Inhaltsverzeichnis
Während des Produktions- und Herstellungsprozesses können beim Biegen von Blechteilen verschiedene Biegequalitätsprobleme auftreten, die die Verbesserung der Produktionseffizienz und die Stabilität der Produktqualität beeinträchtigen können. Dieser Artikel befasst sich ausführlich mit häufigen Biege- und Schneidqualitätsproblemen in der Produktionspraxis, analysiert die Ursachen der Probleme und schlägt Lösungen vor, um Erfahrungen und Referenzen für ähnliche Probleme in der nachfolgenden Produktionspraxis bereitzustellen.
Einführung
Beim Blechbiegen wird eine Universalform (oder Spezialform) verwendet, die mit einem CNC-Abkantpresse um Bleche in verschiedene gewünschte geometrische Querschnittsformen von Werkstücken zu biegen. Die Rationalität des Biegeprozesses wirkt sich direkt auf die endgültige Formgröße und das Aussehen des Produkts aus. Eine sinnvolle Auswahl von Biegeformen ist für die endgültige Formgebung der Produkte von entscheidender Bedeutung.
Im tatsächlichen Produktionsprozess treten aufgrund der Unsicherheit der Produktgröße und der Vielfalt der Produkttypen beim Biegen kaltverarbeiteter Werkstücke häufig Probleme wie Größenstörungen und nicht übereinstimmende Formwinkel auf, die die Produktion erheblich erschweren. Aufgrund des Einflusses von Faktoren wie Produktgröße, Form, Material, Form, Ausrüstung und Zusatzeinrichtungen während des Biegeprozesses können verschiedene Qualitätsprobleme auftreten, die die Produktionseffizienz und die Stabilität der Produktqualität beeinträchtigen. Daher ist es besonders wichtig, das Auftreten dieser Biegequalitätsprobleme anzugehen und zu vermeiden. Dieser Artikel fasst hauptsächlich die häufigsten Qualitätsprobleme beim Blechbiegen in der Produktionspraxis zusammen und beschreibt sie, analysiert die Gründe anhand der Produktionserfahrung und schlägt Lösungen vor.
Häufige Probleme mit der Biegequalität
Biegen und Knacken
Biegerisse sind das Phänomen, dass nach dem Schneiden, Scheren oder Stanzen häufig Grate oder kleine Risse an den Kanten von Materialien auftreten. Beim Biegen bilden sich leicht Spannungskonzentrationen, die zu Rissen führen. Die U-förmige Verstärkungsnut von Lokomotivteilen reißt nach dem Biegen an den Ecken, wie in Abbildung 1 dargestellt.
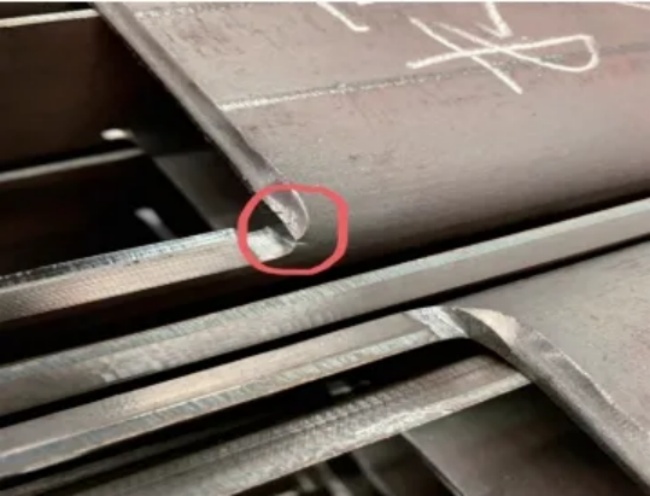
Abbildung 1 Biegung und Rissbildung
Die Hauptgründe für Verbiegungen und Risse sind:
- Unsaubere Grate an den Kanten der Teile.
- Die Biegerichtung verläuft parallel zur Walzrichtung des Bleches.
- Der Biegeradius des Bleches ist zu klein.
Während des Produktions- und Herstellungsprozesses müssen Biege- und Rissphänomene entsprechend den spezifischen Umständen behandelt werden. Zur Lösung des Biege- und Rissproblems in Abbildung 1 kann die Methode des Hinzufügens von Prozesslöchern oder Prozessnuten angewendet werden, wie in Abbildung 2 dargestellt.
