Table of Contents
A CNC V grooving machine is designed to create grooves, notches, or channels on the surface of a workpiece with a high level of precision. These machines are typically used in industries like automotive, aerospace, electronics, and construction, where accurate cuts and patterns are essential. They are operated through computer software that dictates the movement of cutting tools and the positioning of the workpiece, ensuring consistency and precision.
When considering a V grooving machine for your business, understanding the factors that influence its cost is crucial. The “V grooving machine price” can vary significantly based on multiple factors such as the machine’s specifications, brand reputation, and the region in which you purchase it. Whether you’re looking for a high-end model with advanced features or a more budget-friendly option, this complete guide will help you learn more about the machine, navigate the market and make an informed decision.
What Is A CNC V Grooving Machine?
A CNC V grooving machine is a specialized piece of equipment used in metal and woodworking industries to create precise V-shaped grooves on the surface of various materials. These grooves are essential in allowing materials like metal sheets, composite panels, and wood to be bent or folded at sharp angles without causing deformation or damage. The machine uses a cutting tool that removes material along a defined path, creating a groove that facilitates cleaner and more accurate bends.
When exploring the realm of precision sheet metal fabrication, one of the most significant advancements is the V grooving machine. Also known as a V groover, this powerful tool is specifically designed to create precise grooves in various metal sheets. But why is this so crucial? In metalworking, the accuracy and depth of these grooves play a vital role in determining both the bendability and the aesthetic quality of the final product.
The operation of a CNC V grooving machine is straightforward yet remarkably effective. It utilizes rotary cutting tools to carve a V-shaped groove into the metal sheet. The depth and angle of this groove are carefully controlled, enabling precise bending along the grooved lines. This process not only ensures the accuracy of the bends but also facilitates the creation of sharp, clean angles—an essential feature in industries such as architectural metalworking and high-end cabinetry.
CNC V Grooving Machine Application
Manufacturing Applications
Vertical CNC V-groove machines are often used in manufacturing industries where high processing accuracy is required, such as manufacturing precision parts, metal casings, precision instruments, etc. Its vertical design allows for better control of cutting angle and depth during processing, thereby ensuring product quality and assembly accuracy. In addition, vertical V-groove machines are generally suitable for fine machining and engraving of material surfaces.
Application In Building Decoration Field
In the field of architectural decoration, horizontal V-groove machines are often used to cut V-grooves on building materials, such as processing aluminum plates, stainless steel plates, etc. Due to its large processing depth and ease of operation, horizontal V-grooving machines are a common choice for decorative manufacturers.
Vertical V-groove machines are also used in the field of architectural decoration. They are especially suitable for fine processing and engraving of architectural decoration materials, such as the production of exquisite metal carved panels.
Understanding CNC V Groove Technology
The process of grooving using a CNC machine begins with the design phase. Operators use CAD (Computer-Aided Design) software to create the groove pattern, which is then converted into a set of instructions using CAM (Computer-Aided Manufacturing) software. These instructions, known as G-code, are loaded into the CNC control unit.
Once the machine is programmed, the operator mounts the workpiece onto the worktable and selects the appropriate cutting tools. The machine then begins the grooving process, following the programmed tool path to cut the groove with precision. During the process, the cutting tool and worktable move in synchronization, ensuring that the groove is cut to the exact specifications.
V Grooving VS. Traditional Grooving Methods
V Grooving technology stands apart from traditional grooving methods in several key ways. Traditional methods often involve manual processes or less advanced machinery, which can lead to inconsistencies and limitations in the depth and precision of the grooves. V Grooving, with its CNC technology, offers unparalleled precision and consistency. This method also allows for more complex and intricate grooving patterns, which are challenging to achieve with traditional methods.
CNC V Grooving Technology Advantages
- Precision Cutting:V grooving involves using rotary cutting tools, typically controlled by a CNC (Computer Numerical Control) system, to carve out V-shaped grooves along predetermined lines on the metal sheet. The depth and angle of these grooves are meticulously controlled to ensure consistency and precision.
