Table of Contents
CNC press brake machine is a high-precision mechanical equipment used for bending, forming and other processing operations on metal sheets. Its operation requires certain skills and experience. This machine may seem complex and powerful, but in fact, as long as you master the correct operating methods, you can easily control it. This article aims to provide you comprehensive CNC press brake operation guide, helping you quickly get started and improve work efficiency.
CNC Press Brake Operation General Introduction
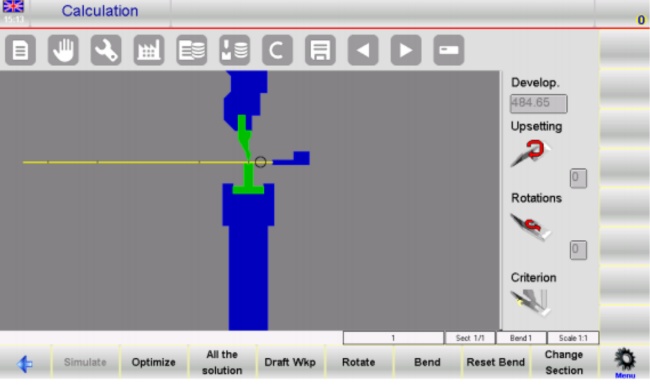
CNC press brake operation method mainly includes the following steps.
- Preparation for startup: Before starting the operation, first clarify your bending target, including the thickness, material, and bending angle of the sheet that needs to be bent. These pieces of information will determine how you set the parameters of the CNC bending brake Check the equipment performance, program, and mold settings of the machine to ensure that it is in good condition. Start the main power supply of the machine tool, activate the hydraulic motor, and perform the machine tool zeroing operation.
- Mold setting and programming: Select appropriate upper and lower molds based on the length, plate thickness, and bending pressure gauge of the workpiece, and ensure that the bending pressure is less than the pressure resistance of the mold. Program on the CNC controlled LCD panel, considering direct programming mode or angle programming mode, to avoid interference between the workpiece, upper and lower molds, and the gauge. Be sure to ensure accurate parameter settings to avoid affecting the bending effect.
- Adjustment and preparation: Adjust the stroke of the hydraulic press brakemachine to ensure that there is a gap of plate thickness when the upper mold descends to the bottom, avoiding damage to the mold and machine. Choose the appropriate slot width and adjust the blocking material after adjustment.
- Start bending: Press the foot switch to start bending, which can be released at any time, and the bending machine will stop. Continue to press the switch to bend when needed.
- Programming and running: Use the control system to write bending programs, input parameters such as bending angle and starting position. Load the written program into the control system of the CNC press brakemachine, select automatic mode to run, and the machine will automatically complete the bending operation according to the set parameters and steps.
- Check and complete the work: After completing the bending, check whether the size, angle, and shape of the workpiece meet the requirements. Make necessary adjustments and fine-tuning to ensure the quality of the workpiece. Clean up the work area, record operational parameters and programs.
By following the above steps, the hydraulic bending brake machine can be effectively operated to bend various metal sheets.
Operation Precautions
During the CNC press brake operation, operators need to pay attention to safety and avoid accidents.
When performing bending operations, attention should be paid to controlling the bending force and speed to avoid problems such as breakage and deformation.
When adjusting the mold, attention should be paid to ensuring the parallelism and gap between the upper and lower molds to ensure the quality and accuracy of the bending.
During the operation, it is important to observe the running status of the machine and the bending of the board, and make timely adjustments and controls.
After completing the operation, cleaning and maintenance work should be carried out to ensure the normal operation of the machine.
Press Brake Machine Maintenance
Before performing machine maintenance or cleaning, the upper punch should be aligned with the lower dies and the machine should be lowered and turned off until the work is completed. If startup or other operations are required, the mode should be selected as manual and safety should be ensured. The maintenance content is as follows:
Hydraulic Oil Circuit
- Check the oil level in the fuel tank every week, and also check it after hydraulic system maintenance. If the oil level is below the oil window, add hydraulic oil.
- The hydraulic oil used in this machine is ISO HM46 or MOBIL DTE25.
- The new machine should have its oil changed after 2000 hours of operation, and every 4000-6000 hours of operation thereafter. After each oil change, the oil tank should be cleaned.
- The system oil temperature should be between 35 ℃ and 60 ℃, and should not exceed 70 ℃. If it is too high, it may cause deterioration and damage to the oil quality and accessories.
