مقدمة
جدول المحتويات
ثني الصفائح المعدنية هو عملية تصنيع بالغة الأهمية تُستخدم لتشكيل الصفائح المعدنية بالزاوية والشكل المطلوبين. تلعب دورًا مهمًا في الصناعات مثل صناعة السيارات والفضاء والبناء والإلكترونيات. ولكن لماذا تفشل عملية ثني الصفائح المعدنية غالبًا في الحفاظ على شكلها؟ تكمن الإجابة في ظاهرة تسمى الارتداد. أحد التحديات الرئيسية التي تواجه عملية الثني هو الارتداد. يحدث هذا عندما يعود المعدن جزئيًا إلى شكله الأصلي بعد الانحناء، والذي يتأثر بعوامل مثل خصائص المادة ونصف قطر الانحناء والقوة المطبقة. قد يؤدي الارتداد في ثني الصفائح المعدنية إلى منتجات نهائية غير دقيقة. في هذه المقالة، سوف نستكشف أسباب الارتداد في ثني الصفائح المعدنية، وتأثير الارتداد على الدقة، والاستراتيجيات الفعالة لتقليل الارتداد. يمكن أن يؤدي فهم هذه المفاهيم إلى تحسين دقة وجودة أعمال معالجة المعادن بشكل كبير.
ما هو Springback في ثني الصفائح المعدنية؟
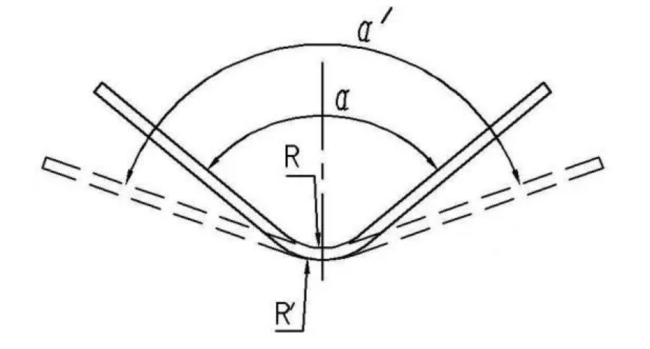
عندما لا تتمكن اللوحة المعدنية من الحفاظ على الزاوية أو الانحناء الدقيق المتوقع بعد الانحناء، يحدث ارتداد. عندما يتم تطبيق القوة لثني اللوحة المعدنية، فإنها تخضع لتشوه مرن وبلاستيكي. التشوه البلاستيكي دائم، في حين أن التشوه المرن مؤقت وسيتعافى بمجرد إزالة القوة الخارجية. يتسبب تعافي هذا التشوه المرن في عودة اللوحة جزئيًا إلى موضعها الأصلي، مما يؤدي إلى ارتداد.
المبدأ الفيزيائي
إن المبدأ وراء الارتداد يكمن في الضغوط الداخلية التي يتم توليدها أثناء الانحناء. فعندما تنثني الورقة، يتم شد السطح الخارجي للانحناء (الإجهاد الناتج عن الشد)، بينما يتم ضغط السطح الداخلي (الإجهاد الانضغاطي). وبمجرد إزالة قوة الانحناء، يحاول المكون المرن لهذه الضغوط إعادة المادة إلى حالتها غير المشوهة. وتعتمد درجة الارتداد على التوازن بين التشوه المرن والبلاستيكي داخل المادة.
العوامل المؤثرة على السبرينغباك
هناك العديد من العوامل التي تؤثر على كمية الارتداد الذي يحدث في ثني الصفائح المعدنيةإن فهم هذه العوامل يمكن أن يساعد في التنبؤ بالارتداد والتحكم فيه أثناء عملية التصميم والتصنيع.