- Enhanced Bendability:The grooves created by V grooving allow the metal to be bent more easily and accurately along the grooved lines, without causing material deformation such as warping or bulging. This results in sharper, cleaner bends that meet high aesthetic and structural standards.
- Material Versatility:V grooving technology is applicable to a wide range of materials, including stainless steel, aluminum, copper, and other metals, making it a versatile tool in various fabrication processes.
- CNC Integration:The integration of CNC systems in V grooving machines allows for automated, precise control over the grooving process, ensuring each cut is made according to exact specifications. This automation enhances both the efficiency and accuracy of the process.
Classification of V Grooving Machines
Grooving machines can be classified based on several criteria, including their design, operation, and application. Here are the main classifications:
Based On Operation
- Manual Grooving Machines:Operated manually, requiring direct input from the operator for each cut.
- Semi-Automatic Grooving Machines:Combine manual operation with some automated features, such as power feed.
- Fully Automatic CNC Grooving Machines:Equipped with CNC technology, allowing for fully automated grooving processes with programmable settings.
Based On Design
- Vertical Grooving Machines:Designed with a vertical spindle, suitable for vertical grooving operations.
- Horizontal Grooving Machines:Feature a horizontal spindle, commonly used for horizontal grooving tasks.
Horizontal CNC V Grooving Machine VS Vertical CNC V Grooving Machine
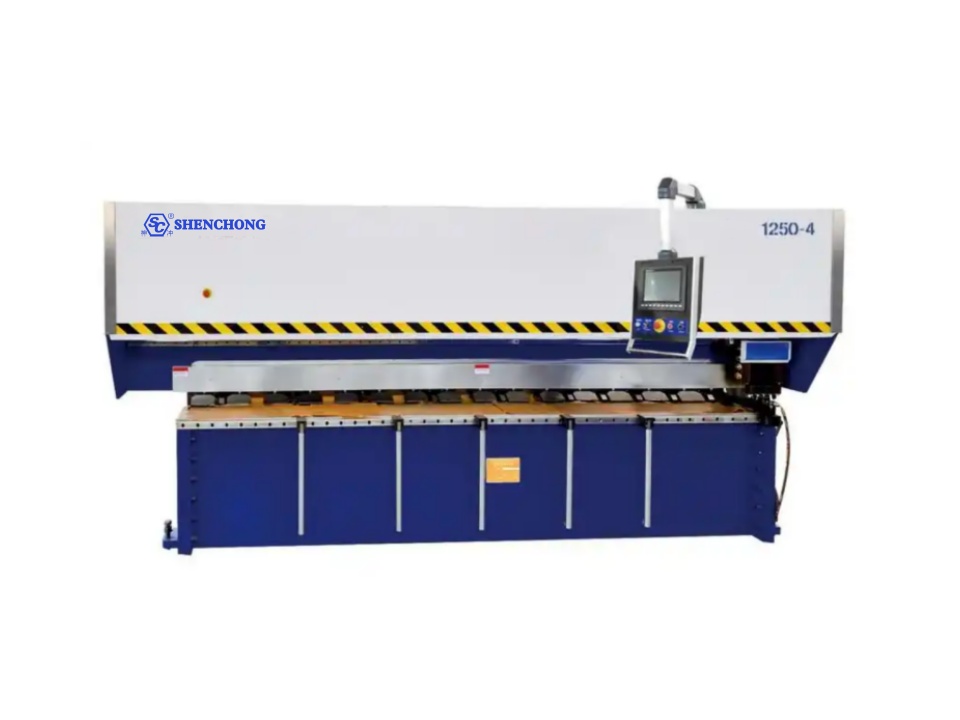
Horizontal V Groover Machine
The horizontal V-shaped tank machine is equipped with a variety of metal processing machines, and its main function is to process the V-shaped groove on metal sheets. Various types of equipment used in the control technology, continuous advance setting process, number control tool operation, practical precision, consistent V-shaped groove processing. The advantages of the horizontal CNC V groove machine are easy to operate, high processing precision, and efficiency, and can be used to process various types of metal plate materials
Low operator requirements: Operation horizontal CNC V grooving machine requires no personnel equipment, and high skill requirements, easy to cultivate.