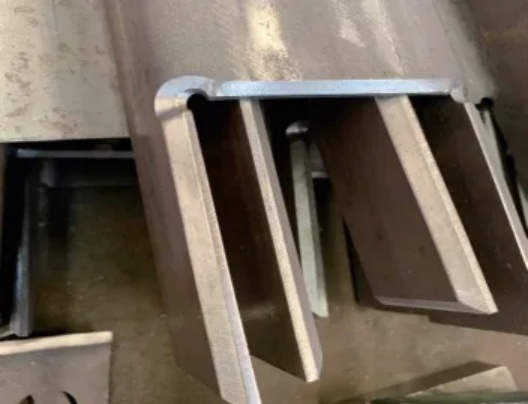
Abbildung 2: Prozesslöcher hinzufügen
Biegeinterferenz
Biegestörungen betreffen hauptsächlich Produkte mit sekundärer oder höherer Biegung, bei denen die Biegekante mit der Form oder Ausrüstung kollidiert, was dazu führt, dass sie nicht richtig geformt werden können. Biegestörungen werden hauptsächlich durch die Form, Größe und Form der Teile beeinflusst und werden hauptsächlich durch die Konstruktionsstruktur des gebogenen Teils selbst, die ausgewählte Biegefolge und die ausgewählte Biegeform verursacht. Daher umfassen die Hauptlösungen:
- Herstellen neuer oder Ersetzen von Formen (z. B. Biegemesserformen).
- Umformung von Biegeformen (zB mechanische Bearbeitung von Ortteilen).
- Passen Sie die Biegereihenfolge an (z. B. umgekehrte Verformungsmethode).
- Ändern Sie die Biegegröße der Teile. Beispielsweise besteht die Montagehalterung für den Chassis-Zubehörkanal der Shanghai Metro Line 18 aus U-förmigem Kanalstahl mit einer mittleren Breite von 100 mm, einer Kantenhöhe von 80 mm und einem Biegeradius von 15 mm. Simulieren Sie das Biegen basierend auf den vorhandenen Formen in der Werkstatt, um Biegestörungen zu erzeugen.
Als Reaktion auf dieses Interferenzphänomen wurde für das Biegeoberwerkzeug eine lokale mechanische Bearbeitungsmethode übernommen (siehe Abbildung 3). Eine 140 mm × 48 mm große Kerbe wurde entlang der Mittellinie des vorhandenen R15 mm-Oberwerkzeugs mit geradem Messer (L = 800 mm) geschnitten (siehe Abbildung 4). Die Kerbenposition wurde durch Kombination mit der simulierten Biegeinterferenzposition bestimmt, ohne ihre ursprüngliche Funktion zu beeinträchtigen. Nach der Modifizierung der Biegeform wurde das Problem der Biegeinterferenz erfolgreich gelöst.
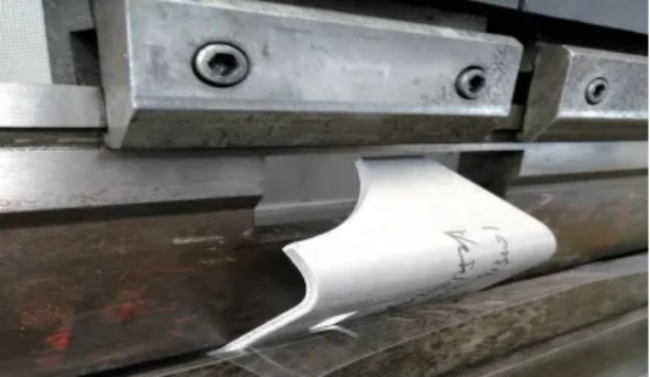
Abbildung 3: Biegen nach der Oberformbearbeitung
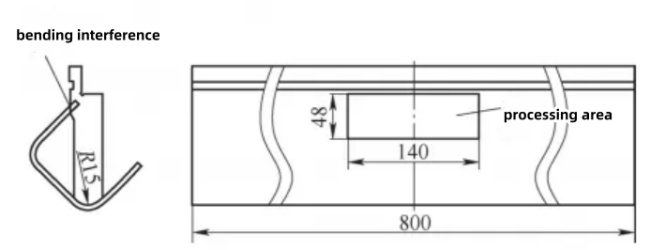
Abbildung 4: Biegeinterferenz, Bestimmung des Bearbeitungsbereichs
Biegeeindrücke
Biegeeindrücke sind ein Phänomen, bei dem beim allmählichen Kontakt des Blechs mit der Innenfläche der V-förmigen Nut der konkaven Form Reibung entsteht, die deutliche Spuren auf der Oberfläche des Blechs hinterlässt. Bei einigen Zubehörteilen mit hohen Oberflächenanforderungen kann das herkömmliche Biegen die Produktqualitätsanforderungen nicht erfüllen, und die Biegeeindrücke (siehe Abbildung 5) können die Anforderungen des nächsten Prozesses nicht erfüllen.