1. خصائص المواد
- قوة الخضوع:المعادن ذات قوة الخضوع الأعلى تكون أكثر عرضة للارتداد لأنها تقاوم التشوه الدائم ولديها ميل أكبر للعودة إلى شكلها الأصلي. غالبًا ما تظهر الفولاذ عالي القوة وسبائك الألومنيوم ارتدادًا أكثر أهمية مقارنة بالفولاذ منخفض الكربون.
- معامل المرونة:تحدد معامل المرونة أو الصلابة للمادة قدرتها على العودة إلى شكلها الأصلي بعد تشوهها. تظهر المعادن ذات معامل المرونة الأعلى، مثل الفولاذ، مرونة أكبر من المواد الأكثر ليونة مثل الألومنيوم أو النحاس.
يتناسب حجم زاوية الارتداد بشكل مباشر مع قوة الخضوع αa للمادة ويتناسب عكسيا مع معامل المرونة (E). أي أنه كلما زادت قوة الخضوع للمادة، كلما كان معامل المرونة أصغر، وكلما كان الارتداد أصغر في الصفائح المعدنية. وعلى العكس، كلما كان الارتداد أكبر.
بالنسبة لقطعة العمل المنحنية ذات متطلبات الدقة العالية، من أجل تقليل الارتداد، يجب اختيار الفولاذ منخفض الكربون بدلاً من مواد مثل الفولاذ عالي الكربون أو الفولاذ المقاوم للصدأ.
2. سمك الورقة
تميل الصفائح الأكثر سمكًا إلى التعرض لقدر أقل من الارتداد مقارنة بالصفائح الأقل سمكًا. ويرجع هذا إلى أن الصفائح الأكثر سمكًا تخضع لمزيد من التشوه البلاستيكي أثناء الانحناء، مما يقلل من تأثير الاستعادة المرنة. وعلى العكس من ذلك، تكون الصفائح الأقل سمكًا أكثر مرونة ومرونة، مما يؤدي إلى ارتداد أكثر وضوحًا.
3. نصف قطر الانحناء
تؤثر نسبة سمك الورقة إلى نصف قطر الانحناء بشكل كبير على الارتداد. عندما يكون نصف قطر الانحناء كبيرًا نسبيًا لسمك الورقة، يحدث تشوه أكثر مرونة، مما يؤدي إلى ارتداد أكبر. يؤدي نصف قطر الانحناء الأصغر إلى تشوه أكثر بلاستيكيًا ويقلل من الارتداد.
هذا مفهوم مهم. عندما تسمح خصائص المواد، يجب أن تختار صفائح الأجزاء المنحنية من الصفائح المعدنية أصغر نصف قطر انحناء ممكن لتحسين دقة التصنيع. ومن الجدير بالذكر بشكل خاص أن الأجزاء ذات نصف قطر الانحناء الكبير تشكل تحديات معينة في التحكم في دقة التصنيع والجودة.
4. زاوية الانحناء
كلما زادت زاوية الانحناء، زادت أهمية الارتداد في تأثير ثني الصفائح المعدنية. على سبيل المثال، عند ثني صفيحة بزاوية كبيرة (مثل 90 درجة أو أكثر)، تتعرض المادة لمزيد من الضغط، مما يزيد من احتمالية الارتداد بمجرد إزالة قوة الانحناء.
على العكس من ذلك، فإن زاوية مركز الانحناء الأصغر تعني مساحة تشوه أصغر، مما يؤدي إلى كمية تراكمية أصغر من التشوه المرن وبالتالي ارتداد إجمالي أصغر في ثني الصفائح المعدنية.
5. طريقة الانحناء
تؤثر طرق الانحناء المختلفة، مثل الانحناء الهوائي والتثبيت، على درجة الارتداد. في الانحناء الهوائي، يتم دعم الورقة جزئيًا فقط، مما يؤدي إلى استعادة أكثر مرونة، بينما في التثبيت (حيث يتم ضغط الورقة بالكامل في القالب)، يتم تقييد المعدن بشكل أكثر إحكامًا، مما يقلل من الارتداد.