Horizontal CNC V Grooving Machine Advantages
Low operator requirements: Personnel operating a CNC V-groove machine do not need to have excessive skill requirements and are easy to train and take up positions.
During V-groove processing, the user does not need to move the steel plate and will not scratch the surface of the plate, making the operation more convenient.
After processing, it is simple and convenient to clean up the waste materials, which improves work efficiency.
The horizontal V-groove machine has a relatively low price and high cost performance, making it suitable for users with limited budgets.
For decoration manufacturers, the horizontal V-groove machine is a good choice and can meet the processing needs of decoration materials.
Horizontal CNC V Grooving Machine limitation
It is only suitable for processing plates with a thickness less than 3 mm, and cannot meet the needs of thicker plates.
Due to structural limitations, the horizontal V-groove machine may be slightly inferior to the vertical type in terms of processing accuracy, and is not suitable for processing occasions that require higher accuracy.
For users who need to process large-size plates or thicker plates, the processing range of the horizontal V-groove machine is limited, so you need to choose carefully.
Vertical CNC V Grooving Machine
Vertical CNC V grooving machine uses a rotary cutting tool to carve a “V” shaped recessed tank on a metal plate, and the depth and angle of the recessed tank can be carefully controlled, making it possible to make a precise curve. The various types of engineering do not require high curvature precision, and can be formed at a fixed angle, while the construction metal processing and high-end cutting, etc. are carried out in addition.
Vertical CNC V Grooving Machine Advantages
Large cutting depth, vertical V-shaped tank machine, horizontal type with larger cutting depth, suitable for progressive processing of thick materials.
High stability, horizontal placement of the work table, no material movement during machining, and excellent process stability.
However, this product is designed with attention to detail, durability, and accuracy. Usually, the main parts of the frame are made of high-grade steel or iron, and the structure is reduced in design and movement during the operation process. This is a matter of safety and stability for mechanical design.
Vertical CNC V Grooving Machine Limitation
Materials with high hardness requirements: Materials with high hardness can be used for Japanese knives.
Cutting depth limit: since the equipment structure limit, cutting depth possible limit.
Key Components Of A CNC V Grooving Machine
To understand how a CNC grooving machine works, it is important to familiarize yourself with its key components. Each part plays a crucial role in ensuring the machine’s precision, speed, and effectiveness.
CNC Controller
CNC controller is is the brain of the CNC V grooving machine, responsible for executing the programmed instructions that control the grooving process. Operators input the design specifications, and the CNC unit translates these instructions into precise movements of the cutting tools and workpiece.
The control unit includes software that allows operators to design complex patterns and control the machine’s speed, tool path, and depth of the groove. Modern CNC systems often feature user-friendly interfaces, touchscreens, and advanced programming capabilities, allowing for greater flexibility in grooving operations.
CNC V Grooving Machine Cutting Tool
The cutting tool is perhaps the most critical component of a CNC grooving machine, as it directly interacts with the workpiece to create grooves. Typically made from high-speed steel (HSS) or carbide, the cutting tool must be sharp, durable, and capable of withstanding high temperatures generated during machining.
CNC grooving machines can be equipped with various cutting tools, depending on the type of groove required. These include single-point tools for simple grooves, multi-point tools for intricate patterns, and specialty tools for materials like hard alloys or brittle ceramics. The selection of the right tool is crucial for ensuring the desired groove quality and minimizing tool wear.
Worktable
The worktable provides stability and support to the workpiece, ensuring that it remains in position during the grooving operation. In CNC grooving machines, the worktable is usually motorized and can move along multiple axes, allowing for complex groove patterns to be created without having to reposition the workpiece manually.
