Table of Contents
Introduction
Metal profile bending machines are indispensable tools in the metalworking and manufacturing industries. These machines are designed to bend and shape metal profiles into various forms, catering to a wide range of applications in construction, automotive, aerospace, shipbuilding, and other sectors. This article delves deep into the intricacies of profile bending machines, covering their types, components, working principles, applications, advantages, and considerations for choosing the right machine.
What Is A Profile Bending Machine?
A profile bending machine, also known as a section bender or roll bender, is a mechanical device used to bend various types of metal profiles, such as angles, channels, I-beams, H-beams, tubes, and pipes, into desired shapes. These machines apply force through a set of rolls or dies, gradually deforming the metal profile to achieve the required curvature or angle.
Metal Profile Bending Machines Working Principle
The profile bending machine is a linear down-adjustment type profile bending machine. The two side rolls of the machine are the main driving rolls, and the three working rolls are the main driving rolls. The position of the upper roll is fixed, and the lower roll clamps the workpiece upwards to prevent deformation of the section. One side roller corresponds to the upper roller to do linear lifting movement, hydraulic control, and displacement digital display, which is beneficial to control the profile forming process, and there are CNC idlers and twist correction devices on both sides, which is conducive to ensuring the rolling quality of asymmetric cross-section profiles and forming double surface workpiece.
Applications Of Profile Bending Machines
Profile bending machines are versatile tools used in a wide range of industries. Some of the common applications include:
Construction:
- Bending steel beams and columns for structural frameworks.
- Creating curved metal components for architectural designs.
- Fabricating railings, staircases, and decorative elements.
Automotive:
- Shaping exhaust pipes and roll cages.
- Forming chassis components and suspension parts.
- Manufacturing custom metal parts for vehicle modifications.
Aerospace:
- Bending lightweight metal profiles for aircraft frames.
- Fabricating components for spacecraft and satellites.
- Producing aerodynamic shapes for aerospace applications.
Shipbuilding:
- Bending steel plates and beams for hull construction.
- Forming structural elements for ship superstructures.
- Creating custom metal parts for marine applications.
Manufacturing:
- Producing metal frames and enclosures for machinery.
- Fabricating conveyor systems and material handling equipment.
- Manufacturing components for industrial equipment and tools.
Types Of Profile Bending Machines
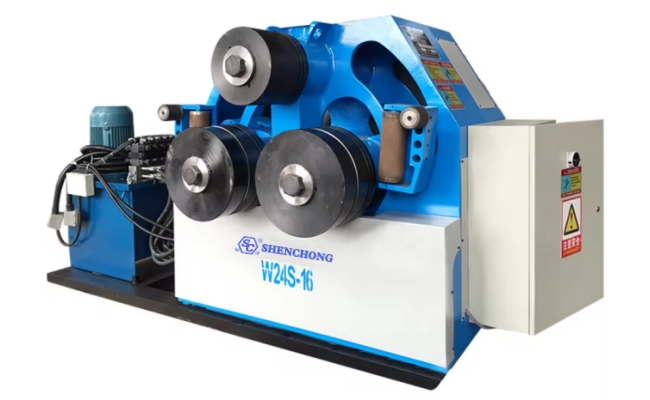
Metal profile bending machines come in several types, each designed for specific applications and materials. The main types include:
Manual Profile Bending Machines
- Suitable for light-duty bending tasks.
- Operated by hand, using a lever or crank to apply force.
- Ideal for small workshops and hobbyists.
Hydraulic Profile Bending Machines
- Use hydraulic power to apply force, offering greater bending capacity.
- Suitable for medium to heavy-duty applications.
- Provide precise control over the bending process.
CNC Profile Bending Machines
- Equipped with Computer Numerical Control (CNC) systems for automated and highly accurate bending.
- Suitable for complex and repetitive bending tasks.
- Widely used in industrial applications requiring high precision.
Electric Profile Bending Machines
- Utilize electric motors to drive the rolls or dies.
- Offer a balance between manual and hydraulic machines in terms of power and precision.
- Commonly used in small to medium-scale operations.
Horizontal Profile Bending Machine Or Vertical Profile Bending Machine
Horizontal and vertical type profile bending machines are specialized equipment used for bending various metal profiles into desired shapes. Here’s a detailed look at each type.
Horizontal Type Profile Bending Machine
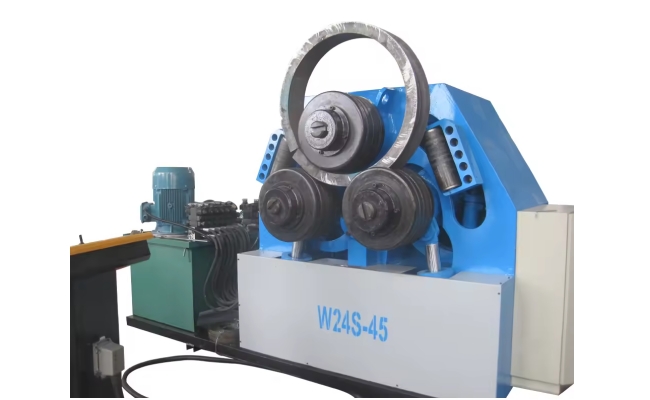
Description:
- The machine is oriented horizontally, with the bending process occurring on a horizontal plane.
