Table of Contents
Automatic metal deburring refers to the process of removing burrs, sharp corners, sharp edges or other irregular parts during metal processing through automated equipment and technology. Burrs are usually small protrusions or excess parts that are inevitably formed during cutting, stamping, drilling, milling and other processing processes, which may affect the appearance, performance or safety of the product. Through automated deburring, processing efficiency, product quality and production consistency can be improved while reducing the risks of manual operation.
Automated metal deburring is the process of removing burrs and irregularities formed after processing by processing the surface and edges of metal workpieces with the help of various automated equipment (such as deburring machines, robots, lasers, vibration grinding, etc.). This process can be performed on different metal materials (such as steel, aluminum, stainless steel, etc.) and applied to workpieces of different shapes and sizes.
1. Working principle of automatic metal deburring
The working principle of automated sheet metal deburring varies depending on the equipment and technology, mainly including the following:
Mechanical grinding:
Use tools such as abrasive belts, grinding wheels or brushes to grind the edges of metal workpieces to remove burrs. Suitable for most conventional metal materials.
Vibration grinding:
Use the mutual friction between the grinding medium and the metal workpiece under vibration to gradually remove the burrs on the workpiece surface. Suitable for smaller and precise metal parts.
Laser deburring:
Use a laser beam to accurately ablate the burrs on the metal surface. Suitable for deburring with high precision requirements and thin sheet metal.
Water jet deburring:
Use high-pressure water flow to impact the workpiece to remove burrs. Suitable for precise, heat-free deburring needs.
Electrochemical deburring (ECM):
Use the principle of electrolysis to dissolve the burr part through electric current in the electrolyte. Especially suitable for complex shapes and high-precision parts.
Fully automatic deburring systems usually consist of multiple devices that automatically complete burr identification, location, removal and quality inspection processes. Compared with traditional manual deburring methods, fully automatic systems have significant advantages and are suitable for large-scale production, precision processing and high-demand manufacturing industries.
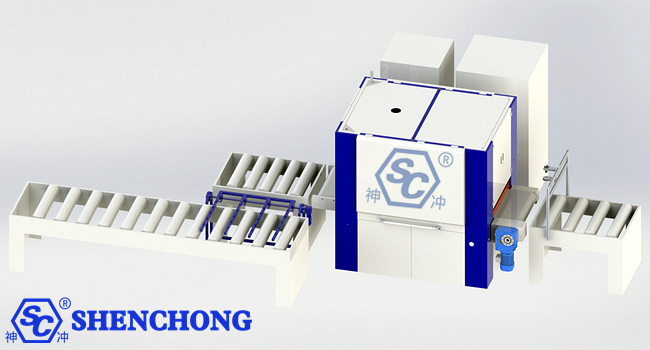
2. Fully automatic deburring workflow
- Raw material conveying and positioning
The workpiece (such as metal sheets or stamping parts) is transported to the deburring station through an automated conveying system (such as chain conveyor, roller conveyor or robotic arm, etc.).
Sometimes, the workpiece needs to be accurately positioned by a visual system or laser scanning to ensure the accuracy of the deburring process.
- Burr identification and analysis
Visual inspection system: Use high-definition cameras, laser scanning and other equipment to identify the edge of the workpiece and the location of burrs in real time.
Intelligent analysis: According to the material, shape and burr type of the workpiece, the system automatically calculates the best deburring solution and makes adjustments.
- Automatic metal deburring
- Sanding machine/grinding machine: Use high-speed rotating sanding belts, grinding wheels or brushes to evenly grind the edges of the workpiece and remove burrs.
- Laser deburring: Use high-energy laser beams to ablate burrs on the metal surface, suitable for precision parts or thin plate processing.
- Vibration grinding: Remove burrs through the mutual friction between the vibrating grinding medium and the workpiece, suitable for small parts or complex shape parts.
- Water jet deburring: High-pressure water jets impact the surface of the workpiece to remove burrs, which is particularly suitable for occasions that require no heat impact and high precision.
- Robot deburring: Industrial robots carry grinding and polishing tools to process the edges of metal sheets or parts according to the program, which is suitable for complex shapes and large-sized workpieces.
- Quality inspection and adjustment
The deburred workpiece is re-checked by the visual inspection system to ensure that the burrs are completely removed and meet the standards.
If it is detected that the burrs are not completely removed, the system will automatically adjust the parameters of the deburring equipment and reprocess it.
- Automatic sorting and stacking
The processed metal workpieces are automatically sorted and stacked in the designated area, ready for subsequent processing, assembly or shipment.
Use robotic arms, automatic stackers and other equipment for efficient sorting and stacking.