Worktables are often equipped with clamping systems that securely hold the workpiece in place. In some machines, vacuum or magnetic clamping systems are used to ensure an even more secure grip, especially when working with thin or delicate materials.
Spindle
The spindle holds and rotates the cutting tool at high speeds during the grooving process. In a CNC grooving machine, the spindle’s performance is critical, as it dictates the speed, torque, and accuracy with which the cutting tool engages the workpiece.
Most modern CNC grooving machines are equipped with motorized spindles that allow for high-speed grooving operations. The spindle speed can be adjusted based on the material being grooved, ensuring optimal cutting conditions. Additionally, the spindle is designed to minimize vibrations, which can negatively affect the groove’s accuracy and surface finish.
Clamping System
The clamping system of a CNC grooving machine is designed to securely hold the workpiece, typically metal sheets, in place during the grooving process. It ensures stability, precision, and safety by preventing material movement, reducing vibrations, and distributing pressure evenly.
Common clamping systems include mechanical, pneumatic, hydraulic, vacuum, and magnetic clamps, each offering unique advantages depending on the material and application. A reliable clamping system is essential for maintaining accuracy and efficiency in CNC operations.
Linear Guides And Ball Screws
Precision in CNC grooving machines is largely dependent on the smooth and accurate movement of the cutting tool and workpiece. Linear guides and ball screws are two components that ensure this movement is both accurate and stable.
Linear Guides: These are responsible for guiding the movement of the machine’s axes (X, Y, and Z) with minimal friction. Linear guideways ensure smooth, friction-free movement, allowing the cutting tool to traverse the workpiece with high precision. They are made of hardened steel and designed to minimize wear, ensuring long-lasting accuracy.
Ball Screws: Ball screws convert the rotational motion of the machine’s motors into linear motion. They play a key role in positioning the workpiece and cutting tool during machining. Ball screws offer high precision and minimal backlash, ensuring that the machine can produce grooves with tight tolerances.
Servo Motors
Servo motors play a crucial role in CNC grooving machines by providing precise control over the cutting process. These motors enable accurate positioning and movement of the cutting tool, ensuring consistent and high-quality grooves in various materials. Equipped with feedback systems, servo motors allow for real-time adjustments in speed and torque, facilitating efficient operation and reduced cycle times.
Their ability to coordinate multi-axis movements enhances the machine’s versatility, making them essential for modern automated manufacturing. Overall, servo motors significantly improve the accuracy, efficiency, and reliability of CNC grooving operations.
Chip Management System
During the grooving process, material is removed from the workpiece in the form of chips. These chips can accumulate around the cutting area, obstructing the view of the workpiece, and interfering with the accuracy of the groove. To address this issue, CNC grooving machines are equipped with chip management systems.
These systems include chip conveyors or vacuums that remove chips from the machining area and deposit them into a collection bin. Efficient chip management not only keeps the work area clean but also prevents chips from causing damage to the machine or the workpiece.
Tool Changer
Many CNC v grooving machines are equipped with automatic tool changers, allowing for the rapid swapping of cutting tools during machining. This feature is particularly useful when creating complex grooves that require different tools or when machining multiple workpieces with varying groove patterns.
The tool changer stores multiple cutting tools and selects the appropriate one based on the programmed instructions. This automation eliminates the need for manual tool changes, reducing downtime and increasing production efficiency.
Coolant System
Grooving, especially in harder materials like metals, generates significant heat due to the friction between the cutting tool and the workpiece. Overheating can lead to tool wear, decreased accuracy, and poor surface finish. To mitigate this, CNC grooving machines are equipped with coolant systems.
The coolant system circulates a cutting fluid that cools both the tool and the workpiece during machining. This fluid not only prevents overheating but also helps lubricate the cutting process, reducing friction and extending tool life. Some CNC machines are equipped with mist or air-based cooling systems for materials that do not require liquid coolants.