- It is commonly used for bending larger and heavier profiles due to its stable and robust structure.
Advantages:
- Easier handling of long and heavy profiles.
- Typically offers better control and precision for large-scale projects.
- Allows for bending of a wide range of profile sizes and shapes.
Applications:
- Construction and building industries for bending beams, pipes, and other structural elements.
- Automotive and shipbuilding industries for creating frame and body components.
- Manufacturing of metal furniture and various metal products.
Vertical Type Profile Bending Machine
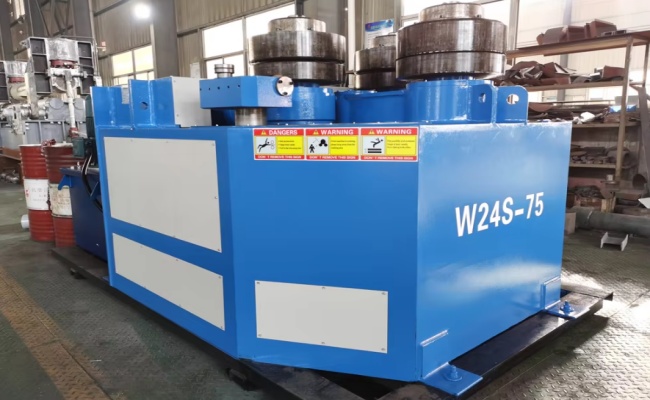
Description:
- The machine is oriented vertically, with the bending process occurring on a vertical plane.
- It is often used for smaller and lighter profiles and can be more compact in design.
Advantages:
- Saves floor space due to its vertical orientation.
- Easier to operate for smaller and more delicate profiles.
- Suitable for high precision bending in smaller scale operations.
Applications:
- Metal fabrication shops for bending smaller profiles like rods, bars, and tubes.
- Artistic metalworking for creating decorative elements and components.
- Aerospace and automotive industries for smaller structural parts.
Key Differences
- Orientation:Horizontal machines lay flat, while vertical machines stand upright.
- Profile Size and Weight Handling:Horizontal machines are better for larger and heavier profiles, whereas vertical machines are suitable for smaller, lighter profiles.
- Space Requirements:Vertical machines occupy less floor space compared to horizontal machines.
- Application Focus:Horizontal machines are often used in large-scale industrial projects, while vertical machines are used in smaller, precision-focused tasks.
These machines play a crucial role in industries requiring precise and consistent bending of metal profiles to create various products and structural components.
Advantages Of Profile Bending Machines
Metal profile bending machines offer several advantages that make them essential in modern manufacturing and construction:
Versatility
- Capable of bending a wide range of metal profiles and materials.
- Suitable for various industries and applications.
Precision and Accuracy
- Advanced machines, especially CNC models, provide highly accurate and repeatable bends.
- Ensures consistent quality in mass production.
Efficiency
- Automated and hydraulic systems enable fast and efficient bending processes.
- Reduces manual labor and increases productivity.
Cost-Effectiveness
- Reduces the need for welding and assembly of multiple parts.
- Minimizes material waste by achieving precise bends with minimal errors.
Customizability
- Allows for the creation of custom shapes and designs.
- Enables the production of complex and unique components.
Key Components Of Metal Profile Bending Machines
Understanding the components of a profile bending machine is crucial for grasping its operation and capabilities. The main components include:
Frame
- The sturdy base that supports the entire machine.
- Typically made of heavy-duty steel to withstand high bending forces.
Rolls/Dies
- The tools that make contact with the metal profile and apply the bending force.
- Available in various shapes and sizes to accommodate different profiles.
- Can be arranged in different configurations (e.g., three-roll, four-roll) depending on the machine type.
Hydraulic/Electric System
- Powers the movement of the rolls or dies.
- Hydraulic systems use fluid pressure, while electric systems use motor-driven mechanisms.
Control Panel
- The interface through which the operator controls the machine.
- Includes buttons, switches, and digital displays for adjusting settings and monitoring the bending process.
Support And Guide Systems
- Additional components that provide stability and guidance to the metal profile during bending.
- Ensure accurate and consistent bending results.
How To Use Profile Bending Machines?
The operation of a pipe and tube profile bending machine involves several key steps, regardless of the specific type of machine. Here’s a general overview of the working process:
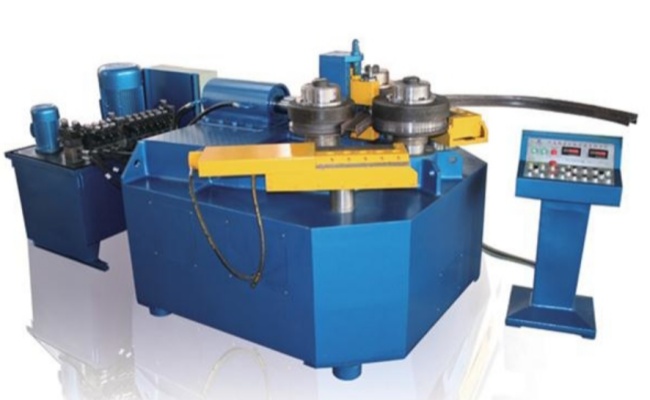
Setup
- The metal profile to be bent is placed on the machine, typically between the rolls or dies.
