Table of Contents
Sheet metal bending (sometimes referred to as sheet metal flanging) is one of the most important and widely used techniques in sheet metal manufacturing.
Sheet metal bending allows manufacturers to turn a straight sheet metal part into an angled component, which is more cost-effective than welding or fixing two separate parts together.
Sheet metal bending typically works by applying force to the sheet metal in a way that causes permanent deformation. However, there are many different bending methods and bending machines that can be used to achieve the best results.
This article serves as an introduction to sheet metal bending, introducing the basic knowledge of bending, typical bending equipment, types of sheet metal bending, and technical precautions such as bending allowance and rebound.
What Is Sheet Metal Bending?
Sheet metal bending is a metal processing technique used to transform flat sheet metal parts into V-shaped, U-shaped, or grooved shapes.
This is an important and convenient manufacturing process because bending a flat metal plate into a new shape is much cheaper than processing V, U, or channel shapes from solid workpieces or casting them in a foundry. In addition, the parts produced by bending are more robust than those made by welding two flat metal sheets into a V-shape.
Many types of sheet metal bending involve the use of machines called brakes, sometimes referred to as bending machines or sheet metal folding machines. Force can be applied manually or using hydraulic devices.
Sheet Metal Bending Methods
There are several sheet metal bending methods, all of which are similar in function but differ in operation. Therefore, knowing the ideal method to choose is the first step you need to take to succeed with your sheet metal forming project.There are several sheet metal bending methods, all of which are similar in function but differ in operation. Therefore, knowing the ideal method to choose is the first step you need to take to succeed with your sheet metal forming project.
V Bending
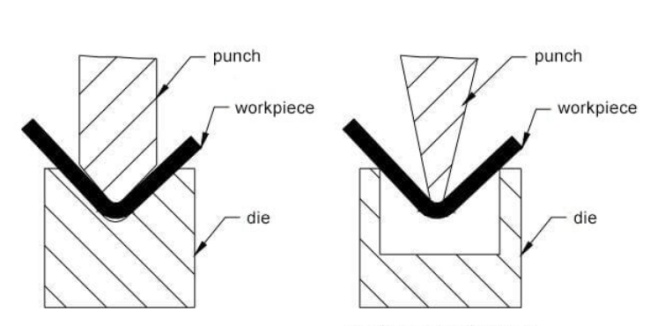
V-bending is the most common sheet metal bending method. V-shaped punch and die used in the process. The v-shaped punch forces the sheet metal workpiece into the “v-shaped” groove in the die, forming sheet metals with different bend angles. Operators can achieve acute, obtuse, or 90° bend angles, depending on the v-shaped punch and die angle.
Air Bending
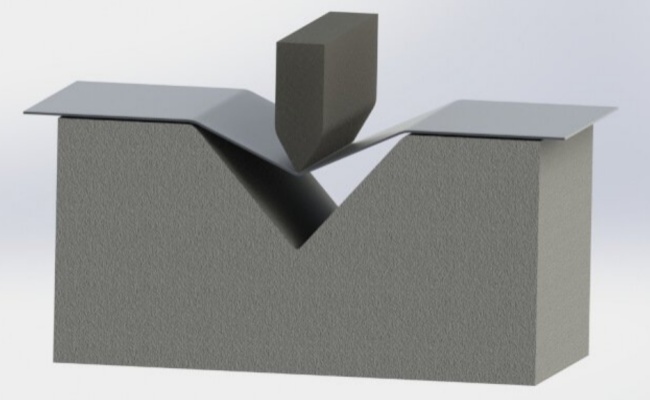
Air bending is quite similar to the V-bending method: it relies on v-shaped punch and die to bend sheet metals. This method is not as accurate as other methods, but it is very flexible: it can be used to create bends in V, U, and other shapes. However, unlike the conventional v-bending process, the punch in the air bending method does not force the sheet into the bottom of the cavity. Instead, it leaves space (or air) underneath the sheet, allowing more bend angle control than conventional v-bending.
Bottom Bending

Bottoming (or bottom bending) is a type of v-bending that also solves the springback challenge. It involves deforming the sheet metal in the bend region by applying additional force through the tip of the punch after completion of bending. During the bottoming process, the punch completely presses the metal plate into the mold, forming a bend that corresponds to the geometric shape inside the mold.
