Table of Contents
With the rapid development of modern manufacturing in intelligence, automation, and digitization, laser processing technology characterized by high precision, efficiency, and flexibility is widely used in the field of engineering machinery manufacturing. This article explores the application and development potential of laser processing technology in engineering machinery manufacturing, analyzes its advantages in key processes such as cutting, welding, surface treatment, and precision machining, and proposes its important role in improving product quality and production efficiency, providing technical basis and practical guidance for the technological innovation and industrial upgrading of engineering machinery manufacturing.
Principles And Characteristics Of Laser Processing Technology
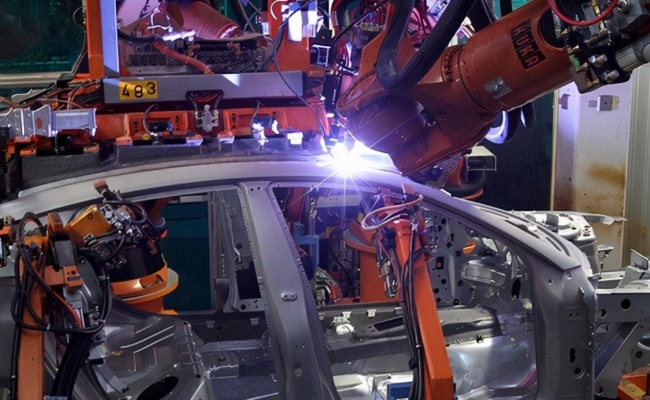
Basic Principles of Laser Processing Technology
Laser processing technology is a method of processing materials using high-power density laser beams. The principle is to achieve melting, vaporization, or changes in the heat affected zone of the material through the interaction between the laser and the material, in order to achieve the processing purpose. Laser processing technology has the characteristics of non-contact, high precision, high speed, and strong flexibility, which can achieve the processing of complex shapes, reduce the thermal impact and deformation of materials. In the field of engineering machinery manufacturing, the application of laser processing technology can significantly improve processing accuracy and efficiency, reduce production costs, and is one of the indispensable high-precision technologies in modern manufacturing.
Main Types Of Laser Processing Technology
Laser cutting, laser welding, laser marking, laser engraving, laser surface hardening, laser cladding, etc. are common application types in laser processing technology. Laser cutting technology occupies an important position in metal sheet processing with high cutting speed and excellent cutting quality. Laser welding is widely used in the field of precision welding due to its advantages of deep melting width, small heat affected zone, and small deformation. Laser marking and engraving technology play an important role in product identification and artistic creation with high precision and low wear. Laser surface hardening and cladding technology improve the wear resistance and corrosion resistance of workpieces by changing the surface properties of materials. These technologies have their own characteristics and complement each other, promoting the application of laser processing technology in engineering machinery manufacturing. Widely applied and developed.
Advantages And Limitations Of Laser Processing Technology
Laser processing technology plays an important role in modern manufacturing due to its high processing accuracy, fast speed, small heat affected area, and the ability to achieve automation and intelligent control. Laser processing can achieve fine operation of materials, reduce material waste, and improve production efficiency. Its non-contact characteristics reduce mechanical stress on workpieces, making it suitable for processing brittle materials and high-precision requirements. However, this technology also has certain limitations, such as high equipment costs, specific requirements for operating environments, limited processing efficiency of some materials, and the possibility of high energy consumption and heat effect control problems during laser processing.
The Application Direction Of Laser Processing Technology In Engineering Machinery Manufacturing
Application 1: Cutting Technology
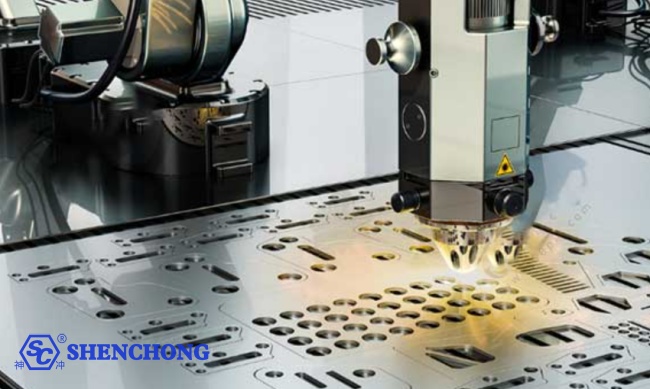
Laser cutting technology plays a crucial role in engineering machinery manufacturing. This technology uses high-energy density laser beams to perform non-contact cutting of materials, achieving high-precision and high-speed processing effects. Compared with traditional mechanical cutting methods, it has unparalleled advantages, including smaller heat affected zones, less processing deformation, wider material adaptability, and more flexible processing path design. Laser cutting technology is widely used in the processing of thick plates and irregular parts. Construction machinery usually requires structural parts to have high strength and stiffness. Laser cutting can accurately cut according to the design drawings, ensuring the geometric dimensions and accuracy requirements of the parts, improving the performance and reliability of the whole machine, and can also achieve one-time molding of complex shapes, simplifying the processing flow, shortening the production cycle, and reducing manufacturing costs. However, laser cutting technology also faces some challenges in its application process. For high reflectivity materials such as copper and aluminum, the efficiency and quality of laser cutting may be affected. Laser cutting equipment and operating costs are relatively high, and there are also high requirements for the technical level of operators.