6. تأثير قوة الانحناء F
بالنظر إلى نصف قطر الانحناء وزاوية المركز وسمك المادة معينين، فإن قوة الانحناء F الأكبر ستؤدي إلى ارتداد أصغر، في حين أن قوة الانحناء الأصغر ستؤدي إلى ارتداد أكبر في ثني الصفائح المعدنية.
حساب صمام الزنبرك في ثني الصفائح المعدنية
تتضمن عملية حساب الارتداد في ثني الصفائح المعدنية تحديد الفرق بين زاوية الانحناء الأولية والزاوية بعد استعادة المادة لبعض شكلها الأصلي بسبب الاستعادة المرنة. فيما يلي عملية خطوة بخطوة لتقدير وحساب الارتداد.
المعلمات الرئيسية
تعتمد كمية الارتداد على عدة عوامل مثل خصائص المادة، والسمك، ونصف قطر الانحناء، وطريقة الانحناء.
- معامل يونغ (E):هذه هي معامل مرونة المادة، الذي يقيس مدى صلابتها.
- قوة الخضوع (σ_y):هذا هو الضغط الذي تبدأ عنده المادة بالتشوه بلاستيكيًا.
- نصف قطر الانحناء الأولي (R_b):نصف قطر الانحناء الذي تشكله اللكمة قبل الارتداد.
- سمك الورقة (طن):سمك الصفائح المعدنية.
- زاوية الانحناء النهائية (θ):الزاوية بعد الارتداد.
عامل الارتداد (Ks)
إحدى أبسط الطرق لحساب الارتداد هي استخدام عامل الارتداد ك، وهي نسبة زاوية الانحناء النهائية بعد الارتداد إلى زاوية الانحناء الأولية قبل الارتداد. ويمكن تقديرها باستخدام المعادلة التالية:
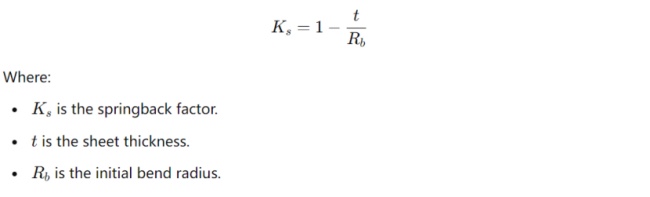
حساب زاوية الارتداد
يمكن حساب زاوية الارتداد عن طريق ضرب زاوية الانحناء الأولية بعامل الارتداد:
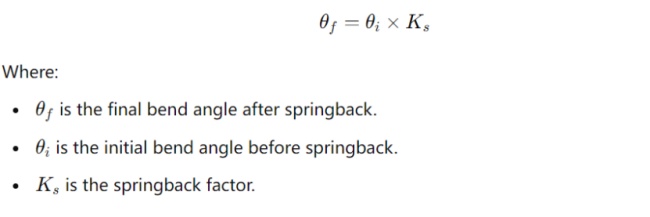
تقدير الارتداد بناءً على خصائص المواد
للحصول على نهج أكثر تفصيلاً، وخاصة عند استخدام مواد عالية القوة، يمكن حساب الارتداد باستخدام الصيغة التالية:
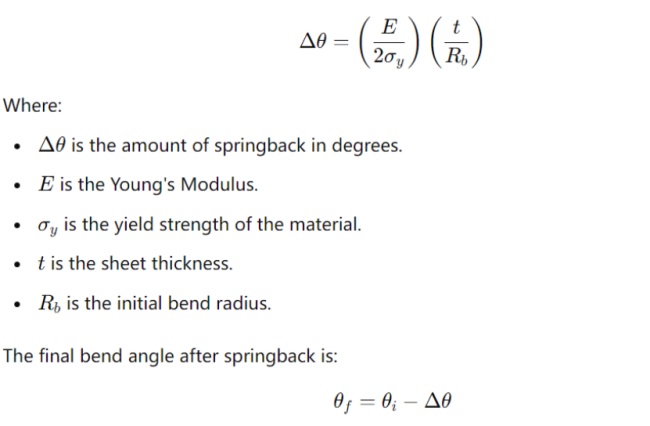
مثال على الحساب
لنفترض أن لديك البيانات التالية:
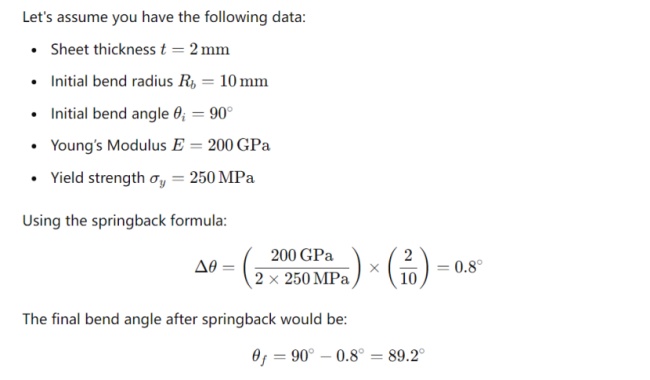