Like the air bending method, bottoming offers a precise bend angle control. However, air bending requires a higher press force than bottom bending needed.
Edge Bending
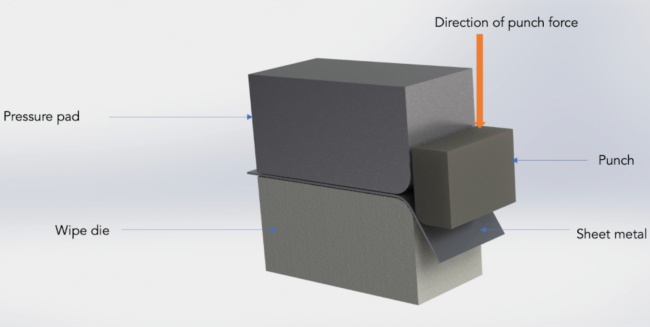
This method is used in panel bender and involves the use of upper and lower molds that move up and down for bending. It is usually used for shorter metal sheets to reduce sharpness and prevent damage to the bending edge.
In the edge bending method, the sheet metal is held against a die by a pressure pad. The punch then forces against the edge of the sheet that extends beyond the die and pressure pad, causing it to bend over the end of the die.
This method offers a good mechanical advantageㅡwhich means it allows you to apply less force to create desired bends (and bend angles).
Roll Bending
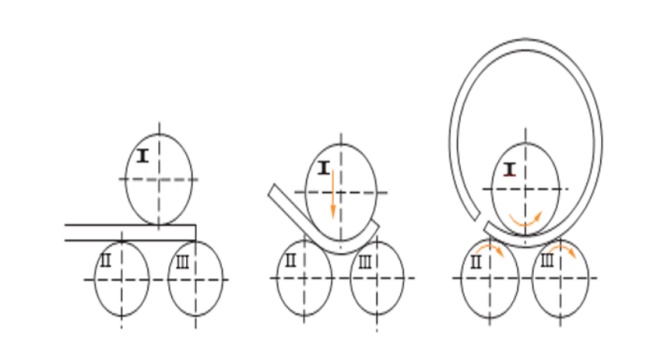
The roll bending method allows you to bend sheet metals into rolls, tubes, cones, or curved shapes. This unique sheet metal forming process uses sets of rollers that feed (and bend) the metal stock to the desired curvature.
This process is used for bending workpieces with large curls and involves the use of three rolls driven by a hydraulic system to bend the sheet.
Roll bending method can be processing by the 4 rollers plate bending machine or 3 rollers plate bending machine.
Rotary Bending
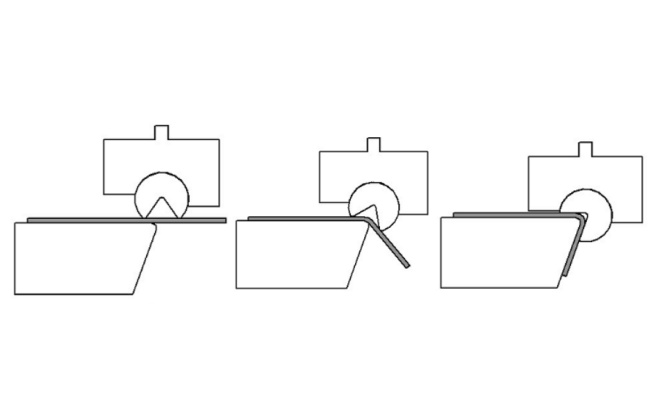
Rotary bending can bend sheet metal with a degree of more than 90. The final profile is similar to a V-bend, but the profile surface is smoother. In rotary bending, the sheet metal is clamped to a rotating die and drawn around the die to form a geometry that radius matches the desired bend radius. This method often adopts an internal supporting mandrel to prevent wrinkling on the wall of the bent sheet metal.