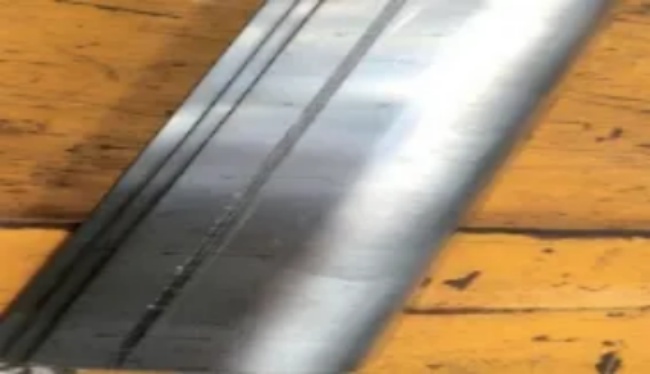
Abbildung 5: Biegeeindruck
Die Biegevertiefung wird hauptsächlich durch die Härte des Blechs und die Struktur der unteren Form beeinflusst. Je höher die Härte des Blechs, desto größer ist seine Widerstandsfähigkeit gegen plastische Verformung, wodurch es für das Material schwieriger wird, sich plastisch zu verformen und es leichter wird, eine Vertiefung zu erzeugen. Die Wahrscheinlichkeit einer Biegevertiefung in häufig verwendeten Blechmaterialien ist: Aluminium > Kohlenstoffstahl > Edelstahl. Je größer die Öffnungsbreite der Biegeform, desto größer ist die Breite der Biegevertiefung und desto geringer ist die Vertiefungstiefe. Je größer die Größe R der unteren Formöffnungsschulter, desto geringer ist die Vertiefungstiefe.
Neben der Verbesserung der Materialhärte und der unteren Formstruktur können auch Gummipolster gegen Eindrücke und untere Biegeformen mit Kugelform verwendet werden, um das Problem von Biegeeindrücken zu lösen. Das Gummipolster gegen Eindrücke beruht hauptsächlich auf physikalischer Isolierung, um das Auftreten von Eindrücken zu reduzieren, wie in Abbildung 6 gezeigt. Die Biegeform mit Kugelform wandelt die für herkömmliche Biegeformen erforderliche Extrusionsreibung in Rollreibung um, wodurch die Reibung verringert und Schäden am Produkt minimiert werden, wie in Abbildung 7 gezeigt.
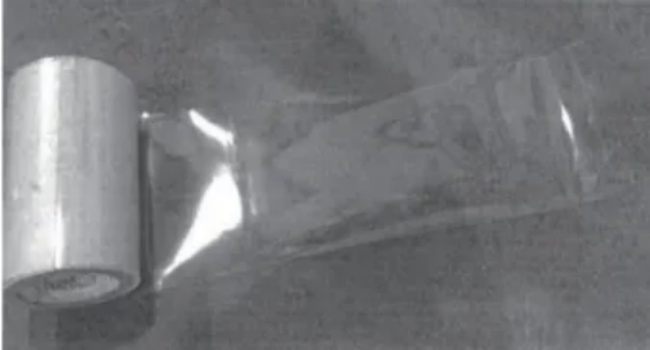
Abbildung 6: Gummipolster gegen Eindrücken
Abbildung 7: Kugelbiege-Unterform
Biegerückfederung
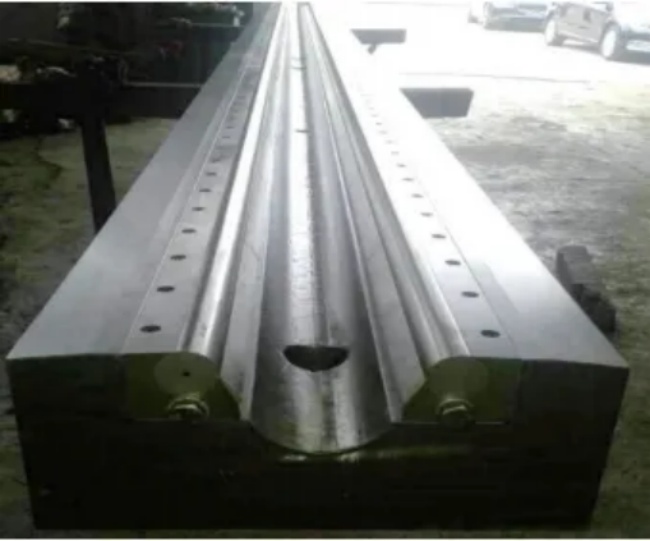
Während des Biegeprozesses werden Materialien gleichzeitig plastisch und elastisch verformt. Wenn das Werkstück die Biegeform verlässt, tritt eine elastische Rückverformung ein, wodurch Form und Größe des gebogenen Teils nicht mehr mit der Belastung übereinstimmen. Dies wird als Biegerückverformung bezeichnet. Biegerückfederung ist einer der Hauptgründe für einen unzureichenden Biegewinkel. Die Hauptfaktoren, die den Rückprall beeinflussen, sind die mechanischen Eigenschaften des Blechs und die Bedingungen der Biegeverformung. Die Größe des Rückfederungswerts ist direkt proportional zur Streckgrenze des Blechs und