Filter
- The filter should be replaced or thoroughly cleaned every time the oil is changed.
- If the machine tool has related alarms or other filter abnormalities such as poor oil quality, it should be replaced.
- The air filter on the fuel tank should be inspected and cleaned every 3 months, preferably replaced every year.
Hydraulic Components
- Clean hydraulic components (substrates, valves, motors, pumps, oil pipes, etc.) monthly to prevent dirt from entering the system and avoid using cleaning agents.
- After using the new press brake machine for one month, check whether there is any deformation at the bent parts of the oil pipes. If there is any abnormality, they should be replaced. After two months of use, tighten all the connections of the accessories and turn off the machine when doing this work.
Selection And Debugging Of Press Brake Tools
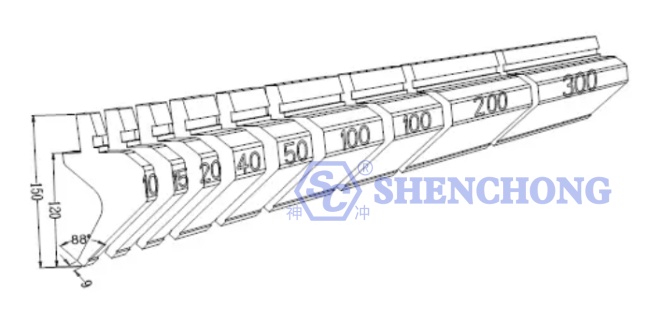
Upper Punch
The press brake upper punch, also known as the folding knife, is divided into two types: integral and segmented. The length of the integral upper mold is 415mm and 835mm, respectively.
Split length: 10, 15, 20, 40, 50, 100 (left ear), 100 (right ear), 200, 300 (mm). The segmentation module can be used to combine bending lengths of different lengths The upper mold is divided into four types: straight upper punch, curved upper punch, curved upper punch, and special upper punch.
Types And Processing Characteristics Of Straight Upper Punch
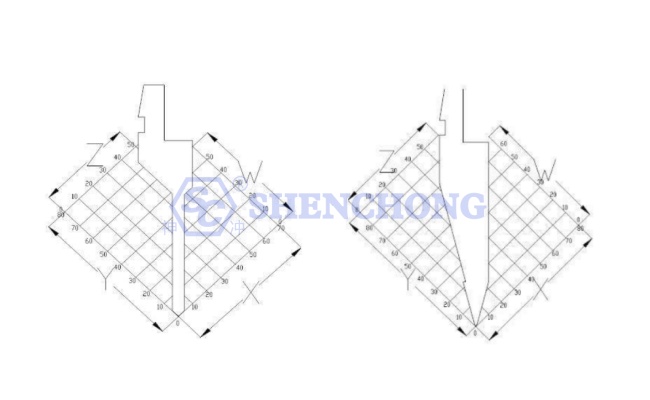
Straight upper punch is suitable for bending symmetrical products, both front and rear directions can be avoided, and the tool thickness is 6MM, so the bending opening can be as small as 6mm.
Tool analysis: From the simulation diagram of tool bending, it can be seen that the tool can be avoided in both front and back positions, but the length of Z and W is smaller than that of X and Y. The tool tip angle of this type of tool is 88 degrees, and the tool tip R angle is 0.2. In addition, tools with a tool tip angle of 30 degrees and 45 degrees are commonly used The angle of the cutting edge is 30 degrees, and the R-angle of the cutting edge is 0.67, so it can be bent at an angle of 30 degrees to 180 degrees. By using the small angle of the tool tip, it can avoid sprouting holes or nuts. In addition, it can also be used as a deep insertion mold, and the tool can be avoided in both front and back positions.
Types And Processing Characteristics Of Curved Upper Punch
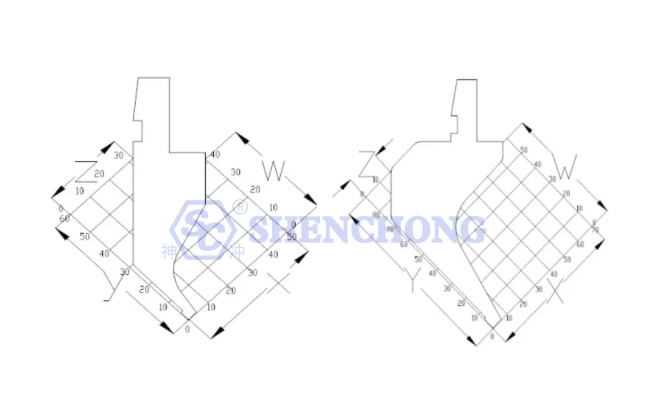
Tool analysis: The tool mainly uses the avoidance in the W direction during the bending process. When X>15MM, its avoidance effect becomes worse and worse. It only meets the bending conditions when Y>30, otherwise it will hit the back of the tool. This type of tool is commonly known as a small curved upper punch. When X>25MM, its avoidance effect becomes worse and worse. When Y>75, the bending condition is met, otherwise it will hit the back of the upper punch. This type of tool is commonly known as a large curved upper punch.