Sheet Metal Bending Machines
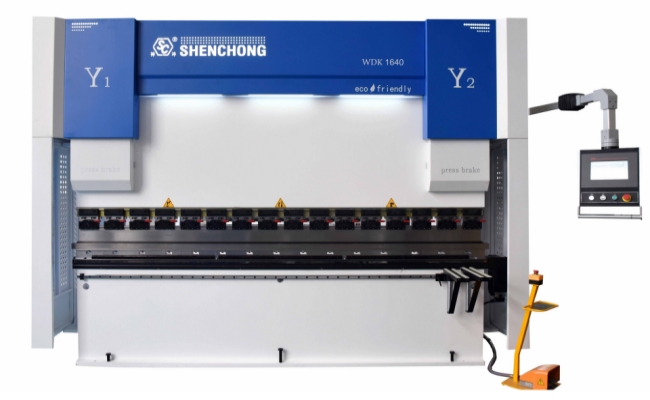
Hydraulic press brake machine is one of the most important equipment for bending and forming workpieces in the sheet metal industry. Its function is to bend steel plates into various shapes of parts according to process requirements.
Press brake machien is a type of plate bending machine that uses a moving upper punch and corresponding lower die. During bending process, the metal plate is placed on the lower die and the punch is forcibly moved into the metal, forcing it into the lower die notch. According to the shape of the lower die, a press brake can be used to produce V-shaped bends, U-shaped bends, and other shapes. The hydraulic press brake can meet the needs of various workpieces by replacing the press brake tooling.
Hydraulic bending brake machines can be divided into torsional axis synchronization and electro-hydraulic synchronization according to synchronization methods. The most high-end press brake currently on the market is the servo hybrid press brake.
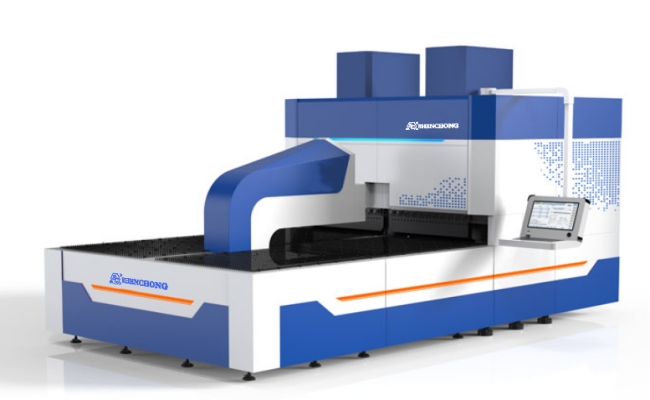
Panel bender is a machine used in manufacturing and processing industries to bend or shape metal plates into specific shapes. The working principle is usually to clamp and position the metal plate, and then use a mechanical or hydraulic system to bend the metal along a predetermined axis. Bending centers play a crucial role in industries that require accurate and efficient shaping of metal sheet shapes, reducing the need for manual labor and improving the overall quality of finished products.
Panel bender can automatically create multiple bends for each side, including up/down bends, flat or curved bends. The intelligent flexible panel bending center servo system adopts a pure electric servo fully closed-loop system, which can support 16 axis concurrent linkage at the upper limit of the system. In actual use, 9 axes (11 axes) are used, which means that 9 axes (11 axes) are concurrent linkage in practical sense. The bending action is smooth, and the mechanical operation coordination is high. It can successfully complete various complex action combinations, and the overall work efficiency of the machine is very high.
The intelligent flexible panel bender adopts a universal bending mold, which achieves bending of various shapes through multi axis parallel linkage and full servo control, and can bend various complex shapes. Complex shapes that can be folded into various combinations such as right angles, non right angles, arcs, top folds, and bottom folds.
The panel bender focuses on solving various complex bending problems for thin plates. It can be widely used in the field of steel cabinet shell (file cabinet, tool cabinet, outer cover, electrical cabinet, communication cabinet, gas cabinet, water meter cabinet, etc.), kitchenware field (refrigerator, air conditioner, stove, etc.), furniture, ventilation, refrigeration, purification, door industry, decoration, elevator and other related metal forming fields, suitable for bending different types of workpieces.