umgekehrt proportional zum Elastizitätsmodul. Je kleiner der relative Biegeradius (R/t-Verhältnis von Biegeradius zu Blechdicke) des gebogenen Teils ist, desto kleiner ist der Biegerückfederungswert. Die Form des gebogenen Teils beeinflusst auch die Größe des Biegerückfederungswerts. Im Allgemeinen haben U-förmige Teile einen kleineren Rückfederungswert als V-förmige Teile.
Die wichtigste Methode zur Überwindung der Biegerückfederung ist die Winkelkompensationsmethode. Dabei wird im Allgemeinen eine Neigung gleich dem Rückfederungswinkel auf der Biegeform erzeugt, wodurch die Auswirkungen der Biegerückfederung effektiv ausgeglichen werden können. Wie in Abbildung 8 dargestellt, können Werkstücke mit einem Biegewinkel von 90° problemlos gebogen werden, wenn eine Biegeform mit einer Neigung von 80° verwendet wird.
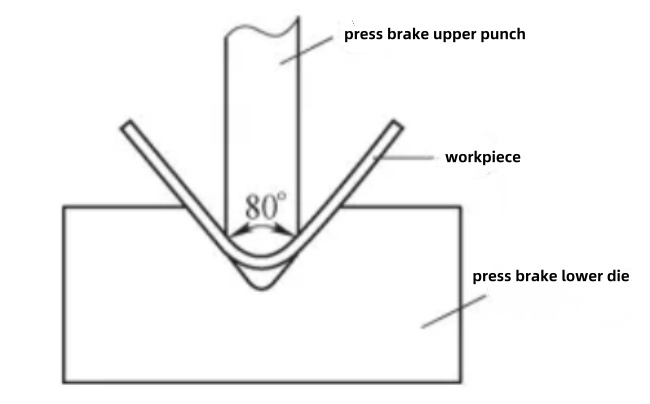
Abbildung 8: Biegerückfederungskompensation
Aufgrund der vielen Faktoren, die die Biegerückfederung beeinflussen, ist es sehr schwierig, den Rückfederungswert genau zu berechnen. Durch Probeformkorrektur und Erfahrungssammlung sind das Beherrschen des Rückfederungsgesetzes, die Anwendung geeigneter Kompensationen und das Ergreifen von Maßnahmen zur Überwindung der Rückfederung in der Formstruktur und anderen Aspekten wirksame Methoden zur Gewährleistung der Produktqualität.
Biegeschlittenmaterial
Unter Biegerutschen versteht man das Phänomen, dass das zu biegende Werkstück keinen vollständigen und wirksamen Auflagepunkt auf der unteren Matrizennut hat. Dies führt dazu, dass das Werkstück zum Verrutschen neigt und die Biegung nicht richtig positioniert werden kann.
Die Hauptgründe für das Verbiegen von Gleitmaterialien sind die folgenden.
- Wenn die Breite der Unterform zu groß ist und die Biegegröße weniger als die Hälfte der Breite der Unterform beträgt, kommt es zum Gleiten.
- Wenn das Werkstück durch seine Form und Größe beeinflusst wird und die Positionierungsgröße der Schablone zu kurz ist oder keine wirksame Schablonenpositionierungskante vorhanden ist, können Biege- und Gleitphänomene auftreten.
Es gibt zwei Hauptmethoden, um das Problem von Biege- und Gleitmaterialien zu lösen.