Safety Protection
CNC grooving machines are powerful and potentially hazardous pieces of equipment. To protect operators and ensure safe operation, these machines are equipped with various safety features. These include:
- Emergency Stop Buttons: Located in easily accessible areas, these buttons immediately halt the machine in case of an emergency.
- Overload Protection: Sensors monitor the machine’s load and automatically shut it down if an overload is detected, preventing damage to the machine and the workpiece.
- Enclosures and Guards: CNC grooving machines are often enclosed to prevent chips, coolant, and debris from escaping and posing a hazard to the operator.
Factors Influencing V Grooving Machine Price
The price of a V grooving machine can vary greatly depending on a range of factors. Understanding these factors is crucial for making an informed purchasing decision that aligns with your production needs and budget.
Horizontal CNC V Grooving Machine Price
The horizontal CNC V grooving machine price can vary widely depending on factors such as machine specifications, brand, and additional features. Generally, the cost for a horizontal V grooving machine ranges from $13,000 to $62,000 or more, depending on the complexity and capabilities of the machine.
Vertical CNC V Grooving Machine Price
The price of a vertical CNC V grooving machine can vary significantly based on several factors, including the machine’s specifications, brand, and the region in which it is purchased. On average, the cost of a vertical V grooving machine can range from $17,000 to $68,000 or more.
Machine Specifications
- Size and Capacity:Larger machines that can handle thicker and wider sheets of metal typically command higher prices. The capacity to work with various material thicknesses also impacts the cost.
- Material Compatibility:Machines capable of processing a wide range of materials, such as stainless steel, aluminum, copper, and other metals, generally cost more due to their versatility.
- Precision and Speed:Machines that offer higher precision in cutting and faster operation speeds tend to be more expensive. These features are essential for industries requiring tight tolerances and high production efficiency.
Technological Features
- CNC Control Systems:V grooving machines equipped with advanced CNC (Computer Numerical Control) systems allow for automated, precise control over the grooving process, which typically increases the machine’s price.
- Automation and Integration:Features like automated material handling, advanced user interfaces, and integration with other fabrication systems can add to the cost. These features enhance productivity and reduce manual labor.
- Safety Features:Machines with enhanced safety mechanisms, such as emergency stops, protective covers, and sensors, are often priced higher due to the added value in protecting operators and ensuring compliance with safety standards.
Brand and Manufacturer
- Reputation:Established brands with a reputation for quality, reliability, and advanced technology often come at a premium. These brands usually offer better support, longer warranties, and higher resale values.
- Country of Manufacture:Machines produced in countries with higher manufacturing costs, such as Japan, Germany, or the United States, tend to be more expensive compared to those made in regions with lower production costs, like China.
Customization and Special Features
Machines that are customized to meet specific production needs or come with special features (such as unique cutting angles, additional tools, or proprietary technology) will generally be more expensive than standard models.
By considering these factors, businesses can better assess the total cost of ownership for a V grooving machine and choose a model that offers the best balance of price, performance, and long-term value.
After-Sales Support and Warranty
- Comprehensive Support:Manufacturers that offer extensive after-sales support, including training, maintenance services, and quick access to replacement parts, may charge more for their machines, but this support can be invaluable in maintaining long-term productivity.
- Warranty Length and Coverage:A longer or more comprehensive warranty can increase the initial cost of the machine, but it also provides peace of mind by covering potential repairs or replacements.
Conclusion
With continued advancements in CNC technology, CNC V grooving machines are becoming even more efficient, versatile, and accessible, allowing manufacturers across industries to produce high-quality grooved components with minimal manual intervention. CNC V grooving machine complete guide will help you learn more about the machine, navigate the market and make an informed decision. Selecting the right V Grooving machine for your needs involves careful consideration of several key factors. Understanding these aspects will help ensure that you invest in a machine that not only meets your current requirements but also adapts to future projects and technological advancements. By considering these factors, you can make an informed decision on which V Grooving machine is the best fit for your operational needs and future growth.