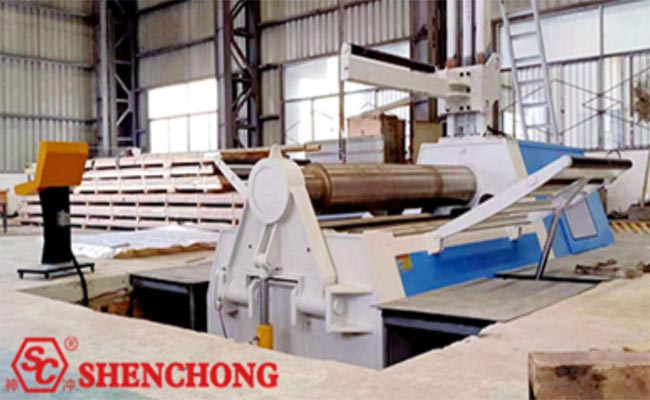
A plate rolling machine is a device that uses work rolls to bend and shape sheet metal, and can form different shapes of parts such as cylindrical and conical parts. It is a very important processing equipment. The working principle of a plate bending machine is to use external forces such as hydraulic pressure and mechanical force to move the working rollers, thereby bending or forming the sheet metal. Based on the rotational motion and positional changes of work rolls of different shapes, elliptical, arc-shaped, cylindrical and other parts can be processed.
The types of rolling machines vary depending on the field of use. Divided by the number of rolls, it is divided into three roll plate rolling machine and four roll plate rolling machine. The three roll rolling machine is divided into symmetrical three roll rolling machine, horizontal downward adjustment three stick rolling machine, curved downward adjustment rolling machine, upper roll universal three roll rolling machine, and hydraulic CNC rolling machine. From the perspective of transmission, it can be divided into mechanical and hydraulic types.
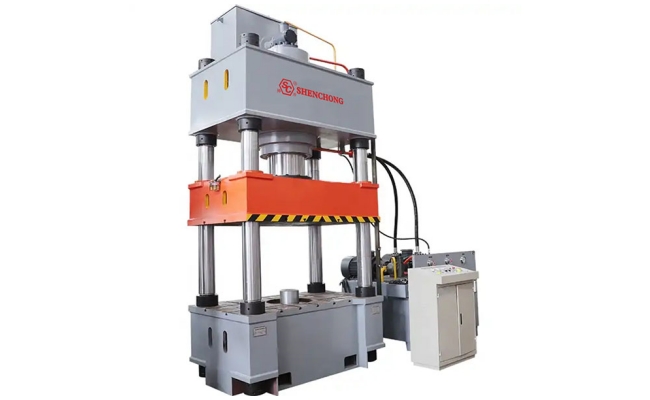
A press machine refers to a molding machine used for industrial products to be formed by pressure, generally using hydraulic cylinders, hence also known as hydraulic presses. The press is the main equipment for compression molding and sheet metal forming, which is divided into frame structure and column structure according to the frame structure form. According to the position of the pressure main oil cylinder, the press can be divided into upward and downward pressure types. For pressing large plastic laminates, a downward pressure press with the oil cylinder at the bottom can be used, while an upward pressure press is often used for pressing general plastic parts. According to the type of working fluid, it can also be divided into hydraulic presses driven by hydraulic oil and hydraulic presses driven by oil-water emulsions.