- The operator sets the desired bending parameters, such as the bending radius, angle, and speed.
Bending Process
- The machine applies force through the rolls or dies, gradually bending the metal profile.
- The profile is fed through the machine, with the rolls or dies exerting pressure to achieve the desired curvature.
- For complex shapes, multiple passes or adjustments may be required.
Monitoring and Adjustments
- The operator continuously monitors the bending process to ensure accuracy.
- Adjustments can be made to the machine settings as needed to achieve the precise bend.
Completion
- Once the desired shape is achieved, the machine is stopped, and the bent profile is removed.
- The final product is inspected for quality and accuracy.
Types Of Bending Operations
- Cold Bending: Performed at room temperature, suitable for most metals. It maintains the material’s properties and is energy-efficient.
- Hot Bending: Involves heating the metal profile before bending. It is used for materials that are difficult to bend cold or for achieving tighter radii without cracking.
Maintenance And Safety Considerations
Proper maintenance and safety practices are crucial for the optimal performance and longevity of profile bending machines. Here are some key maintenance and safety considerations:
Regular Inspections
- Conduct routine inspections of the machine components, including rolls, dies, hydraulic/electric systems, and control panels.
- Check for wear and tear, and replace any damaged parts promptly.
Lubrication
- Ensure all moving parts are adequately lubricated to reduce friction and prevent wear.
- Follow the manufacturer’s recommendations for lubrication intervals and types of lubricants.
Cleaning
- Keep the machine clean and free from debris, dust, and metal shavings.
- Regularly clean the rolls and dies to maintain bending accuracy.
Calibration
- Periodically calibrate the machine to ensure accurate bending angles and radii.
- Follow the manufacturer’s guidelines for calibration procedures.
Safety Measures
- Provide proper training to operators on the safe use of the machine.
- Implement safety protocols, such as wearing protective gear, using safety guards, and following emergency procedures.
Documentation
- Maintain detailed records of maintenance activities, repairs, and inspections.
- Keep track of machine settings and parameters for consistent performance.
Considerations For Choosing A Profile Bending Machine
Selecting the right metal profile bending machines depends on several factors. Here are some key considerations to keep in mind:
Material Type and Thickness
- Determine the types of metal profiles you will be bending and their thickness.
- Choose a machine with sufficient capacity to handle the materials.
Bending Radius and Angle
- Consider the required bending radius and angles for your applications.
- Ensure the machine can achieve the desired bends accurately.
Production Volume
- Assess the volume of production and the frequency of bending tasks.
- Choose a machine that can handle the workload efficiently.
Automation and Control
- Decide whether you need a manual, hydraulic, electric, or CNC machine.
- Consider the level of automation and control required for your operations.
Budget and Maintenance
- Evaluate your budget for purchasing and maintaining the machine.
- Consider the long-term costs and benefits of different machine types.
Space and Installation
- Assess the available space in your workshop or facility.
- Ensure the machine can be installed and operated safely within the given space.
Future Trends In Profile Bending Technology
The field of profile bending technology continues to evolve, driven by advancements in automation, materials science, and manufacturing techniques. Here are some future trends to watch:
Integration with Industry 4.0
- Incorporation of smart sensors and IoT (Internet of Things) technology for real-time monitoring and predictive maintenance.
- Enhanced data analytics for optimizing bending processes and improving efficiency.
Advanced Materials
- Development of new materials with improved strength-to-weight ratios and bendability.
- Machines capable of handling advanced materials, such as composites and high-strength alloys.
Enhanced Automation
- Increased use of robotics and automated handling systems for loading and unloading profiles.
- Greater integration of CNC systems with artificial intelligence for adaptive bending processes.
Sustainability
- Focus on energy-efficient machines and eco-friendly manufacturing practices.
- Adoption of green technologies to reduce the environmental impact of metal bending operations.
Customization and Flexibility
- Machines designed for quick changeovers and adaptability to different bending tasks.
- Customizable machines to meet specific industry requirements and applications.
Conclusion
Metal profile bending machines are vital tools in the metalworking industry, offering versatility, precision, and efficiency in shaping metal profiles for various applications. Understanding the types, components, working principles, and applications of these machines is essential for selecting the right equipment and optimizing bending processes. As technology continues to advance, profile bending machines will become even more sophisticated, driving innovation and productivity in metalworking and manufacturing.
Whether you are involved in construction, automotive, aerospace, shipbuilding, or any other industry requiring precise metal bending, investing in a suitable profile bending machine can significantly enhance your capabilities and contribute to the success of your projects. By considering factors such as material type, bending requirements, automation, and maintenance, you can make informed decisions and achieve the best results in your metal bending operations.
SC Machinery is a professional bending machine manufacturer, we offer clients hydraulic press brake, plate rolling machine and tube and pipe profile bending machine for over 25 years. Please feel free to contact with us for more machine information.