Types And Processing Characteristics Of Circular Arc Upper Punch
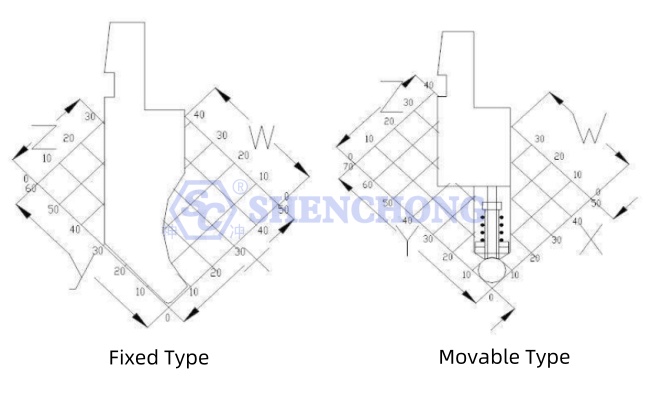
Tool analysis: Arc upper punches are divided into fixed and movable types. Arc upper punch meet the processing conditions of different arc bends by replacing the round rod. Fixed arc upper punch have the same avoidance effect as small bending tools when the X size is greater than 10MM. The common selection criteria for the V-groove of the lower mold are the diameter of the arc plus two plate thicknesses.
Types And Processing Characteristics Of Special Upper Punch
The special upper punch for press brake include stage difference molds, flattening molds, and some special shaped bending molds.
A: There are two types of existing differential molds: 415mm and 835mm. The size specifications of the dividing shape are consistent with those of the cutting tool, and the bending shape is shown in the forming diagram. However, when the thickness of the sheet is thick, such as T=2.0, considering the severe indentation and the limitations of the mold itself, it will be difficult to form.
B: The upper mold of the flattening mold is a flat mold, and the lower mold can be replaced by a regular bending lower mold, but it should avoid the V-groove. It is mainly used for dead edge flattening, riveting nuts and other processing methods.
Press Brake Lower Die
The lower die of the press brake includes bending lower mold, inserting deep lower mold, etc.
The selection of the lower die for the press brake is mainly based on the thickness of the processed product. When it is necessary to select large or small V notches for processing due to processing limitations, the bending coefficient needs to be adjusted accordingly. Mold analysis: The types of V notches mainly include 4V, 6V, 7V, 8V, 10V, 12,16V, 25V, and some special large V notches bending tools.
Basic Principles Of Bending Process Arrangement
- Bending from inside out.
- Bend from small to large.
- First bend the general shape, then bend the complex shape.
- The principle is that the bending of the previous process does not affect the subsequent process.
Control Method For Bending Size
- To avoid cumulative errors, measure the unfolded size for each fold during processing.
- Avoid leaning against bent edges and avoiding leaning against large angles.
- The product must be positioned with the bent edge, and the previous folding angle should be slightly less than 90 degrees.
- Determine the accuracy of measuring tools before processing.
- Perform initial inspection before formal processing and conduct regular inspections during the processing.
- Select the appropriate machine according to the precision requirements of the processed product.
- Avoid choosing tools that are not concentric, and confirm that the upper mold tool tip is on the same straight line before processing.
- Choosing good processing methods and arranging techniques to simplify processing difficulty.
- Accurate positioning, any abnormal positioning needs to be detected immediately.
Currently, CNC press brake controller can automatically optimize bending steps for users, which means operators do not need to manually design the bending steps by using CNC hydraulic press brake.
Conclusion
To know more about CNC press brake operation knowledge helps the operators improve the bending results and better maintain the machine. SC Machinery is one of the most famous hydraulic press brake manufacturers in China. For more information about press brake, please feel free to contact with us.