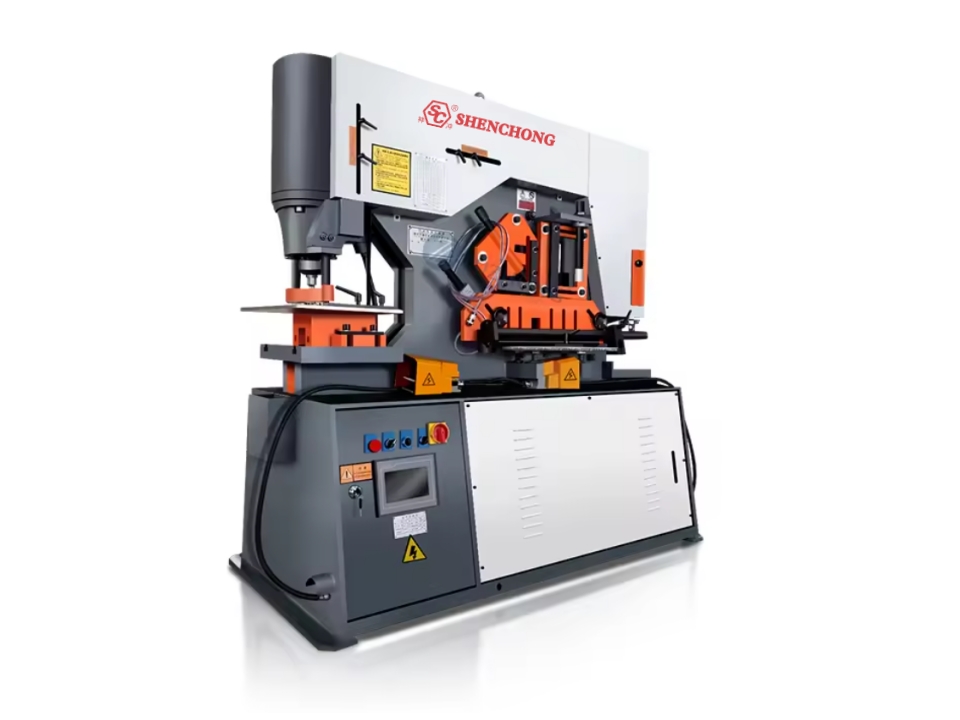
ironworker machine is a machine tool equipment that integrates multiple functions such as metal cutting, punching, shearing, bending, etc. It has the advantages of easy operation, low energy consumption, and low maintenance cost. It is the preferred equipment for metal processing in modern manufacturing industries (such as metallurgy, bridges, communication, power, military, etc.). ironworkers are divided into two types: hydraulic ironworker machine and mechanical ironworker machine.
Challenges During Sheet Metal Bending
Springback
When sheet metal is bent into a new shape, it will naturally springback to a certain extent after removing the bending force. This is called ‘springback’.
Due to the compressive strength of bent metal plates, springback may occur. During sheet metal bending, one side is subjected to tension, while the other side is subjected to compression. However, due to the higher compressive strength than tensile strength of the material, the compressed side successfully resists deformation and self decompresses upon removal of force.
Springback is not the main issue, but it means that manufacturers must compensate for the expected rebound by excessively bending the metal plate. If the metal intentionally bends slightly excessively, a small amount of natural rebound will result in the correct angle.
Of course, calculating springback is far from simple, and there are several variables that can affect the severity of sheet metal springback, including the type and specifications of the material. In addition, a larger inner radius will result in greater springback.
The springback of a metal plate is proportional to the material’s yield strength and inversely proportional to its elastic modulus. Low-carbon steel has less springback and is ideal for high-precision workpieces, while high-carbon steel and stainless steel have significant springback. The larger the bending radius, the greater the springback. Smaller bending radii result in higher accuracy.
Bending Allowance
When bend a metal plate, the outer side of the plate will be elongated, resulting in a change in its length. This means, for example, that the total length of the two sides bent in a V-shape will be longer than the original length of the sheet plate.
So, if the size changes, how can we accurately design a part to ensure it fits with other components? How do we determine how long a metal sheet must be? To compensate for the size variation, we must consider the bending allowance: the difference between the length of the unbent plate and the sum of the lengths of each side of the finished bent plate.
The calculation of bending allowance will consider factors such as sheet metal thickness, bending radius, and bending angle. The bending coefficient calculator can be used to calculate the required bending coefficient for sheet metal parts.
Best Material And Gauge For Sheet Metal Bending
Some sheet metal materials are more suitable for bending than others. Generally speaking, the best bending material is ductile rather than brittle.
The commonly used materials for sheet metal bending include:
- Low carbon steel: can be bent at any temperature.
- Spring steel: can bend after annealing.
- Alloy steel 4140: bendable after annealing.
- Aluminum 5052: Compared with other aluminum alloys, it has a high degree of bendability.
- Copper: Highly bendable.
Materials that are more difficult to bend (although not impossible) include aluminum 6061, titanium, brass, and bronze.
Conclusion
This article introduces the basic knowledge about sheet metal bending. Sheet metal bending can be achieved using various machines, including press brakes, hydraulic press, panel bender and ironworkers. SC Machinery is a leading sheet metal forming services provider across Asia. We offer high-quality bending services to companies serving a broad range of industries.