dünne Materialien, bei denen übermäßige Kraft den Schnitt verzerren könnte.
Äußere Bedingungen
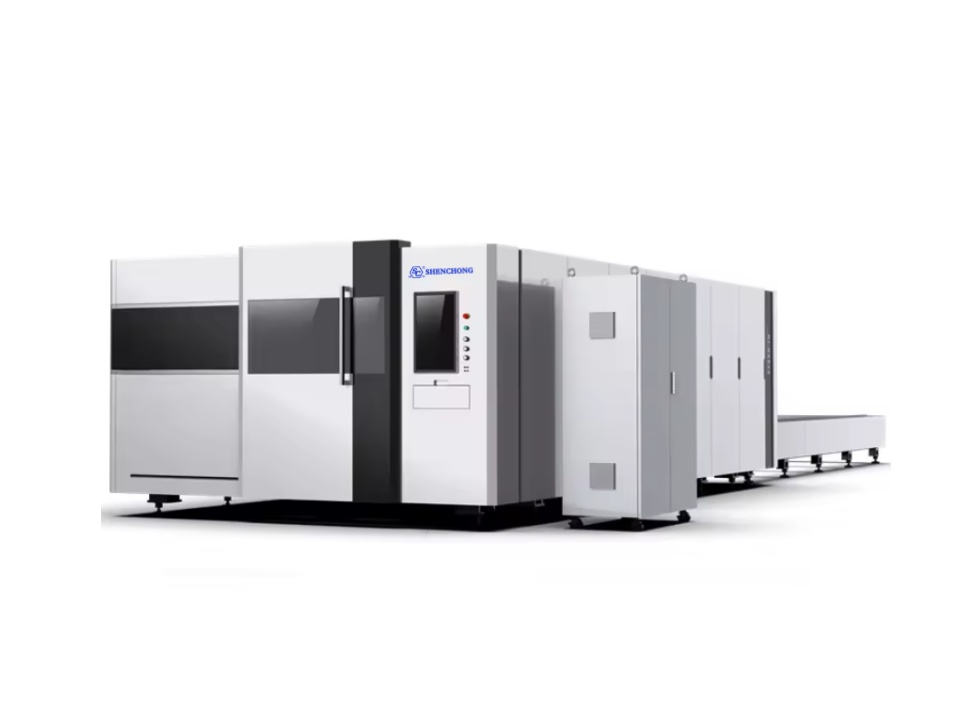
Maschinenstabilität und Kalibrierung
Die richtige Kalibrierung und Stabilität der Faserlaserschneidmaschine sind für die Aufrechterhaltung einer gleichbleibenden Laserschneidqualität unerlässlich. Faktoren wie Laserausrichtung, Spiegelsauberkeit und der Zustand des Schneidkopfes können das Ergebnis beeinflussen. Regelmäßige Wartung ist entscheidend, um sicherzustellen, dass die Maschine mit maximaler Effizienz arbeitet.
- Gut kalibrierte Maschine: Führt zu gleichmäßigen, hochwertigen Schnitten mit minimalem Nachbearbeitungsbedarf.
- Schlecht gewartete Maschine: Führt zu Strahlfehlausrichtung, unregelmäßigen Schnittkanten und inkonsistenter Leistung.
Schneidbett-Design
Das Design des Schneidbetts beeinflusst die Wärmeableitung während des Schneidvorgangs. Ein gut gestaltetes Schneidbett minimiert die Wärmereflexion zurück in das Material und verhindert so einen Hitzestau und mögliche Verformungen.
- Belüftetes Schneidbett: Reduziert die Rückreflexion und sorgt für eine bessere Schnittqualität.
- Solides Schneidbett: Kann die Wärmereflexion erhöhen und so zu Materialverzerrungen oder -schäden führen.
Software und Steuerungssysteme
CNC-Programmierung
Die CNC-Programmierung (Computer Numerical Control) beeinflusst direkt den Schnittweg, die Geschwindigkeit und die Gesamtpräzision. Schlecht optimierte CNC-Programme können zu ineffizienten Schnitten führen, was zu Kanten von schlechter Qualität, übermäßiger Hitzeentwicklung oder Materialverschwendung führt.
- Präzise CNC-Programmierung: Führt zu optimierten Schneidpfaden und hochwertigen Schnitten bei minimalem Materialabfall.
- Ineffiziente Programmierung: Kann zu inkonsistenter Schnittqualität führen, insbesondere bei komplexen Formen oder dicken Materialien.
Echtzeit-Überwachungssysteme
Moderne Laserschneidmaschinen sind mit Echtzeit-Überwachungssystemen ausgestattet, die Parameter wie Laserleistung, Fokus und Gasdruck im laufenden Betrieb anpassen, um optimale Schneidbedingungen aufrechtzuerhalten.
- Mit Monitoringsystemen: Die Maschine kann automatische Anpassungen vornehmen, um eine gleichbleibende Schnittqualität sicherzustellen, auch wenn sich die Umgebungs- oder Materialbedingungen ändern.
- Ohne Überwachungssysteme: Es ist ein manueller Eingriff erforderlich, der möglicherweise nicht so präzise oder reaktionsschnell ist und daher zu potenziellen Qualitätsproblemen führen kann.
Umgebungstemperatur und Luftfeuchtigkeit
Umgebungsbedingungen wie Temperatur und Luftfeuchtigkeit können die Leistung des Laserschneidvorgangs beeinflussen. Hohe Temperaturen können das Kühlsystem des Lasers beeinträchtigen, während hohe Luftfeuchtigkeit das Hilfsgas beeinträchtigen oder Kondensation auf Spiegeln und Linsen verursachen kann, was die Qualität des Laserstrahls beeinträchtigt.
- Kontrollierte Umgebung: Sorgt für gleichbleibende Schneidergebnisse und verhindert Schwankungen in der Schnittqualität.
- Unkontrollierte Umgebung: Kann zu Überhitzung oder Kondensation führen und so die Effizienz und Präzision des Laserschneidprozesses verringern.
Abschluss
Laserschneiden ist ein komplexer Prozess und die Qualität des Laserschnitts wird von zahlreichen Faktoren beeinflusst, unter anderem von Materialeigenschaften, Laserparametern, Hilfsgasverbrauch, Maschinenstabilität und äußeren Bedingungen.