وبالتالي، بعد الارتداد، ستكون زاوية الانحناء تقريبًا 89.2∘89.2^\circ89.2∘، مما يشير إلى قدر ضئيل من الاسترداد. يعمل تعديل زاوية الانحناء أثناء العملية على تعويض ذلك.
حلول للتخفيف من حدة الارتداد
على الرغم من أنه لا يمكن القضاء على الارتداد في ثني الصفائح المعدنية بشكل كامل، إلا أنه يمكن استخدام استراتيجيات مختلفة للتحكم في آثاره وتقليلها أثناء عملية الثني.
تطبيقات وأهمية التحكم في الارتداد
يعد التحكم في الارتداد أمرًا ضروريًا في الصناعات التي تتطلب الدقة، مثل صناعة السيارات والفضاء الجوي. يجب أن تلتزم المكونات مثل ألواح هيكل السيارة وأغطية الطائرات والإطارات الهيكلية بتفاوتات ضيقة. يمكن أن يؤدي الارتداد المفرط إلى إعادة العمل المكلفة أو إهدار المواد أو حتى المساس بسلامة الهيكل.
في الإنتاج الضخم، يساعد تقليل الارتداد إلى الحد الأدنى في الحفاظ على جودة ثابتة عبر دفعات كبيرة، مما يقلل من تكاليف المواد ويحسن الكفاءة. كما يسمح التحكم الدقيق في الارتداد للمصنعين باستخدام مواد عالية القوة دون المساس بجودة المنتج.
تحسين تصميم الأجزاء المنحنية
- إن تحسين التصميم الهيكلي للأجزاء المنحنية يمكن أن يقلل من زاوية الارتداد دون التأثير على وظائفها. على سبيل المثال، يمكن أن يؤدي قمع الأضلاع المقوية في المنطقة المنحنية أو استخدام الحواف المشكلة إلى زيادة صلابة وتشوه الجزء المنحني، وبالتالي تقليل الارتداد.
- إن استخدام مواد ذات معامل مرونة مرتفع، وقوة خضوع منخفضة، وصلابة منخفضة، ومرونة جيدة يمكن أن يقلل من الارتداد ويسهل التحكم في الارتداد مع تلبية متطلبات الاستخدام.
تحسين إجراءات العملية
1. الانحناء الزائد
تتضمن عملية الثني الزائد ثني الصفائح المعدنية قليلاً إلى ما هو أبعد من الزاوية المطلوبة للتعويض عن الارتداد. تتطلب هذه التقنية الخبرة والحسابات الدقيقة لتحديد المقدار الصحيح من الثني الزائد المطلوب للمواد والسمك المختلفة.
