Table of Contents
Argentina customers ordered SC Machinery CNC press brake WEK 250T 4000MM 4+1 ESA S630. SC CNC press brake machines are widely sold in many countries and regions in South America.
1. Argentina CNC press brake for sale configuration
– WEK electro-hydraulic synchronous series
– 250 tons 4000 mm
– 4+1 axes
– ESA S630 CNC controller
– Optional cylinder compensation
200ton 4000mm 4+1 axis ESA630 CNC hydraulic press brake machine is usually used for large size and high precision metal sheet bending processing, suitable for metal materials of different thicknesses, such as stainless steel, carbon steel, aluminum alloy, etc. The following are some main parameters and features of this type of Argentina cnc hydraulic press brake machine.
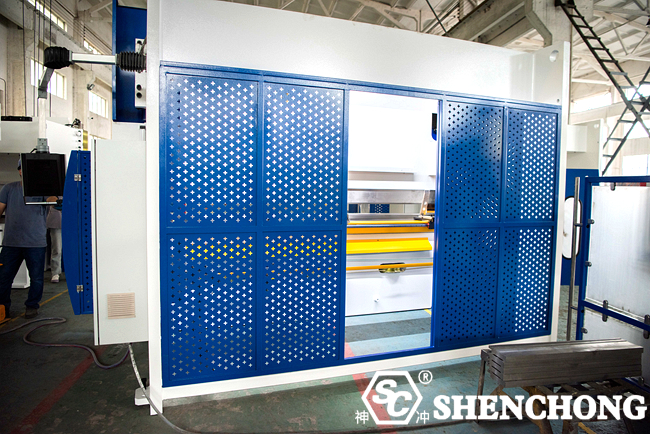
2. Basic parameters of Argentina CNC press brake
Maximum bending capacity: 200 tons
The maximum bending force that this model can withstand is 200 tons, which is suitable for processing thicker metal sheets.
Bending length: 4000 mm
The maximum bending length is 4000 mm, which can handle larger-sized sheets.
Bending thickness:
The thickness of the material that can be bent is usually between 1mm and 12mm, and the specific value will vary depending on the type of material and the bending requirements.
4+1 axis system:
– Y1, Y2 axis control the oil cylinders on both sides
– X controls the back gauge to move forward and backward
– R controls the back gauge to move up and down
– V is the workbench compensation.
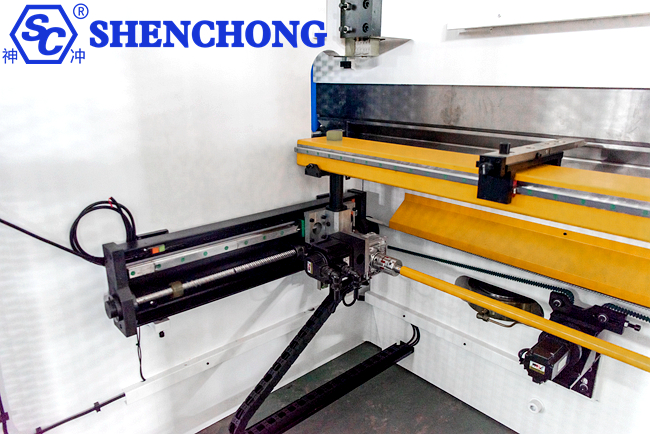
3. Cylinder compensation
The press bending cylinder compensation refers to the automatic adjustment of the uneven gap between the upper and lower dies (i.e., bending depth) caused by load changes during the bending process by the control of the hydraulic cylinder, ensuring consistent bending effect and accuracy throughout the bending process.
Working principle:
Cylinder compensation usually relies on the automatic adjustment of the hydraulic system of the bending machine. During operation, the system will detect the gap between the upper die and the lower die in real time through the sensor, and adjust the pressure or position of the hydraulic cylinder according to the detection results, so that the mold is always kept in an ideal working state to avoid changes in the bending depth due to load changes.
– Load change detection
When the pressure or position of the upper and lower dies of the press brake changes, the sensor will feedback this information.
– Automatic adjustment of the cylinder
According to the signal fed back by the sensor, the hydraulic system will adjust the pressure of the cylinder to automatically compensate for the gap error caused by load changes.
– Maintaining bending accuracy
The compensation effect of the cylinder can ensure that the mold of cnc hydraulic press brake machine can still maintain a consistent depth and angle under different workpieces and bending forces, ensuring accurate bending effects.
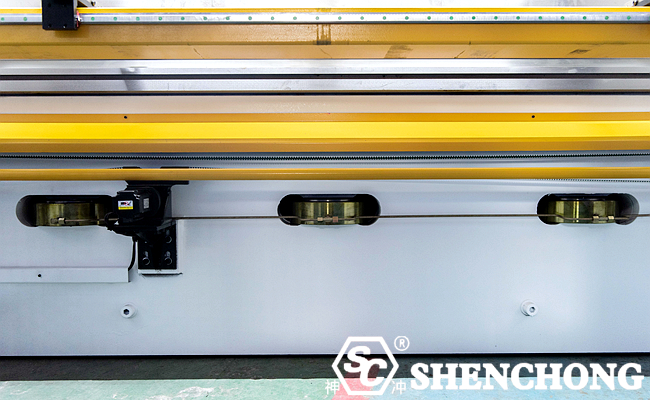
Function and significance:
– Compensate for changes in the gap between the upper and lower dies
In actual operation, with the change of bending force, especially for large tonnage and large-sized workpieces, the upper and lower dies of the bending machine may deform or displace to a certain extent, resulting in uneven bending depth and affecting the bending quality of the workpiece.
The cylinder compensation system can effectively offset the slight changes in the gap between the upper and lower dies caused by different loads by adjusting the pressure or position of the hydraulic cylinder in real time, ensuring the consistency of the bending depth and angle.
– Improve bending accuracy
Through compensation, the force of the upper and lower dies is more uniform, so that the accuracy of each bending can be improved, especially in the bending of workpieces with high precision requirements. The cylinder compensation system is particularly important. It can ensure that the bending depth of each part of the workpiece is consistent during the bending process, avoiding precision deviations caused by pressure differences or mold wear.
– Extend the service life of the machine
Through timely compensation adjustment, the excessive wear of the machine caused by deformation during the bending process can be reduced, especially in the case of excessive pressure, avoiding excessive burden on the mold and hydraulic system, thereby extending the service life of the machine.
– Adapt to workpieces of different thicknesses
When bending materials of different thicknesses, the cylinder compensation system can automatically adjust and make precise compensation according to the thickness and hardness of the material, ensuring that the bending effect can meet expectations under different processing conditions.
4. ESA630 CNC system
ESA 630 is a widely used CNC system with high stability and strong adaptability, supporting precise CNC operation.
Provides real-time display, automatic parameter adjustment, position feedback and other functions to ensure high-precision and high-efficiency processing.
Supports the writing and storage of multiple bending programs to meet different bending needs.
5. Application scope
Metal processing: Suitable for bending processing of various types of metal sheets, widely used in automobiles, home appliances, ships, steel structures, machinery manufacturing and other industries.
Precision bending: It is very suitable for bending processes that require precise angles and shapes, especially for the production of complex parts.
Argentina CNC press brake 200 tons 4000 mm 4+1 axis ESA630 is an efficient and precise bending equipment suitable for industries that require high bending accuracy and large-size processing. The equipped ESA630 CNC system makes the machine operation more intelligent and automated, and can provide stable and reliable performance in complex production environments.