Application 2: Welding Technology
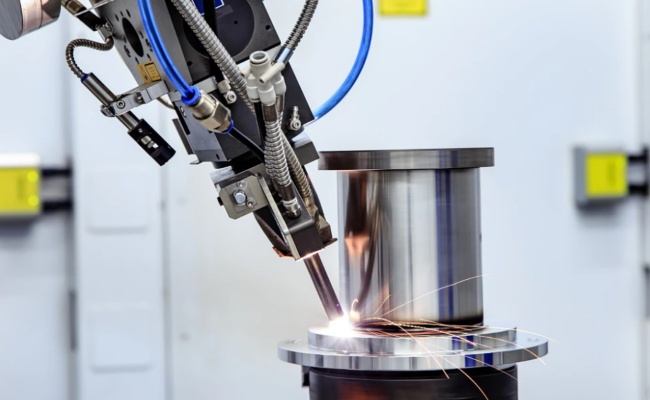
Laser welding technology, as an advanced connection process, achieves material melting and solidification by focusing the high temperature generated by the laser beam, thereby forming a weld seam. It has significant characteristics such as deep melting width, small heat affected zone, fast welding speed, and small deformation, making laser welding play a key role in improving the connection strength and overall performance of engineering machinery structural components. Laser welding technology is widely used in the connection of high-strength steel, aluminum alloys and other materials. The working environment of construction machinery is complex and varied, which has extremely high requirements for the strength and durability of structural components. Laser welding technology can provide high-quality welds, improve the mechanical properties of welded joints, and meet the reliability needs of construction machinery under harsh working conditions.
The highly automated and intelligent level of laser welding technology provides higher production efficiency and lower labor costs for engineering machinery manufacturing. By precisely controlling welding parameters, laser welding can achieve welding operations in complex shapes and difficult to access areas, solving the problems that traditional welding methods are difficult to overcome. Laser welding technology also has certain limitations in practical applications, with strict requirements for operating environment and material surface quality, high sensitivity to welding parameters, and the need for precise control to avoid welding defects.
Application 3: Surface Treatment Technology
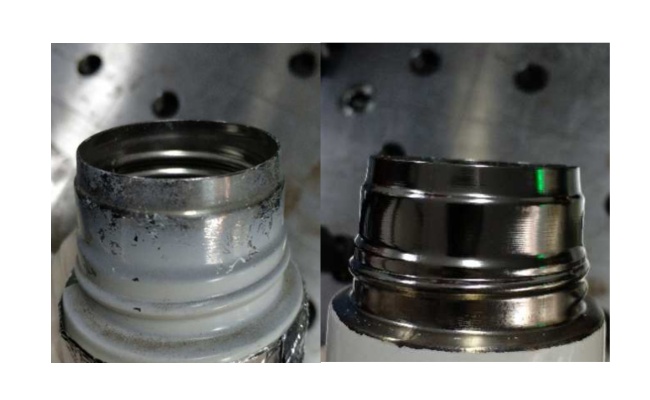
Laser surface treatment technology is a key technology in the field of engineering machinery manufacturing. By irradiating the material surface with a laser beam, the surface properties of the material can be improved, including laser hardening, laser cladding, and laser alloying. Moreover, without changing the properties of the material matrix, the wear resistance, corrosion resistance, and fatigue strength of the material surface can be significantly enhanced. In the field of construction machinery, the working environment is often harsh, and there are extremely high requirements for the durability and reliability of components. The application of laser surface treatment technology can effectively extend the service life of mechanical components, reduce maintenance costs, and laser cladding technology can add a layer of material with specific properties to the surface of mechanical components, endowing them with additional characteristics such as wear resistance, corrosion resistance, or high temperature resistance.
The non-contact and highly controllable nature of laser surface treatment technology has unique advantages in processing complex shapes or difficult to reach areas. Compared with traditional surface treatment techniques, laser treatment reduces material waste, improves processing efficiency, and also reduces environmental impact. Laser surface treatment technology also faces some challenges in practical applications. The complexity of the technology itself requires operators to have high professional skills. The high cost of equipment and strict requirements for environmental conditions are also factors that restrict its widespread application. In order to overcome these challenges, researchers need to continuously explore more efficient treatment processes, optimize parameter settings, and reduce costs through technological innovation.
Application 4: Precision Micro-fabrication Technology
In the precision machining process of important components of construction machinery, the wide adaptability of material types is a major advantage of the application of laser micro machining technology. For materials such as metals, ceramics, or plastics, laser micro machining can provide efficient application solutions, providing stronger technical support for the diversified design and functional integration of construction machinery. However, it should be noted that precise control of laser parameters is highly required in the micro machining process, and even extremely small deviations may lead to a decrease in machining accuracy. In order to unleash the potential of laser microfabrication technology in precision component manufacturing, researchers need to continuously improve the technological level of laser equipment, update and optimize laser control systems, reduce equipment costs through the integration of various disciplines, strengthen the training of equipment operators, and enhance their understanding and application capabilities of laser microfabrication technology.
The Development Trends and Challenges of Laser Processing Technology in Construction Machinery Manufacturing
With the rise of intelligent manufacturing and the demand for sustainable development, the application prospects of laser processing technology in the construction machinery manufacturing industry are becoming increasingly broad. Laser processing technology will pay more attention to the development direction of efficiency, precision, and intelligence. The research and development of high-power lasers will promote significant improvements in cutting and welding speed and quality. The advancement of laser microfabrication technology will also meet the demand for high-precision components. With the integration of computer-aided design and artificial intelligence algorithms, the laser processing process will achieve higher levels of automation and intelligence.
Laser processing technology also faces many challenges in its development, including high equipment costs, high requirements for operational skills, and a deep understanding of material properties. The thermal effects, deformation control, and stability of processing accuracy during laser processing are also technical difficulties that need to be solved. Researchers need to strengthen basic research, optimize process parameters, develop new laser processing equipment, and cultivate professional talents to promote the widespread application and in-depth development of laser processing technology in engineering machinery manufacturing. Through continuous technological innovation and process improvement, laser processing technology is expected to play a more critical role in improving the performance of construction machinery, reducing production costs, and promoting the green transformation of the manufacturing industry.