2. ضبط قوة الانحناء
إن زيادة قوة الانحناء أو تطبيق عملية انحناء ثانوية يمكن أن يساعد في زيادة التشوه البلاستيكي في المادة. وهذا يقلل من الاستعادة المرنة ويقلل من الارتداد. هذه التقنية فعالة بشكل خاص في تقليل الارتداد للمواد عالية القوة.
3. استخدام نصف قطر انحناء أصغر
من خلال تصميم نصف قطر الانحناء ليكون أصغر، تتعرض المادة لمزيد من التشوه البلاستيكي، مما يقلل من الاستعادة المرنة المسؤولة عن الارتداد. ومع ذلك، يجب توخي الحذر لتجنب إنشاء نصف قطر صغير جدًا، مما قد يؤدي إلى تشقق أو تلف المادة.
4. اختيار المواد ومعالجتها
يمكن أن يؤدي اختيار مواد ذات قوة خضوع أقل أو استخدام المعالجات الحرارية لتقليل صلابة المواد إلى تقليل الارتداد. على سبيل المثال، يمكن استخدام التلدين لتليين المعادن، مما يجعلها أكثر ليونة وأقل عرضة للارتداد.
5. محاكاة تحليل العناصر المحدودة (FEA)
تسمح أدوات البرمجيات الحديثة، مثل تحليل العناصر المحدودة (FEA)، للمصنعين بمحاكاة عملية الانحناء والتنبؤ بدرجة الارتداد قبل ثني الورقة فعليًا. تساعد هذه المحاكاة المهندسين على ضبط معلمات الانحناء لضمان نتائج دقيقة، مما يقلل من التجربة والخطأ في مرحلة الإنتاج.
ضبط الخلوص في قوالب الانحناء
يساعد تقليل الفجوة بين القوالب على تقليل الارتداد. عندما تكون الفجوة بين أسطح القالب المنحنية أقل من سمك المادة، يمكن تقليل الارتداد بشكل كبير، مما يؤدي حتى إلى ارتداد سلبي طفيف. يمكن أن تؤدي الفجوة الصغيرة جدًا إلى ترقق المادة وخدوش السطح على قطعة العمل وتقصير عمر القالب. عندما ينحرف سمك اللوح بشكل سلبي، يمكن أن تتسبب الفجوة المفرطة المتكونة بين المثقب والقالب أيضًا في الارتداد. الحل هو تصميم قوالب ثني الفجوة القابلة للتعديل.
تحسين تصميم قوالب الانحناء
بناءً على قيم الارتداد المقدرة أو التجريبية، يمكننا التعويض (أو الخصم) ضمن نطاق الشكل والحجم لأجزاء العمل القالبية لجعل الأجزاء المنحنية تلبي متطلبات الشكل والحجم الموضحة في رسم المنتج.
1) زاوية ارتداد الانحناء للمواد اللينة مثل النحاس الناعم 0215 و0235 و08 و10 و20 وH2 أقل من 5 درجات. عندما يكون انحراف سمك المادة صغيرًا، يمكن تصميم منحدر (زاوية تعويض الارتداد) على المثقب أو القالب. الفجوة بين المثقب والقالب تساوي الحد الأدنى لسمك المادة، ويمكن حتى استخدام فجوة سلبية للتغلب على الارتداد.
2) بالنسبة للمواد اللينة مثل النحاس الناعم Q215 وQ235 و08 و10 و20 وH62، عندما يتجاوز سمك المادة 0.8 مم ونصف قطر الانحناء كبير، يمكن تصميم الجزء العامل من المثقب مع نتوءات محلية. وهذا يركز ضغط العمل للمثقب عند الزوايا المنحنية.
من خلال زيادة الضغط عند الانحناء، قمنا بتعزيز مكون التشوه البلاستيكي في منطقة التشوه، وتحسين توزيع الضغط، وبالتالي تقليل التشوه المرن وتقليل الارتداد إلى أقصى حد ممكن.