- Methode 1. Wählen Sie ein geeignetes Biegewerkzeug. Wählen Sie im Allgemeinen eine Werkzeugbreite von 4-6 Mal der Dicke der zu biegenden Platte.
- Methode 2. Durch die Verwendung der Methode zum Hinzufügen von Vorlagen oder Prozesskanten kann das Problem des Materialschlupfes aufgrund einer schlechten Positionierung aufgrund des Biegens gelöst werden. Im Allgemeinen wird das Biegen durch eine gerade Kante des Werkstücks positioniert, was erfordert, dass zwei Endflächen zur Positionierung mit der Biegeschablone in Kontakt stehen. Im tatsächlichen Produktionsprozess gibt es jedoch Situationen, in denen die Kante der Produktschablone zu kurz ist oder keine wirksame Positionierungskante vorhanden ist, was dazu führt, dass die Biegepositionierung nicht abgeschlossen werden kann. Die Lösungen sind:
- Wenn die Plattendicke t ≤ 6 mm ist, fügen Sie zur Positionierung eine Prozesskante hinzu. Die Position der Prozesskante sollte auf gleicher Höhe mit der Endkante des Zubehörs sein. An der Verbindungsstelle sollte Laserschneiden verwendet werden, um das Schleifen und Entfernen nach Abschluss des Biegevorgangs zu erleichtern.
- Wenn die Plattendicke t größer als 6 mm ist, kann zum Positionieren eine Schablone ausgeschnitten werden. Die Schablonendicke kann gleich oder geringfügig kleiner als die Werkstückdicke sein. Beide Positioniermethoden können das Problem des Biegens und Gleitens von Materialien lösen.
Großes Bogenbiegen
Während des Produktions- und Herstellungsprozesses kommt es häufig vor, dass der Biegeradius des Werkstücks groß ist und in der Werkstatt keine passende große Bogenform vorhanden ist. In diesem Fall ist der Produktionszyklus von Integralformformen oder großen Bogenformen länger und die Kosten sind zu hoch, während die Verwendung der Mehrdurchgang-Biegeformtechnologie für kleine Bögen kostengünstiger und breiter anwendbar ist. Im Projekt Super Bus 2.0 gibt es beispielsweise eine Komponente mit einer vertikalen Platte und drei vertikalen Platten mit einem Biegeradius von 125 mm und einem Biegewinkel von 90 °, wie in Abbildung 9 dargestellt. Da in der Werkstatt keine entsprechenden Biegeformen vorhanden sind, können mehrere Biegeverfahren verwendet werden. Zunächst wurde eine 3D-Software verwendet, um das Layout und die Biegung an der Position R125 mm zu modellieren. Nach der Modellierung entfaltete die Software automatisch das 2D-Flachplattendiagramm. Durch Eingabe eines Biegeradius von 45 mm in die Software und Vergleich mehrerer Dateneingaben wurde bestätigt, dass das Kreisbogensegment durch Biegen mit 8 Schnitten gewährleistet werden konnte. Anschließend wurden die Biegedaten (Biegewinkel, Länge der Biegelinienposition) für jeden Schnitt generiert, wie in Abbildung 10 dargestellt. Abschließend wurde auf Grundlage der Biegedaten vor Ort ein Probebiegen durchgeführt, wie in Abbildung 11 dargestellt.