- Waste collection and treatment
The generated waste, abrasives or wastewater are collected centrally through a special waste treatment system to ensure a clean environment and optimize resource utilization.
3. Features of automatic metal plate deburring
- Versatility
Automatic metal deburring equipment can usually cope with a variety of different metal materials and workpiece shapes, and has strong adaptability. For example, a multifunctional deburring machine may support the deburring of aluminum, stainless steel, carbon steel and other materials at the same time.
- Intelligence
Modern automated equipment is usually equipped with sensors, vision systems and AI algorithms, which can detect the location and shape of burrs in real time and automatically adjust the deburring process.
Intelligent systems can also realize remote monitoring and fault warning of equipment, and improve the controllability of the production process.
- Widely applicable
Automated metal deburring technology is applicable to a variety of industrial fields, such as automotive, aviation, electronics, home appliances and other industries.
It can handle metal parts of various shapes, from simple flat plates to complex three-dimensional parts.
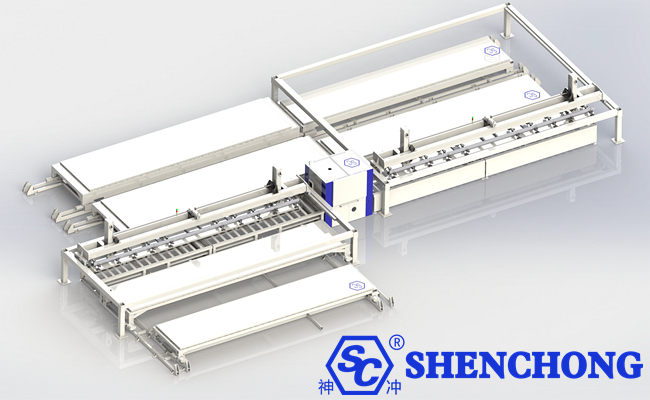
4. Advantages of automated deburring
High efficiency:
Automated systems can achieve continuous and high-speed processing, significantly improve production efficiency, and are particularly suitable for mass production.
It is much faster than manual operation, avoiding the time waste and errors caused by manual processing.
Consistency and precision:
Automated equipment can ensure the consistent quality of burr removal for each workpiece, and can ensure accurate deburring effect regardless of the complexity of the workpiece shape.
Avoids unevenness and errors in manual operation.
Improve product quality:
The surface of the workpiece after deburring is smoother, reducing wear and damage to the product in subsequent processing.
Improve the assembly and aesthetics of metal parts, reduce the safety risks of products, and avoid damage caused by sharp edges.
Reduced labor intensity:
Automated equipment replaces manual deburring, reducing dependence on manual labor, especially for repetitive and high-intensity work, avoiding fatigue and errors caused by long-term operation.
Reduced costs:
Although the initial equipment investment is high, automated deburring can reduce long-term labor costs, improve work efficiency, and reduce scrap rates. Efficient automated production can also enhance the competitiveness of enterprises and reduce overall manufacturing costs.
Safety:
Avoids possible injuries (such as cuts, punctures, etc.) that may occur during manual deburring, reducing safety hazards in the workplace.
Environmental protection:
Some automated deburring technologies (such as wet processing, vibration grinding, etc.) can reduce waste and dust and reduce environmental pollution. High-pressure water jet deburring and other methods can also achieve zero pollution treatment.
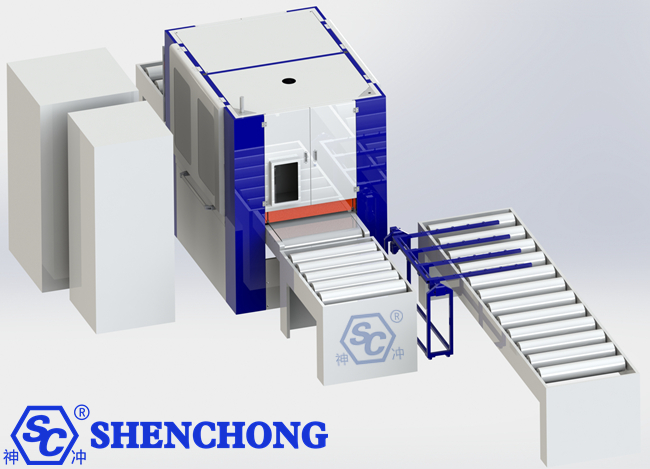
5. Conclusion
Fully automatic metal deburring technology has become an important innovation in modern manufacturing. With the continuous advancement of technology, the degree of automation is getting higher and higher, and it can handle more complex workpieces and meet higher production needs.
If you have specific production needs or process requirements, further understanding of different equipment or solutions will help you choose the most suitable fully automatic deburring system.