3) بالنسبة للمواد الصلبة مثل Q275، 45، 50، H62، عندما يكون نصف قطر الانحناء r>t، يمكن تصميم زاوية تعويض الارتداد على القالب أو اللكمة بناءً على قيم الارتداد المقدرة مسبقًا أو التي تم الحصول عليها تجريبياً للقضاء على الارتداد.
بدلاً من ذلك، يمكن تصميم الجزء العلوي من القالب كسطح على شكل قوس (للانحناء على شكل حرف U)، مما يؤدي إلى انحناء عكسي محلي في الجزء السفلي. وهذا يعني أنه عند إزالة الجزء من القالب، فإن ارتداد المنحنى العكسي سيتسبب في ارتداد سلبي على كلا الجانبين، مما يعوض الارتداد الإيجابي للجدران الجانبية.
4) بالنسبة للانحناء على شكل Z، قد يكون لزاويتي الانحناء للانحناء على شكل Z قيم ارتداد مختلفة، مما قد يتسبب في عدم توازي السطحين العلوي والسفلي للأجزاء على شكل Z. لتجنب هذه الظاهرة، يجب إمالة اللكمة والقالب للخارج بزاوية Δ φ. بالنسبة للألواح المدرفلة على البارد بسمك أقل من 1 مم، تؤخذ زاوية الميل عمومًا على أنها 2 درجة ~ 3 درجات.
5) بالنسبة للمواد الأكثر ليونة، يمكن استخدام قوالب مطاطية بدلاً من القوالب الصلبة، كما هو موضح في الشكل 1-10. ونظرًا لحقيقة أن المطاط يمكنه نقل الضغط في اتجاهات مختلفة مثل السائل في حاوية صلبة، فإن عملية الانحناء تخضع لتغييرات مفيدة مقارنة باستخدام القوالب الصلبة.
اللوحة مدعومة بالكامل على المطاط، مع دعم أقوى في المنتصف من على الجانبين. لذلك، عندما ينحني الجداران المستقيمان للوحة حول الزوايا المستديرة للثقب، فإنهما يلتصقان تمامًا بسطح الثقب، وتكون الجدران المستقيمة أقل عرضة للانحناء المفرط، مما يقلل من الارتداد.
إذا تم استخدام مطاط الإيلاستومر عالي الصلابة، فإن التأثير يكون أفضل. بالإضافة إلى الدقة العالية، فإن استخدام قوالب المطاط لا يترك خدوشًا على سطح الأجزاء المنحنية، كما أن تنوع المطاط وقوالب الإيلاستومر المطاطي جيد جدًا.
خاتمة
يعد الارتداد تحديًا متأصلًا في ثني الصفائح المعدنية، مدفوعًا بالتعافي المرن للمادة بعد التشوه البلاستيكي. تؤثر عوامل مثل خصائص المادة وسمك الصفائح ونصف قطر الانحناء وطريقة الانحناء على درجة الارتداد. ومع ذلك، من خلال استخدام استراتيجيات مثل الإفراط في الانحناء وضبط قوى الانحناء واستخدام أدوات المحاكاة، يمكن للمصنعين التحكم بشكل فعال في الارتداد وإنتاج أجزاء عالية الجودة ودقيقة التشكيل. مع استمرار نمو الطلب على المكونات خفيفة الوزن والقوية والدقيقة في الصناعات مثل السيارات والفضاء، فإن إتقان إدارة الارتداد سيظل جانبًا بالغ الأهمية في تصنيع الصفائح المعدنية.
آلات SC هو محترف الفرامل الصحافة باستخدام الحاسب الآلي ومصنع آلات الضغط واللكم، ونحن نقدم حلول الانحناء للعملاء لأكثر من 25 عامًا. لا تتردد في الاتصال بنا إذا كنت بحاجة إلى آلات الانحناء.