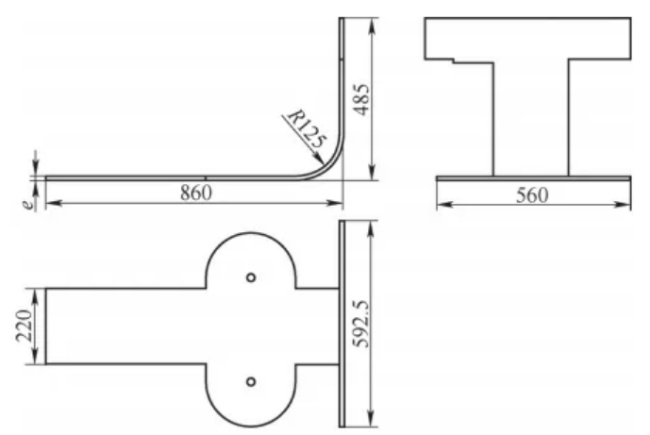
Abbildung 9: Bogenförmige Werkstücke
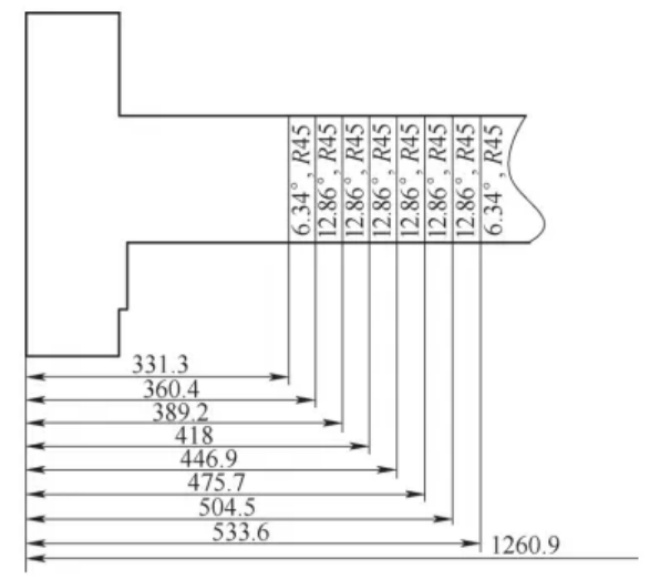
Abbildung 10: Abwicklungsdiagramm und Biegelinienposition

Abbildung 11: Probebiegen der Form vor Ort
Biegevorsprung
Biegevorsprung bezieht sich auf das Phänomen, bei dem das Metallmaterial aufgrund von Materialkompression auf beiden Seiten der gebogenen Ecke des Blechs hervorsteht, was zu einer Breite führt, die größer als die ursprüngliche Größe ist. Die Größe des Biegevorsprungs hängt im Allgemeinen von der Dicke der Zubehörplatte und dem Biegeradius ab. Je dicker die Platte, desto kleiner der Biegeradius und desto deutlicher der Vorsprung.
Um dieses Biegequalitätsproblem zu vermeiden, können beim Zeichnen des Biegeentfaltungsdiagramms auf beiden Seiten der Biegelinie Prozesskerben hinzugefügt werden, wie in Abbildung 12 dargestellt. Der Prozessspalt hat im Allgemeinen die Form eines Kreisbogens mit einem Durchmesser von mindestens dem 1,5-fachen der Dicke des Werkstücks, um den Biegevorsprung auszugleichen und das Problem des Biegevorsprungs effektiv zu lösen. Bei Werkstücken, die bereits Biegevorsprünge aufweisen, wird im Allgemeinen manuelles Polieren zur Bearbeitung verwendet.
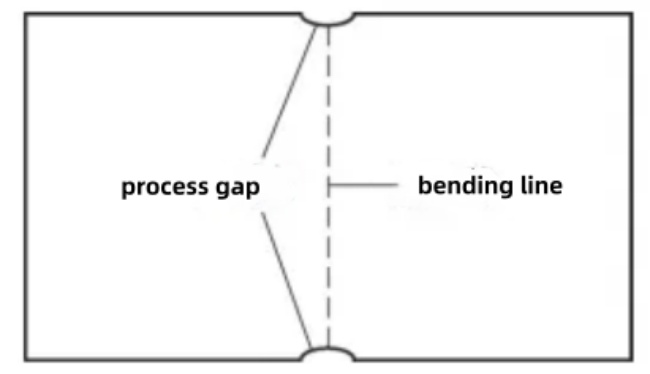
Abbildung 12: Prozesslücke
Abschluss
Es ist zu beachten, dass bei den oben aufgeführten häufigen Biege- und Schnittqualitätsproblemen in der Produktionspraxis die Auswirkungen menschlicher oder gerätebezogener Faktoren (wie falsche Entfaltungsmaße, falsche Auswahl der Biegeparameter und Alterung der Geräte) nicht berücksichtigt wurden. In der Produktionspraxis sollten geeignete Biegeprozessparameter basierend auf der Geräteleistung, der Produktgröße und den Materialeigenschaften ausgewählt und strikt gemäß den Betriebsspezifikationen ausgeführt werden. Wir müssen nicht nur die Auswirkungen verschiedener Faktoren wie Projektfortschritt, Kosten und Qualität umfassend berücksichtigen und geeignete Methoden zur Lösung von Biegequalitätsproblemen anwenden, sondern auch Erfahrungen sammeln, um das Auftreten und die Auswirkungen von Biegeproblemen in der Prozessanalysephase vorherzusagen und gezielte Maßnahmen zu ihrer Vermeidung zu ergreifen. Dieser Artikel listet mehrere häufige Biegequalitätsprobleme und ihre Lösungen auf und hofft, Branchenkollegen einige Referenzen und Anleitungen zu bieten.